CAF: filamento anódico conductor (CAF)
en PCB
Exploremos un fascinante aspecto indeseable de las placas de circuito impreso llamado filamento anódico conductor (CAF). CAF es el crecimiento del cobre por electromigración entre dos conductores. En este artículo, hablaremos de cómo se fabrican las placas de circuito impreso, qué causa el CAF, especialmente las multicapas con mayor densidad de diseño, y las posibles medidas para prevenir o limitar el riesgo de CAF.
Comprender el proceso de fabricación de PCB
Antes de hablar del CAF, entendamos cómo se fabrican los PCB. En las construcciones multicapa, los orificios chapados crean conexiones entre las distintas capas del apilamiento. Tras el taladrado y la limpieza de los orificios, se aplica una fina capa de cobre químico o material conductor similar en la superficie de la placa de circuito impreso y en los orificios antes del chapado con cobre galvánico final.
¿Qué es el CAF?
El fallo del filamento anódico conductor es el crecimiento de la electromigración de cobre entre dos puntos de una placa de circuito impreso. El fallo del CAF reduce la resistencia y, finalmente, crea un cortocircuito entre dos conductores de cobre de polarización opuesta.
El fallo del CAF puede producirse entre conductores como: agujero chapado a agujero chapado, agujero chapado a traza o traza a traza. Los modos de fallo más comunes son entre los orificios chapados y entre los orificios chapados y las trazas.
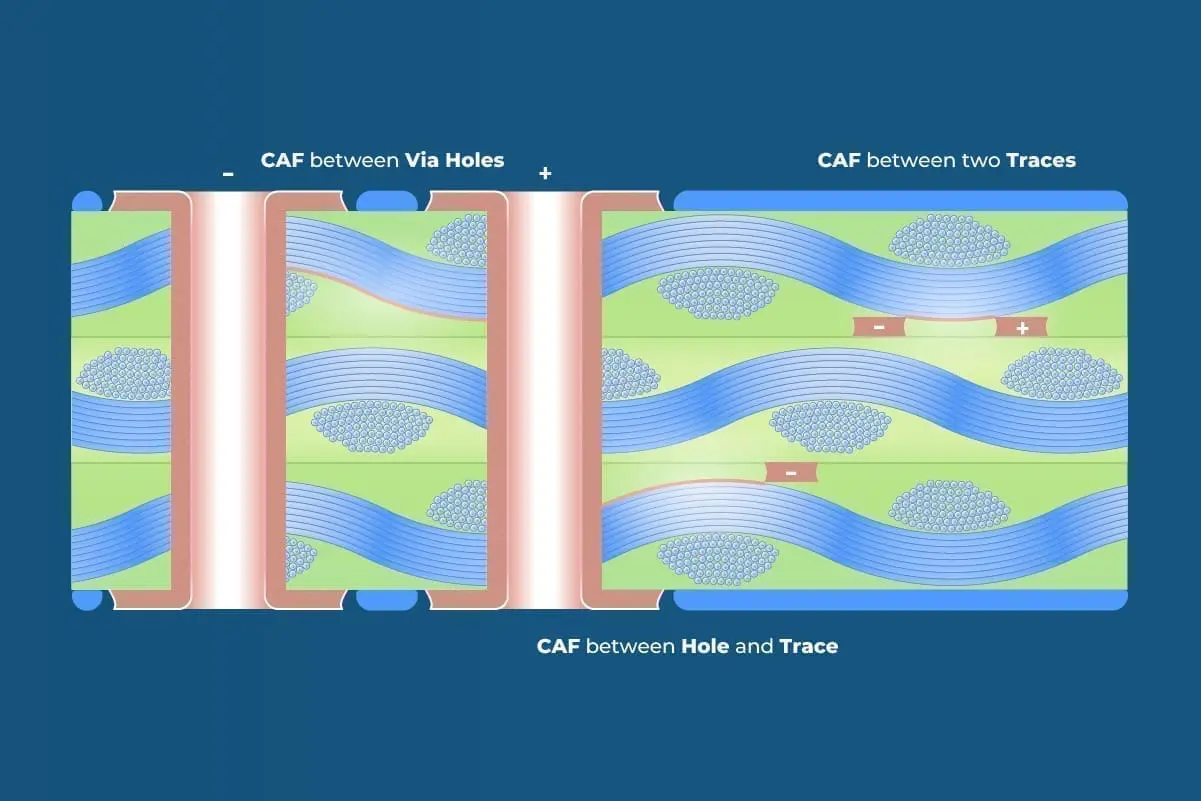
El fallo del CAF consta de dos fases:
La primera etapa es una degradación de la interfaz entre la resina y el vidrio tejido. Los principales factores conocidos que influyen en la primera etapa son las condiciones de humedad y temperatura en la placa de circuito impreso. El horneado/secado de la placa de circuito impreso parece tener un efecto reversible en la primera etapa. Esto amplifica la importancia de mantener la placa de circuito impreso en condiciones secas durante el proceso de PCBA, así como durante la vida útil de las aplicaciones.
La segunda etapa es el crecimiento de la electromigración de cobre entre los conductores que puede comenzar tras la degradación de la interfaz resina/vidrio. Los principales factores conocidos que influyen en la segunda etapa son la distancia entre dos conductores de cobre de polarización opuesta, la colocación/el ángulo entre los orificios frente a la dirección de la fibra de vidrio, la tensión de polarización, la humedad, la temperatura, y la concentración de pH. Las condiciones para que los iones de Cu migren del conductor con carga + al conductor con carga – a lo largo de la interfaz entre la resina y las fibras de vidrio puede compararse con las condiciones de un proceso galvánico de chapado con Cu. La formación de la migración del cobre es irreversible y la formación no se ve afectada por la cocción/el secado cuando se ha completado el CAF.
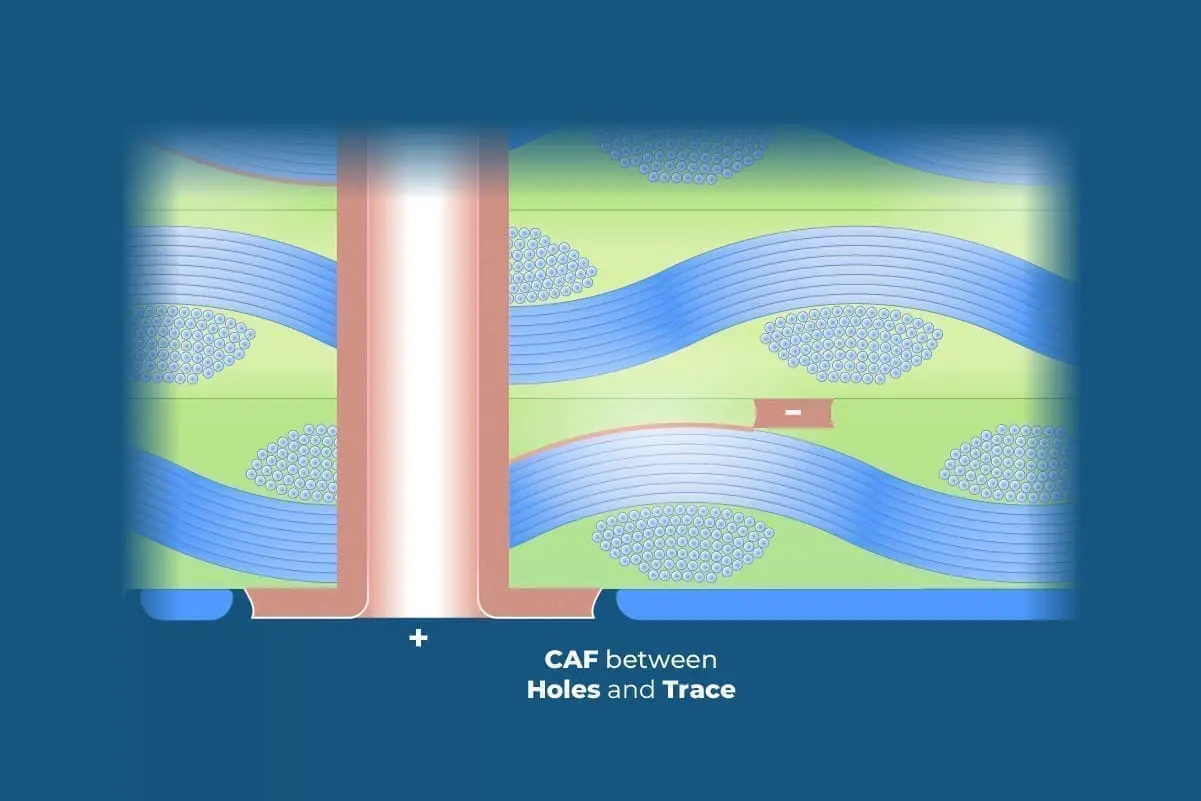
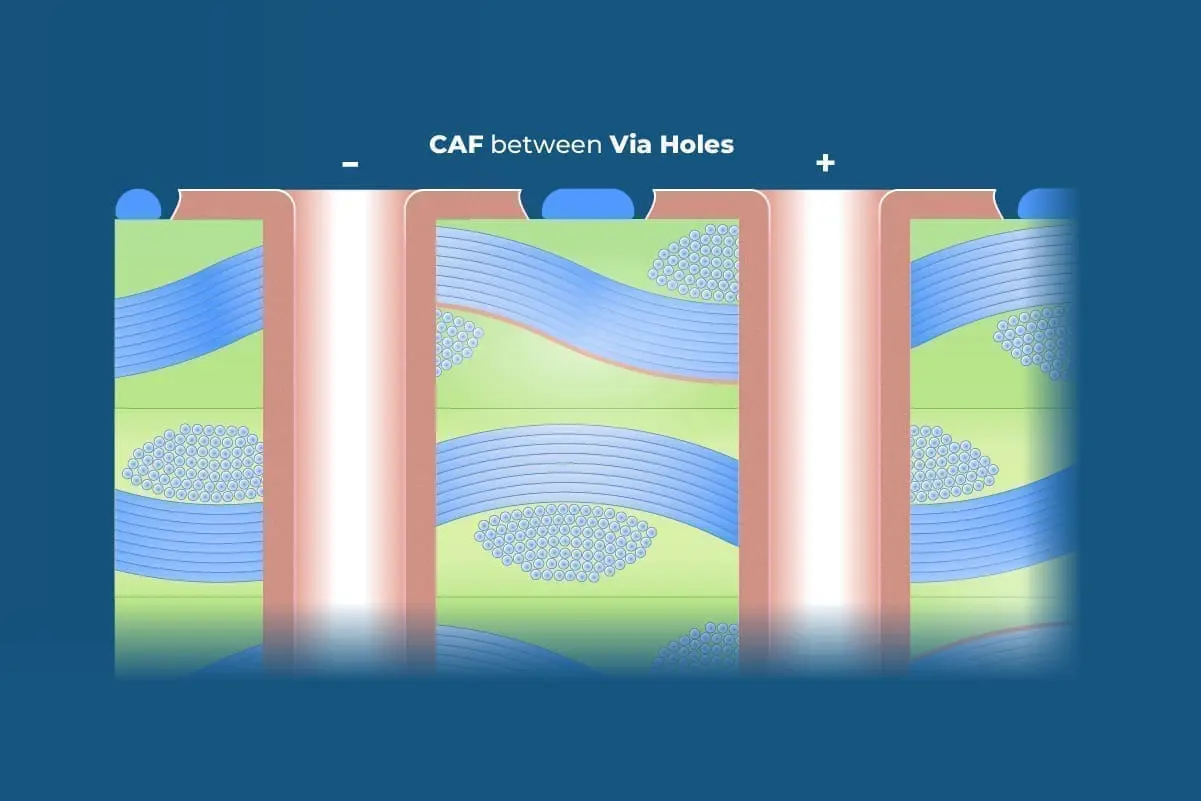
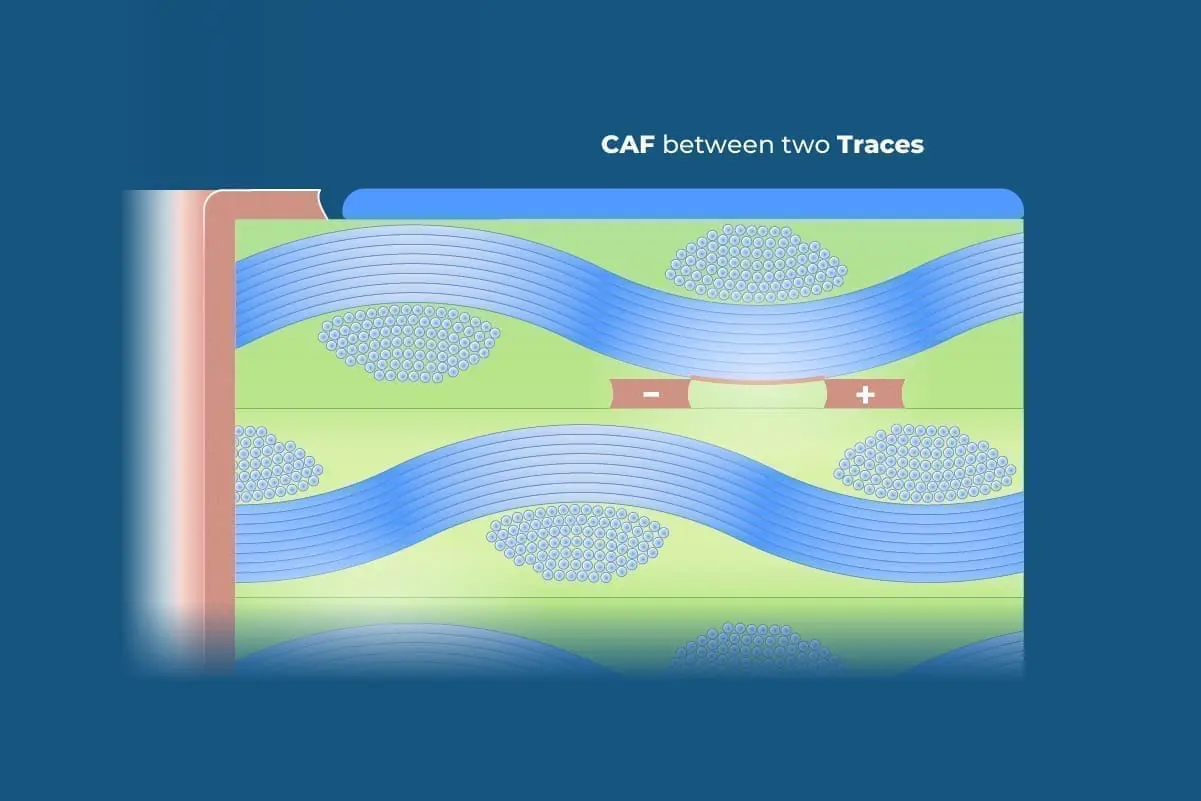
Prevención del CAF
Elección del material: Reducir el riesgo de CAF especificando un valor de Tg elevado y un material resistente al CAF.
Diseño: Elimine las almohadillas no conectadas en las capas interiores, pero mantenga la distancia de aislamiento como si hubiera almohadillas en la capa interior. Esto reducirá el riesgo de CAF al aumentar la distancia Cu-Cu. Evite las vías de tensión próximas a las vías de tierra siempre que sea posible. Cuando sea inevitable, no coloque las vías alineadas con el vidrio tejido. Desplácelas en un ángulo de 45°, para evitar la formación de CAF a lo largo de las fibras de vidrio. Además, se recomienda aumentar la separación entre dichas vías.
Fabricación de PCB: El fabricante se centrará en limitar/evitar los huecos durante el proceso de laminación. Los parámetros de avance/velocidad de la broca deben estar equilibrados para evitar la degradación de la interfaz resina/vidrio en las primeras fases. El producto químico desincrustante del orificio se eliminará con firmeza antes del chapado con Cu para evitar cualquier acumulación ácida entre el FR4 y la pared del orificio chapada con Cu.
Montaje de PCBA: Asegúrese de que las placas de circuito impreso estén secas antes del proceso de soldadura. La humedad atrapada en el interior de la placa de circuito impreso puede convertirse en vapor durante la soldadura y provocar una microdelaminación que, con el tiempo, puede provocar CAF.
Limpieza tras el montaje: Limpie a fondo la placa de circuito impreso después del montaje para eliminar cualquier contaminante que pudiera causar CAF.
Revestimiento protector del PCBA: Aplique una capa protectora al PCBA para protegerlo de la humedad, la sal y otras sustancias dañinas durante la vida útil de las aplicaciones.
Conclusión
El CAF puede producirse en todos los tipos de PCB basados en FR4, pero como se ha mencionado anteriormente, ciertas condiciones aceleran el fenómeno, lo que hace que algunas aplicaciones sean más vulnerables al CAF que otras. Las placas de circuito impreso de alta corriente y las placas de circuito impreso con una alta densidad de cableado parecen ser las más afectadas, especialmente si están expuestas a temperaturas de funcionamiento y humedad elevadas.
Sin embargo, conocer las condiciones es el primer paso para prevenir el CAF al:
- utilizar un material resistente al CAF
- diseñar con un enfoque en el espaciado y la colocación de las vías GND y VCC
- elegir un proveedor con un buen control del proceso
- garantizar unas condiciones secas antes de soldar
- limpiar las placas de circuito impreso después del montaje
- utilizar un revestimiento protector para blindar los PCBA que funcionan en entornos difíciles
Si necesita más información, póngase en contacto con nosotros en el Grupo ICAPE.
Autor: Erik Pedersen/Jordan Labbe