Einführung in HDI PCB Mikrovias
Die Miniaturwunder enträtseln
Gedruckte Schaltungen (PCBs) sind seit Jahrzehnten das Rückgrat moderner elektronischer Geräte. Mit dem technischen Fortschritt wächst die Nachfrage nach kleineren, leichteren und effizienteren Geräten. PCB-Mikrovias spielen eine entscheidende Rolle bei der Erfüllung dieser Anforderungen. Dieser umfassende Leitfaden befasst sich mit der Welt der Leiterplatten-Mikrovias, den Typen, Herstellungsverfahren, Anwendungen und wichtigen Designüberlegungen. Ob Sie nun ein erfahrener Leiterplattendesigner oder ein neugieriger Enthusiast sind, dieser Artikel wird für Sie diese Miniaturwunder, die die Elektronik der Zukunft antreiben, enträtseln.
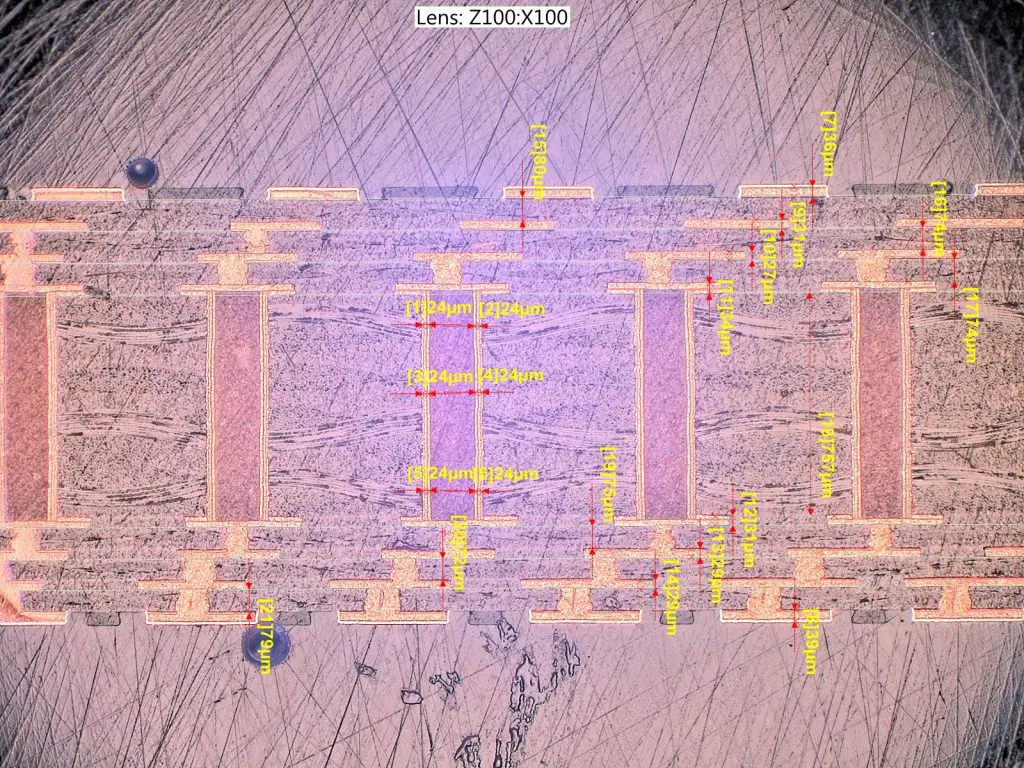
Was sind PCB-Mikrovias?
Mikrovias sind winzige Löcher, die eine oder mehrere Lagen einer Leiterplatte durchziehen und in der Regel einen Durchmesser von 0,1 mm bis 0,15 mm haben. Diese mikroskopisch kleinen Wunderwerke dienen als Pfade für Signale oder Stromverbindungen zwischen verschiedenen Schichten der Leiterplatte und ermöglichen Verbindungen mit hoher Dichte.
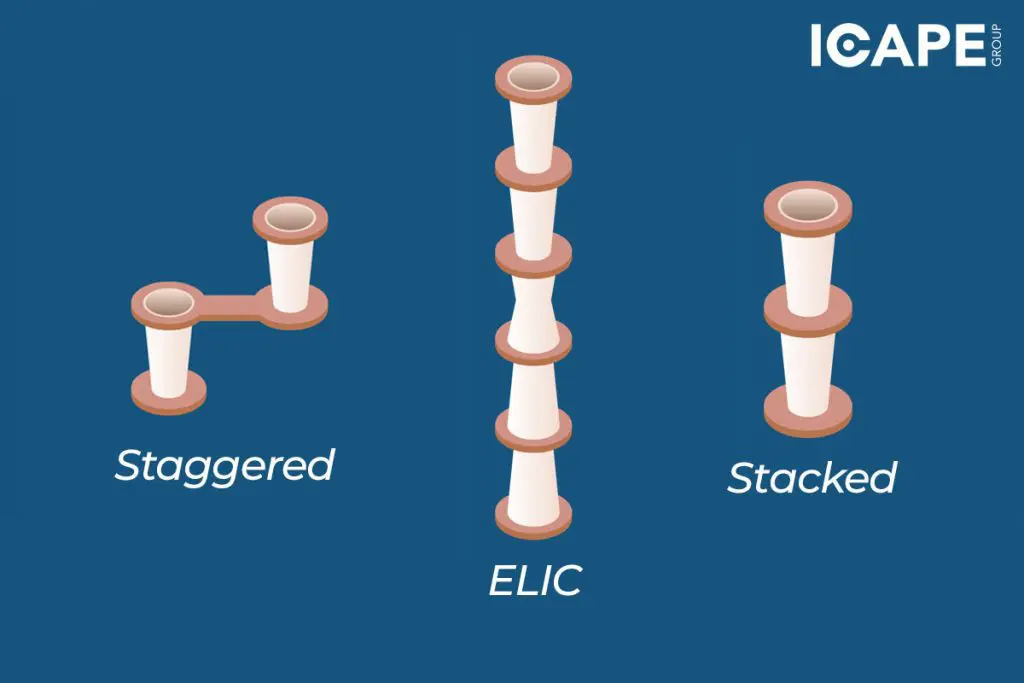
Was sind Vias und Mikrovias?
Via-Löcher werden verwendet, um elektrische oder thermische Verbindungen zwischen den Schichten einer Leiterplatte herzustellen. Grundsätzlich gibt es 4 Arten von Via-Löchern:
- Through Via-Holes (Durchgangslöcher) – mechanisch gebohrte Löcher, die durch alle Schichten des Stapels gehen.
- Buried Via-Holes (vergrabene Bohrungen) – mechanisch gebohrte Löcher, die 2 oder mehr innere Schichten miteinander verbinden.
- Blind Via-Holes (Sacklöcher) – mechanisch gebohrte Löcher, die die äußere Schicht mit einer oder mehreren inneren Schichten verbinden.
- Mikrovias – lasergebohrte Löcher, die eine Schicht mit der nächsten Schicht im Stapel verbinden. (Es ist grundsätzlich möglich, Mikrovias mechanisch zu bohren, aber mit dem Laser ist dies viel einfacher und kostengünstiger.) Die gängigste Mikrovia-Größe ist 80-100µm mit einer Tiefe von 60-100µm. Das Seitenverhältnis ist das Verhältnis zwischen dem Dielektrikum, das die Cu-Schichten isoliert, und dem Durchmesser des Lochs. Die meisten Anbieter verlangen ein Seitenverhältnis von 0,6: 1 zu 1: 1 und die häufigste ist 0,8: 1 (z. Dielektrikum 80um Laserbohrer Durchmesser 0,1mm) Die neue Generation von Laserbohrmaschinen kann Vias mit Durchmessern von bis zu 40-50um bohren und einige von ihnen sind sogar in der Lage, Löcher gleichzeitig von beiden Seiten eines Materials zu bohren. Dies bietet die Möglichkeit, dünne Dielektrika vor dem Laminierungsprozess mit dem Laser zu bohren. Das ist besonders bei der Herstellung von IC-Substraten wie PCBs nützlich.
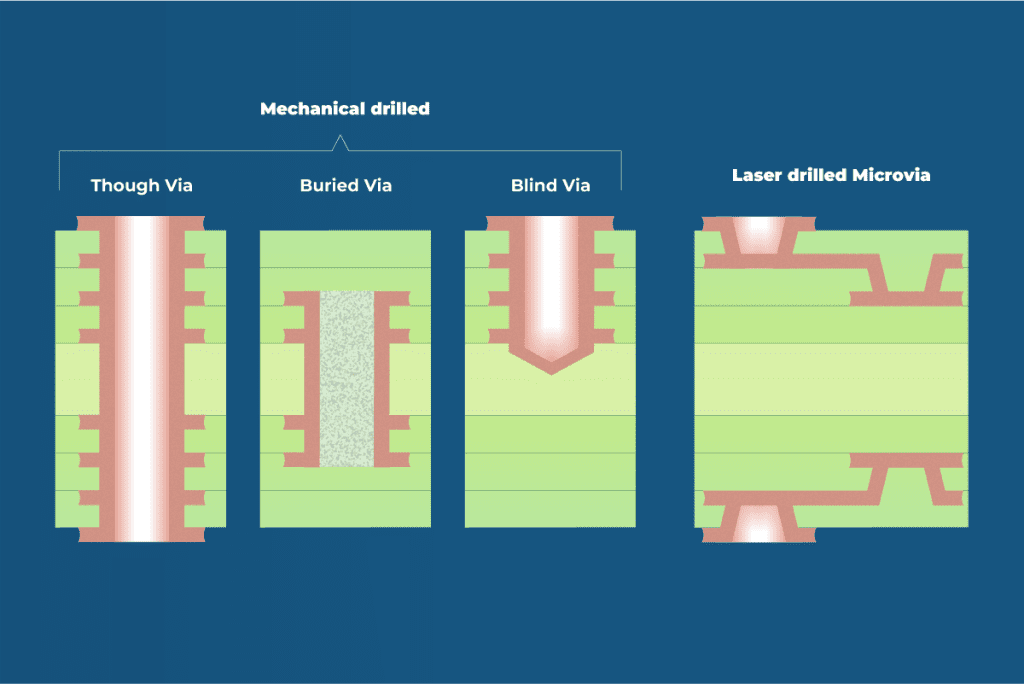
HDI-Stack-up-Strukturen und HDI-Stufen
Standard-Leiterplatten mit PTH (Plated Through Holes) erfordern nur 1 Laminierung, 1 mechanische Bohrung, 1 Lochreinigung, 1 chemische Cu-Beschichtung und 1 galvanische Cu-Beschichtung. Bei HDI-Strukturen kann es erforderlich sein, diese Schritte mehrfach zu wiederholen.
Alle HDI-Leiterplatten beginnen mit dem Aufbau der mittleren Innenlagen und wiederholen die Schritte Laminieren, Bohren, Reinigen und Beschichten, bis der endgültige Stapel fertiggestellt ist. Im Folgenden zeigen wir einige Beispiele.
Die IPC-2226 Typ-1-Konstruktion erfordert nur eine Laminierung, eine mechanische Bohrung, eine Laserbohrung von einer oder beiden Seiten, eine einmalige Lochreinigung, eine chemische Cu-Beschichtung und eine galvanische Cu-Beschichtung. Dies wird auch als 1-stufige HDI bezeichnet.
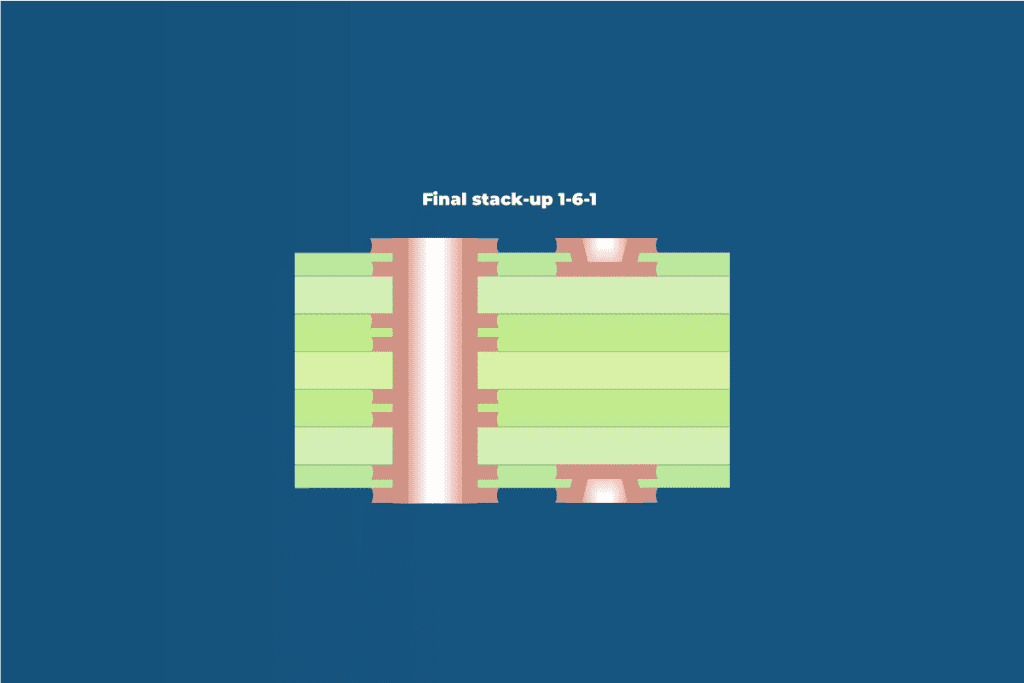
Wenn 1-Schritt-HDI nicht ausreicht, um den Komponentenabstand oder die allgemeine Leiterplattendichte zu unterstützen, können zusätzliche vergrabene Vias hinzugefügt werden, um die Verdrahtungsdichte zu erhöhen. Die IPC-2226 Typ-2-Konstruktion erfordert 2 Laminierungen, 2 mechanische Bohrungen, Laserbohrungen von einer oder beiden Seiten, 2-maliges Reinigen der Löcher, 2 chemische Cu-Beschichtungen, 2 galvanische Cu-Beschichtungen und 1-malige Harzfüllung. Dies wird auch als 2-stufiges-HDI bezeichnet.
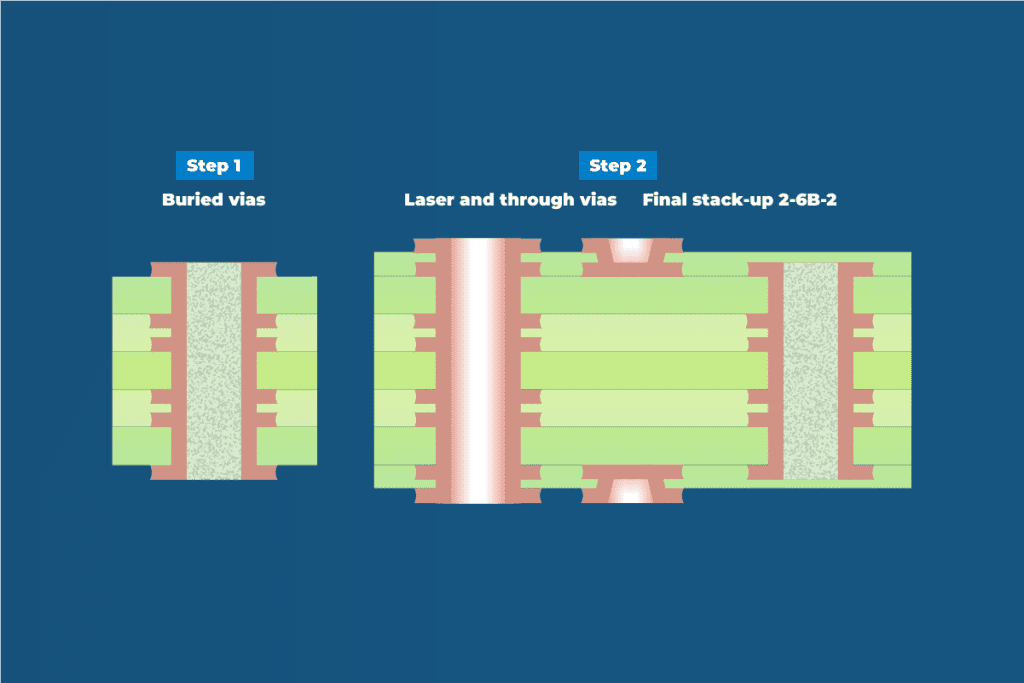
Wenn die Typ-2-Struktur nicht ausreicht, um den Bauteilabstand oder die allgemeine Leiterplattendichte zu unterstützen, können zusätzliche Laser-Vias und vergrabene Vias verwendet werden. Strukturen des Typs 3 enthalten mindestens 2-stufige Mikrovias. Die unten gezeigte IPC-2226 Typ 3-Konstruktion erfordert mindestens 3 Laminierungen, 2 mechanische Bohrungen, 4-maliges Laserbohren, 3-maliges Reinigen der Löcher, 3 chemische Cu-Beschichtungen, 3 galvanische Cu- und Beschichtungen und eine 1-malige Harzfüllung. Dies wird auch als 3-Stufen-HDI bezeichnet.
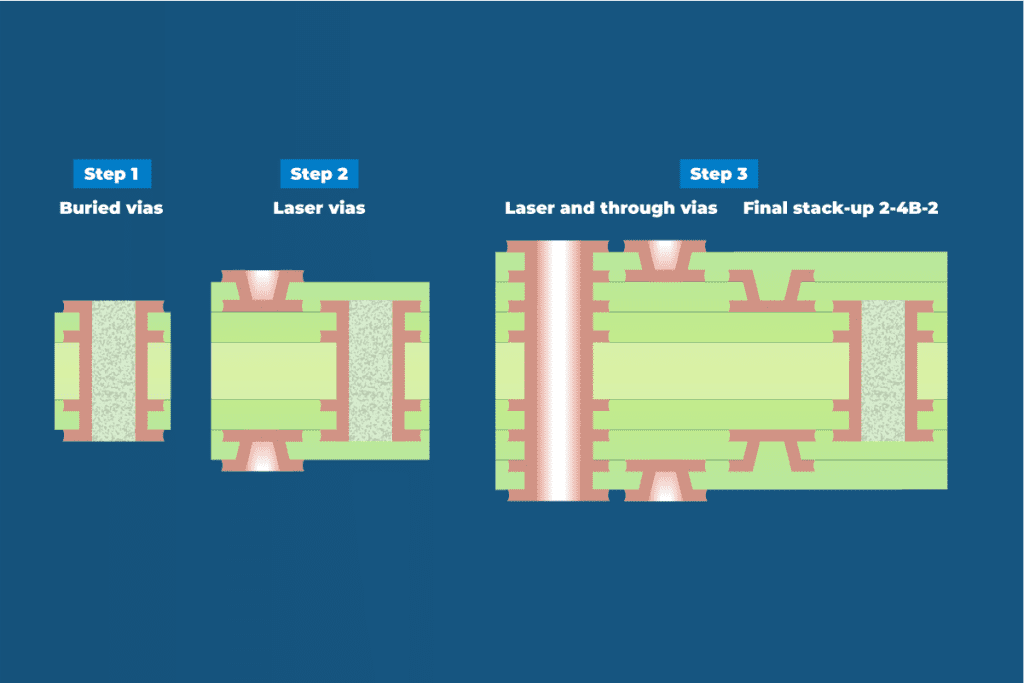
HDI-Schritte Entwicklung
Der BGA-Abstand hat sich von 1,2 mm bei den allerersten BGA-Bauteilen auf 1,0 und 0,8 mm entwickelt, wo Mehrfachschichten, die nur Durchgangslöcher enthalten, zur Herstellung der Verbindungen genügten und Fanouts mit einem „Dogbone“-Design erreicht werden konnten. Heutzutage sind die meisten BGA-Bauteile nur im Raster von 0,5 mm oder darunter erhältlich, was bedeutet, dass die HDI-Technologie mit lasergebohrten Durchgangslöchern eine Notwendigkeit ist, um das Fanout herzustellen. In der Mobiltelefonindustrie hat man sogar begonnen, BGA-Bauteile mit 0,2 mm Abstand einzusetzen.
Diese Entwicklung stößt an die Grenzen der Produktionskapazität und der für die Herstellung von HDI-Leiterplatten verwendeten Geräte.
Die meisten komplexen HDI-Designs, die BGAs mit einer Bohrung von 0,4-0,5 mm enthalten, können mit maximal 2 bis 4 Mikrovia-Schritten von jeder Seite der Leiterplatte aus geroutet werden. Einige Anbieter beherrschen jedoch 5, 6 oder mehr Mikrovia-Schritte. Die Entwicklung der Bauteilminiaturisierung verschiebt zudem die Grenzen immer weiter in Richtung ELIC (Every-Layer-Interconnection), auch Any-Layer-HDI genannt, bei der gestapelte Vias durch jede Schicht des Stapels verlegt werden.
Gestapelte oder gestaffelte Mikrovias / vergrabene Vias
Der Bauteilabstand des BGA zusammen mit der Pad-Größe oder der Designdichte bestimmt, wann gestapelte oder versetzte Mikrovias / vergrabene Vias oder kupfergefüllte Vias zu verwenden sind. Jeder zusätzliche Prozess erhöht die Gesamtkosten der Leiterplatte. Eine sorgfältig vorgenommene Leitungsführung sowie die Auswahl der optimalen HDI-Stack-Up- und Via-Kombination können oft zu Kostensenkungen beitragen. ICAPE möchte Ihr Technologieverständnis mit Fakten und Ratschlägen unterstützen:
Es ist wichtig, die am besten passenden Durchgangs- und Schrittkombination zu wählen, um Ihre Leiterplatte kostenoptimiert zu gestalten.
Die zusätzlichen Kosten für das Hinzufügen einer Mikrovia-Ebene zu einer 1-6B-1-Struktur, durch die eine 2-4(6B)-2-Struktur wie unten entsteht, sind erheblich geringer als die Kosten für eine 2-4B-2-Struktur. Sowohl 1-6B-1 als auch 2-4(6B)-2 sind zweistufige HDI-Konstruktionen, aber 2-4B-2 ist ein dreistufiges HDI.
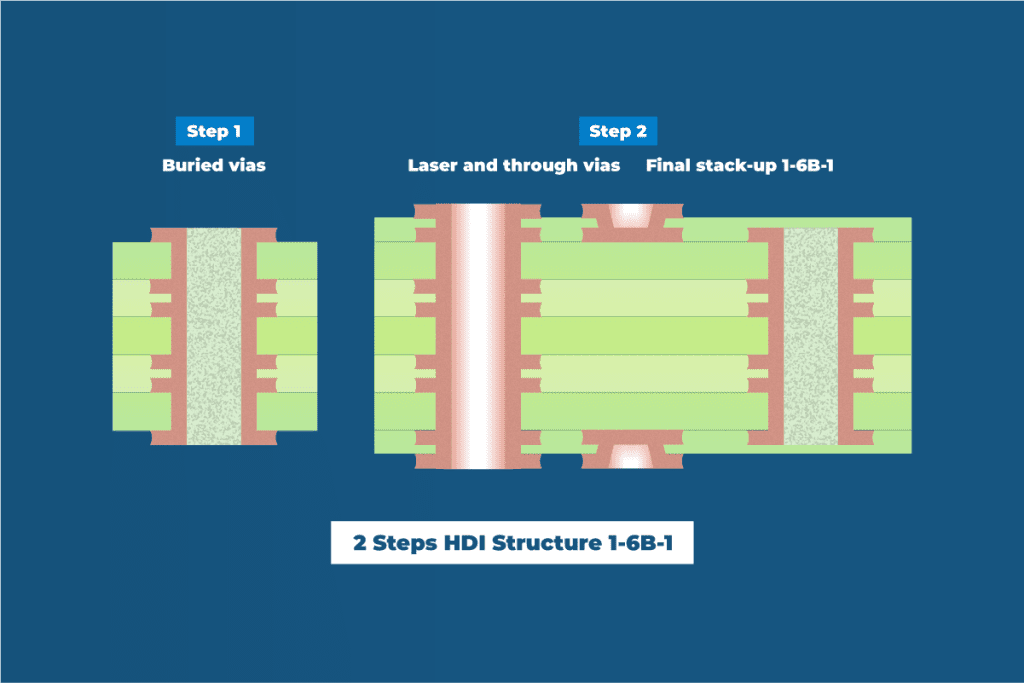
Die einzigen zusätzlichen Prozesse, die bei der Umstellung von 1-6B-1 auf 2-4(6B)-2 hinzukommen, sind 2-maliges Laserbohren.
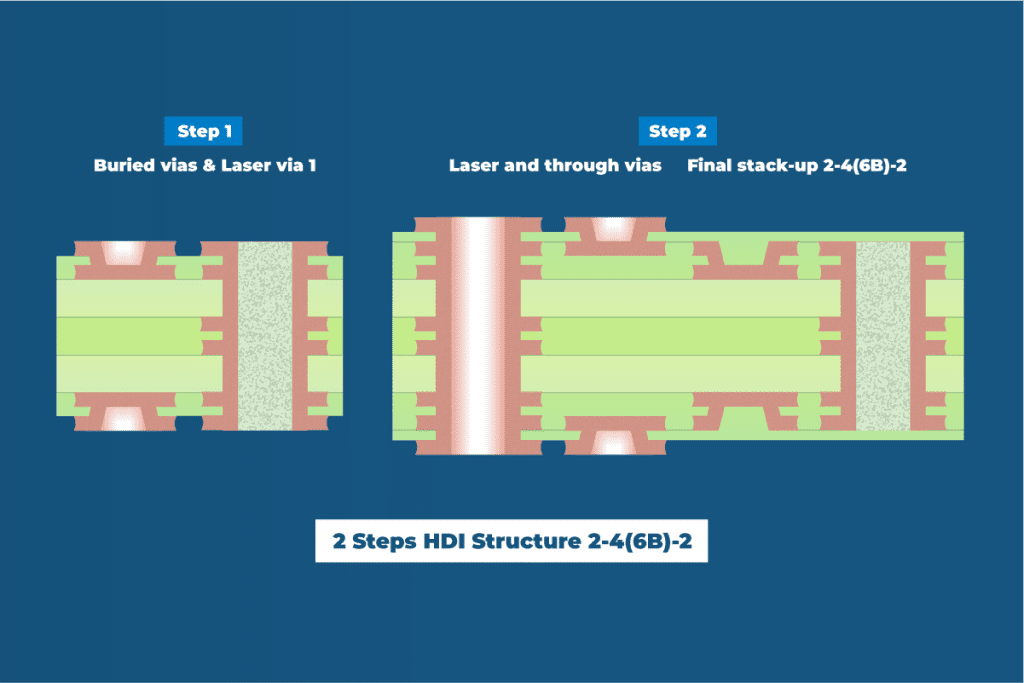
Die Umstellung von 1-6B-1 auf 2-4B-2 erfordert einen zusätzlichen HDI-Schritt mit 2-fachem Laserbohren, 1 zusätzlicher Laminierung, 1 zusätzlicher Lochreinigung, 1 zusätzlichen chemischen Beschichtung und 1 zusätzlichen galvanischen Beschichtung.
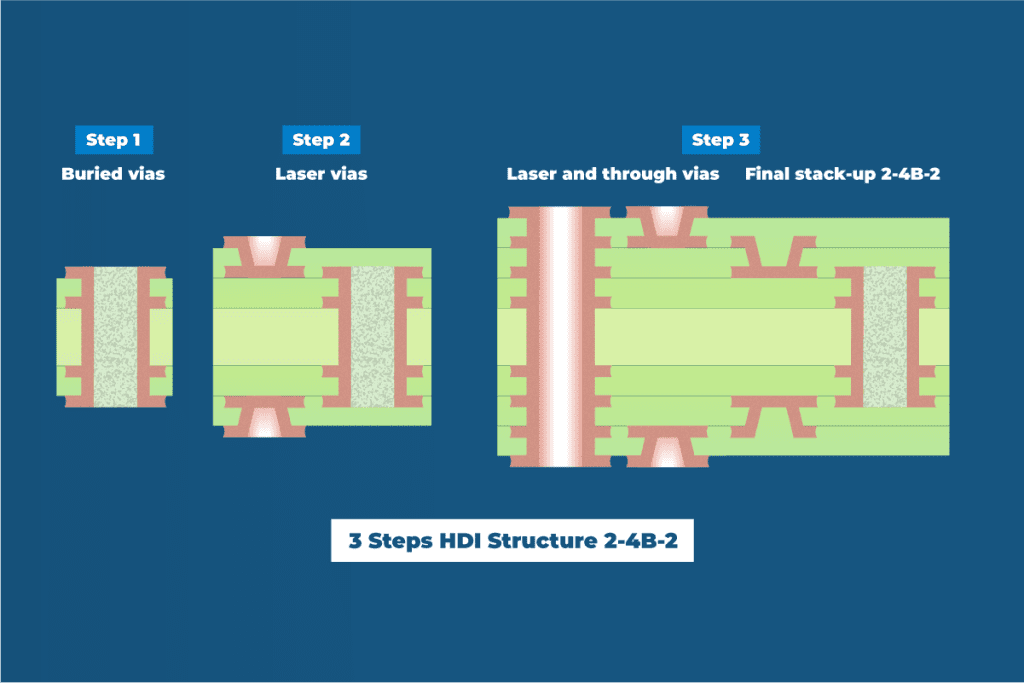
Gestapelte oder gestaffelte Vias?
Gestapelte Mikrovias schaffen mehr Platz für die hochdichte Verdrahtung und das Fanout von BGAs mit einem geringen Raster, erhöhen jedoch die Leiterplattenkosten. Gestapelte Vias sollten nur dann verwendet werden, wenn das Design nicht genügend Platz bietet, um gestaffelte Vias einzusetzen. Mikrovias, die auf vergrabenen Vias gestapelt sind, erfordern ein zusätzliches Cu-Cap-Beschichtungsverfahren für die vergrabenen Vias, und Mikrovias, die auf Mikrovias gestapelt sind, erfordern eine zusätzliche Cu-Füllung der Mikrovias der Innenschicht.
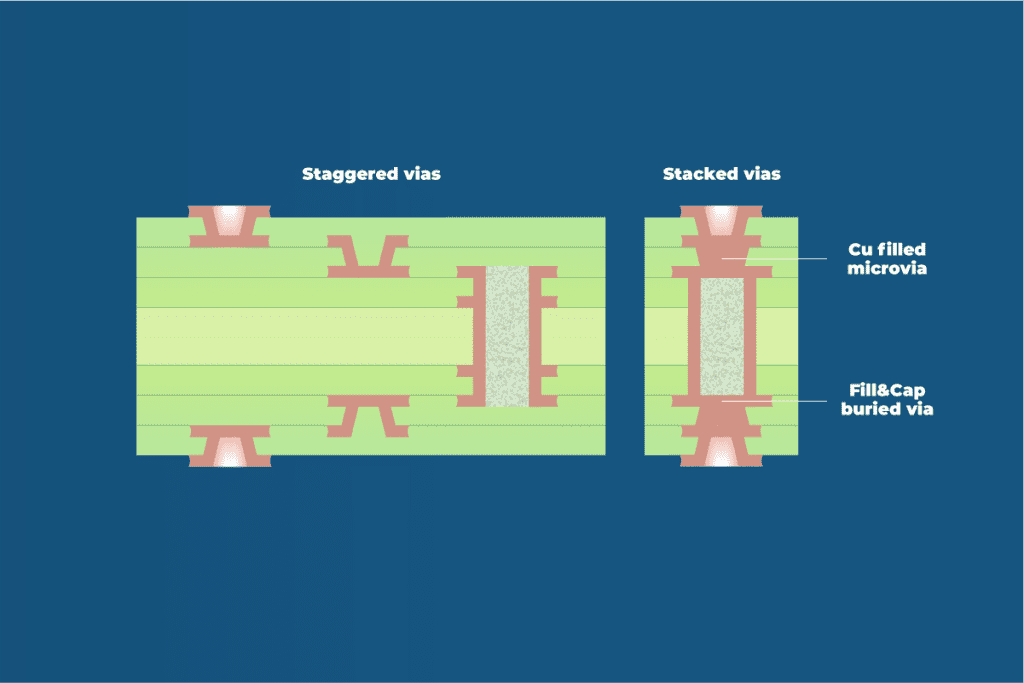
Mit Kupfer gefüllte Mikrovias?
Designs mit Mikrovias in BGA-Pads oder ähnlichen kleinen Lötstellen können von einer Cu-Füllung profitieren, da dies die Möglichkeit von Luftporen in den Lötstellen eliminiert, die Cu-Füllung erhöht jedoch die Leiterplattenkosten. Designs ohne Mikrovias im Pad benötigen keine Cu-Füllung.
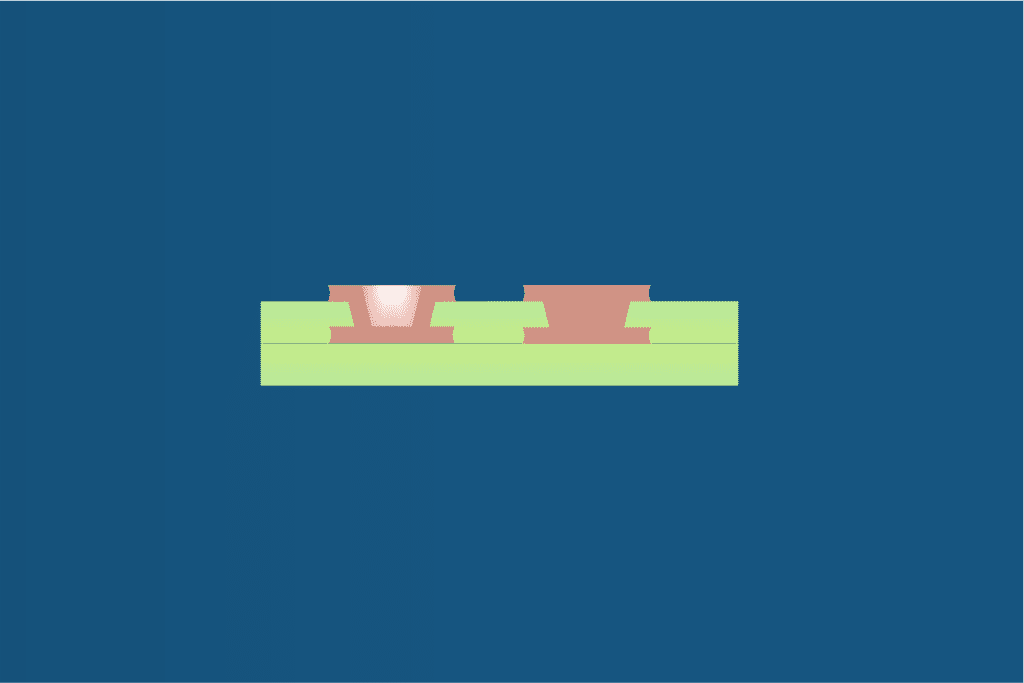
Mikrovia-Integration in das Gesamtdesign
Wenn Sie aufgrund der Verdrahtungsdichte oder des Bauteil-Fanouts die HDI-Technologie mit lasergebohrten Mikrovias und vergrabenen Vias verwenden müssen, ist es sinnvoll, alle mechanischen Vias durch lasergebohrte Mikrovias und vergrabene Vias zu ersetzen, da dies die Herstellungskosten und die Produktionszeit senkt.
Das Laserbohren ist ein wesentlich schnellerer und kostengünstigerer Prozess als das mechanische Bohren, wenn man die Loch-zu-Loch-Kosten vergleicht. Der höhere Preis einer HDI-Leiterplatte im Vergleich zu Standard-Mehrfachschichten hängt mit den zusätzlichen Prozessen zusammen, die für jeden HDI-Schritt erforderlich sind. Die Kosten für den HDI-Prozess sind gleich hoch, unabhängig davon, ob Sie nur einige Mikrovias verwenden, um die BGA-Verdrahtung aufzufächern, oder ob Sie alle Vias durch Mikrovias und vergrabene Vias ersetzen. In diesem Fall wird der Ersatz aller Vias die Zeit und die Kosten für den mechanischen Bohrprozess senken.
Das Ersetzen aller Vias auf der gesamten Leiterplatte ist sinnvoll:
– Das schafft Platz für eine bessere und engere Verdrahtung, was zu einer höheren Anzahl von Komponenten auf geringerem Raum und weniger Gewicht führt.
– Sie trägt zu verbesserter Signalintegrität, kontrollierter Impedanz und reduzierten elektromagnetischen Störungen bei, indem sie kürzere Signalpfade, reduzierte Übertragungsleitungen und verbesserte GND- und VCC-Referenzebenenfunktionalität bei geringerer Lochdurchdringung bietet.
– Damit entfällt die Notwendigkeit, Vias aufzubohren, um Stubsignalreflexionen zu vermeiden.
– HDI-Leiterplatten ohne Vias sind widerstandsfähiger gegen thermische Belastungen, die durch die hohen Temperaturen der Lötprozesse entstehen.
Wie werden mechanisch gebohrte Vias und Laserbohrungen hergestellt?
Sehen Sie sich ICAPE PCB Manufacturing Journey Episode 5 Drilling an.
HDI-Laser-Mikrovias haben die Elektronikindustrie revolutioniert und ermöglichen es, mehr Funktionen in kleinere und leichtere Geräte zu packen. Da sich die Technologie ständig weiterentwickelt, werden Mikrovias auch in Zukunft an der Spitze der PCB-Design-Innovationen stehen und neue Möglichkeiten für hochdichte Verbindungen und fortschrittliche Anwendungen eröffnen. Wenn Leiterplattendesigner die Arten, Herstellungsverfahren und Designüberlegungen im Zusammenhang mit Mikrovias verstehen, können sie deren Leistungsfähigkeit nutzen, um innovative elektronische Geräte für die Zukunft zu entwickeln.
Melden Sie sich für das nächste Webinar von ICAPE zum Thema HDI-Technologie an, in dem wir Ihnen weiteres Wissen und Tipps zur Optimierung Ihres Designs und Ihrer Konstruktionen vermitteln werden.