CAF : Comprendre le filament anodique conducteur (CAF)
sur les PCB
Explorons un aspect indésirable fascinant des PCB appelé filament anodique conducteur (CAF). Le CAF est la croissance de l’électro-migration du cuivre entre deux conducteurs. Dans cet article, nous verrons comment les circuits imprimés sont fabriqués, quelles sont les causes du CAF, en particulier les multicouches avec une densité de conception accrue, et quelles sont les mesures possibles pour prévenir ou limiter le risque de CAF.
Comprendre le processus de fabrication des PCB
Avant de parler du CAF, il convient de comprendre comment les PCB sont fabriqués. Dans les constructions multicouches, les trous plaqués créent des connexions entre les différentes couches de l’empilement. Après le perçage et le nettoyage des trous, une fine couche de cuivre chimique ou d’un matériau conducteur similaire est appliquée sur la surface du circuit imprimé et sur les trous avant le placage galvanique final du cuivre.
Que signifie l’abréviation CAF ?
La rupture du filament anodique conducteur est la croissance de l’électro-migration du cuivre entre deux points d’une carte de circuit imprimé. La défaillance du CAF réduit la résistance et crée finalement un raccourci entre deux conducteurs en cuivre polarisés de manière opposée.
La défaillance du CAF peut se produire entre les conducteurs: trou plaqué à trou plaqué, trou plaqué à trace ou trace à trace. Les modes de défaillance les plus courants se situent entre les trous plaqués et entre les trous plaqués et les traces.
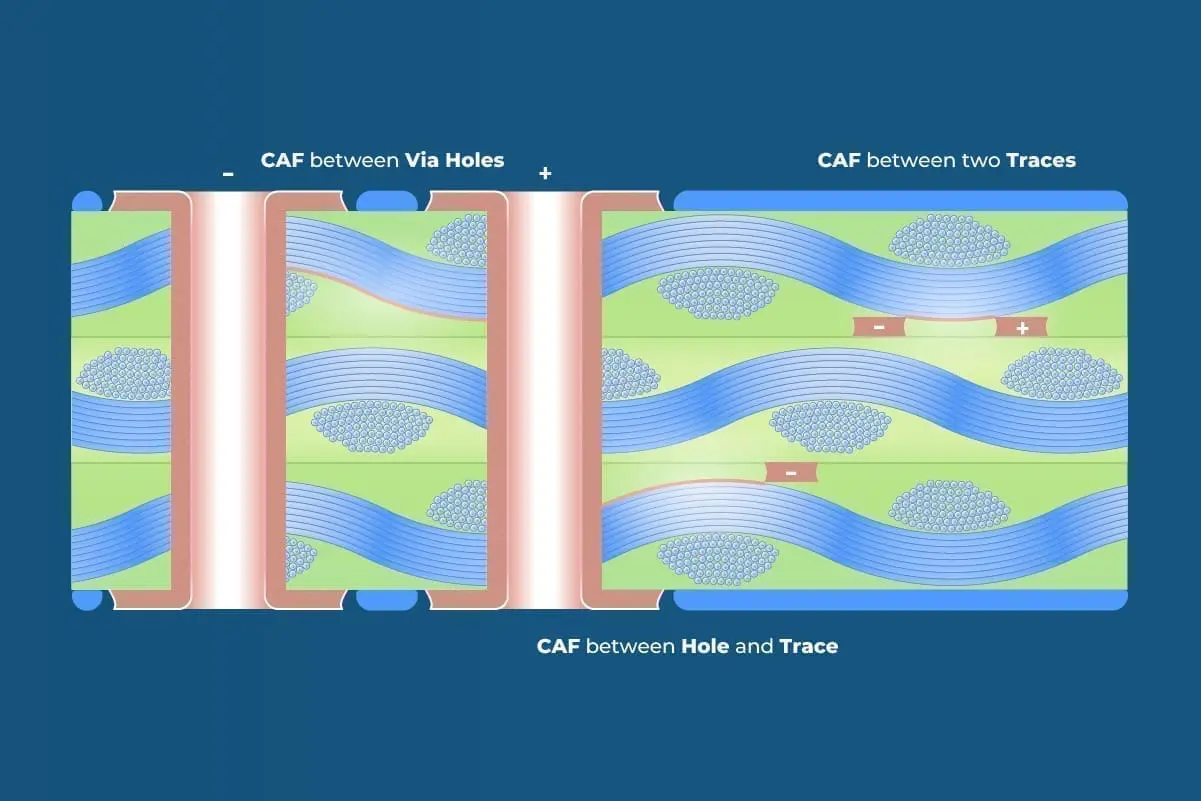
L’échec du CAF se déroule en deux étapes:
La première étape est une dégradation de l’interface entre la résine et le verre tissé. Les principaux facteurs connus qui influencent la première étape sont les conditions d’humidité et de température dans le PCB. La cuisson/séchage du circuit imprimé semble avoir un effet réversible sur la première étape. Cela souligne l’importance de maintenir la carte de circuit imprimé dans des conditions sèches pendant le processus de fabrication de la carte de circuit imprimé ainsi que pendant la durée de vie de l’application.
La deuxième étape est la croissance de l’électro-migration du cuivre entre les conducteurs qui peut commencer après la dégradation de l’interface résine/verre. Les principaux facteurs connus qui influencent la deuxième étape sont les suivants : distance entre deux conducteurs en cuivre polarisés opposés, placement/angle entre les trous par rapport à la direction de la fibre de verre, tension de polarisation, humidité, température, et concentration de pH. Les conditions pour que les ions cu migrent du conducteur chargé en + vers le conducteur chargé en – sont réunies – Le conducteur chargé le long de l’interface entre la résine et les fibres de verre peut être comparé aux conditions d’un processus de placage galvanique de Cu. La formation de la migration du cuivre est irréversible et la formation n’est pas affectée par la cuisson/séchage lorsque le CAF est terminé.
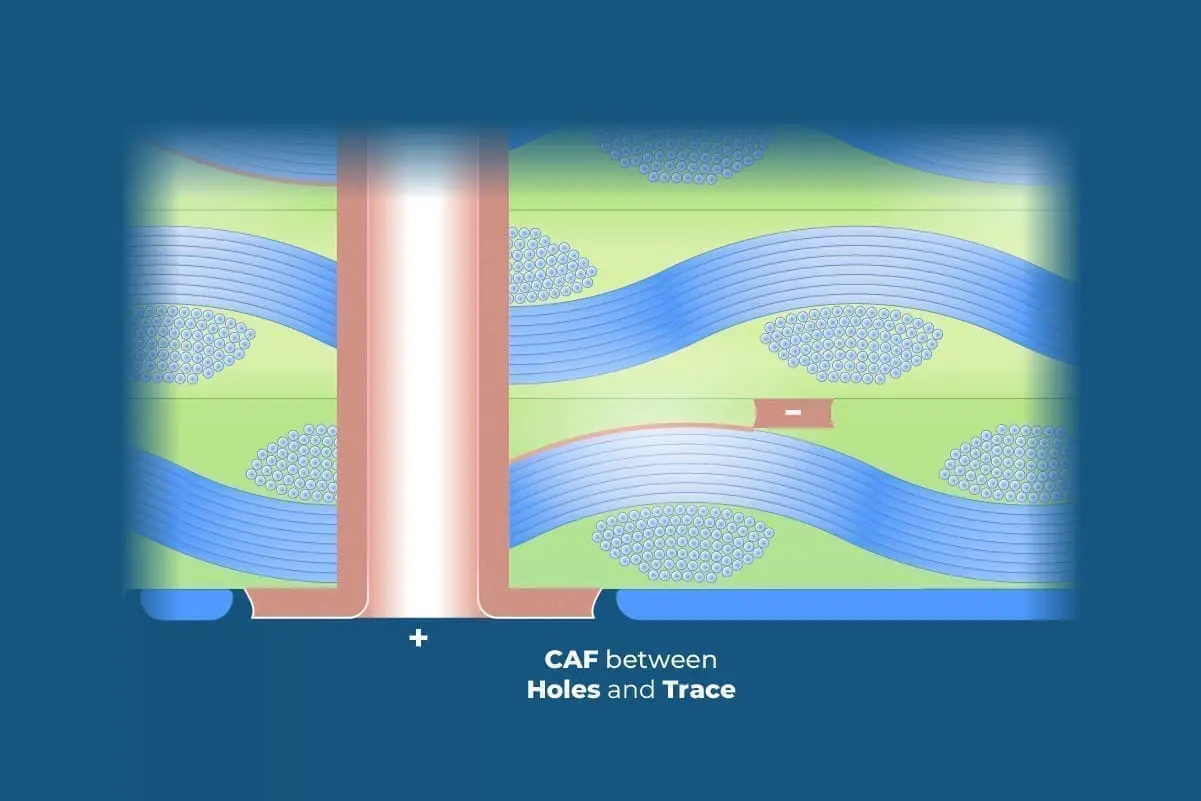
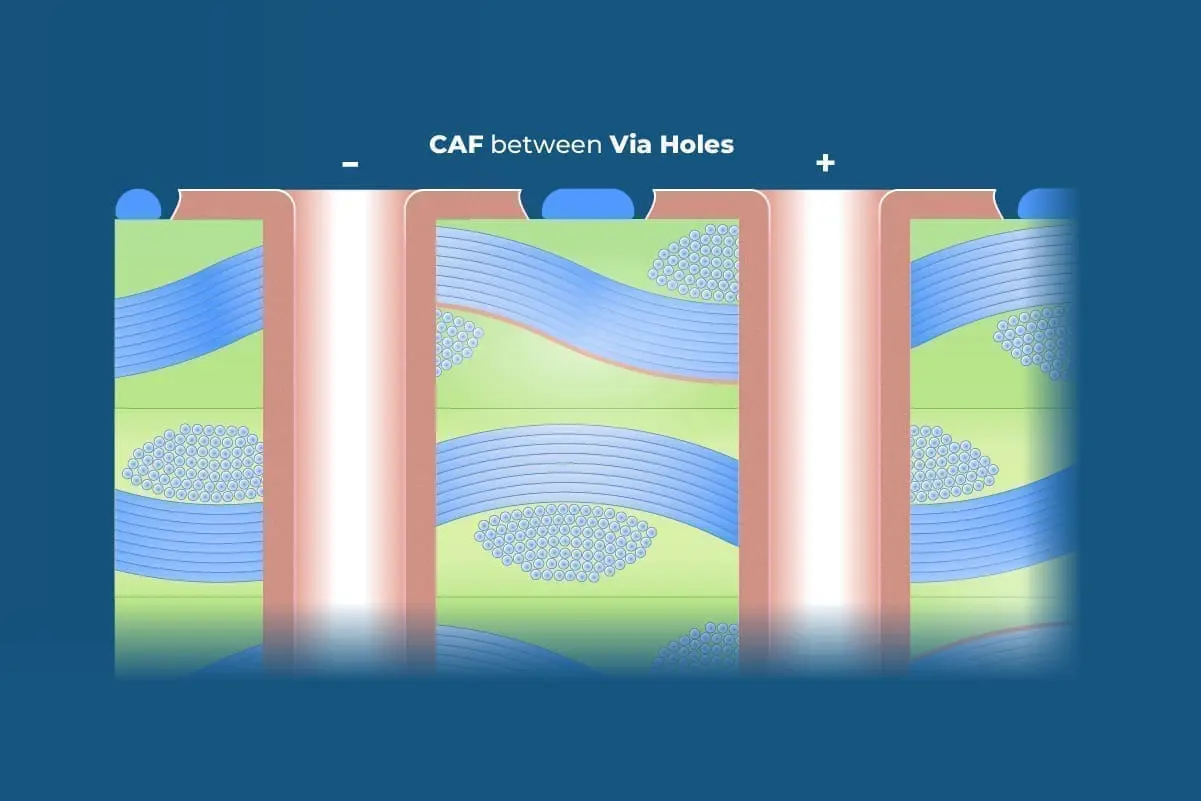
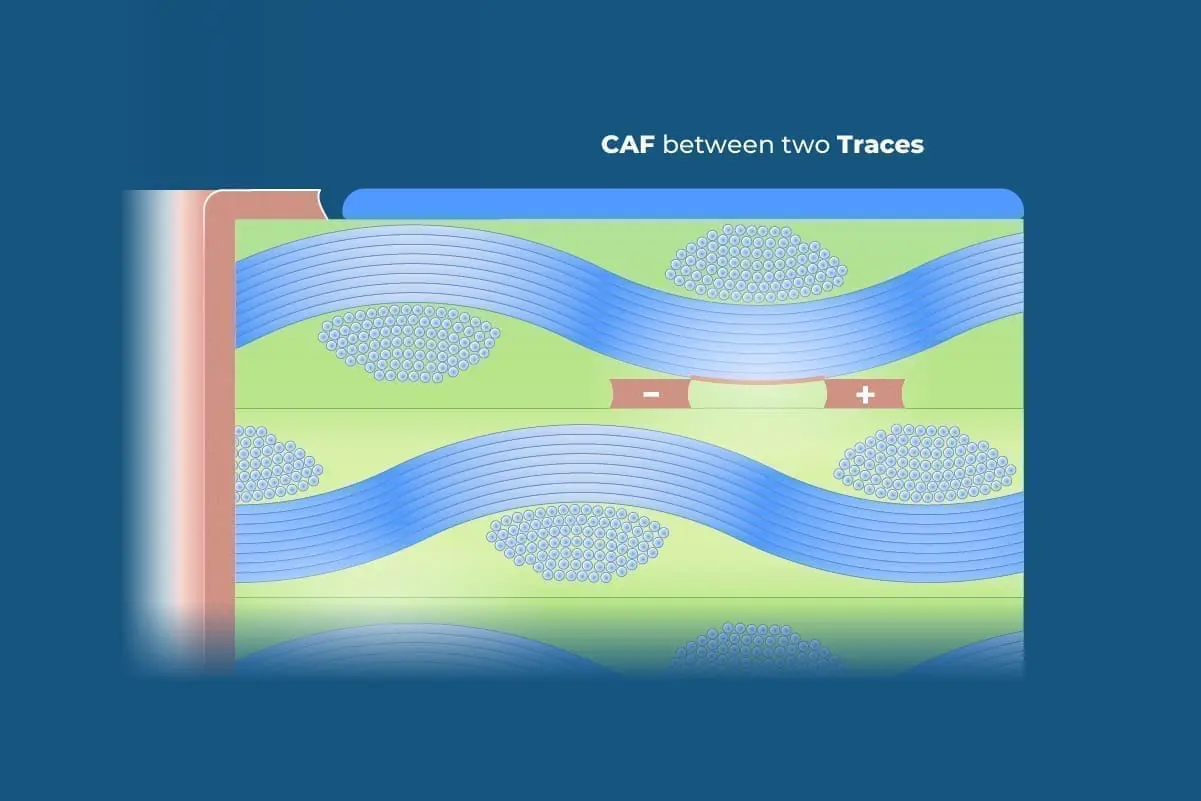
Prévenir le CAF
Choix des matériaux: Réduire le risque de CAF en spécifiant une Tg élevée. et du matériel résistant à la CAF.
Conception: Supprimer les pastilles non connectées sur les couches intérieures mais conserver la distance d’isolement comme s’il y avait des pastilles sur la couche intérieure. Cela réduira le risque de CAF en augmentant la distance Cu-Cu. Dans la mesure du possible, évitez de placer des vias de tension à côté de vias de masse. Si cela est inévitable, ne placez pas les vias dans l’alignement du verre tissé. Les déplacer à un angle de 45°, pour éviter la formation de CAF le long des fibres de verre. En outre, il est recommandé d’augmenter l’espacement entre ces vias.
Fabrication de circuits imprimés: Le fabricant doit s’efforcer de limiter/éviter les vides pendant le processus de laminage. Les paramètres d’avance et de vitesse du foret doivent être équilibrés afin d’éviter toute dégradation précoce de l’interface résine/verre. Le produit chimique de désencrassement du trou doit être fermement enlevé avant le placage de Cu pour éviter toute contraction acide entre le FR4 et la paroi du trou plaqué de Cu.
Assemblage PCBA: Veillez à ce que les circuits imprimés soient secs avant le processus de soudure. L’humidité piégée à l’intérieur du circuit imprimé peut, pendant la soudure, se transformer en vapeur et provoquer un micro-décollement qui, avec le temps, peut conduire au CAF.
Nettoyage après l’assemblage: Nettoyez soigneusement la carte de circuit imprimé après l’assemblage afin d’éliminer tout contaminant susceptible de provoquer un CAF.
Revêtement protecteur du PCBA: Appliquer un revêtement protecteur sur le circuit imprimé pour le protéger de l’humidité, du sel et d’autres substances dommageables pendant la durée de vie de l’application.
Conclusion
Le CAF peut se produire sur tous les types de circuits imprimés en FR4 mais, comme indiqué ci-dessus, certaines conditions accélèrent le phénomène, ce qui rend certaines applications plus vulnérables au CAF que d’autres. Les circuits imprimés à courant élevé et les circuits imprimés à forte densité de câblage semblent être les plus touchés, surtout s’ils sont exposés à des températures de fonctionnement et à une humidité élevées.
Cependant, la connaissance des conditions est la première étape de la prévention de la CAF:
- l’utilisation d’un matériau résistant à la CAF
- conception en mettant l’accent sur l’espacement et l’emplacement des vias GND et VCC
- choix d’un fournisseur ayant un bon contrôle des processus
- s’assurer que les conditions sont sèches avant de procéder à la soudure
- nettoyer les circuits imprimés après l’assemblage
- utiliser un revêtement protecteur pour protéger les circuits imprimés fonctionnant dans des environnements difficiles
Si vous avez besoin de plus d’informations, contactez-nous au Groupe ICAPE.
Auteur : Erik Pedersen/Jordan Labbe