PCB MANUFACTURING
Proceso
Todos los procesos de fabricación revelados paso a paso. Acompañe a los equipos de ICAPE Group por el interior de nuestras fábricas de PCB para descubrir los secretos de su fabricación.
¿Cómo se fabrican las PCB, paso a paso?
En el complejo mundo de la electrónica, el corazón palpitante de la innovación reside en las placas de circuito impreso (PCB). Estos compactos pero potentes componentes son la columna vertebral de los dispositivos electrónicos y hacen posible la circulación fluida de las señales eléctricas. ¿Alguna vez se ha preguntado sobre el viaje que realiza una PCB desde su concepción hasta su integración? Nuestro próximo artículo ahonda en el completo proceso de la fabricación de las PCB para revelar cada paso con precisión y claridad. Desde la fase de diseño inicial hasta los complejos procesos de grabado y montaje, le guiaremos por la enmarañada red de técnicas y tecnologías que transforman las materias primas en PCB funcionales. Tanto si es un ingeniero con experiencia, un aficionado curioso o alguien intrigado por la magia que se oculta detrás de sus dispositivos electrónicos, acompáñenos en este viaje por el fascinante mundo de la fabricación de las PCB. Prepárese para asistir a la alquimia que convierte el cobre, la fibra de vidrio y la soldadura en circuitos sofisticados que hacen posible el funcionamiento de los dispositivos que utiliza a diario.
Ingeniería de preproducción
¿Cómo se diseña una PCB?
Todo empieza en el Departamento de Ingeniería. Reciben el archivo GERBER, lo comprueban y lo comparan con el pedido, las normas IPC y las capacidades del proveedor.
1- Verificación del archivo Gerber
Los ingenieros de ICAPE Group llevan a cabo una revisión del Diseño para la Fabricación (DFM), comprueban los datos, las capas de cobre, el dibujo mecánico, las especificaciones y la línea y el espacio entre las pistas. Una vez hecho esto, si fuera necesario, creamos un archivo llamado «Cuestiones técnicas».
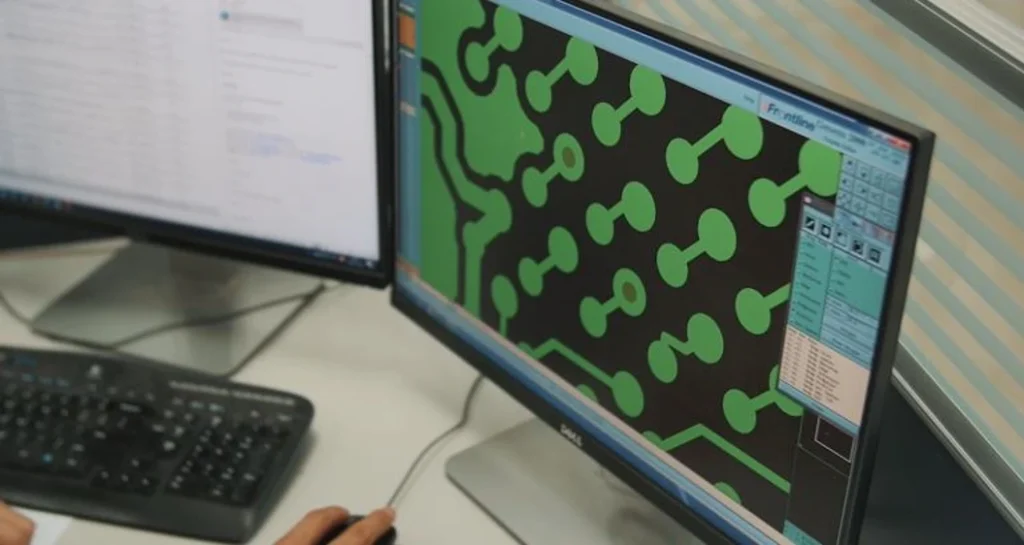
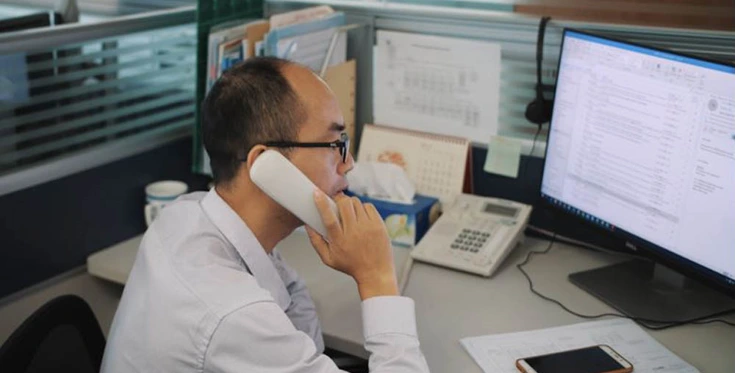
2- Revisión del DFM
Este archivo se envía al cliente para proponerle una posible solución o mejora, como diferentes técnicas de panelización, tipo de máscara de soldadura, diseño, material de base, marca o especificaciones e incluso diferentes tecnologías para que sean factibles y rentables en las fábricas asociadas que se seleccionan de acuerdo con las normas IPC.
3 - Revisión del DFM por empresa asociada
Nuestra fábrica asociada entra en escena, recibe los datos, realiza una segunda revisión del DFM y empieza a combinar los diseños de los circuitos en el panel de producción.
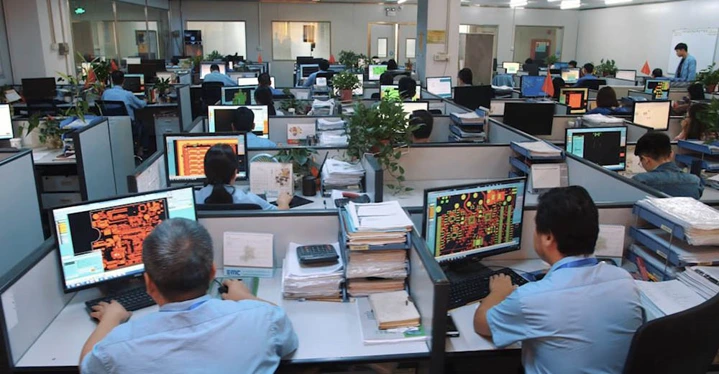
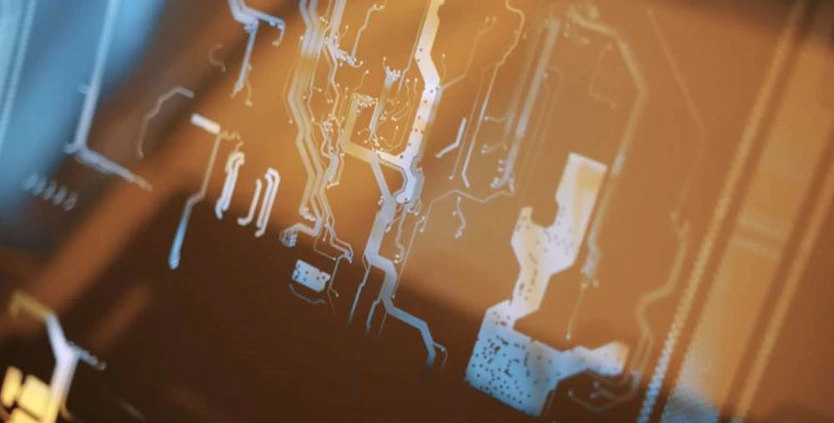
4 - Impresión de diseños
Cada capa de la PCB se verifica y se transfiere a la máquina de impresión. Hay un diseño para cada capa: interior, exterior, máscara de soldadura, impresión de la leyenda y también capas especiales como vías, máscara pelable, carbono, etc. Todos esos diseños pueden utilizarse para miles de paneles.
Materiales de base
¿Cómo seleccionar y preparar los materiales de base?
¿Descubra cómo se almacenan y preparan los paneles antes de pasar a las siguientes etapas del proceso de fabricación!
1- ALMACENAMIENTO
No todos los fabricantes de PCB producen materias primas básicas como preimpregnados o láminas de cobre. Todas las materias primas se suministran de acuerdo con los requisitos técnicos de ICAPE Group. Los materiales se almacenan por tipos, grosor total, grosor del cobre y la marca.
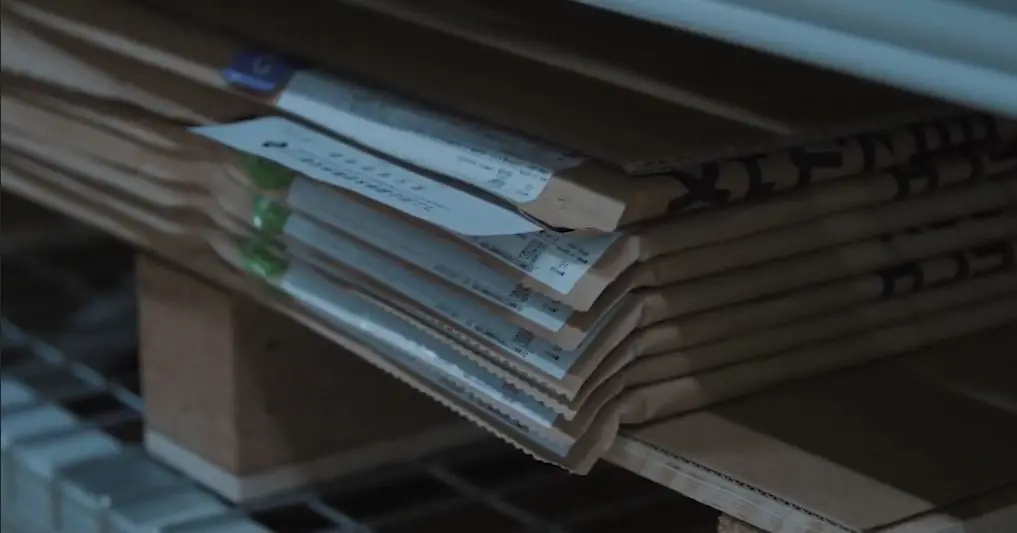
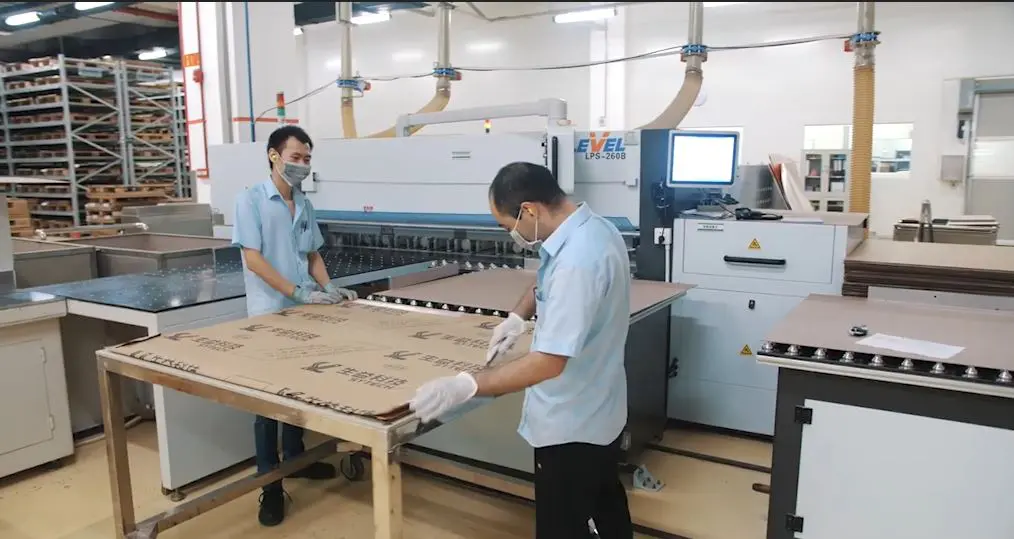
2 - PREPARACIÓN DE PEDIDOS
Según el pedido, la fábrica selecciona los materiales necesarios en el almacén. Los paneles se desembalan y se preparan para pasar por el proceso.
3 - CONTROLES
La inspección de cada lote es un punto fundamental. El cobre y los grosores totales se verifican cuidadosamente con herramientas de alta precisión, para asegurarse de que satisfacen las necesidades de los clientes de acuerdo con la tecnología en creación
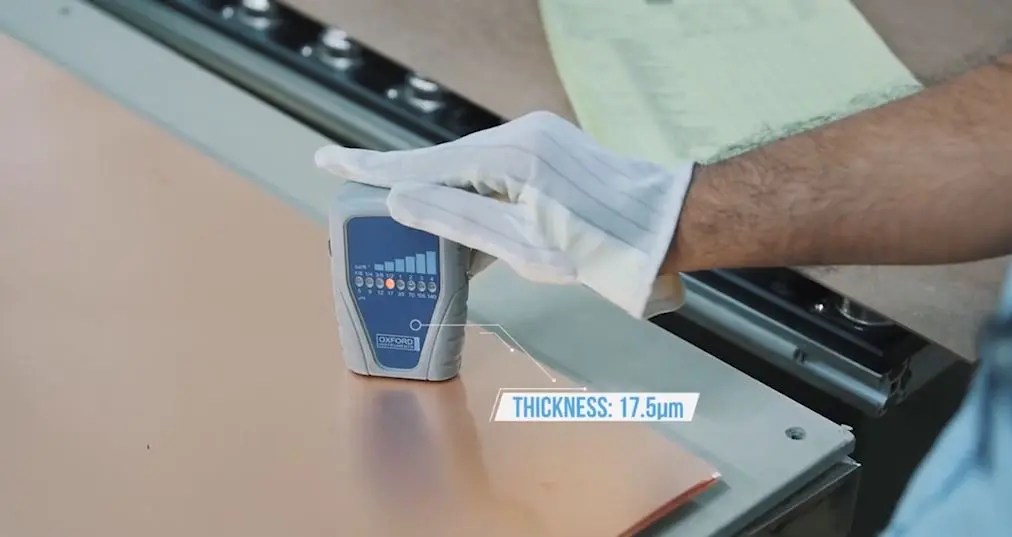
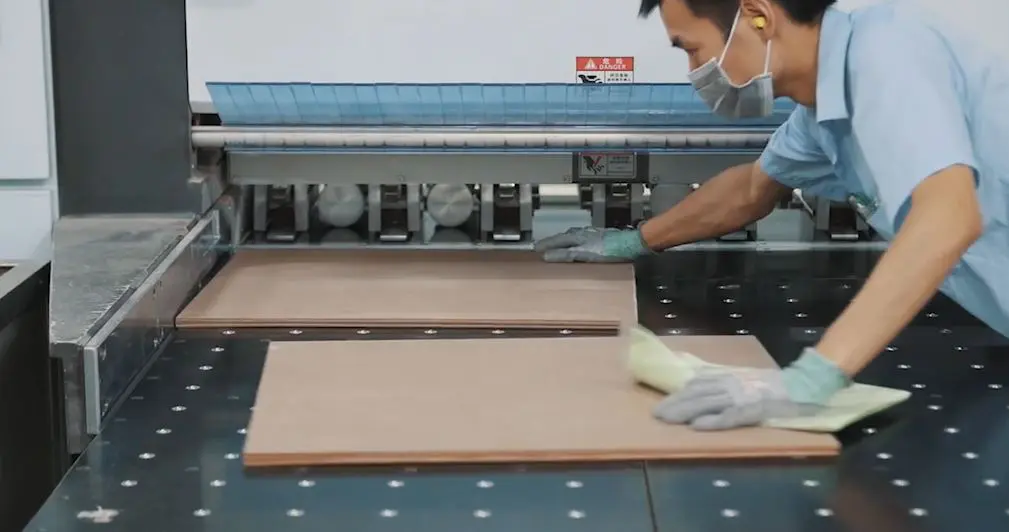
4 - CORTE
El panel debe cortarse a la medida de fabricación. Hoy en día, el acabado de los bordes y la geometría de los paneles son muy importantes para el registro CCD, y los equipos de manipulación.
5 - ACABADO DE ESQUINAS
La mayoría de las empresas han redondeado las esquinas de los paneles para reducir los problemas de arañazos y asegurar su manipulación durante las siguientes etapas del proceso de fabricación
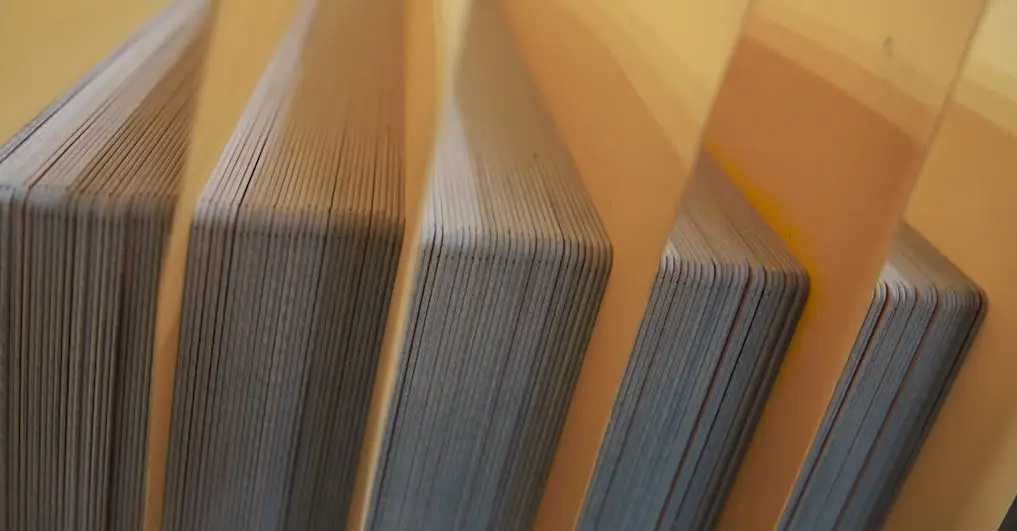
Inner Layer
The inner layer
The inner layer imaging is a very technical step of the process which happens in a clean and yellow room. Why ? Because the dry film is UV sensitive and to avoid any shorts and opens on the inner layer, a level between 3000 and 4000 dust particles per cubic meters must be reached.
1 - CLEANING
The cleanroom uses overpressure to protect and remove any dust coming from outside of the cleanroom. Before entering the cleanroom, the panels are cleaned. Depending on the thickness of the inner layers, the processes are different. For layers thinner than 500 micrometers, the chemical process is used. For thicker layers, the mechanical process is preferred.
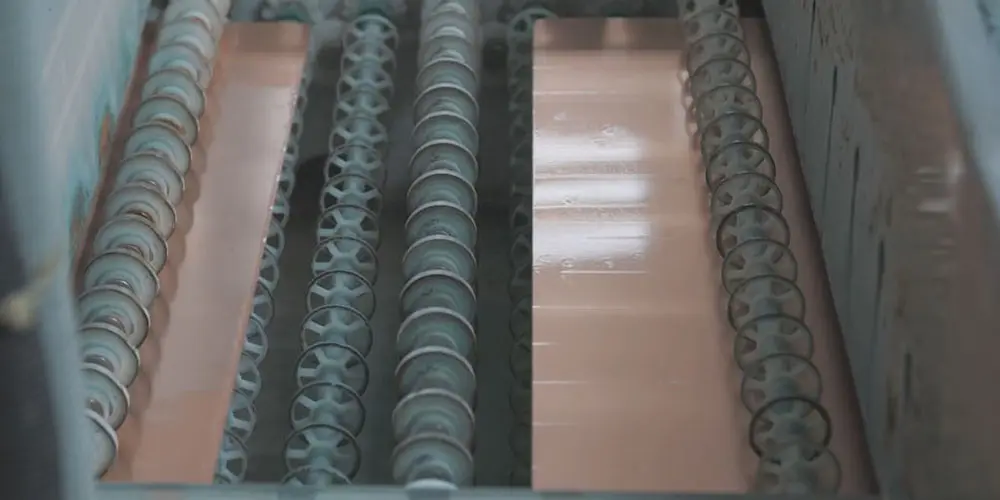
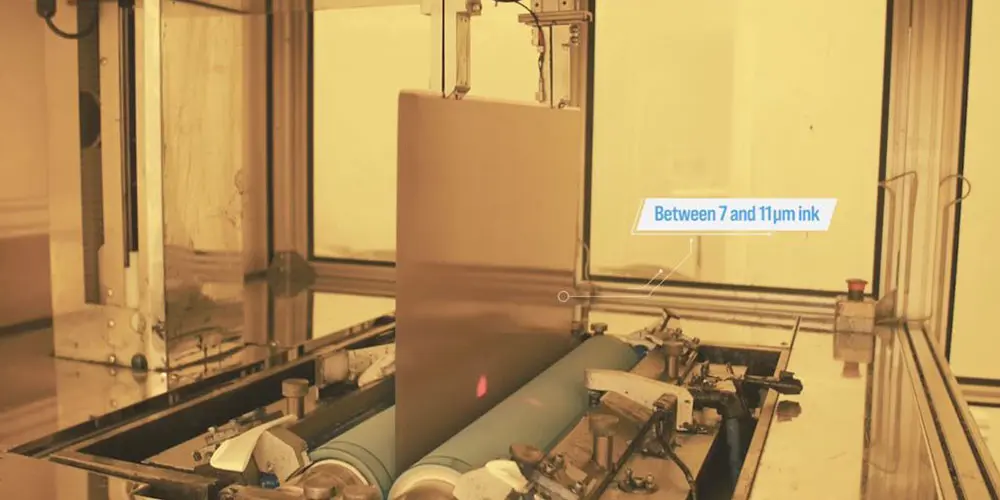
2 - ENDUCTION
When panels arrive in the cleanroom, they are heated, then the photoresist film or the ink ( beteween 7 and 11 µm) is automatically applied onto the panel.
3 - REGISTRATION AND INSOLATION
The boards are registered at +/- 15 to 30 micrometers with 2 or 4 CCD Cameras. A vacuum is created, then a blast of UV light is applied with an average of 1 to 20 seconds depending on the process: this is the insolation. The boards are polymerized and ready to be developed.
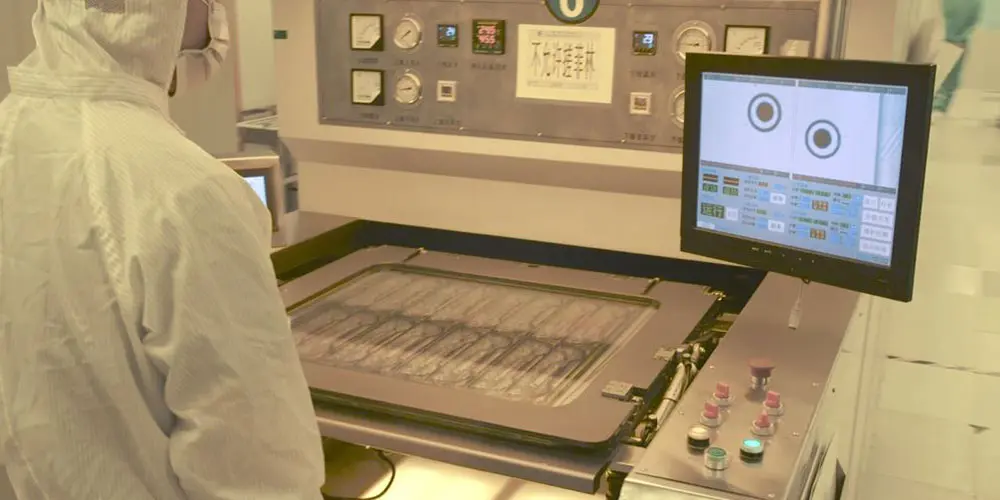
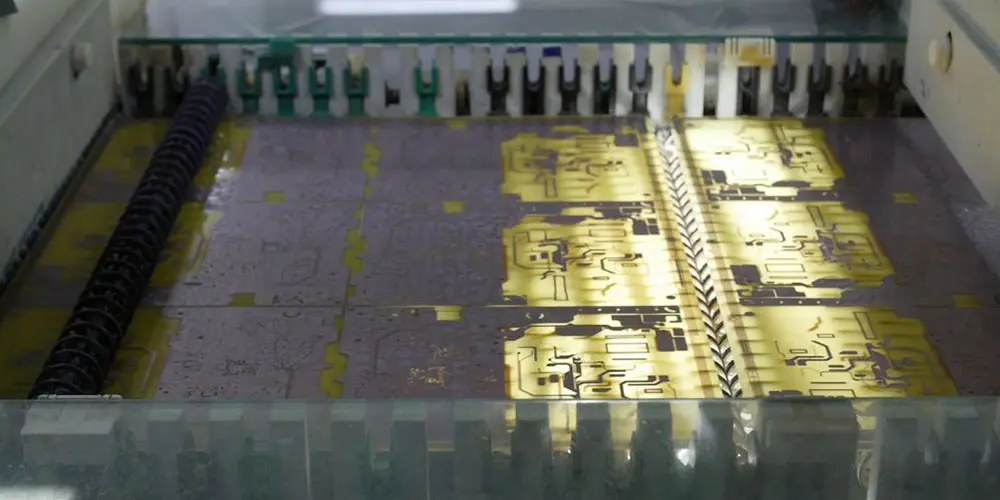
4 - DEVELOPING AND ETCHING
For the development phase, the board is washed with an alkaline solution which removes the photoresist left unhardened. From there, we can see the inner layer image for the first time. Etching is the critical step in layer imaging. The unprotected copper is removed and defines the pattern. After stripping the ink, the photoresist film is now completely removed.
5 - AUTOMATIC OPTICAL INSPECTION (AOI)
After the Multilayer lamination, it is impossible to correct errors occurring on the inner layers. The Automatic Optical Inspection will confirm a total absence of defects. The original design from the GERBER file serves as a model. If the machine detects any inconsistencies, a technician will assess the problem.
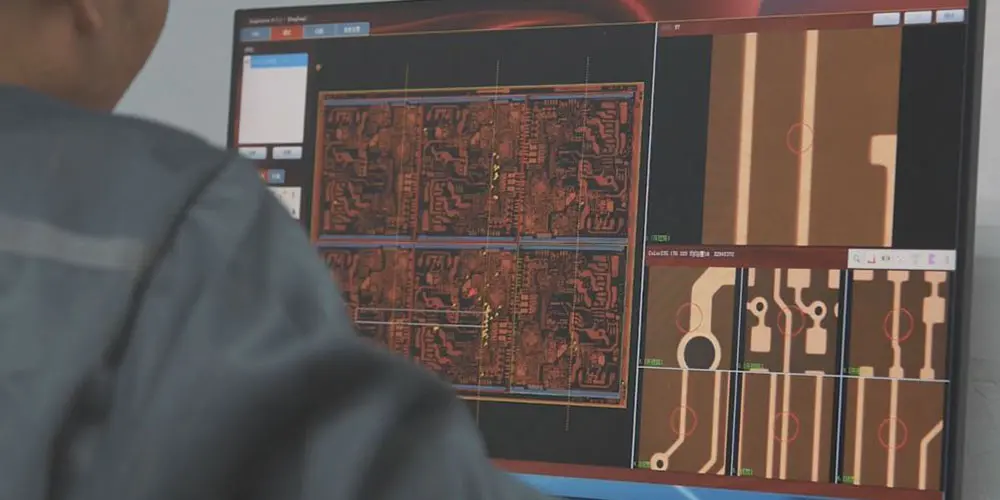
Laminación
¿Qué es la laminación de PCB?
¡Descubra la etapa de laminación del proceso de fabricación de circuitos impresos! Tras la etapa de imagen de la capa interna, las placas pasan por el registro y la laminación. ¡Síganos en nuestra fábrica de HDI en China!
1 - PREPARACIÓN
Los paneles se lavan para eliminar la superficie de cobre corroída, así como posibles huellas dactilares, residuos de película seca, carbonato y residuos antiespumantes del decapado de película seca.
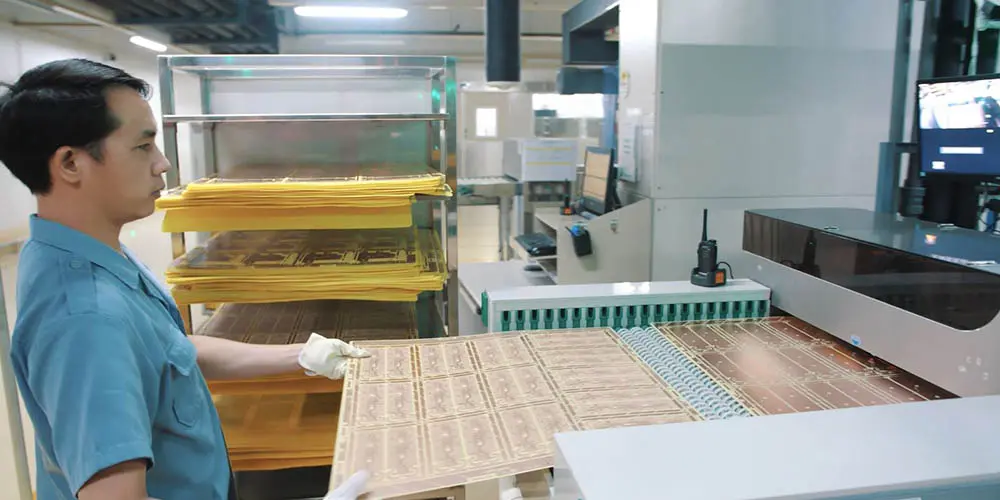
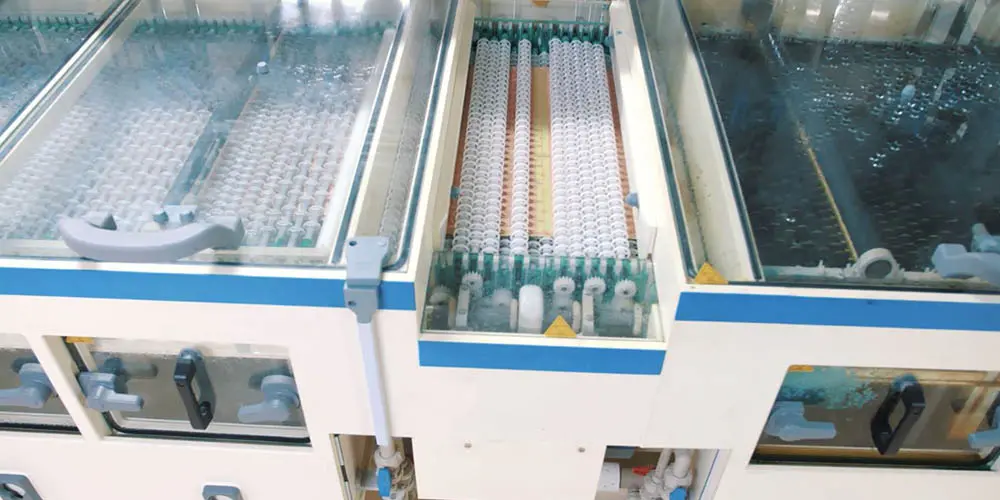
2 - MICROGRABADO
El micrograbado es una condición básica para obtener un tratamiento de óxido marrón o negro homogéneo y adecuado. El proceso reducirá el grosor del cobre de 0,2 a 1 micrómetro.
3 - ÓXIDO NEGRO
El tratamiento con óxido marrón o negro se utiliza para mejorar la adherencia de la resina epoxi y evitar problemas como la delaminación.
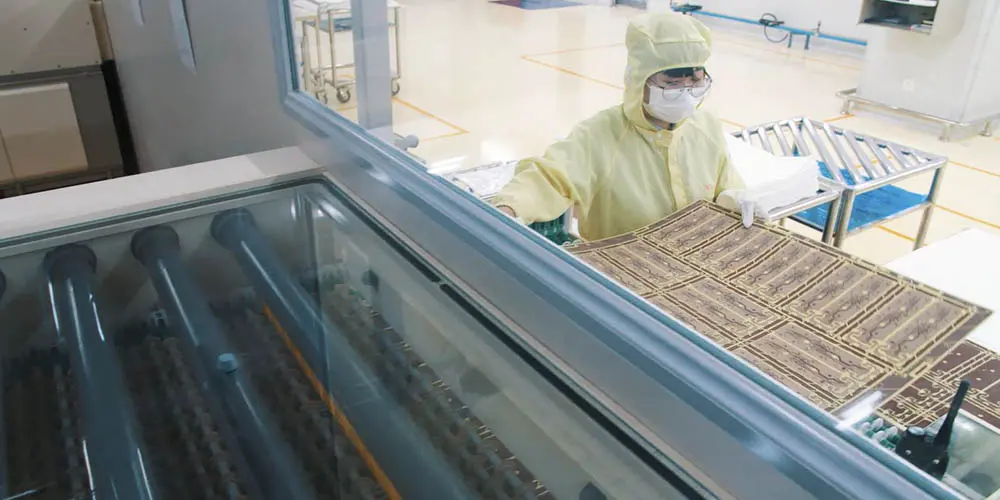
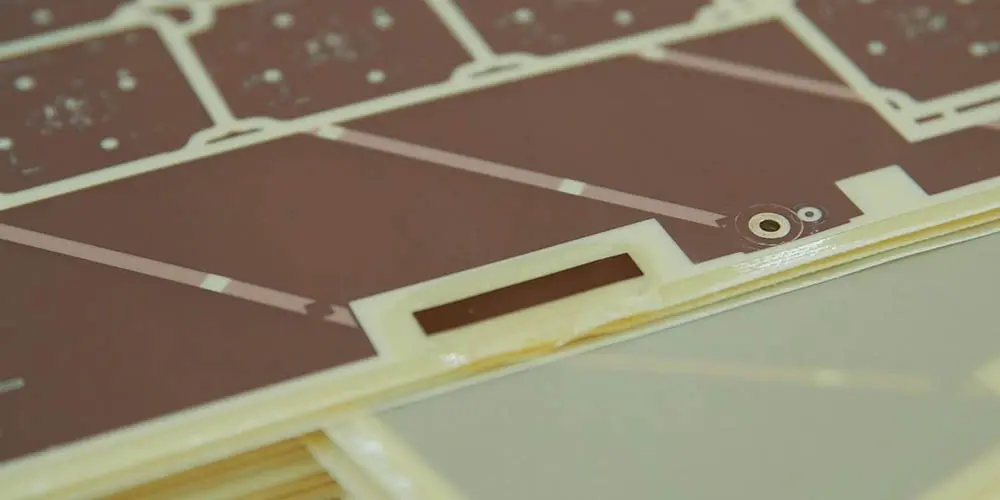
4- CAPA INTERNA APILABLE
El operador apila la capa interna y el preimpregnado en la máquina encoladora, lo que permite pegar el apilado. Una vez pegados, pasamos a utilizar los remaches. El proceso de remachado sirve para completar el registro y reforzar juntos la capa interna y el preimpregnado. Esto refuerza el apilamiento y garantiza que no se mueva durante el proceso de laminación.
5 - APILAMIENTO
La lámina de cobre se intercala entre un parche de acero inoxidable y un preimpregnado. Este acero inoxidable crea una superficie dura y plana. La lámina de cobre completa el apilamiento. Ahora, el panel está compuesto en la parte superior e inferior por una lámina de cobre y un preimpregnado que rodea la capa interna.
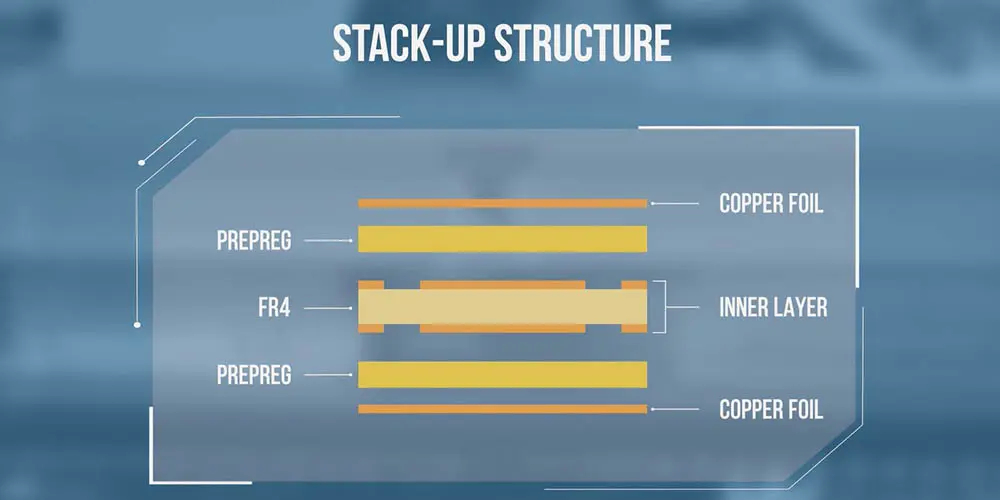
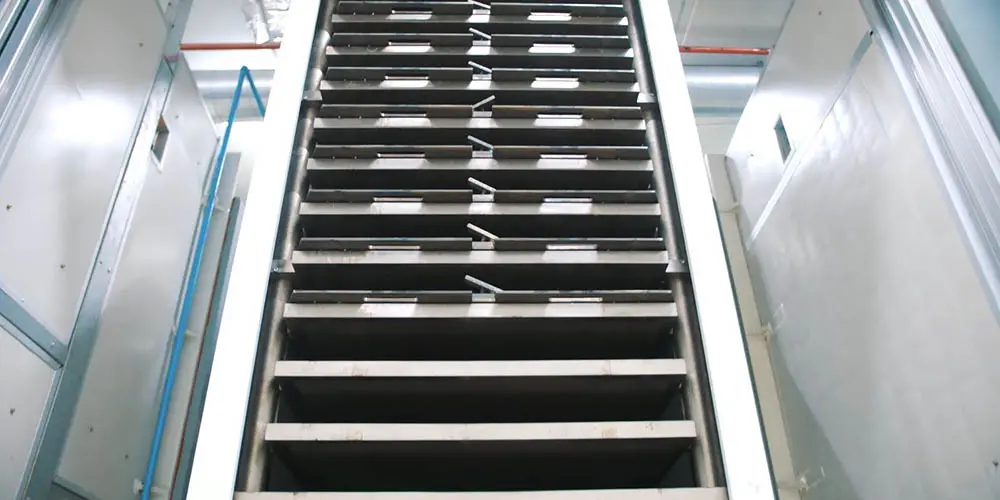
6 - LAMINACIÓN
El apilamiento se somete a temperaturas extremas en función de las fichas técnicas de los materiales. La presión dentro de la máquina de laminación es de 180 toneladas por metro cuadrado y el proceso dura hasta 2 horas. Tras ser expuestas a una presión y temperatura elevadas, las capas forman una sola placa que luego se traslada a una prensa en frío. Posteriormente, se desmoldarán los paneles.
7 - REGISTRO DE AGUJEROS
Estas placas nuevas se prepararán con los agujeros de registro mediante una máquina de rayos X. A continuación, se desbarban, achaflanan y redondean las esquinas.
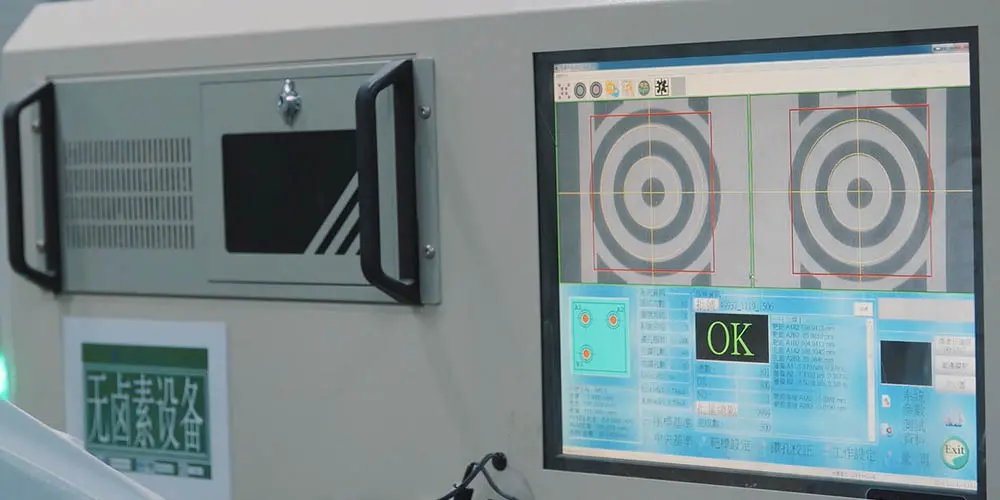
Perforación
¿Cuán complejo es el proceso de perforación?
El quinto episodio de nuestra Jornada de la PCB se centra en uno de los procesos más espectaculares de nuestra serie web: ¡la perforación! No solo es el proceso más impresionante, ¡sino que también es irreversible! Sin duda, este paso debe realizarse con sumo cuidado porque cualquier error, por pequeño que sea, puede causar una gran pérdida. Descubra las diferentes etapas de este proceso (perforación mecánica o láser, diámetro mínimo o incluso controles) siguiendo a nuestros dos expertos de ICAPE Group en una de nuestras fábricas asociadas en China.
1 - PREPARACIÓN
Para mejorar la precisión y la gestión térmica, se utilizan materiales específicos como el aluminio, la madera o la melamina en la parte superior e inferior del apilado.
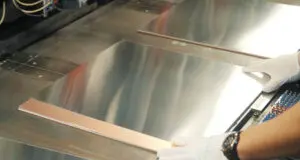
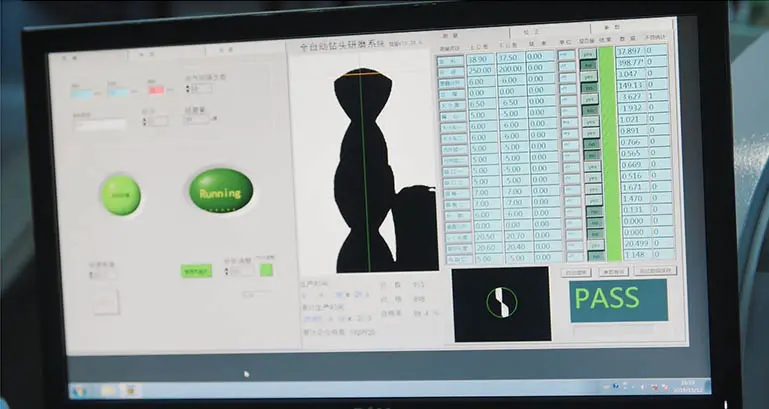
2 - CONTROL DE HERRAMIENTAS
La broca debe tener una forma perfecta y cumplir las normas relativas al número de agujeros que puede realizar la misma herramienta. Para las PCB de alta tecnología, solo se utilizan herramientas nuevas. Para las PCB estándares, las brocas se afilan hasta 3 veces antes de ser cambiadas.
3 - PERFORACIÓN MECÁNICA
Según la serie, para los productos de alta tecnología, la perforadora trabaja en un panel a la vez. Sin embargo, es posible instalar hasta 4 paneles al mismo tiempo, también en función del grosor, con 1 a 6 cabezales de perforación. En los años noventa, solíamos perforar un diámetro mínimo de 400 micrómetros. Actualmente, podemos perforar un mínimo de 150 micrómetros.
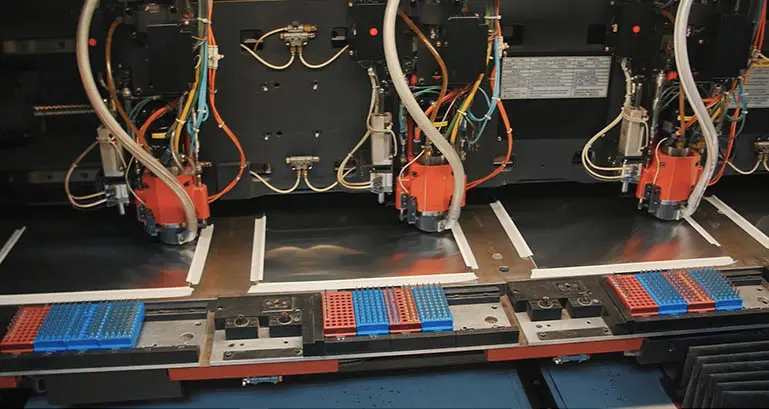
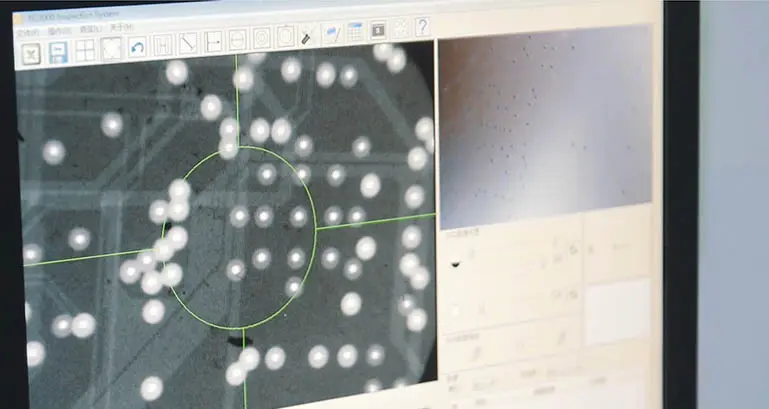
4 - CONTROLES
Para facilitar el control visual, en el borde de cada placa se perforan todos los agujeros de distintos tamaños y se inspeccionan después de la etapa de perforación. Los paneles también se controlan automáticamente con una máquina de verificación de agujeros. Para el control interno, las placas pasan por la máquina de rayos X, que comprueba todo el posicionamiento en relación con la capa interna.
5 - PERFORACIÓN LÁSER
La perforadora láser puede generar orificios para vías de entre 50 y 150 micrómetros. Las herramientas actuales se basan en dos tipos principales de láser: Láser UV o CO2 y, a veces, ambos en función del proceso. Aquí, no hay material superior ni inferior, por lo que solo podemos perforar un panel cada vez y el láser se detiene cuando choca con el cobre de la capa N-1. Hay dos controles principales para garantizar que los agujeros cumplen las dimensiones solicitadas y para comprobar la limpieza.
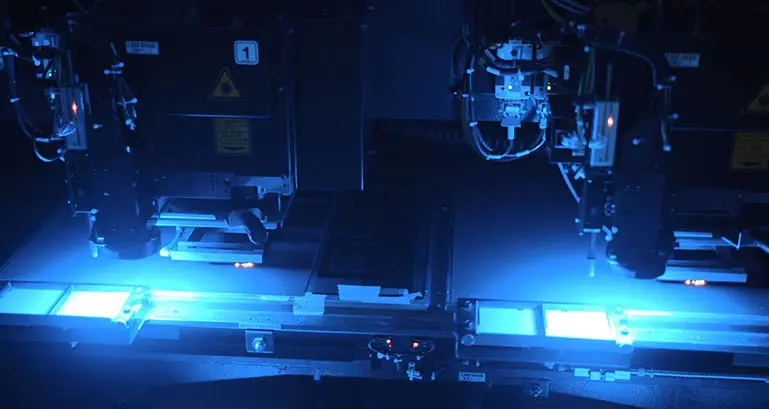
Cobre químico y no electrolítico
¿Cómo depositar el cobre sobre una placa de circuito impreso?
La deposición química de cobre, también llamada cobre químico, crea la conexión eléctrica entre la capa interior y la exterior.
1 - LIMPIEZA ESTÁNDAR
Antes de depositar el cobre químico, la placa debe estar limpia. Para el proceso estándar, los primeros baños limpiarán y eliminarán todos los residuos de la perforación.
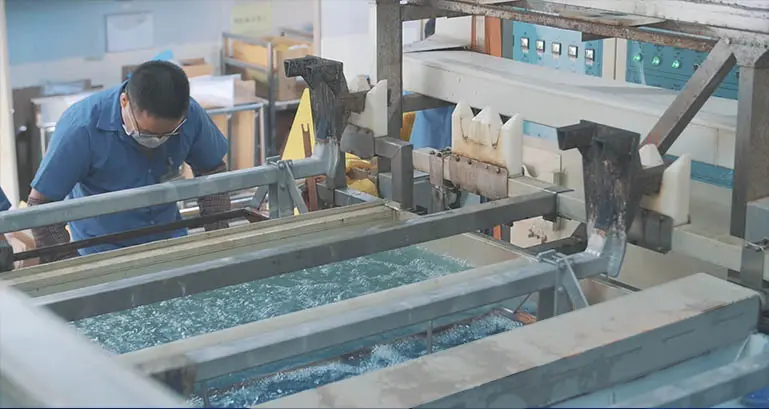
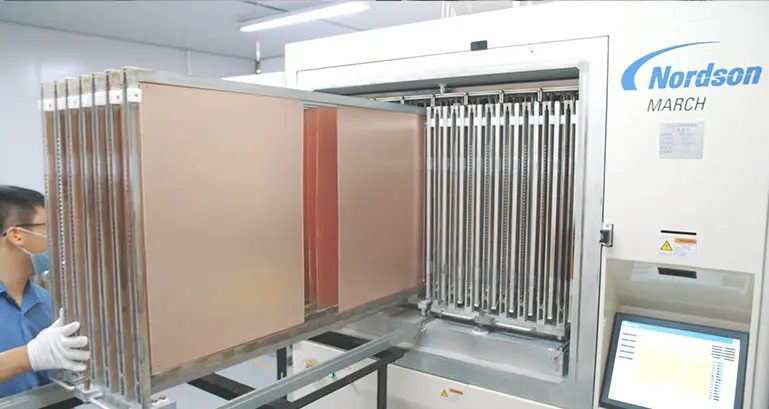
2 - LIMPIEZA POR PLASMA
Para los productos de alta tecnología, es preferible el proceso de plasma: capaz de eliminar residuos más duros como poliimidas, High Tg-FR4, teflón y materiales de microondas RF. Este proceso opcional proporciona una excelente rugosidad y mojabilidad para la deposición química de cobre.
3 - REVESTIMIENTO DE PALADIO
Según la tecnología de la PCB en creación, existen varios tratamientos químicos para obtener agujeros conductores, podemos utilizar cobre, paladio, grafito y polímero. Las placas se sumergen en un baño de paladio, también conocido como baño de activación, para depositar una fina capa de paladio.
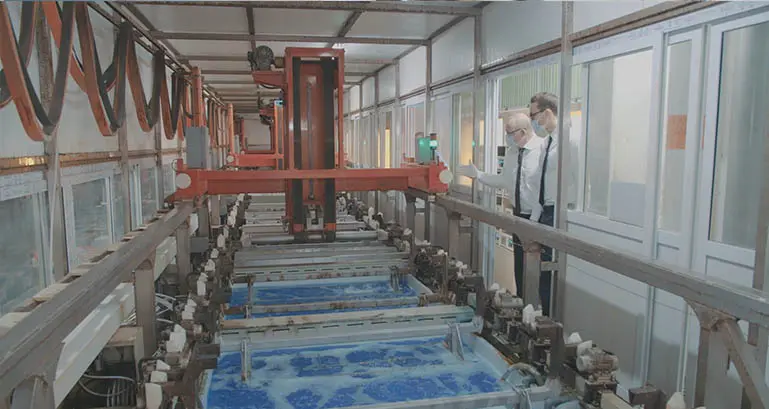
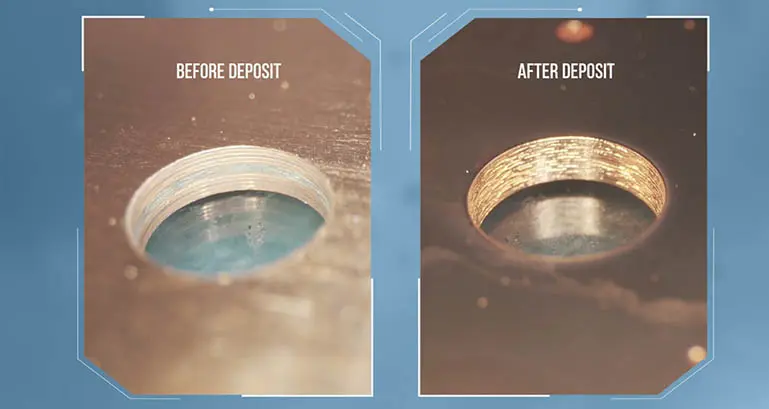
4 - COBREADO
Los paneles se mueven constantemente por el baño para eliminar las posibles burbujas de aire que puedan haberse formado en el interior de los agujeros. El paladio actúa químicamente para atraer un depósito de cobre químico de 1 a 3 micrómetros sobre toda la superficie del panel y los orificios recién perforados.
5 - CONTROLES
El control se lleva a cabo al final de este proceso, principalmente, se realiza una prueba de contraluz para comprobar la porosidad y el revestimiento del cobre.
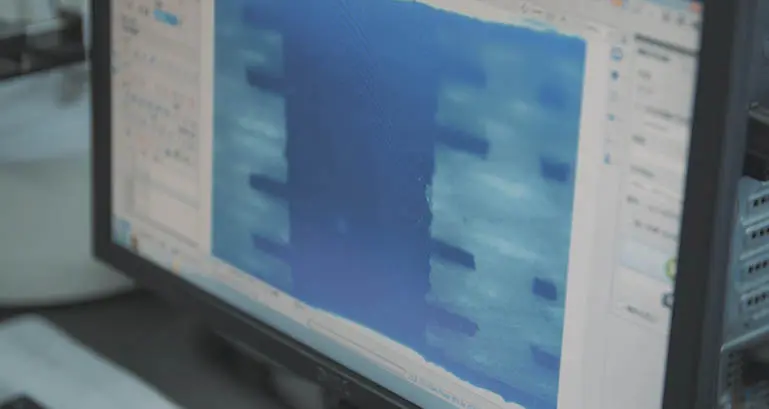
Imagen de la capa externa
¿Cómo crear una imagen de la capa exterior perfecta?
La imagen de la capa exterior es similar a la de la capa interna, pero mucho más compleja por los orificios y la rugosidad de la superficie. ¡Veamos cómo se realiza este espectacular paso del proceso de fabricación de las PCB!
1- PREPARACIÓN Y LAMINACIÓN
Preparación de la superficie: Las placas con un grosor inferior a 500 micrómetros se someten a un proceso de limpieza química, mientras que las más gruesos se someten a uno mecánico mediante cepillos abrasivos. Las placas se calientan para mejorar la adherencia de la película fotorresistente. A continuación, las placas se recubren con un laminado automático en X e Y. La máquina corta directamente el borde.
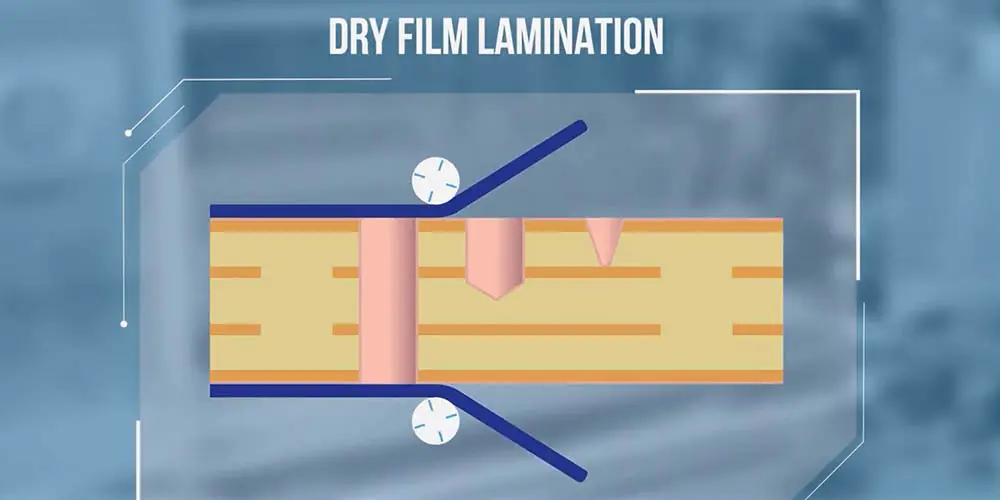
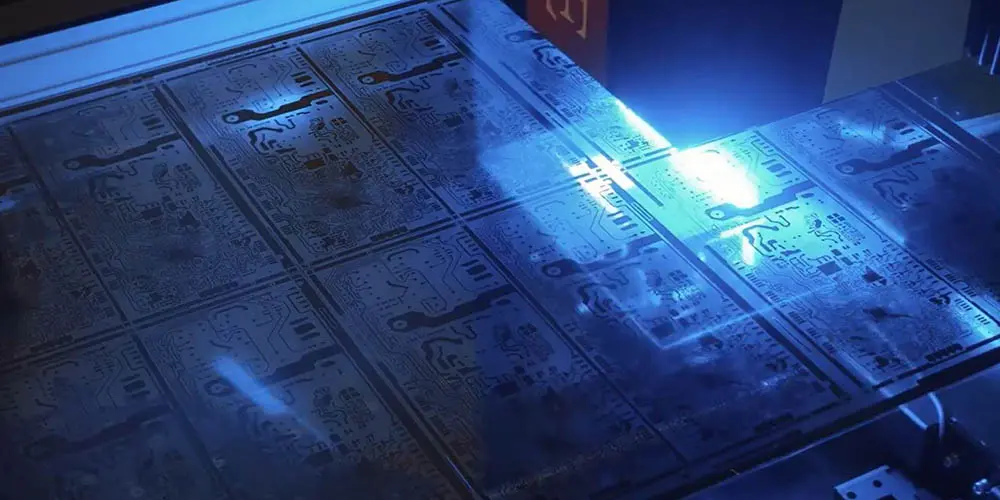
2- REGISTRO E INSOLACIÓN POR UV
En el caso de la insolación semiautomática, el diseño se comprueba de nuevo antes de añadirlo a la máquina. El registro se realiza ópticamente entre los agujeros y los objetivos con 2 o 4 cámaras CCD. Una vez que el panel cumple los criterios de calidad, se aplica un vacío y, a continuación, la placa recibe una ráfaga de luz UV de entre 1 y 20 segundos para polimerizar la fotorresistencia, lo que crea una imagen del patrón del circuito.
3- REGISTRO E INSOLACIÓN LÁSER
Para productos de gama alta y materiales de alta densidad, se utiliza la impresión directa por láser. Esta máquina es totalmente automática, por lo que la carga, el registro con 4 cámaras CCD y la transferencia de la imagen de la capa se realizan en cuestión de segundos. La LDI también es un factor importante cuando se trata de tolerancias estrechas y registros ajustados, como 50 micrómetros o menos.
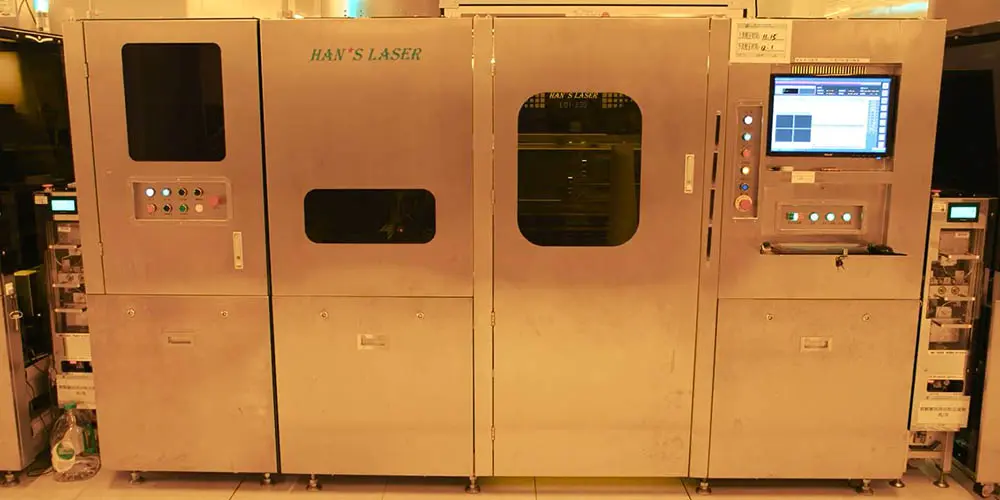
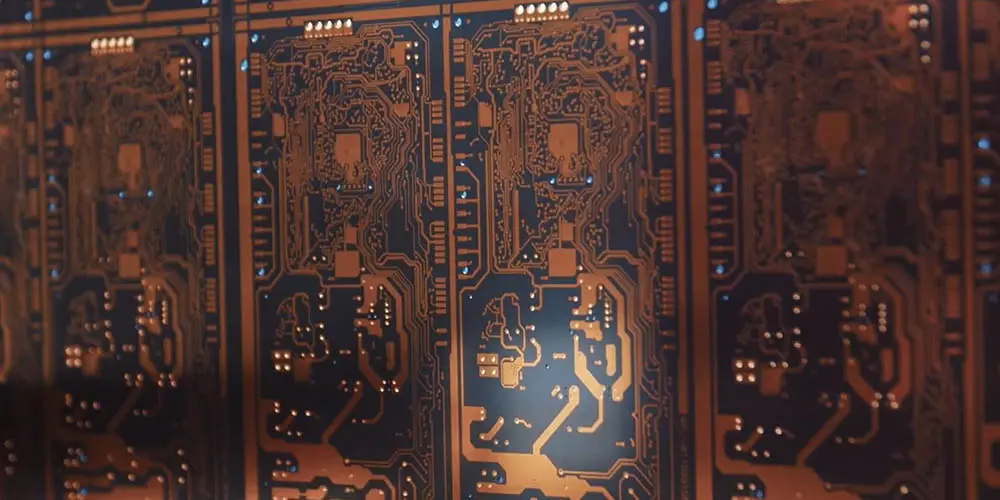
4 - REVELADO
Una vez finalizada la insolación, se retira la protección de la película seca. Las zonas no expuestas a la luz ultravioleta o al láser no están endurecidas y se disolverán en el baño de sodio de revelado, dando a las planchas este bonito color azul. La imagen de la capa exterior ya está impresa, lista para recibir el cobre electrolítico.
5- INSPECCIÓN ÓPTICA AUTOMÁTICA
La inspección óptica automática de las capas exteriores confirmará la ausencia total de defectos, ya sean discontinuidades o cortocircuitos eléctricos. Como en el caso de la capa interior, el diseño original del archivo GERBER sirve de modelo para la cámara óptica. Si la máquina detecta una incoherencia, un técnico evaluará el problema.
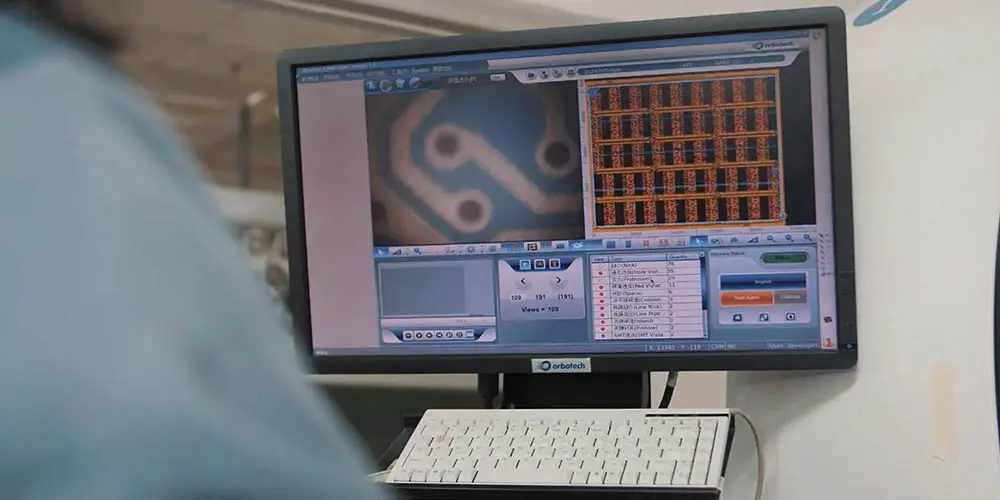
Cobre electrolítico
¿Qué es la deposición electrolítica de cobre?
El cobre puede depositarse electrolíticamente en la placa mediante dos procesos: Proceso de paneles y patrones.
1 - METALIZADO DE PANELES
El cobre se deposita electrolíticamente en toda la superficie, así como en el interior de los agujeros, para mejorar la planitud y la distribución. El cobre electrolítico genera electrólisis, que es un flujo de corriente eléctrica a través de un líquido que provoca cambios químicos. Tras varios baños de 3 min cada uno, se produce la electrólisis, el cobre del baño actúa como ánodo y las placas como cátodo.
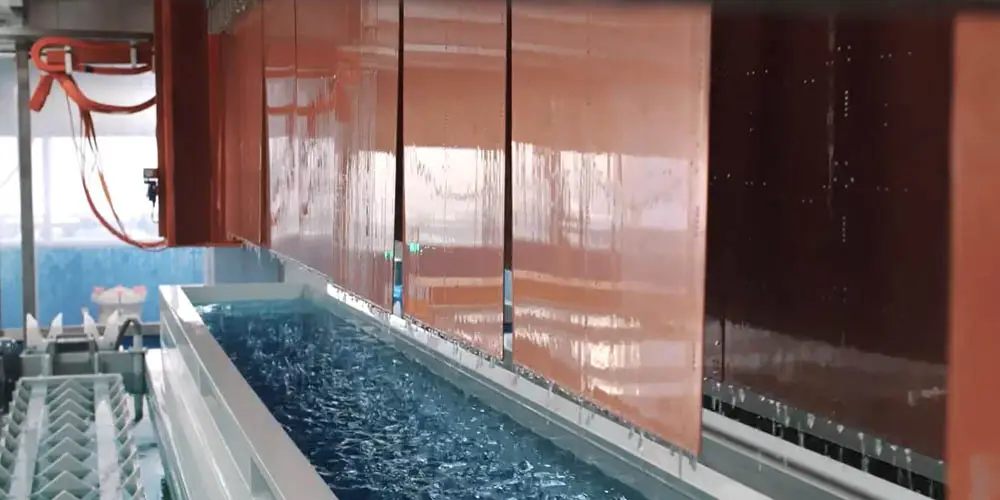
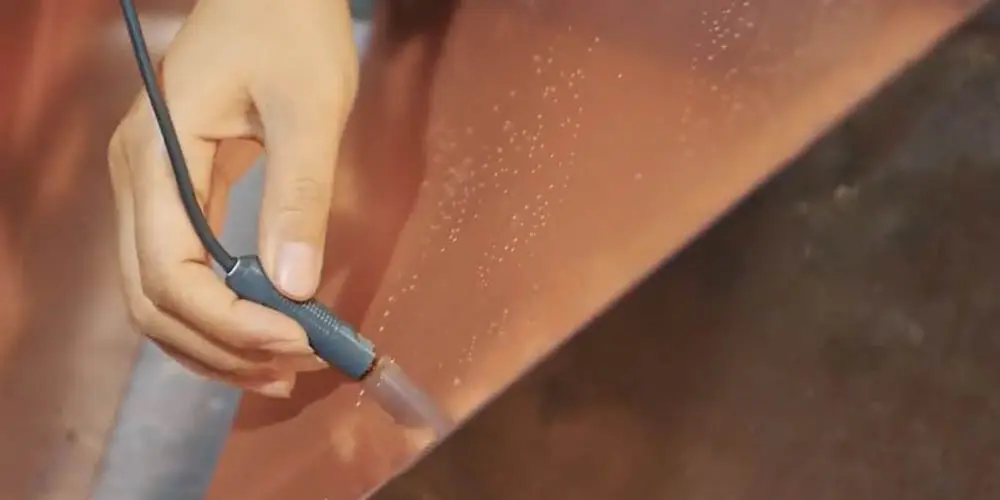
2 - CONTROL
El cobre es ahora más grueso y fiable, con alrededor de 10 a 13 micrómetros de cobre. El siguiente paso para estas placas será la imagen de la capa exterior.
3 - METALIZADO DE PATRONES - DEPOSICIÓN DE COBRE
El cobre se deposita electrolíticamente, pero en cantidades mucho mayores. Para crear una buena conexión y una buena conductividad entre los agujeros, las placas necesitan al menos entre 20 y 25 micrómetros de cobre dentro de los agujeros de las paredes, según las normas IPC. El cobre, que actúa como ánodo, se deposita en las placas durante un baño de 60 minutos.
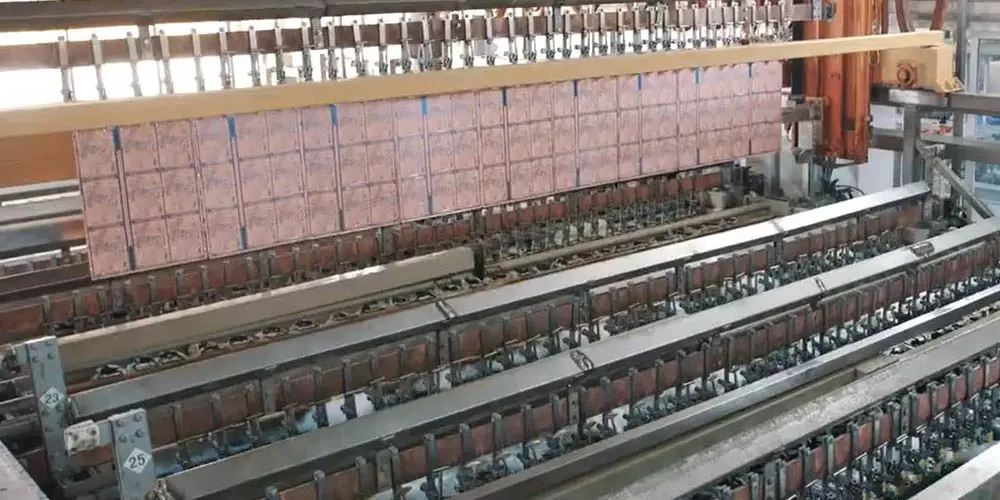
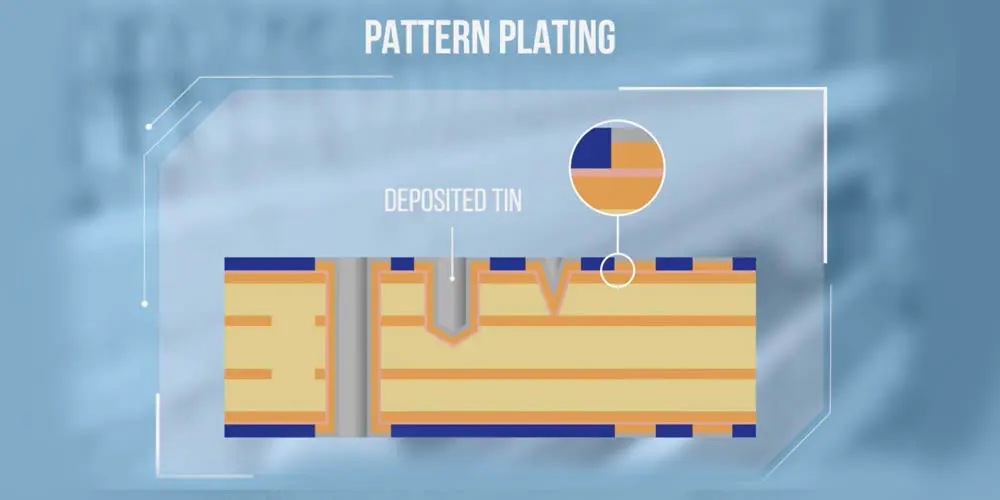
4 - METALIZADO DE PATRONES - DEPOSICIÓN DE ESTAÑO
Tras un baño de aclarado, las placas se sumergen en el estaño electrolítico, que cubre todo el cobre con una capa de entre 1 y 3 micrómetros. El estaño es fundamental para proteger el cobre durante el proceso de grabado.
5 - CONTROL
Una vez cubiertas por completo, se prueban con un método no destructivo para verificar el grosor de la capa.
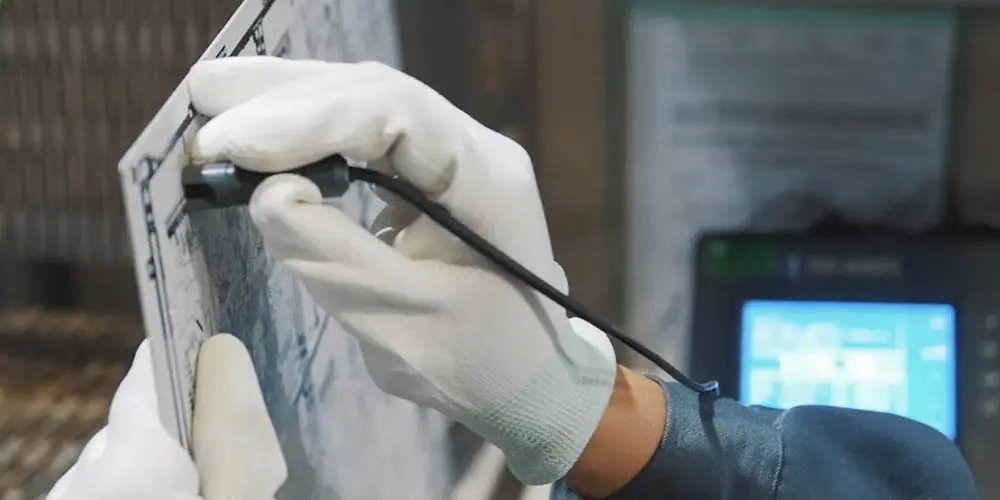
Grabado de PCB
¿Qué es el grabado?
El grabado es un complejo proceso químico que elimina el cobre y el estaño no deseados de las placas.
1 - REMOCIÓN DE LA PELÍCULA
El primer paso comienza con la película seca. Se disuelven todos los residuos y se retira la película, dejando al descubierto el cobre no deseado.
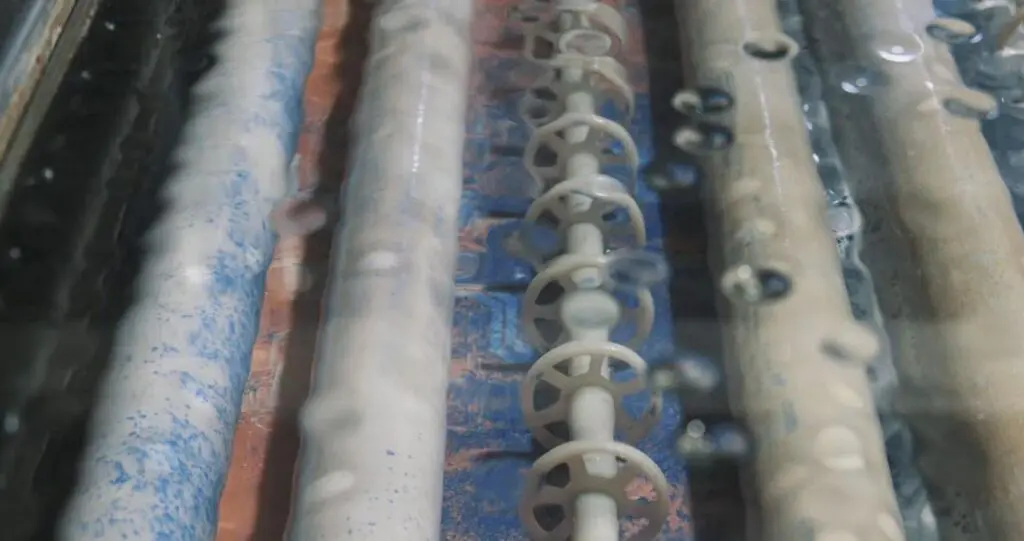
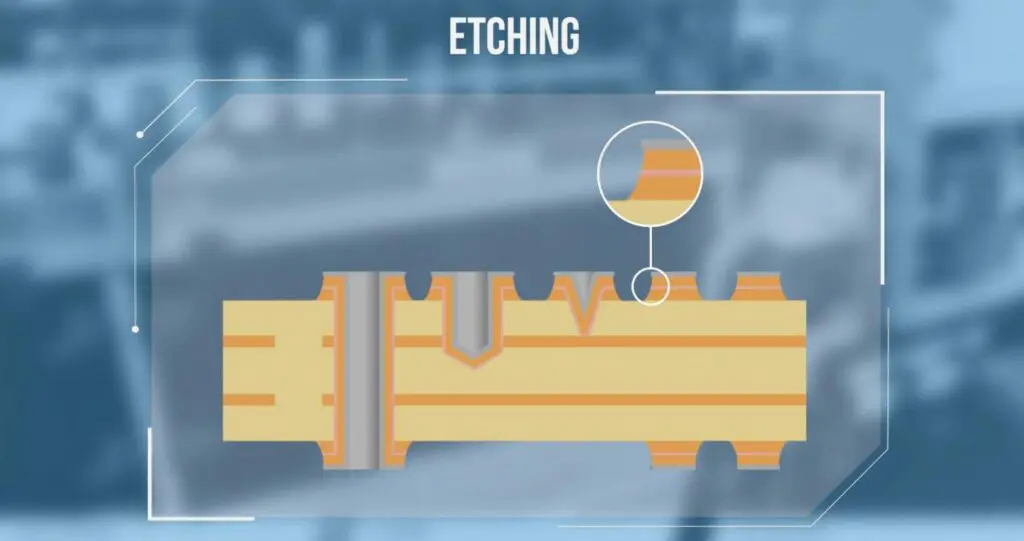
2 - GRABADO
La etapa de grabado se inicia en un baño de una solución química. El desafío consiste en evitar un grabado excesivo o insuficiente que impida obtener una pared recta. En cuanto a la capa interna, se graba el cobre descubierto y se define el patrón. Aquí, el estaño protege el cobre y los agujeros.
3 - REMOCIÓN DEL ESTAÑO
El estaño se elimina químicamente. Las zonas conductoras y las conexiones están ahora correctamente establecidas.
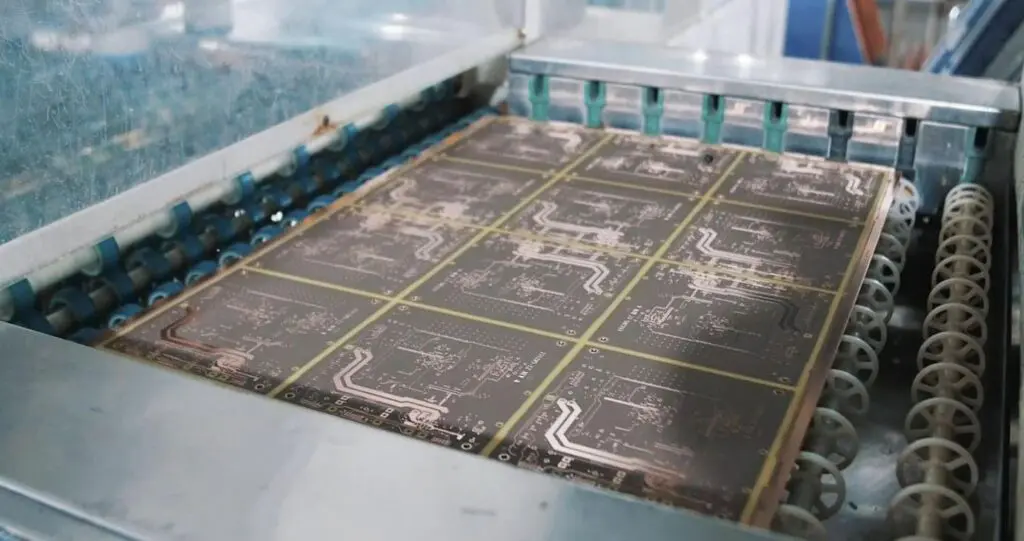
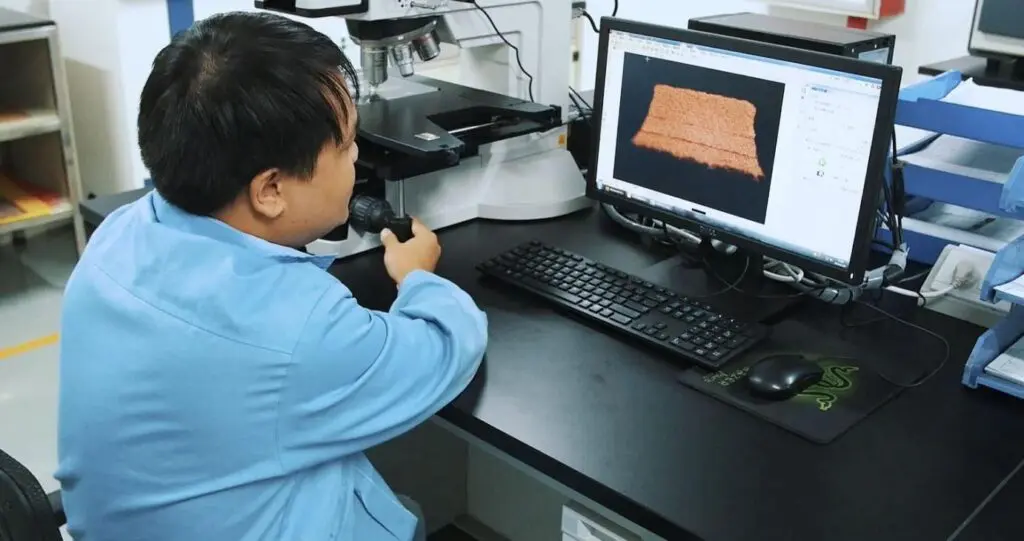
4 - CONTROL
Se realiza una prueba de laboratorio para comprobar el sobregrabado y el subgrabado y asegurarse de que se han eliminado todas las capas de cobre no deseadas, a excepción de la capa de resistencia.
5- INSPECCIÓN ÓPTICA AUTOMÁTICA
La inspección óptica automática se realiza directamente después del grabado y se compara con los datos para poner de manifiesto cualquier incoherencia y garantizar la ausencia de defectos. En algunos casos, un cortocircuito o una discontinuidad eléctrica pueden repararse en esta etapa.
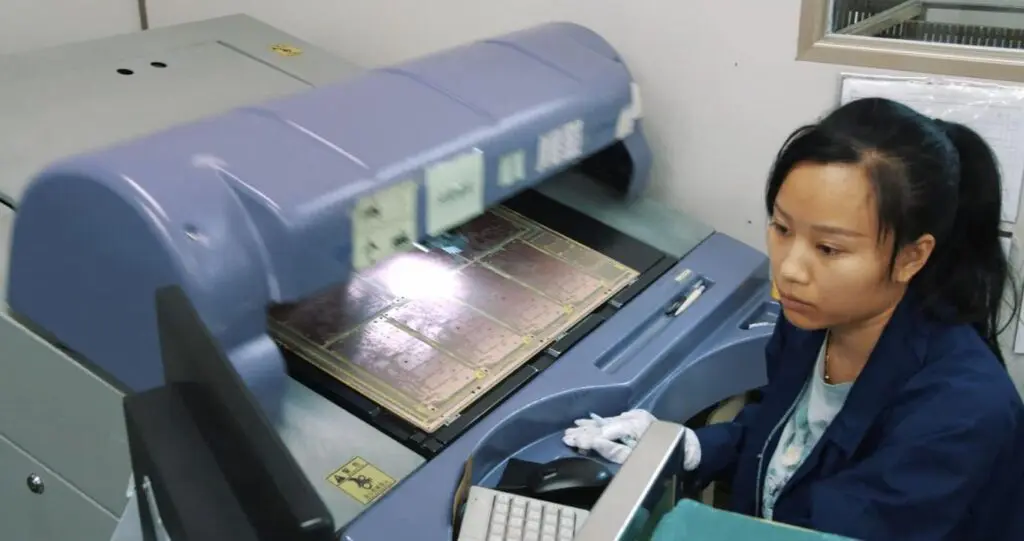
Máscara de soldadura de PCB
¿Por qué necesitan máscaras de soldadura las PCB?
La máscara de soldadura tiene dos beneficios. El primero es evitar la oxidación del cobre y la segunda es tener un aislamiento perfecto entre dos trazas de cobre durante el proceso de montaje. Existen diferentes tipos de máscaras de soldadura para PCB, como el líquido epoxi, el líquido fotosensible (LPI) o el film seco. ¡Profundicemos en ello!
1- REVESTIMIENTO
Existen diferentes formas de aplicar la máscara de soldadura a una PCB: cortina, serigrafía o recubrimiento por deposición de electrospray conforme a las normas IPC. Antes de aplicar cualquier máscara de soldadura, las placas deben limpiarse con un preparado mecánico o químico en una sala limpia sobrepresurizada para evitar que entre polvo del exterior.
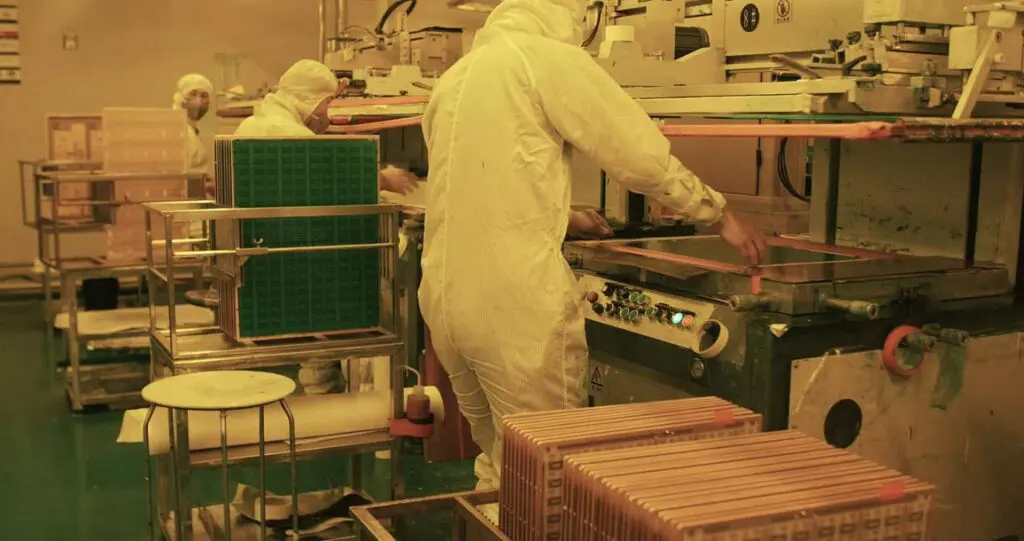
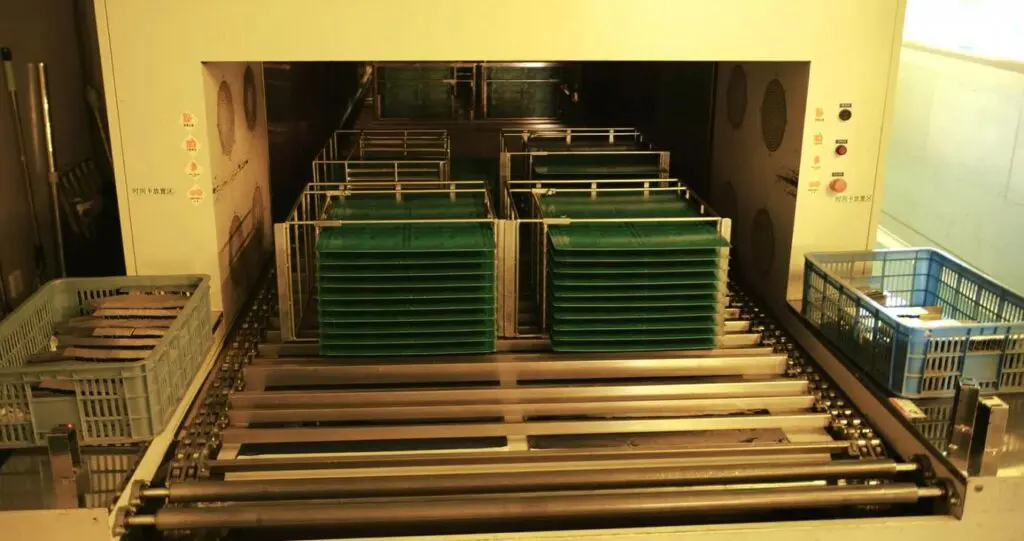
2 - PRECURADO
Una vez que el panel está totalmente cubierto, debe precurarse. Este paso es esencial y elimina todo el disolvente de la tinta. Sin este paso, el registro no se realizará correctamente.
3 -REGISTRO E INSOLACIÓN
Para la máscara de soldadura, la insolación puede realizarse con el registro con 8 cámaras CCD y el diseño. Las placas reciben una ráfaga de luz led durante unos segundos para endurecer la máscara de soldadura donde se ve claramente el diseño. La insolación también puede realizarse mediante LDI (Laser Direct Imaging). Esta vez no es necesario ningún diseño, ya que la máquina realiza la insolación directamente en los lugares seleccionados con haces de luz y endurece el sitio objetivo.
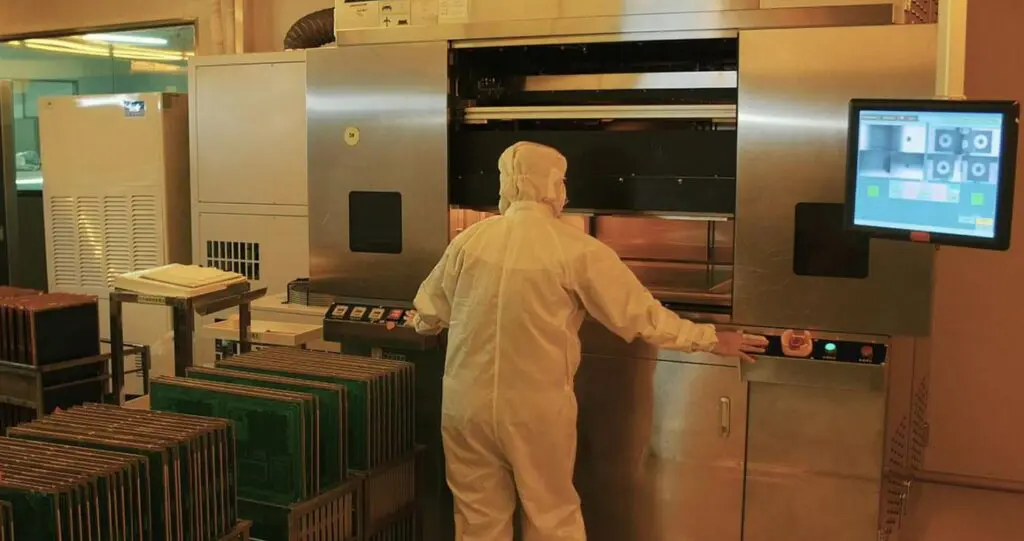
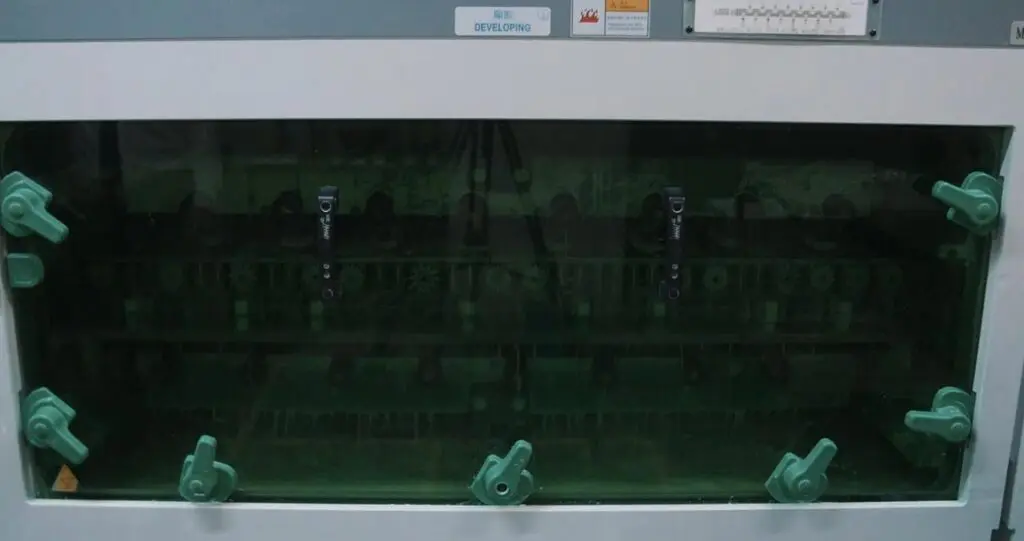
4 - REVELADO
Las partes no protegidas y no endurecidas por la insolación son limpiadas. Aquí, en nuestro ejemplo, se retira la máscara de soldadura alrededor del agujero mecánico pasante.
5- CONTROL Y CURADO
Tras la fase de revelado, se controlan todos las placas. De hecho, la inspección es necesaria para comprobar si hay imágenes defectuosas, restos de tinta en las almohadillas o en los agujeros. Por último, las placas se exponen a alta temperatura durante una hora para curar la máscara de soldadura.
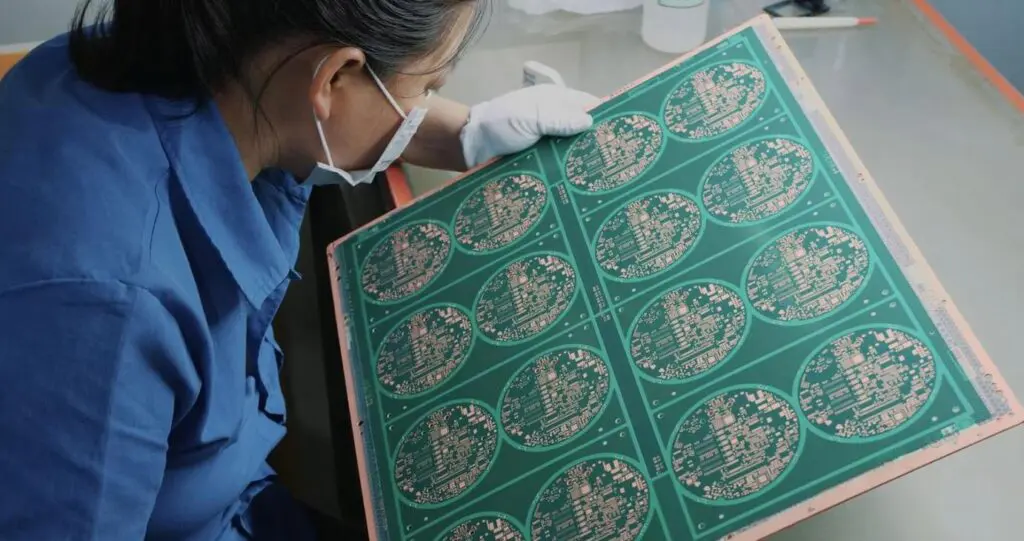
Impresión de leyendas de PCB
¿La impresión de leyendas es importante en una PCB?
El proceso de impresión de leyendas imprime toda la información vital en la placa, como los marcados del fabricante, los números de identificación de la empresa y las etiquetas de advertencia. En este proceso, se utilizan principalmente dos métodos: La serigrafía, también conocida como impresión serigráfica, y DLP para la impresión directa de leyendas con una impresora de chorro de tinta. Parece fácil, pero como cada etapa del proceso de fabricación de las PCB, requiere precisión.
1 - SERIGRAFÍA
Como en la mayoría de las etapas de la fabricación de las PCB, el diseño del archivo GERBER es esencial en el proceso de impresión del patrón de leyenda. El primer método es la serigrafía, también conocida como impresión serigráfica. Ya sean manuales o automáticas, ambas requieren pantallas de poliéster tensadas sobre bastidores de aluminio. Tanto estos como el panel se registran para garantizar una alineación correcta que evite la tinta de impresión en el patrón de cobre y para garantizar que el proceso de soldadura no se vee afectado. La tinta se empuja a través de la plantilla sobre el laminado.
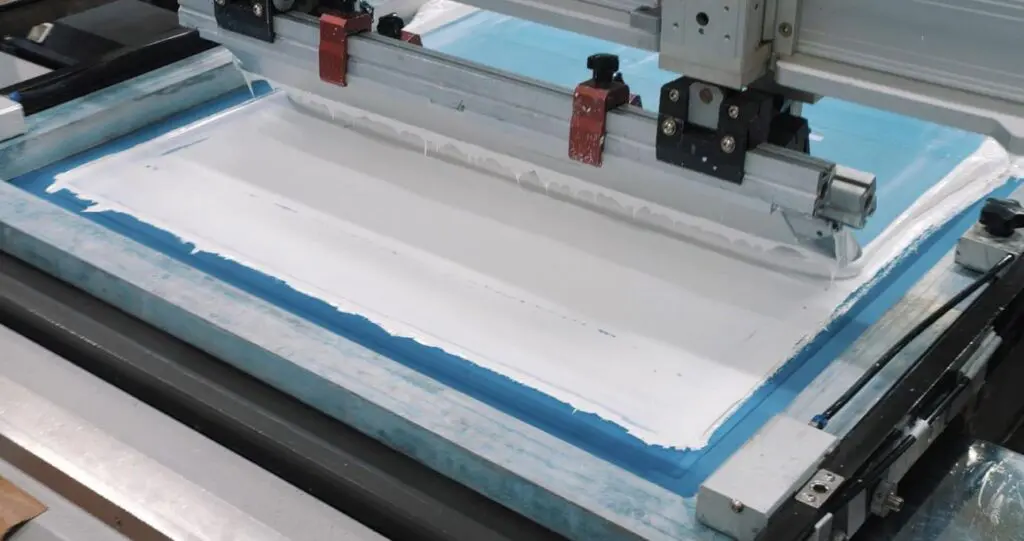
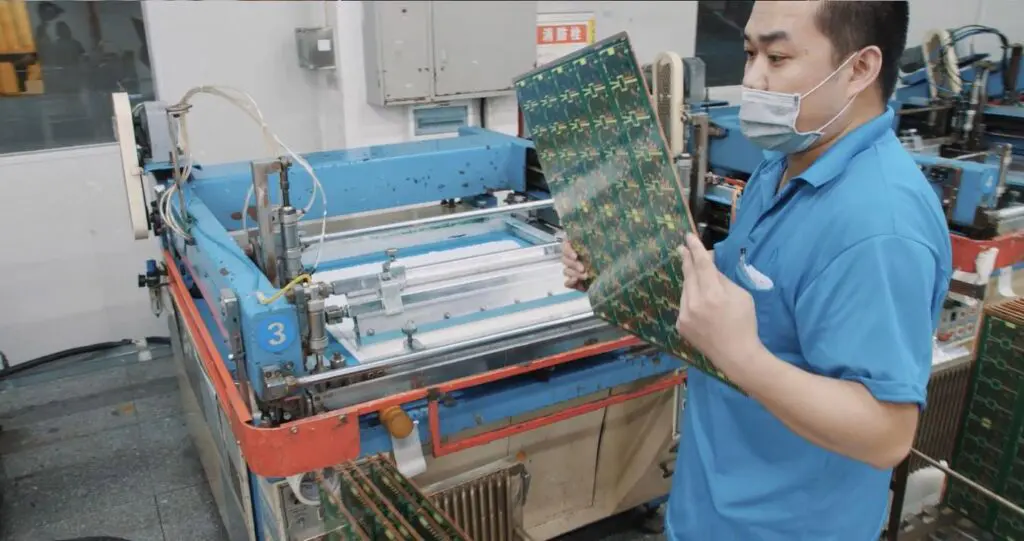
2 - CONTROL
Una vez serigrafiada la PCB con la información correcta, el operario realiza una inspección visual. En caso de defecto, el operario evaluará el problema o retirará la placa del proceso de fabricación
3 - CURING
Si el resultado de la serigrafía es bueno, las placas se curan para endurecer la tinta.
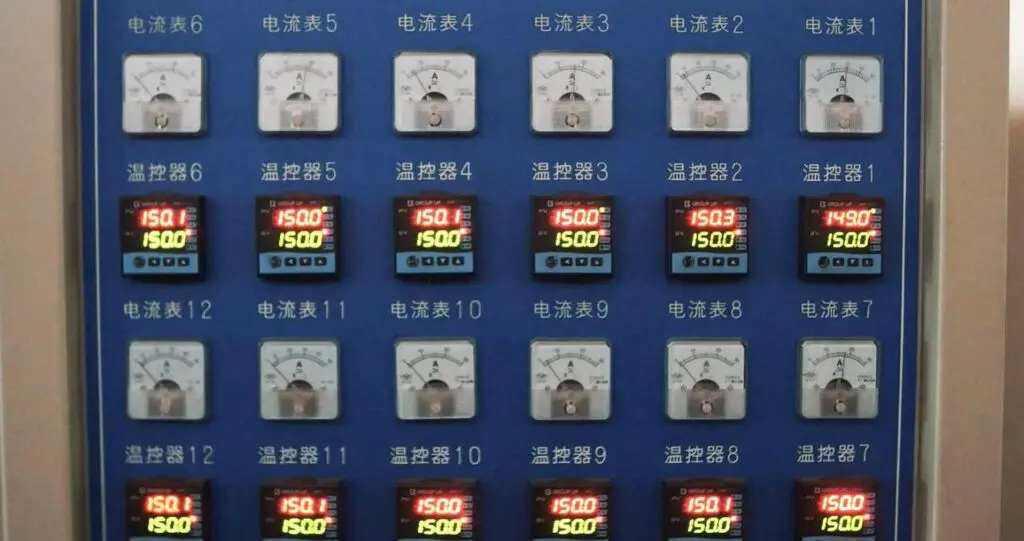
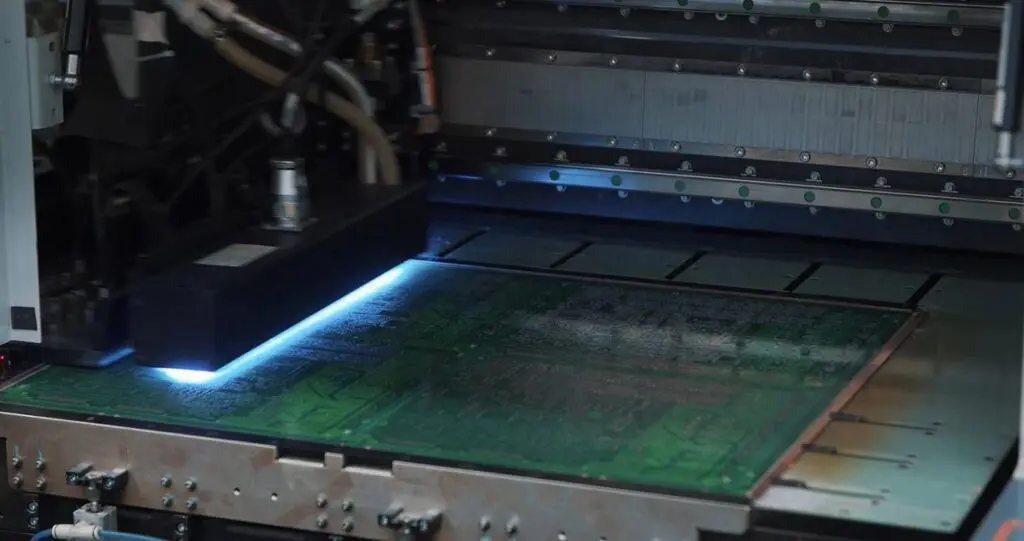
4 - INKJET
El segundo proceso de aplicación del texto de la leyenda funciona como una impresora de chorro de tinta convencional y se conoce como DLP o impresión directa de leyendas. El registro lo realiza automáticamente la máquina. La impresora de chorro de tinta pulveriza gotas de tinta sobre el panel para generar la imagen. Estas gotas de tinta se curan directamente con luces UV.
5 - CONTROL
El operador también realiza un control visual para asegurarse de que la leyenda se imprime correctamente. A pesar de contar con equipos más modernos, la DLP solo es preferible para la creación de prototipos y pequeños volúmenes, mientras que la serigrafía es mucho más rápida y se utiliza para la fabricación en serie.
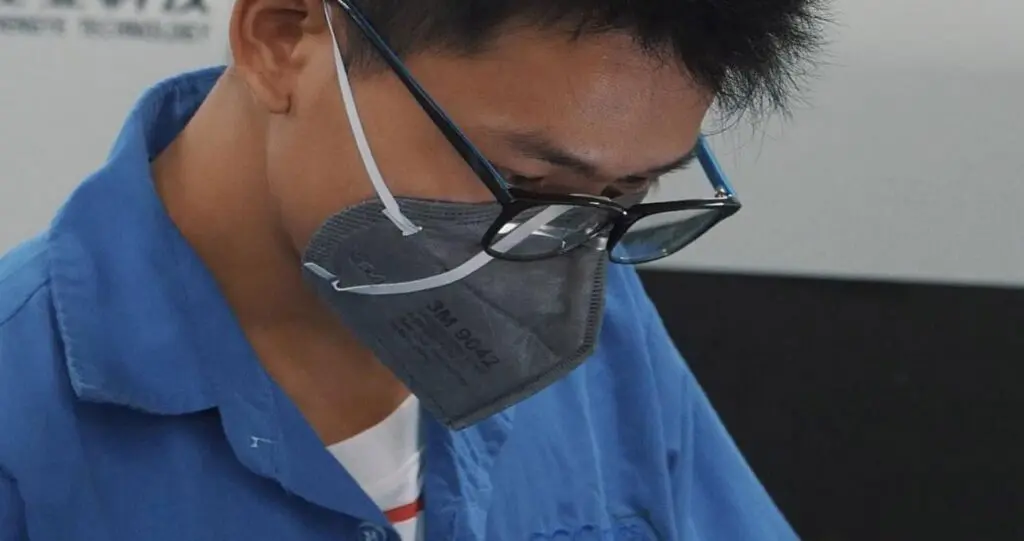
Acabado de superficie de la PCB
¿Qué acabados de superficie hay disponibles?
El acabado de superficie es un revestimiento entre un componente y una PCB desnuda. Se utiliza principalmente por dos razones: Garantiza la soldabilidad durante la etapa de poblado y protege el cobre de la oxidación.
1 - OSP
OSP son las siglas de Organic Solderability Preservative (conservante orgánico de soldabilidad). Es un acabado de superficie a base de agua, respetuoso con el medio ambiente. Luego, las placas se limpian antes de pasar por los baños, lo que proporciona una excelente superficie plana. Este rápido proceso no requiere mucho equipo, lo que lo convierte en un acabado de superficies rentable. El OSP tiene una vida útil corta y puede ser delicado al manipularlo. Por consiguiente, el proceso de enrutamiento se realiza antes de la aplicación del acabado superficial. En resumen, el acabado superficial OSP es respetuoso con el medio ambiente, proporciona una superficie plana, es una solución rentable que se puede reactivar. También hay inconvenientes, como la corta vida útil, puede ser sensible durante la manipulación y puede exponer el cobre durante el ensamblaje final.
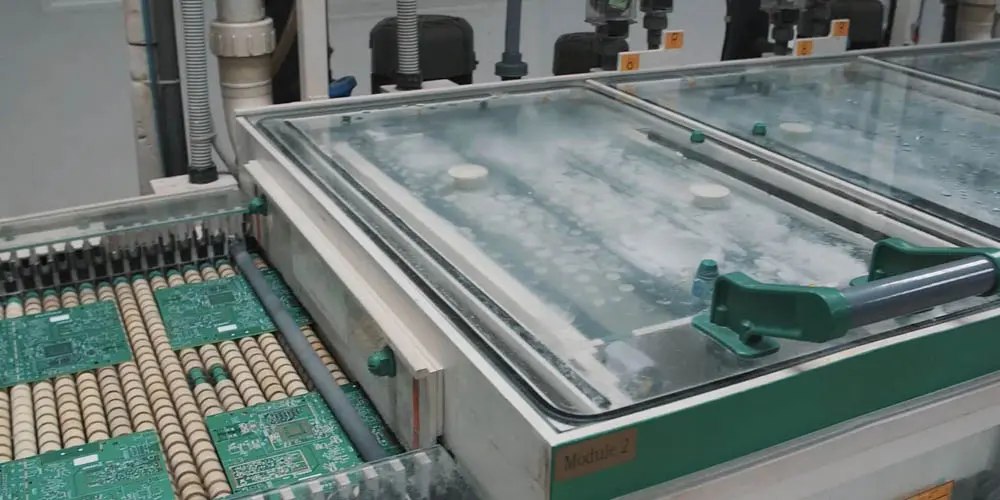
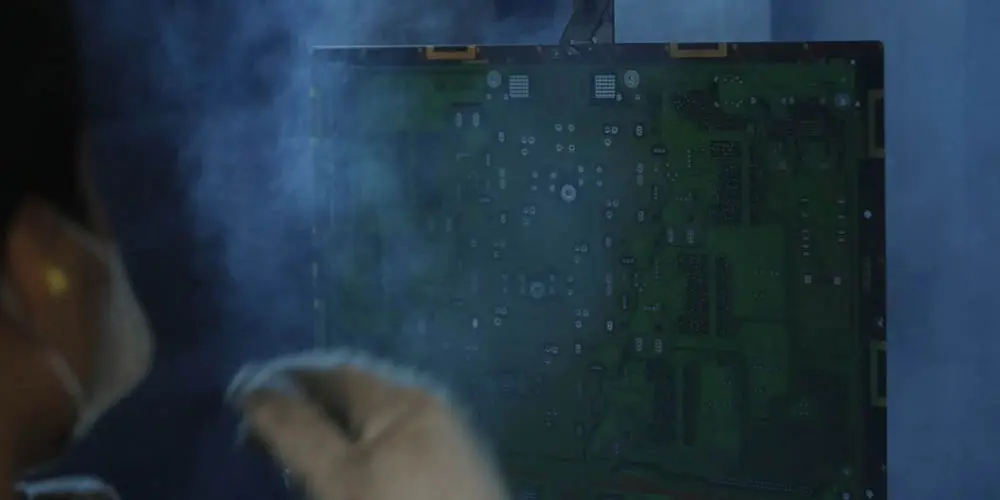
2- HASL SIN PLOMO
HASL sin plomo es la abreviatura de Hot Air Solder Leveling (Nivelación de soldadura por aire caliente), que fue uno de los acabados más populares hasta hace unos años. Aunque es resistente, su bajo precio también se debe sus limitaciones. Durante esta aplicación, todo el panel se somete a un micrograbado para limpiarlo y, a continuación, se le aplica una capa de fundente para facilitar la adherencia del acabado superficial. Posteriormente, la placa se sumerge en soldadura líquida de estaño y se retira utilizando dos cuchillas de aire que soplan aire comprimido caliente sobre la superficie de las placas. La solución sin plomo es una ventaja indiscutible para los productos de alta fiabilidad. Sin embargo, con cada vez más placas HDI, este proceso proporciona superficies irregulares y no es adecuado para componentes de paso fino. En resumen, el acabado superficial HASL sin plomo es una tecnología ampliamente disponible, una solución de bajo coste y buena durabilidad. También tiene inconvenientes, como la superficie, que puede ser irregular, no es adecuada para componentes de paso fino y el proceso puede suponer un estrés térmico para las placas.
3 - ENIG
ENIG son las siglas de Electroless Nickel Immersion Gold (níquel químico por inmersión en oro). Este proceso requiere que la cinta cubra los contornos del circuito para evitar la deposición excesiva de oro y porque la ENIG es un proceso costoso de acabado. El panel se sumerge en varios baños, primero se electrodeposita una capa de 3-6 micrómetros de níquel para aumentar la adherencia. A continuación, también se electrodeposita en el panel un mínimo de 0,05 micrómetros de oro. Un acabado por inmersión proporciona una excelente planitud y el uso de oro proporciona gran soldabilidad. En resumen, la superficie ENIG es ideal para pegar, tiene una gran soldabilidad, proporciona una superficie plana y tiene una buena vida útil. También tiene inconvenientes, principalmente, el hecho de que esta superficie es un proceso complejo y que no es una solución rentable.
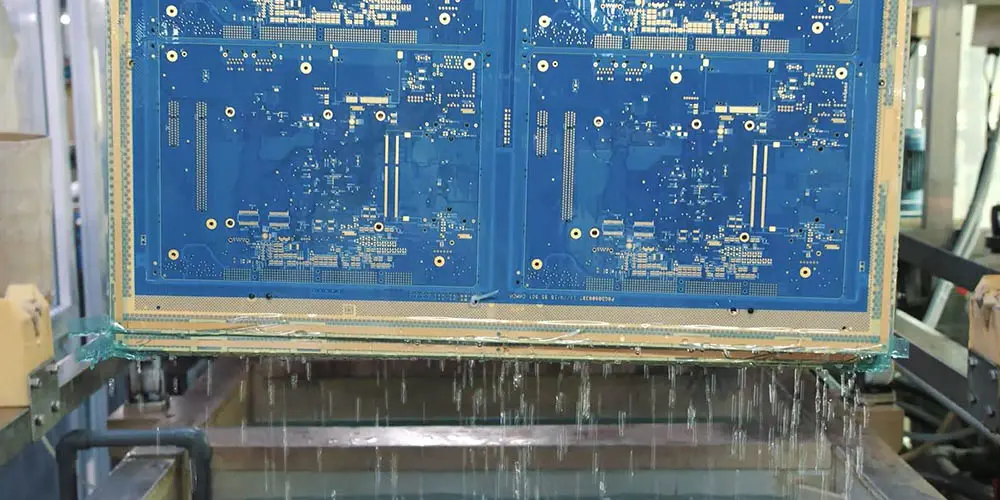
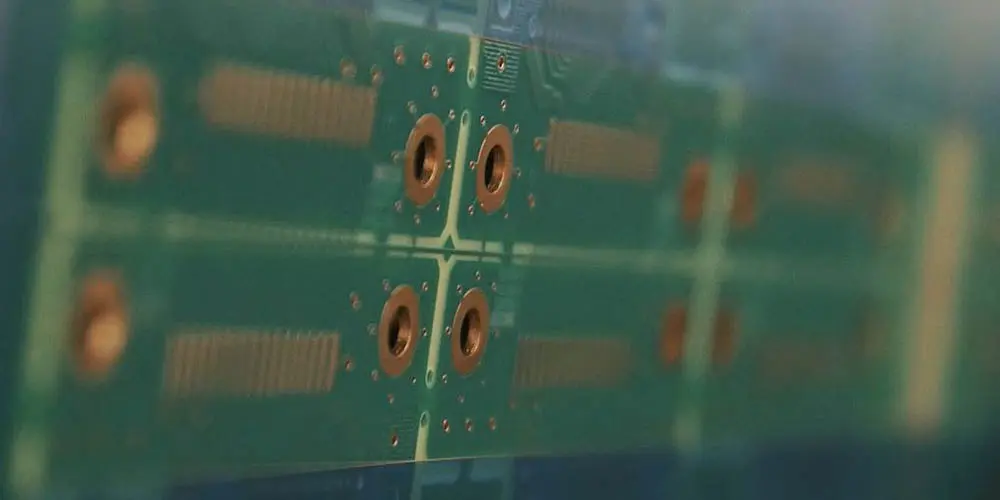
4- CHAPADO EN ORO DURO
Para el chapado en oro duro, se cubre todo el panel con cinta adhesiva. Se retira únicamente la parte que requiere la aplicación de un acabado de superficie. A diferencia de la ENIG, en este caso el grosor del cobre puede variar controlando la duración del ciclo de metalizado. El níquel se electrodeposita en primer lugar y, a continuación, se deposita el oro según lo que desee del cliente. El grosor del oro proporciona una excelente vida útil, pero también una de las opciones de acabado de superficies más costosas. En resumen, el acabado de superficie de chapado en oro duro tiene propiedades mecánicas, una excelente vida útil y proporciona una superficie plana. También tiene inconvenientes, como el elevado coste, la mala soldabilidad y la complejidad del proceso.
5 - ESTAÑADO POR INMERSIÓN
El estañado por inmersión es un depósito de acabado metálico.
Las placas se sumergen en varios baños químicos para crear la mejor adherencia para el estaño. La inmersión proporcionará una planitud perfecta y el estaño protegerá mejor el cobre debajo. Es una opción rentable, pero la fuerte afinidad entre el estaño y el cobre puede dar lugar a la formación de burbujas de estaño.
El acabado superficial de estaño por inmersión está ampliamente disponible, proporciona una superficie plana, es una solución rentable, tiene una buena vida útil y re puede reprocesar.
También tiene desventajas, como que el reprocesamiento es limitado, la manipulación puede ser delicada y existe la posibilidad de que el estaño se desgaste.
ICAPE Group exige específicamente un producto de acabado de alta tecnología en su asociación con fábricas con sede en Alemania a fin de realizar el estañado por inmersión que se adapte a las expectativas del sector de la automoción alemana.
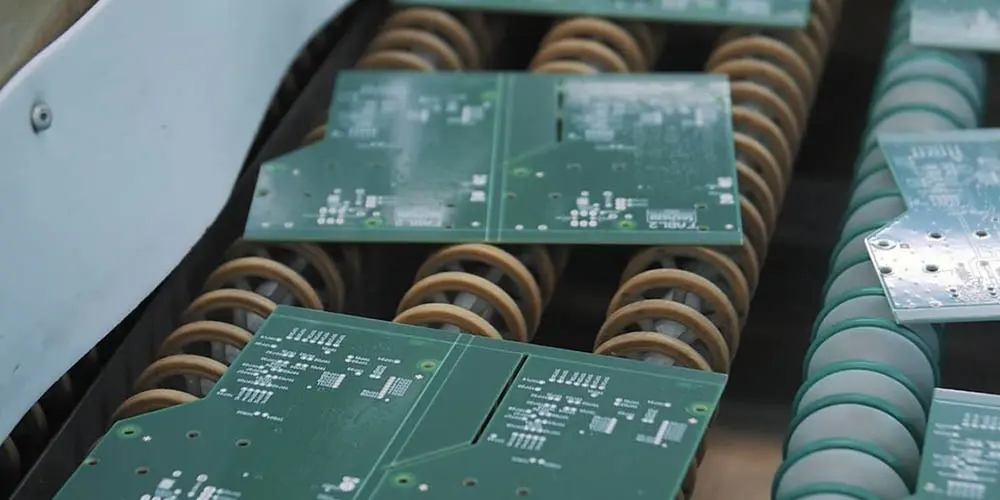
Enrutamiento de PCB
¿Qué es el enrutamiento de PCB?
El objetivo del proceso de enrutamiento, también conocido como perfilado, es cortar cada placa de circuito del panel de producción. De hecho, aunque todas las placas de circuitos estén en el mismo panel, no todas pertenecen necesariamente al mismo cliente
1 - PREPARACIÓN
El operario apila hasta 4 paneles de la misma forma que para el proceso de perforación. En este caso, el proceso de enrutamiento requiere una fresadora y brocas con un número diferente de cabezales: 1, 2, 4 o 6 cabezales.
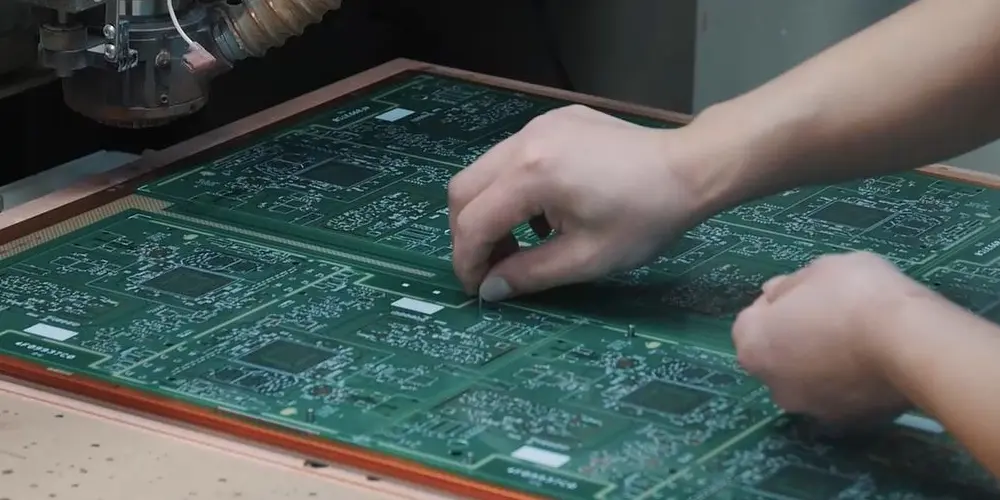
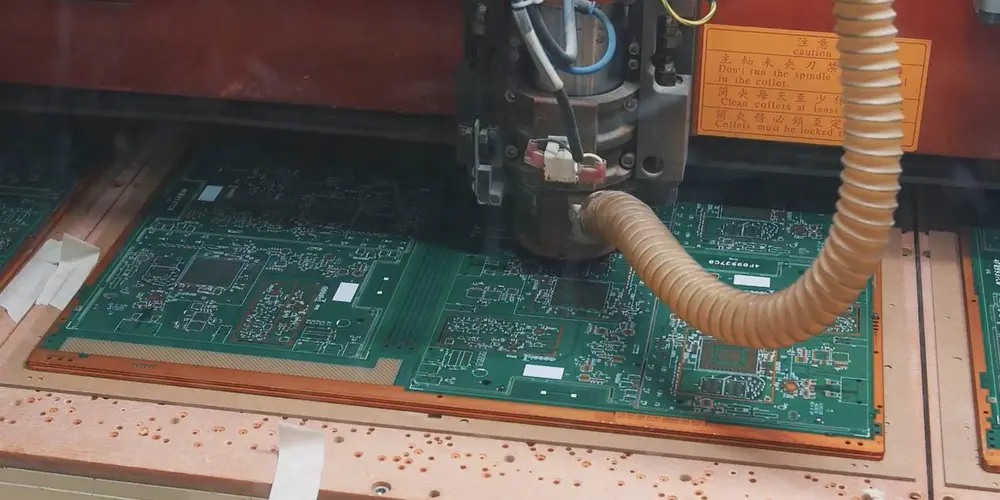
2 - ENRUTAMIENTO
Durante este proceso, se crean los contornos interiores y exteriores de la PCB. Al tiempo, se limpian las placas para garantizar que no quede polvo como resultado de esta operación. Al final del ciclo, el operario retira todas las piezas de la mesa y las placas de circuitos quedan separadas. En función de las necesidades del cliente, las placas también se pueden fresar sin separarse
3 - CONTROL
El operario supervisa las dimensiones del proceso de fresado con una cámara óptica para asegurarse de que los contornos interiores y exteriores se han fresado correctamente y no han afectado al circuito.
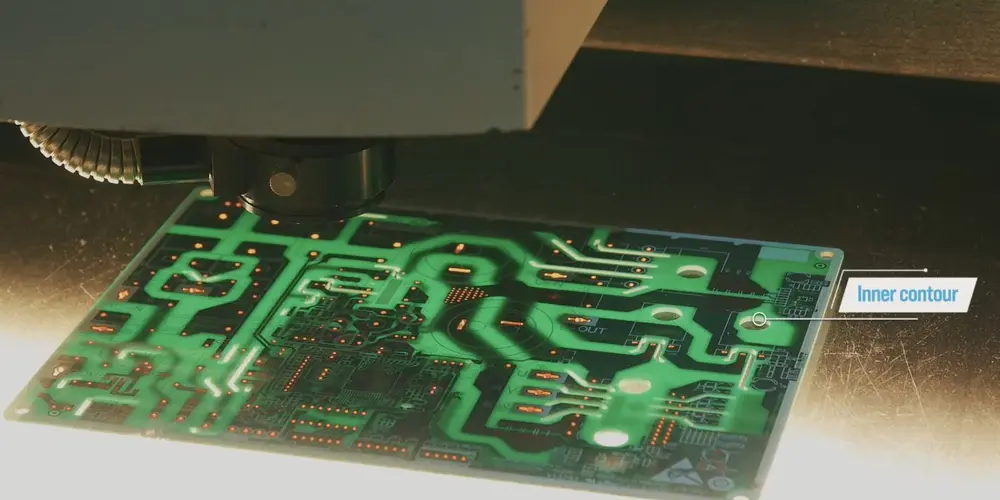
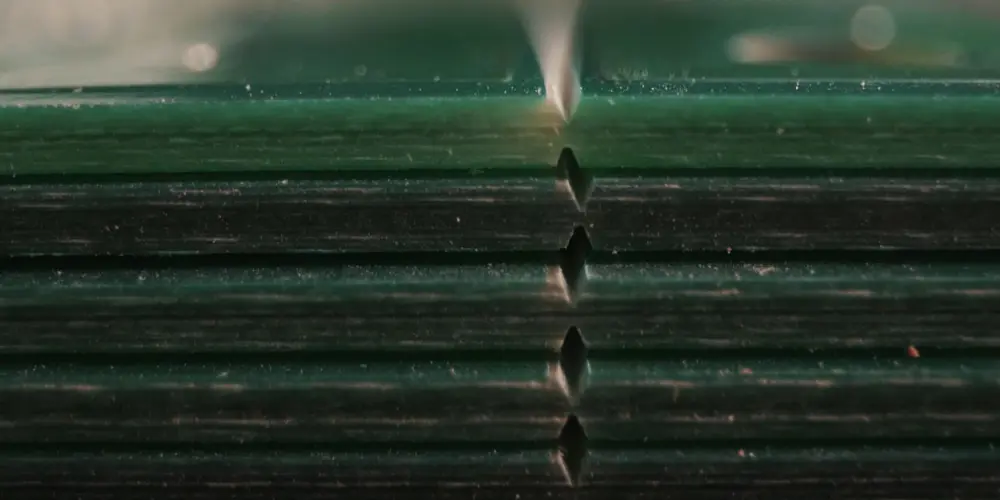
4 - CORTE EN V
Después del fresado, se utiliza el corte en V para precortar las PCB en el panel del cliente, de modo que las placas puedan separarse después de la fase de poblado. Este es el principal objetivo de este paso. A continuación, las placas se desprenden fácilmente.
5 - CONTROL
Una vez finalizado, se realizan controles con un comprobador de corte en V para medir la profundidad de corte en V según el archivo GERBER.
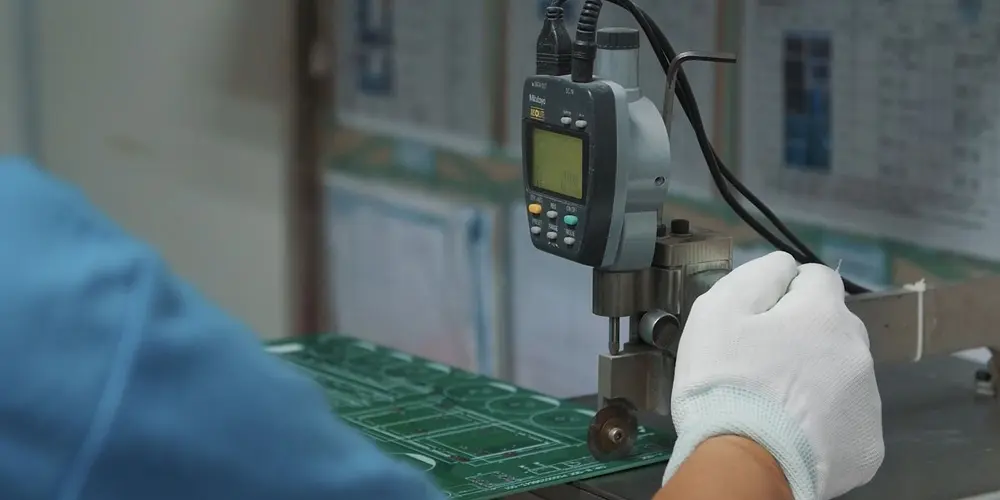
Pruebas eléctricas
¿Cómo controlar los cortocircuitos y las discontinuidades en una PCB?
Estas pruebas se realizan para garantizar que no haya cortocircuitos ni discontinuidades en las placas de circuitos. Hay dos tipos de máquinas con diferentes ventajas: la «sonda volante» y la «cama de clavos».
1 - SONDA VOLANTE
El fichero GERBER es leído por la máquina, el operario coloca las placas en panel o solas. A continuación, los 4, 6 u 8 cabezales, distribuidos en cada lado, comienzan su trabajo: enviar una carga eléctrica a los circuitos, mientras que, cada almohadilla de contacto se toque continuamente para asegurarse de que no hay circuito abierto o cortocircuito. En este caso, un operador intervendrá para resolver el problema.
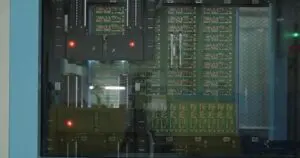
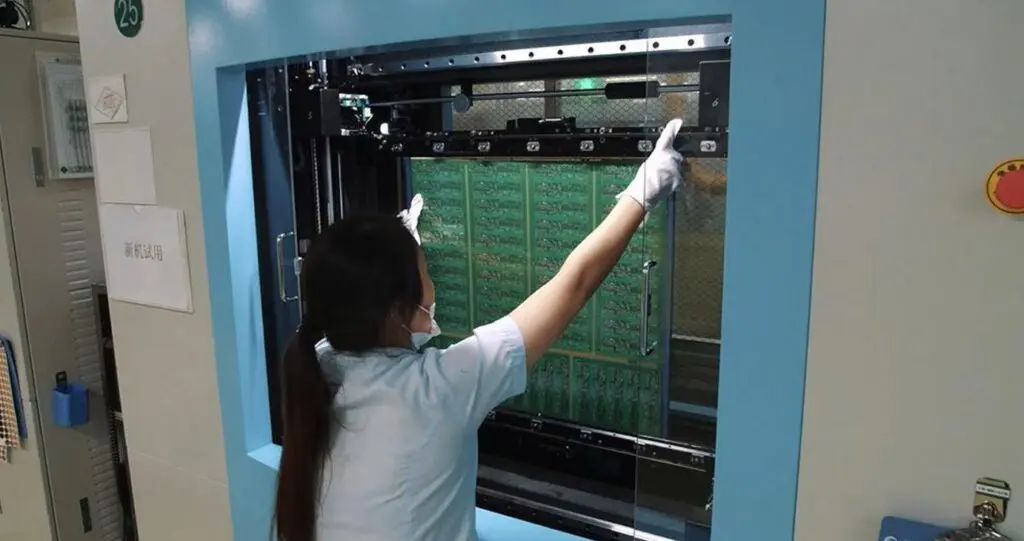
2 - VENTAJAS E INCONVENIENTES
El equipamiento es rentable, lo más habitual es utilizarlo para prototipos y series pequeñas. Además, es adecuado para PCB HDI, pero la principal limitación es cambiar las placas de circuito manualmente cada vez, lo que extiende mucho el funcionamiento en el ciclo.
3 - CAMA DE CLAVOS
La prueba de cuadrícula universal, también conocida como «cama de clavos», requiere un banco de ensayos. Este se diseña a partir del archivo GERBER, por lo que es diferente para cada PCB. El operario debe colocar numerosos pines de distintos tamaños para cubrir toda la zona de pruebas. ¡La preparación es extremadamente cara y tediosa! Los agujeros se alinean con los puntos de prueba de la PCB y todos los puntos de prueba se verifican al mismo tiempo, lo que lo hace muy rápido y fiable.
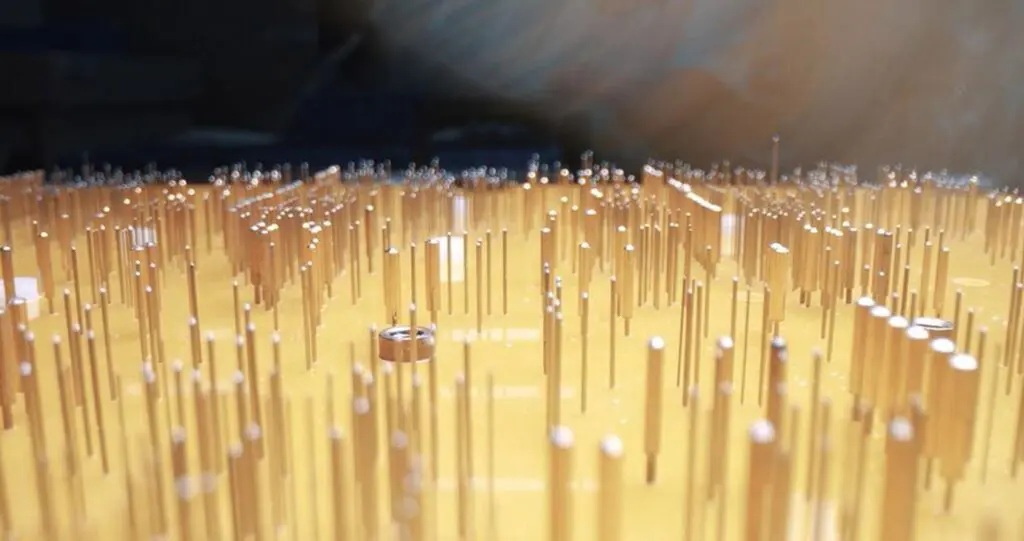
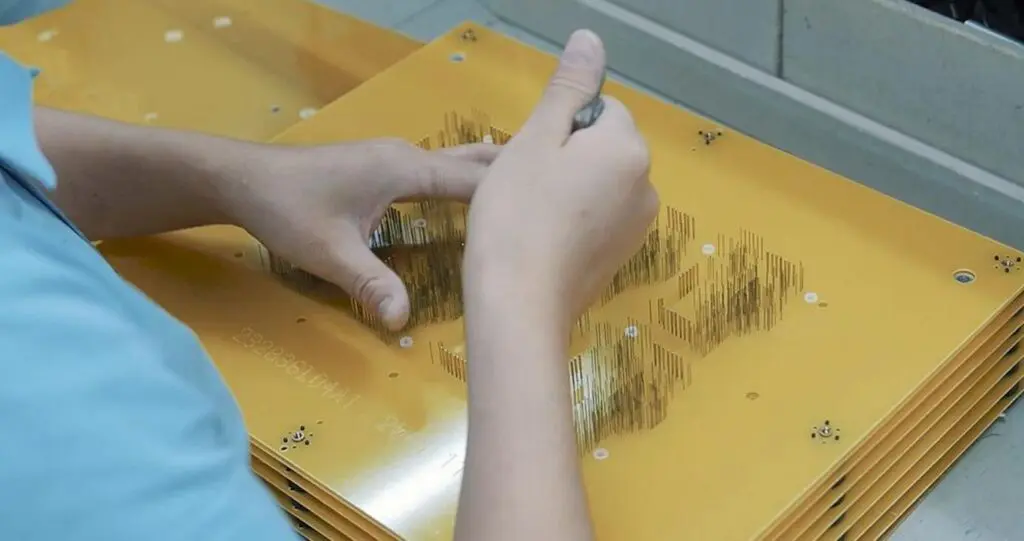
4 - VENTAJAS E INCONVENIENTES
En cuanto a la Sonda volante, el Cama de clavos tiene sus pros y sus contras. Esta prueba eléctrica es perfecta para la producción en masa por su velocidad de procesamiento entre cada PCB. No obstante, hay que tener en cuenta el costoso de equipamiento, la tediosa preparación y los límites de densidad.
5 - PRUEBAS REALIZADAS
Ahora que la prueba eléctrica se ha finalizado, estamos seguros de que el circuito es correcto. A continuación, se realizará la inspección final.
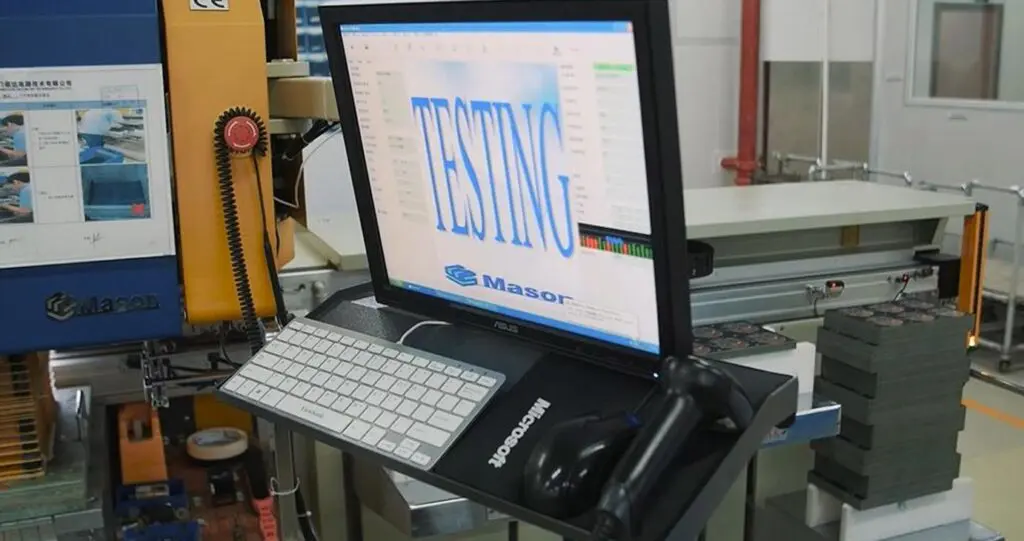
Inspección final
¿Hasta qué punto son importantes las inspecciones finales de las PCB?
Se trata de una etapa fundamental en el proceso de fabricación. En ella, el proveedor controlará toda la placa, desde el aspecto funcional hasta el estético. Lo verifica todo comparándolo con los requisitos de ICAPE y, por supuesto, incluso con las normas IPC. Además, también disponemos de un controlador ICAPE in situ que controlará todo durante el proceso, así como antes del embalaje y el envío.
1 - INSPECCIÓN AUTOMÁTICA
Cada placa pasa por la máquina de inspección visual automática (AVI). Esta máquina verifica la PCB de forma más rápida que los ojos humanos y detecta incoherencias en comparación con el archivo GERBER. A continuación, la placa se coloca en el verificador automático de agujeros para detectar si algunos agujeros tienen tamaños irregulares.
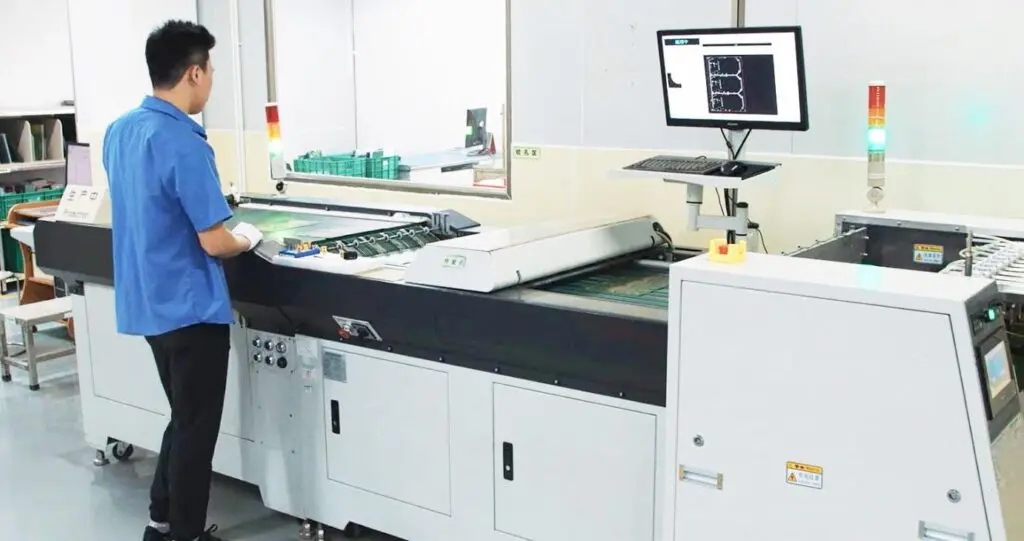
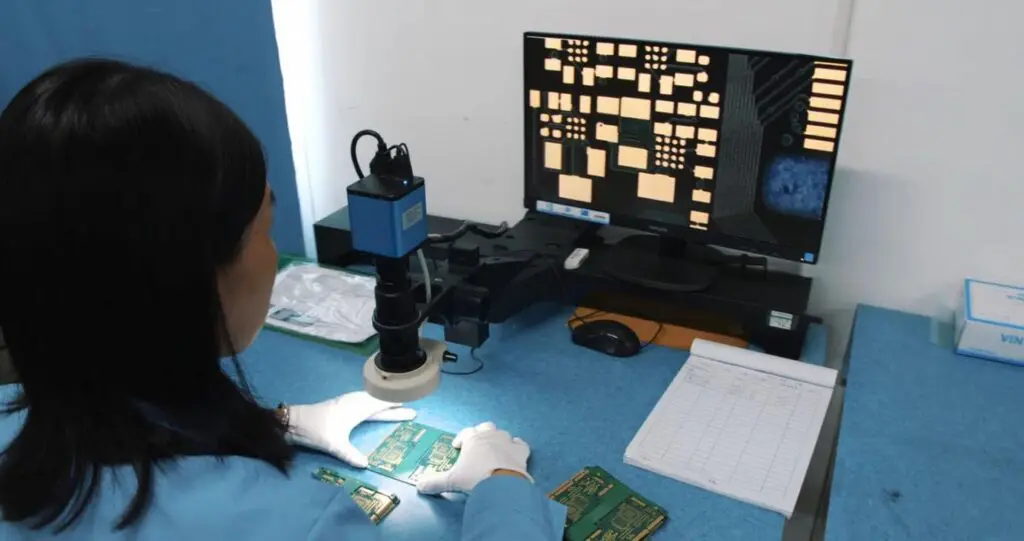
2 - INSPECCIÓN DEL PROVEEDOR
Todos las placas son revisadas visualmente por inspectores muy atentos para controlar cada especificación. Las evaluaciones realizadas por nuestras fábricas asociadas son supervisadas por inspectores internos de ICAPE Group que están constantemente presentes en estas fábricas.
3 - EQUIPOS CONTROL DE CALIDAD Y ASEGURAMIENTO DE CALIDAD
Nuestros equipos de Control de calidad y de Aseguramiento de la calidad se desplazan a nuestras fábricas asociadas para realizar ellos mismos los controles finales. El aseguramiento de la calidad está orientado a los procesos y evita los defectos garantizando los procesos empleado para gestionar y crear PCB entregables. El Control de calidad está orientado al producto y determina que el resultado final sea el esperado.
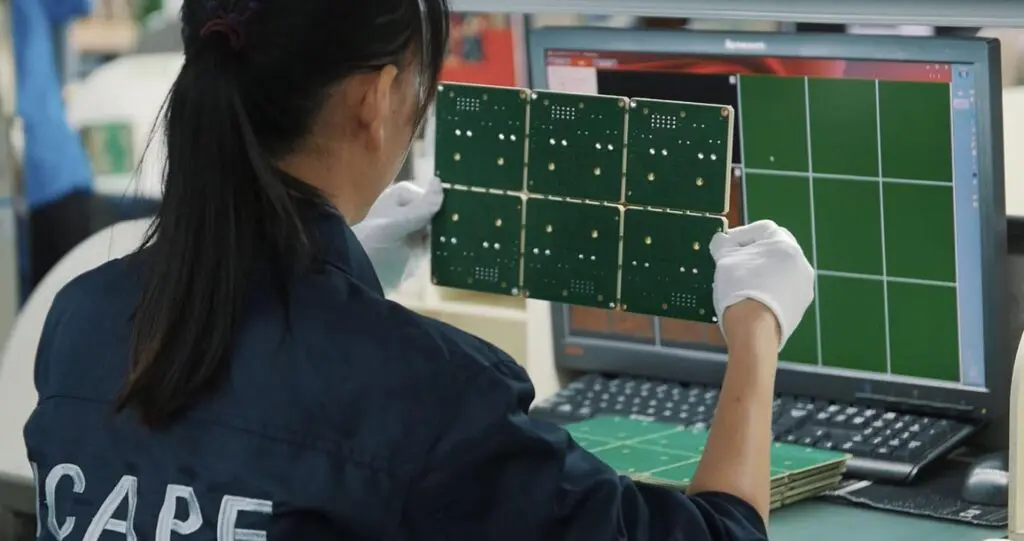
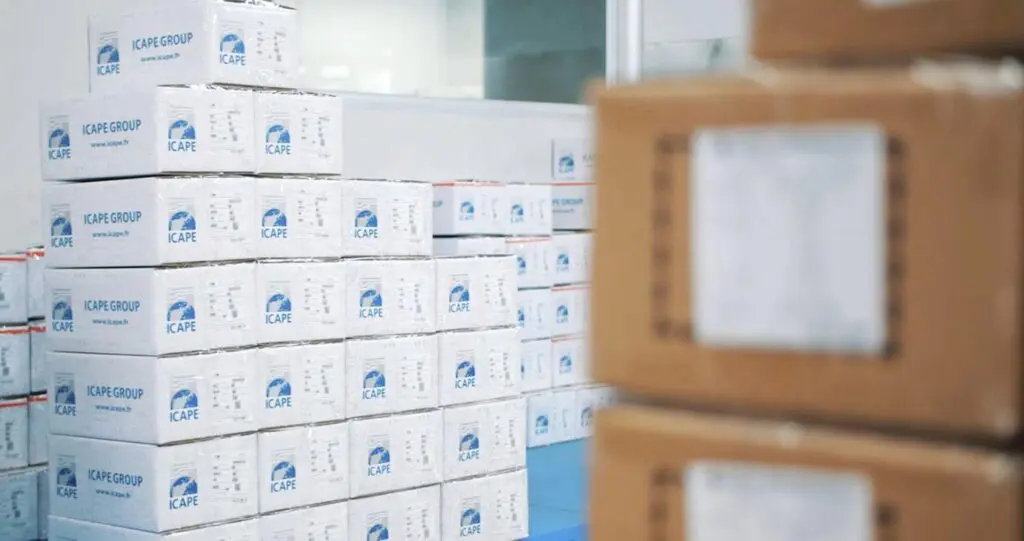
4 - LABORATORIO ICAPE
Nuestro laboratorio es capaz de realizar numerosas pruebas, como el análisis de micro secciones, el control del depósito de cobre en la superficie del agujero, la verificación de los residuos de contaminación iónica, el control del metalizado de la superficie, la rugosidad, el control de la impedancia de la PCB y la integridad de la señal. Además, se pueden realizar pruebas de envejecimiento y choque térmico en la placa de circuito impreso para verificar su fiabilidad en condiciones adversas.
5 - EMBALAJE
Una vez finalizada la inspección, las placas se lavan con agua desionizada para eliminar el polvo y los contaminantes que puedan haber quedado en la PCB. A continuación, las placas se envasan al vacío cuidadosamente. Se añade la etiqueta de envío y ya están listas para su envío. Las placas se pueden enviar según el modo de transporte solicitado, puede ser DDP (entrega derechos pagados), DAP (entrega en un punto) ya sea por avión, tren o barco.
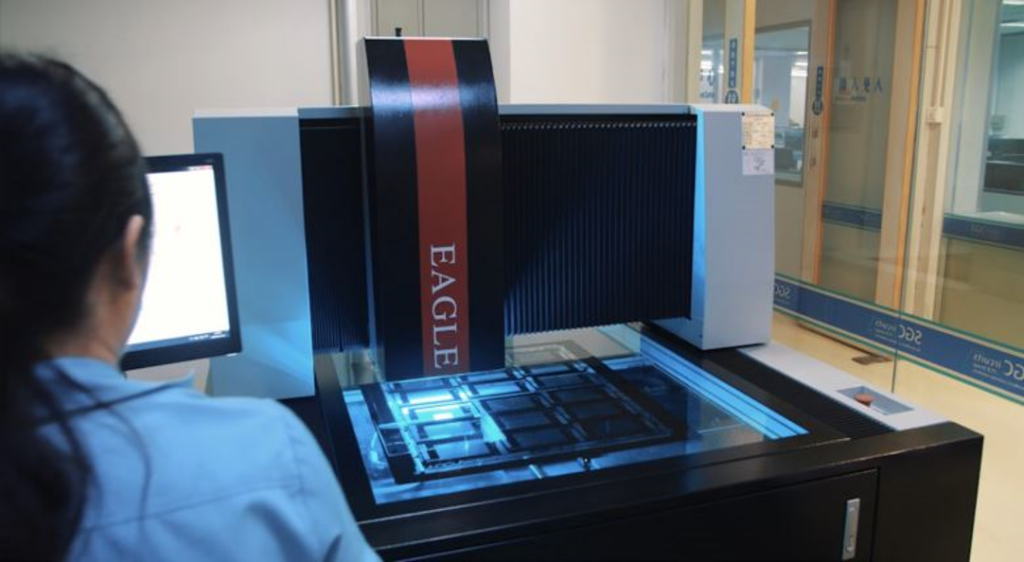