PCB MANUFACTURING
Processo
Tutti i processi produttivi sono stati svelati passo dopo passo. Segui i team del Gruppo ICAPE all’interno delle nostre fabbriche di PCB per scoprire i segreti della produzione di PCB.
Come vengono realizzati i circuiti stampati, passo dopo passo?
Nell’intricato mondo dell’elettronica, il cuore dell’innovazione risiede nel circuito stampato (PCB). Questi componenti, compatti ma potenti, costituiscono la spina dorsale dei dispositivi elettronici, consentendo un flusso continuo di segnali elettrici. Ti sei mai chiesto quale sia l’affascinante percorso che un circuito stampato compie dall’ideazione all’integrazione? Il nostro articolo di prossima pubblicazione approfondisce il processo completo di produzione dei PCB, svelando ogni fase con precisione e chiarezza. Dalla fase iniziale di progettazione agli intricati processi di incisione e assemblaggio, vi guideremo attraverso l’intricata rete di tecniche e tecnologie che trasformano i materiali grezzi in PCB funzionali. Che tu sia un ingegnere esperto, un appassionato curioso o semplicemente che tu sia incuriosito dalla magia che si cela dietro i tuoi gadget elettronici, unisciti a noi in questo viaggio attraverso l’affascinante mondo della produzione di PCB. Preparati ad assistere all’alchimia che trasforma rame, fibra di vetro e saldature nei sofisticati circuiti che alimentano i dispositivi su cui facciamo affidamento ogni giorno.
Ingegneria di pre-produzione
Come progettare un PCB?
Tutto parte dal Dipartimento di Ingegneria. Qui viene ricevuto il file GERBER, viene controllato e confrontato con l’ordine, gli standard IPC e le capacità del fornitore.
1- Controllo dei file Gerber
Gli ingegneri di ICAPE Group effettuano una revisione del Design For Manufacturability (DFM), controllano i dati, gli strati di rame, il disegno meccanico, le specifiche e la linea e la spaziatura tra le piste. Se necessario, creiamo un file chiamato “Domande tecniche”.
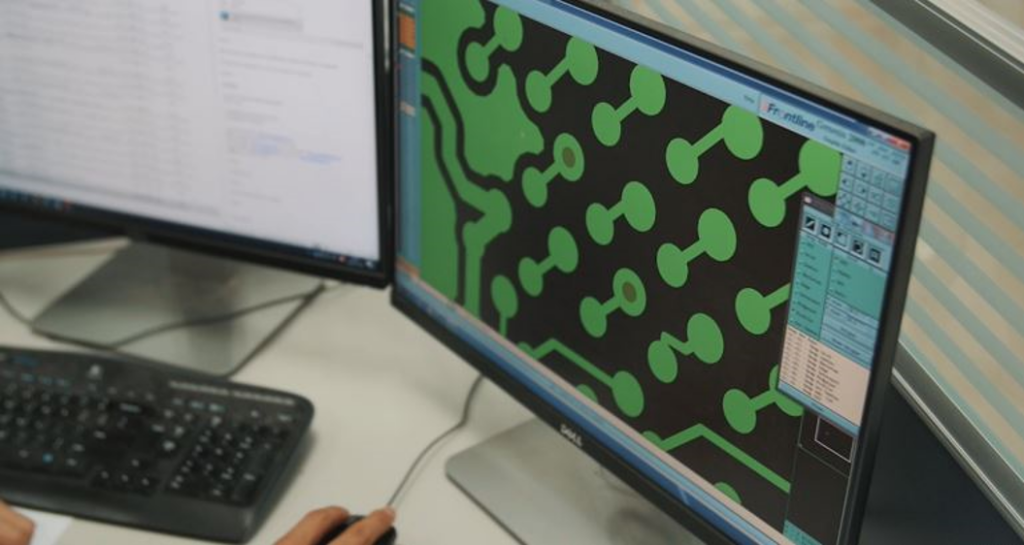

2 - Revisione DFM
Questo file viene inviato al cliente per proporre una possibile soluzione o un miglioramento, come ad esempio diverse tecniche di pannellatura, tipo di maschera di saldatura, design, materiale di base, marca o specifiche, e persino diverse tecnologie, in modo che siano fattibili ed economicamente vantaggiose nelle fabbriche partner selezionate secondo gli standard IPC.
3 - Revisione DFM del partner
La nostra fabbrica partner entra in scena, riceve i dati, esegue una seconda revisione DFM e inizia a combinare i design dei circuiti sul pannello di produzione.


4 - Stampa del disegno modello (artwork)
Ogni strato di PCB viene verificato e trasferito alla macchina di stampa del disegno modello. Abbiamo un disegno modello per ogni livello: interno, esterno, maschera di saldatura, serigrafia e anche strati speciali come via, maschera pelabile, carbonio, ecc. Tutti questi disegni modelli possono essere utilizzati per migliaia di pannelli.
Materiali di base
Come selezionare e preparare i materiali di base?
Scopri come i pannelli vengono immagazzinati e preparati prima di passare alle fasi successive del processo di produzione!
1 - STOCCAGGIO
Ogni produttore di PCB non produce materie prime di base come il prepreg o il foglio di rame. Tutte le materie prime sono fornite in conformità ai requisiti tecnici di ICAPE Group. I materiali sono stoccati per tipo, spessore totale, spessore del rame e marca.
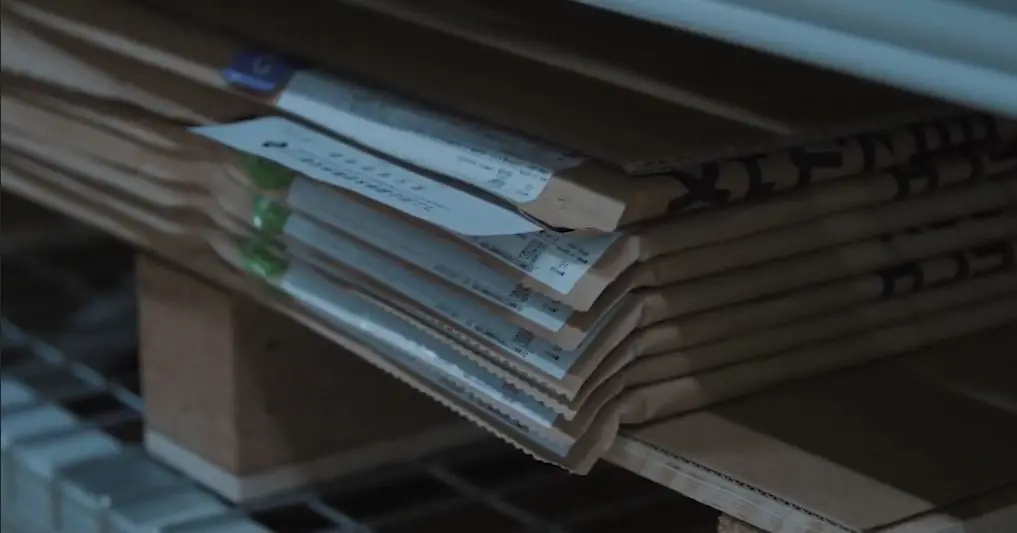
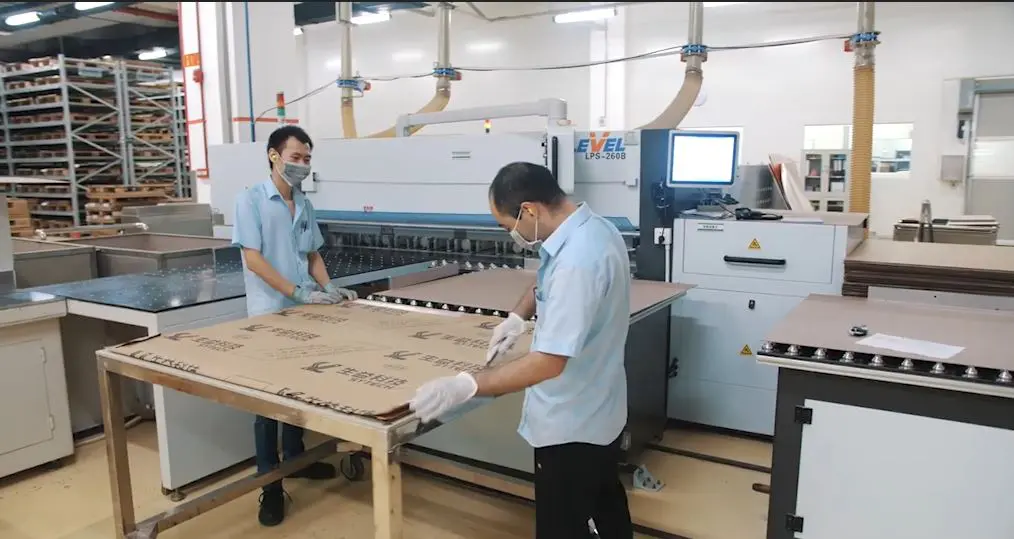
2 - PREPARAZIONE DELL'ORDINE
In base all’ordine, la fabbrica seleziona i materiali necessari nel magazzino. I pannelli vengono disimballati e preparati per il processo.
3 - CONTROLLI
L’ispezione di ogni lotto è un punto essenziale. Il rame e gli spessori totali sono accuratamente controllati con strumenti di alta precisione, per assicurarsi che rispettino le esigenze dei clienti in base alla tecnologia in uso
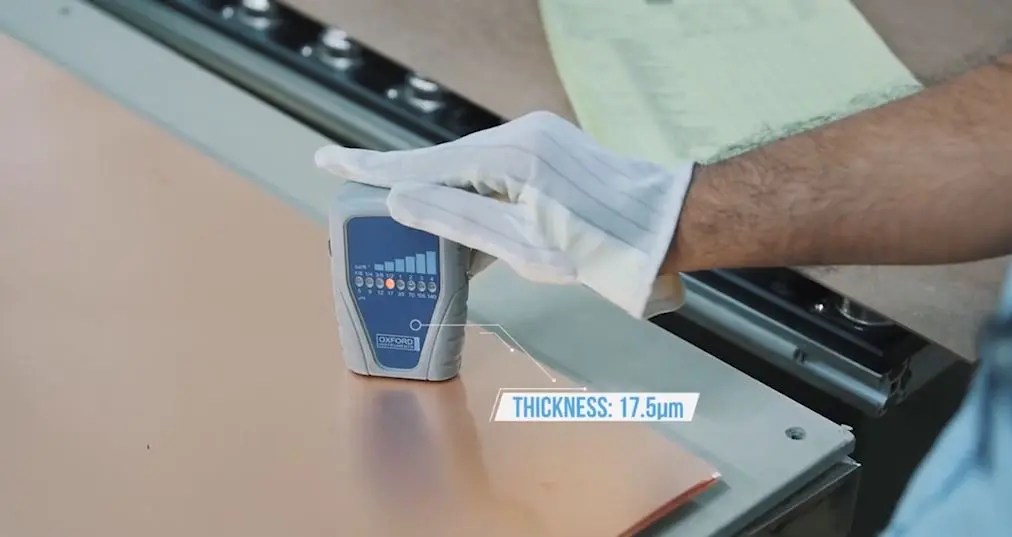
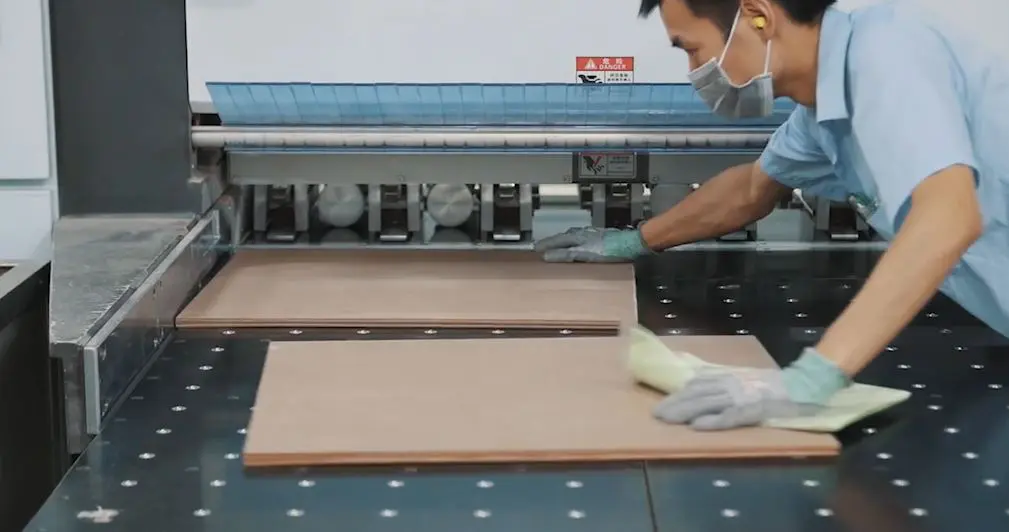
4 - TAGLIO
Il pannello deve essere tagliato a misura di produzione. Al giorno d’oggi, la finitura dei bordi e la geometria dei pannelli sono molto importanti per la registrazione dei CCD e per le apparecchiature di manipolazione.
5 - FINITURA D'ANGOLO
La maggior parte delle aziende ha arrotondato gli angoli dei pannelli per ridurre i problemi di graffiatura e garantire una gestione sicura durante le fasi successive del processo di produzione
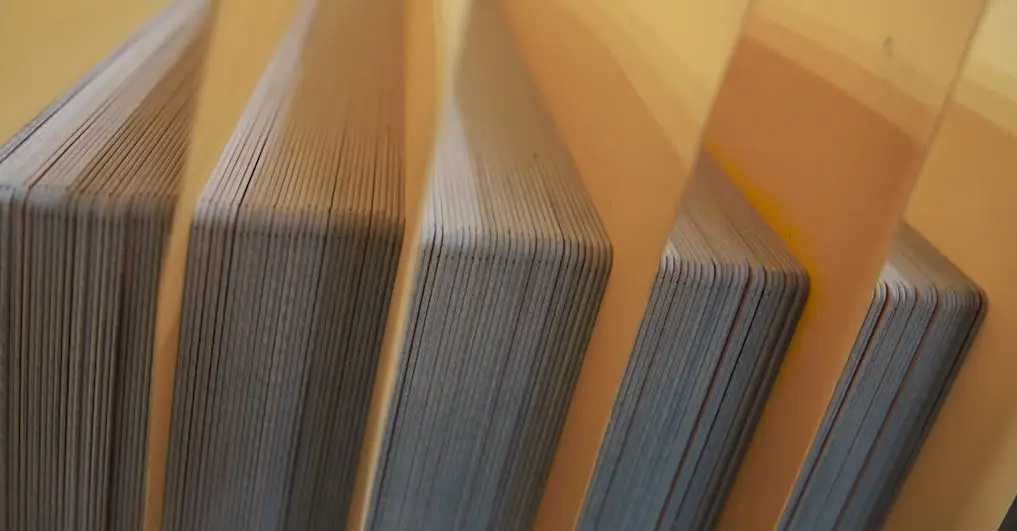
Inner Layer
The inner layer
The inner layer imaging is a very technical step of the process which happens in a clean and yellow room. Why ? Because the dry film is UV sensitive and to avoid any shorts and opens on the inner layer, a level between 3000 and 4000 dust particles per cubic meters must be reached.
1 - CLEANING
The cleanroom uses overpressure to protect and remove any dust coming from outside of the cleanroom. Before entering the cleanroom, the panels are cleaned. Depending on the thickness of the inner layers, the processes are different. For layers thinner than 500 micrometers, the chemical process is used. For thicker layers, the mechanical process is preferred.
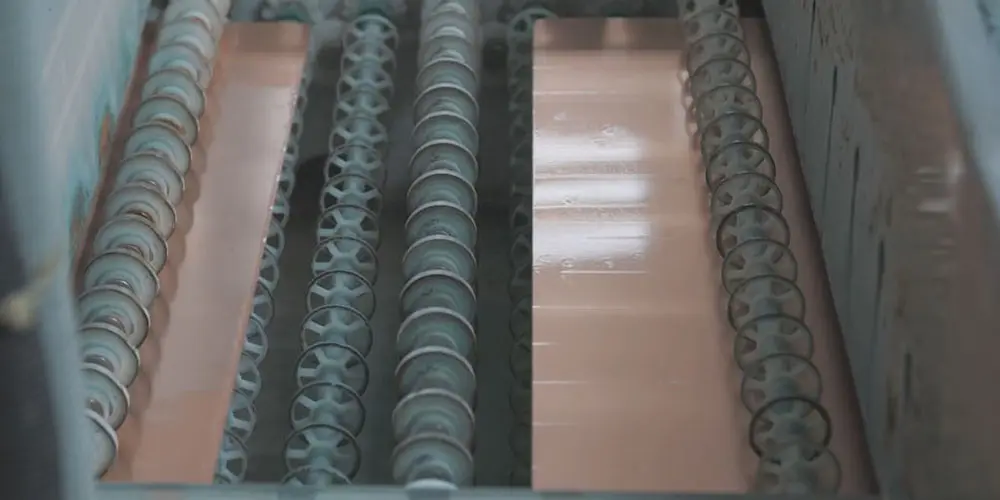
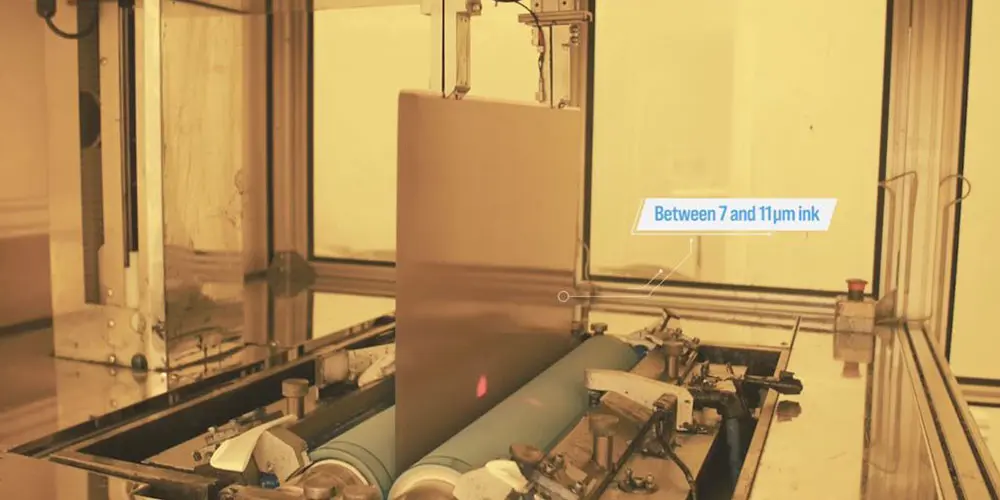
2 - ENDUCTION
When panels arrive in the cleanroom, they are heated, then the photoresist film or the ink ( beteween 7 and 11 µm) is automatically applied onto the panel.
3 - REGISTRATION AND INSOLATION
The boards are registered at +/- 15 to 30 micrometers with 2 or 4 CCD Cameras. A vacuum is created, then a blast of UV light is applied with an average of 1 to 20 seconds depending on the process: this is the insolation. The boards are polymerized and ready to be developed.
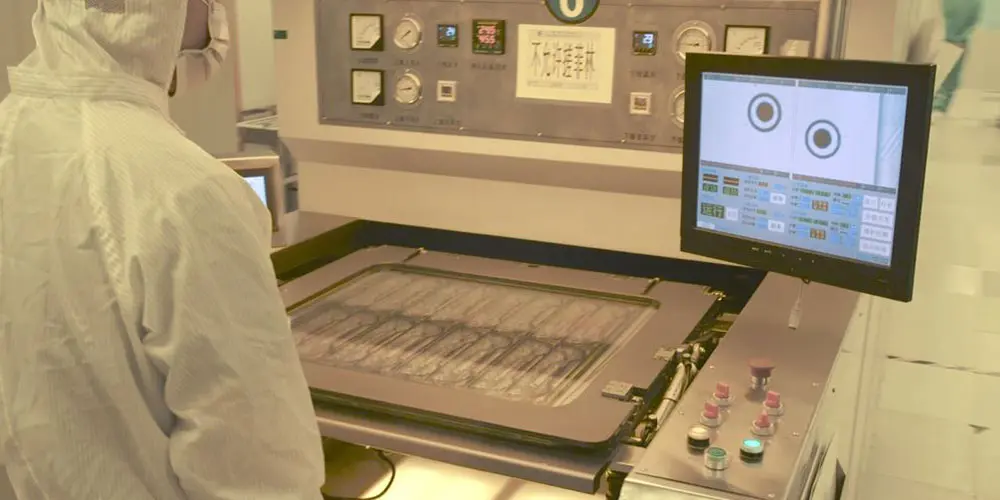
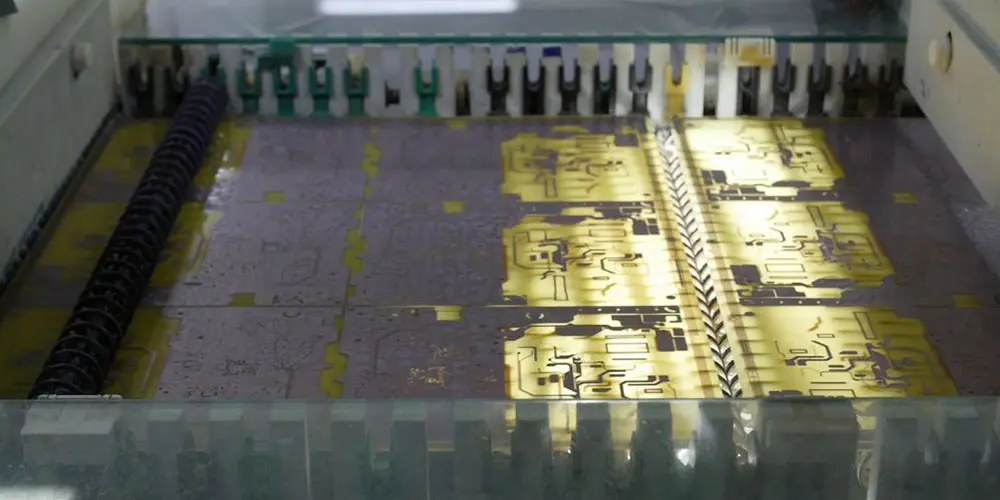
4 - DEVELOPING AND ETCHING
For the development phase, the board is washed with an alkaline solution which removes the photoresist left unhardened. From there, we can see the inner layer image for the first time. Etching is the critical step in layer imaging. The unprotected copper is removed and defines the pattern. After stripping the ink, the photoresist film is now completely removed.
5 - AUTOMATIC OPTICAL INSPECTION (AOI)
After the Multilayer lamination, it is impossible to correct errors occurring on the inner layers. The Automatic Optical Inspection will confirm a total absence of defects. The original design from the GERBER file serves as a model. If the machine detects any inconsistencies, a technician will assess the problem.
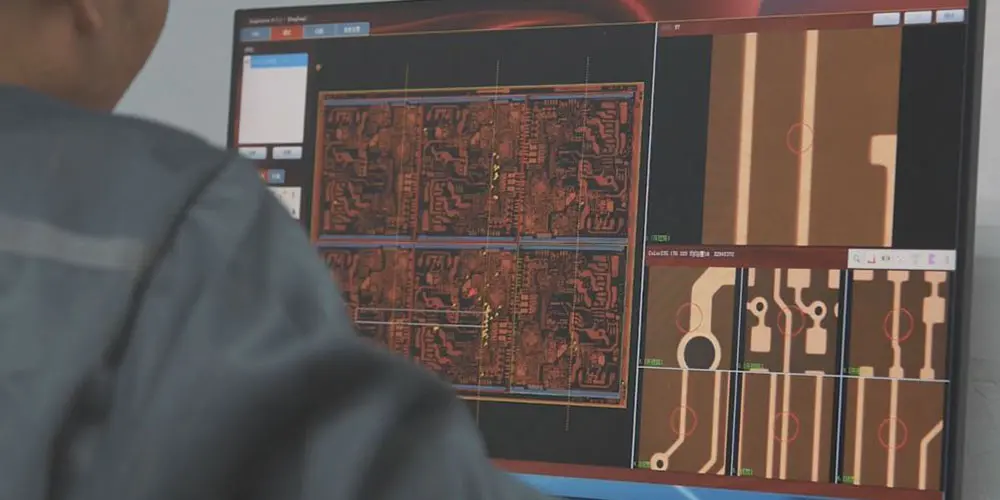
Laminazione
Che cos’è la laminazione dei PCB?
Sali a bordo per scoprire la fase di laminazione del processo di produzione dei circuiti stampati! Dopo la fase di imaging dello strato interno, i pannelli vengono sottoposti a registrazione e laminazione. Seguici nella nostra fabbrica HDI in Cina!
1 - PREPARAZIONE
I pannelli vengono lavati per rimuovere la superficie di rame corrosa e le potenziali impronte digitali, i residui di pellicola secca, i residui di carbonato e di antischiuma derivanti dallo strippaggio del dry film.
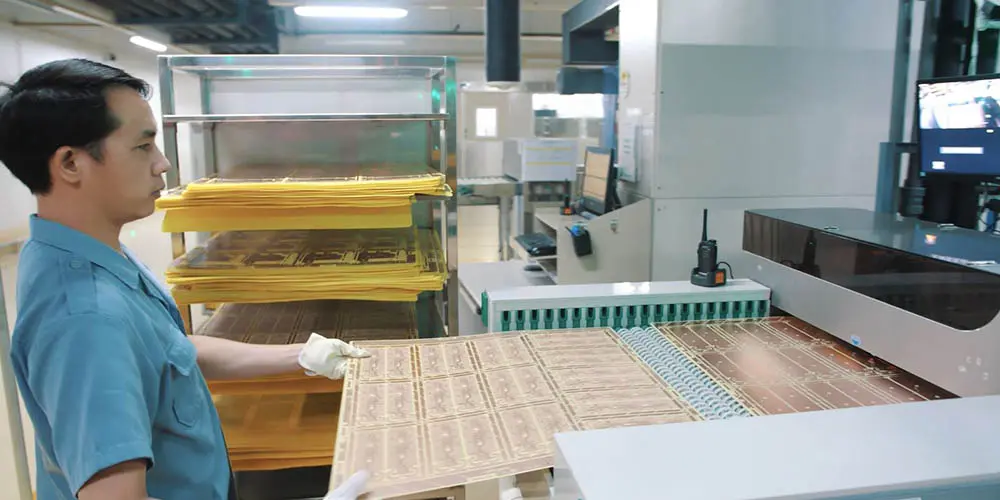
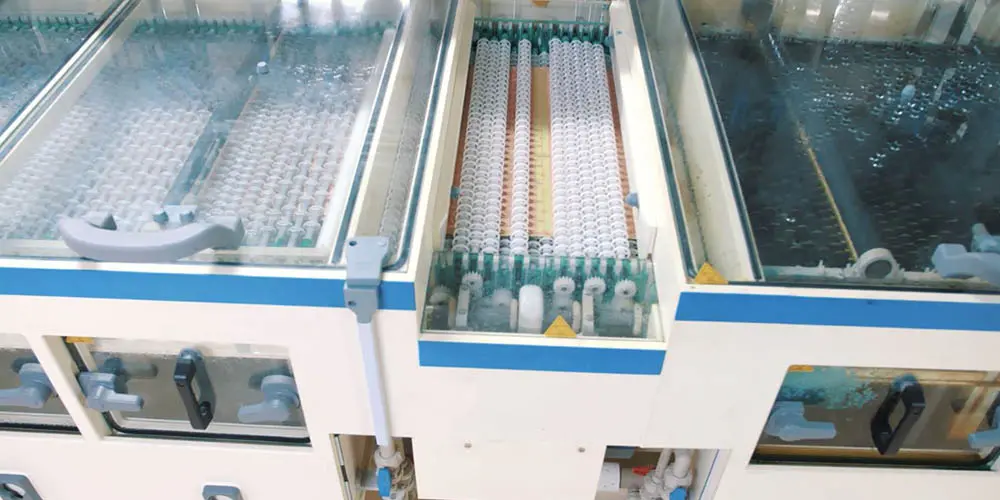
2 - MICROINCISIONE
La microincisione è una condizione fondamentale per ottenere un trattamento omogeneo e adeguato di brunitura. Il processo ridurrà lo spessore del rame da 0,2 a 1 micrometro.
3 - BRUNITURA
La brunitura viene utilizzata per fornire una migliore adesione alla resina epossidica e per evitare problemi come la delaminazione.
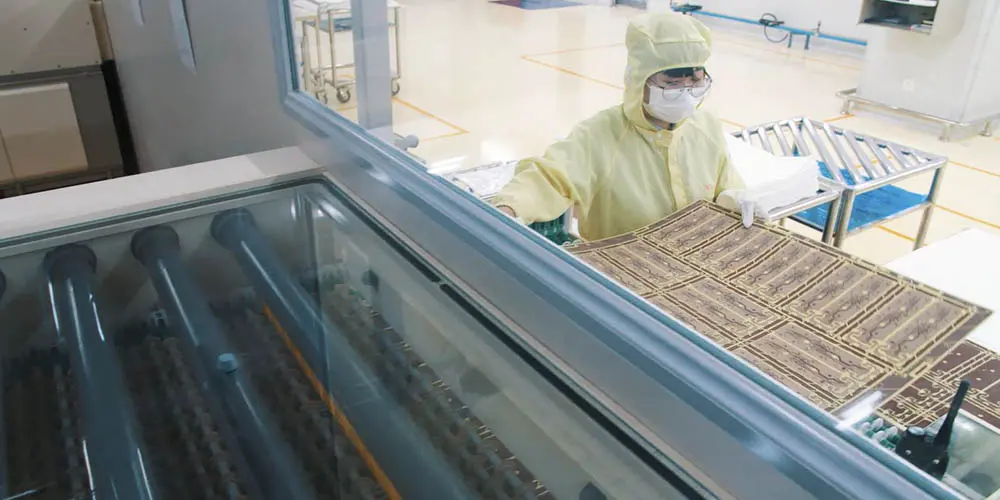
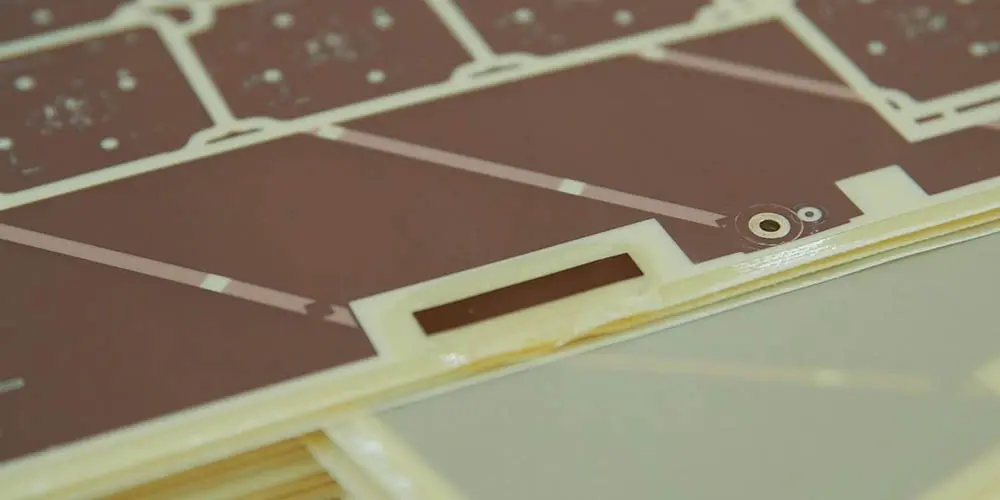
4- STACK-UP DELLO STRATO INTERNO
L’operatore dispone lo strato interno e il prepreg sulla macchina incollatrice, consentendo l’incollaggio dello stack-up. Una volta incollati, si passa all’utilizzo dei rivetti. Il processo di rivettatura serve a completare la registrazione e a rafforzare lo strato interno e il prepreg insieme. Questo rafforza lo stack-up e garantisce che non si muova durante il processo di laminazione.
5 - STACK-UP
Il foglio di rame è inserito tra un pezzo di acciaio inossidabile e un prepreg. L’acciaio inossidabile crea una superficie dura e piatta. Il foglio di rame completa lo stack-up. Il pannello è ora composto in alto e in basso da una lamina di rame e da un prepreg che circonda lo strato interno.
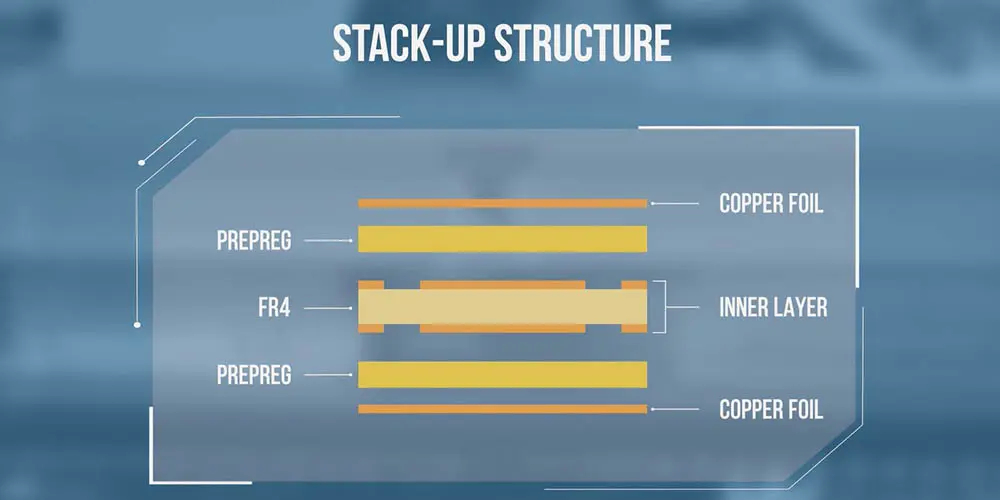
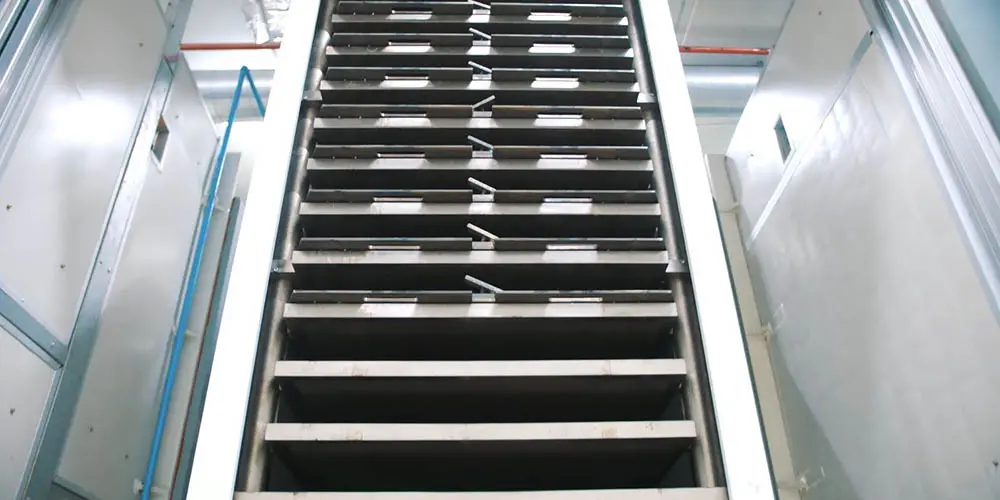
6 - LAMINAZIONE
Lo stack-up è sottoposto a temperature estreme in base alle schede tecniche dei materiali. La pressione all’interno della macchina di laminazione è di 180 tonnellate per metro quadro e il processo richiede fino a 2 ore. Dopo essere stati esposti ad alta pressione e temperatura, gli strati formano un’unica scheda, che viene poi trasferita in una pressa a freddo. In seguito, i pannelli verranno rimossi dagli stampi.
7 - REGISTRAZIONE DEL FORO
Queste nuove schede saranno preparate con i fori di registrazione utilizzando una macchina a raggi X. Quindi verranno sbavate, smussate e arrotondate agli angoli.
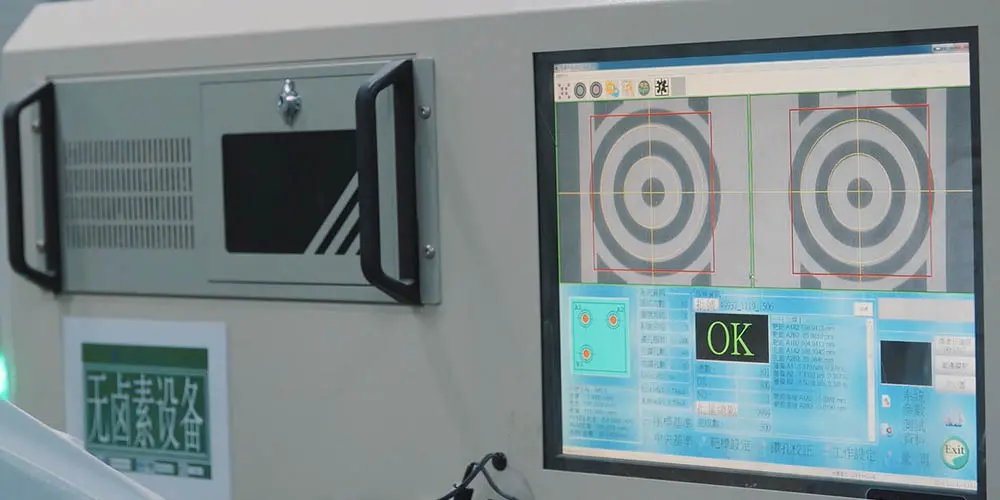
Perforazione
Quanto è impegnativo il processo di perforazione?
Il quinto episodio del nostro Viaggio PCB si concentra su uno dei processi più spettacolari della nostra serie web: la perforazione! Non è solo il processo più impressionante, ma anche il più irreversibile! In effetti, questa fase deve essere eseguita con molta attenzione, perché anche un piccolo errore può portare a una grande perdita. Scopri le diverse fasi di questo processo (foratura meccanica o laser, diametro minimo o anche controlli) seguendo i nostri due esperti di ICAPE Group in una delle nostre fabbriche partner in Cina.
1 - PREPARAZIONE
Per una migliore precisione e gestione termica, vengono utilizzati materiali specifici come l’alluminio, il legno o la melammina nella parte superiore e inferiore dello stack-up.
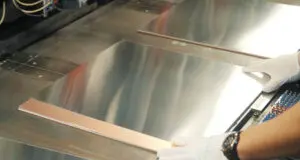
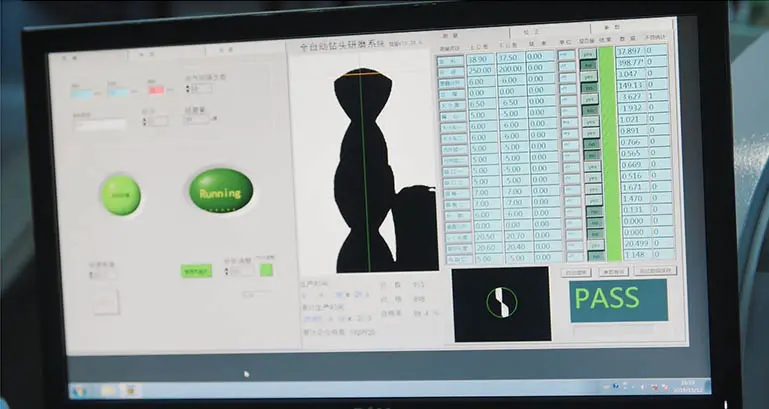
2 - CONTROLLI DEGLI STRUMENTI
La punta deve essere perfettamente sagomata e rispettare le regole relative al numero di fori che possono essere eseguiti dallo stesso utensile. Per i PCB ad alta tecnologia si utilizzano solo nuovi strumenti. Per i PCB standard, le punte vengono affilate fino a 3 volte prima di essere sostituite.
3 - PERFORAZIONE MECCANICA
A seconda della serie, la perforatrice gestisce un pannello alla volta per i prodotti ad alta tecnologia. Tuttavia, è anche possibile installare fino a 4 pannelli contemporaneamente, anche a seconda dello spessore, con 1-6 teste di perforazione. Negli anni ’90, eravamo soliti forare un diametro minimo di 400 micrometri. Oggi siamo in grado di perforare un minimo di 150 micrometri.
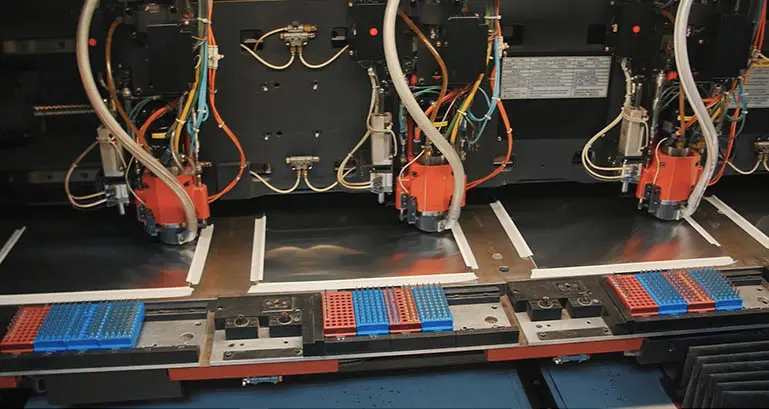
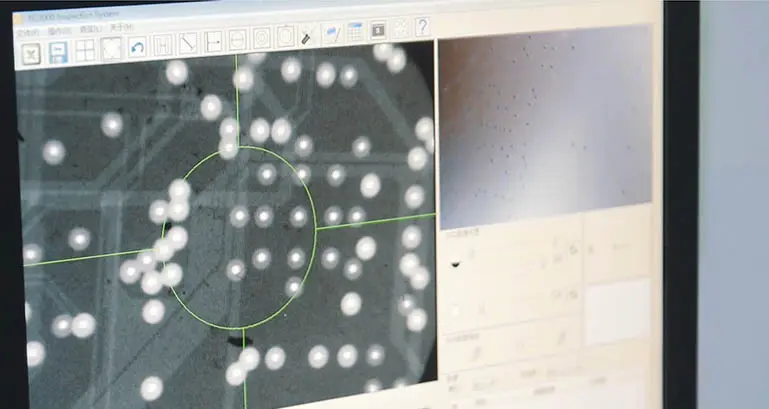
4 - CONTROLLI
Per agevolare il controllo visivo, sul bordo di ogni scheda vengono praticati tutti i fori di dimensioni diverse, che vengono ispezionati dopo la fase di foratura. I pannelli vengono inoltre controllati automaticamente con una macchina per la verifica dei fori. Per il controllo interno, le schede passano attraverso la macchina a raggi X, che controlla l’intero posizionamento in relazione allo strato interno.
5 - PERFORAZIONE LASER
La perforatrice laser può generare via fori tra 50 e 150 micrometri. Gli attuali utensili si basano su due tipi principali di laser: Laser UV o CO2, e talvolta entrambi a seconda del processo. In questo caso, non c’è materiale superiore o inferiore, quindi è possibile forare solo un pannello alla volta e il laser si ferma quando colpisce il rame sullo strato N-1. Esistono due controlli principali per garantire che i fori rispettino le dimensioni richieste e per verificare la pulizia.
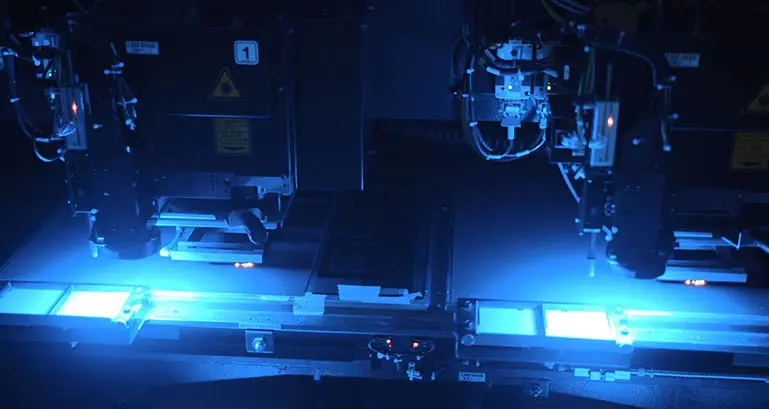
Rame chimico e non elettrolitico
Come depositare il rame su un circuito stampato?
La deposizione chimica del rame, detta anche rame non elettrolitico, crea il collegamento elettrico tra lo strato interno e quello esterno.
1 - PULIZIA STANDARD
Prima di depositare il rame chimico, la scheda deve essere pulita. Per il processo standard, i primi bagni puliscono e rimuovono tutti i residui della perforazione.
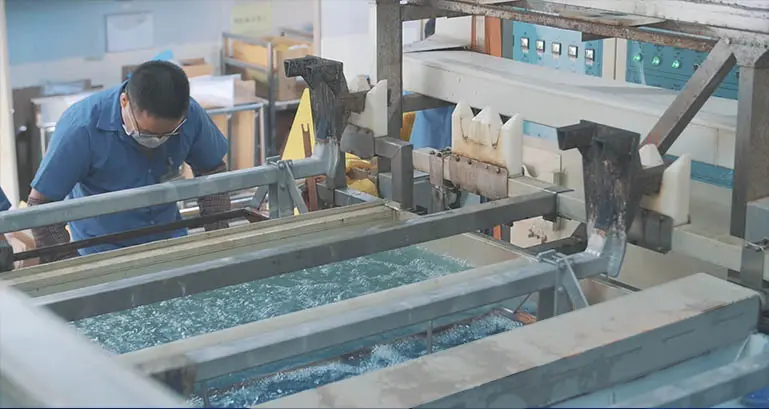
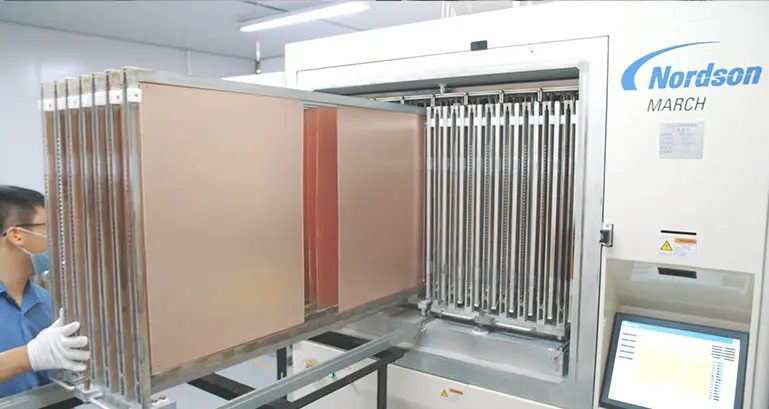
2 - PULIZIA AL PLASMA
Per i prodotti ad alta tecnologia è preferibile il processo al plasma: in grado di rimuovere i residui più duri come le poliimmidi, l’FR4 ad alto Tg, il teflon e i materiali per RF/microonde. Questo processo opzionale fornisce un’eccellente rugosità e bagnabilità per la deposizione chimica del rame.
3 - PLACCATURA AL PALLADIO
Esistono diversi trattamenti chimici per ottenere fori conduttivi, possiamo utilizzare rame, palladio, grafite, polimero, a seconda della tecnologia PCB in fase di creazione. Le schede vengono immerse in un bagno di palladio, noto anche come bagno di attivazione, per depositare un sottile strato di palladio.
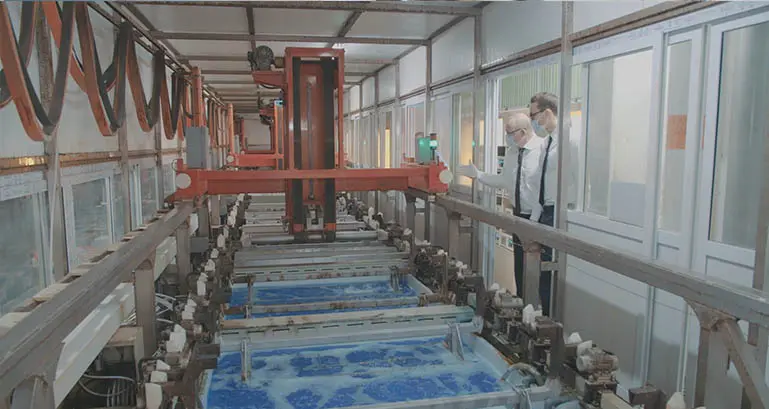
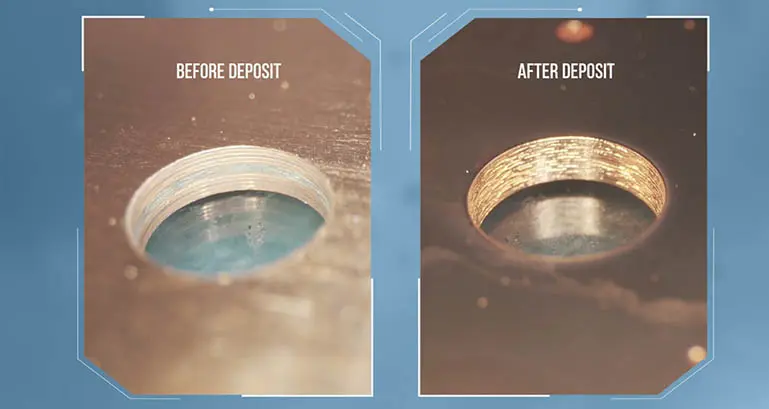
4 - PLACCATURA AL RAME
I pannelli vengono costantemente spostati nel bagno per rimuovere le potenziali bolle d’aria che si possono essere formate all’interno dei fori. Il palladio agisce chimicamente in modo da attirare un deposito di rame chimico da 1 a 3 micrometri sull’intera superficie del pannello e sui fori appena praticati.
5 - CONTROLLI
Al termine di questo processo viene effettuato un controllo, principalmente un test di retroilluminazione per verificare la porosità e il rivestimento del rame.
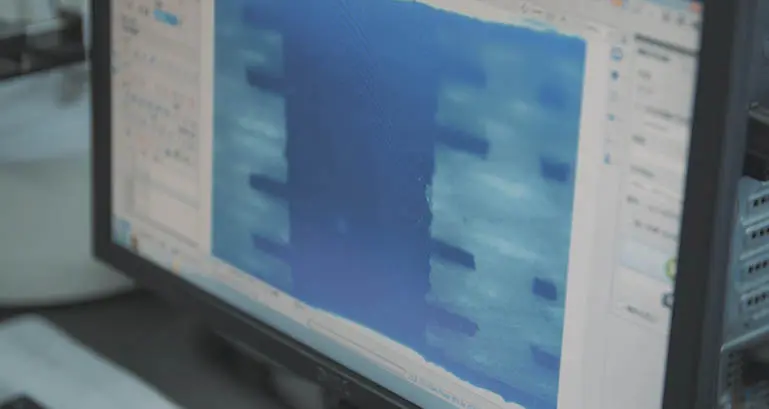
Imaging dello strato esterno
Come creare un’immagine perfetta dello strato esterno?
L’Outer Layer Imaging (imaging dello strato esterno) è simile all’Inner Layer Imaging (imaging dello strato interno), ma molto più complesso con i fori e la rugosità della superficie. Vediamo come si svolge questa spettacolare fase del processo di produzione dei PCB!
1 - PREPARAZIONE E LAMINAZIONE
La superficie viene preparata: le schede più sottili di 500 micrometri sono sottoposte a un processo di pulizia chimica, mentre quelle più spesse sono sottoposte a un processo di pulizia meccanica con spazzole abrasive. Le schede vengono riscaldate per migliorare l’adesione della pellicola fotoresistente. Quindi, le schede vengono rivestite con una laminazione automatica su X e Y. Il bordo viene tagliato direttamente dalla macchina.
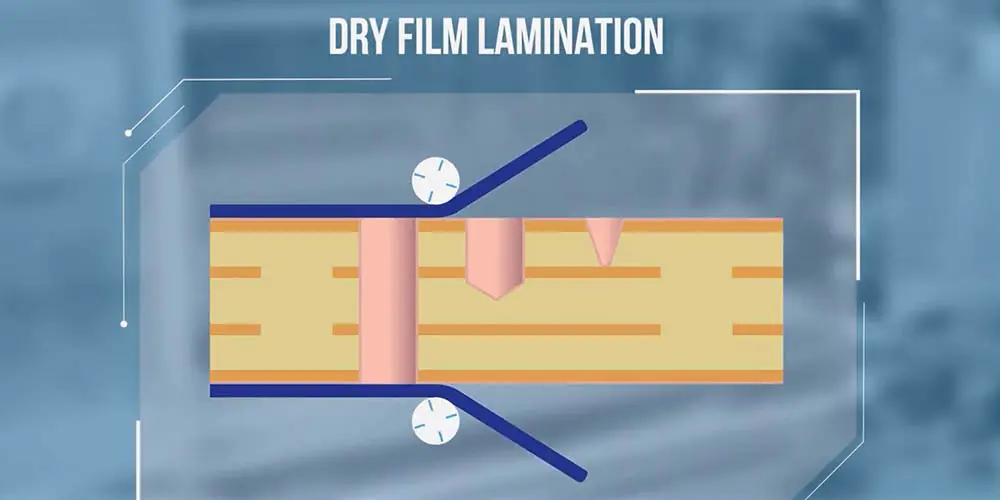
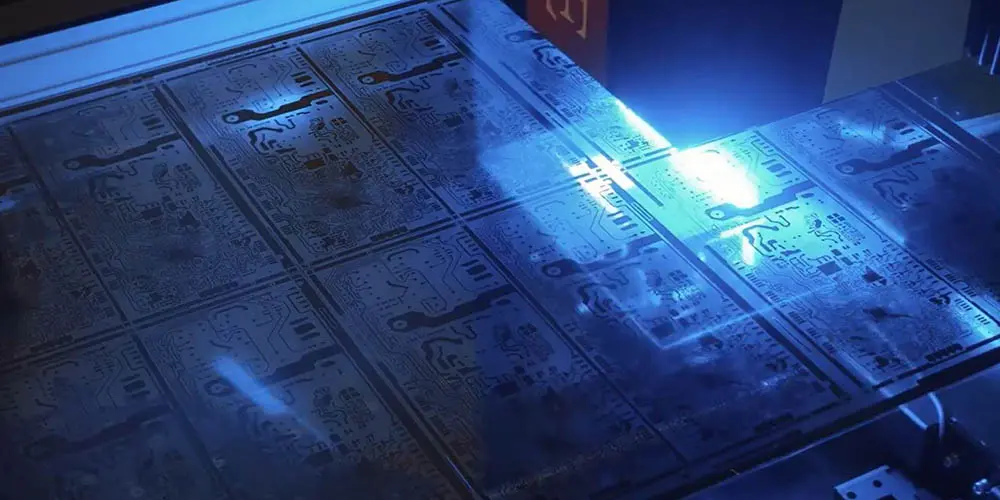
2 - REGISTRAZIONE E INSOLAZIONE UV
Per l’insolazione semiautomatica, il disegno modello (artwork) viene controllato nuovamente prima di essere aggiunto alla macchina. La registrazione avviene otticamente tra i fori e i target con 2 o 4 telecamere CCD. Una volta che il pannello soddisfa i criteri di qualità, viene applicato il vuoto, quindi la scheda viene sottoposta a un fascio di luce UV tra 1 e 20 secondi per polimerizzare la fotoresistenza, creando un’immagine del circuito.
3- REGISTRAZIONE E INSOLAZIONE LASER
Per i prodotti di fascia alta e i materiali ad alta densità, si utilizza il Laser Direct Imaging. Questa macchina è completamente automatica, quindi il caricamento, la registrazione con 4 telecamere CCD e il trasferimento dell’immagine dello strato avvengono in pochi secondi. L’LDI è un fattore importante anche quando si tratta di tolleranze strette e di registrazioni minime, dell’ordine dei 50 micrometri o meno.
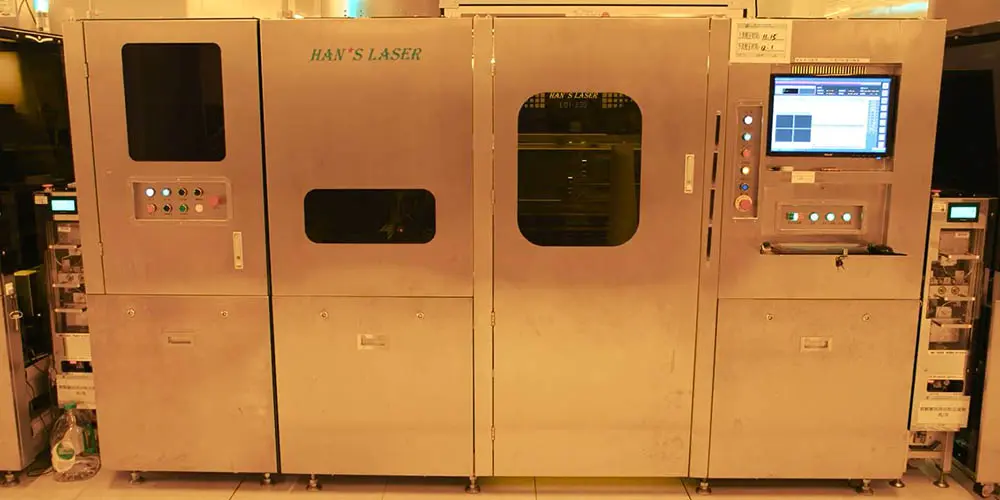
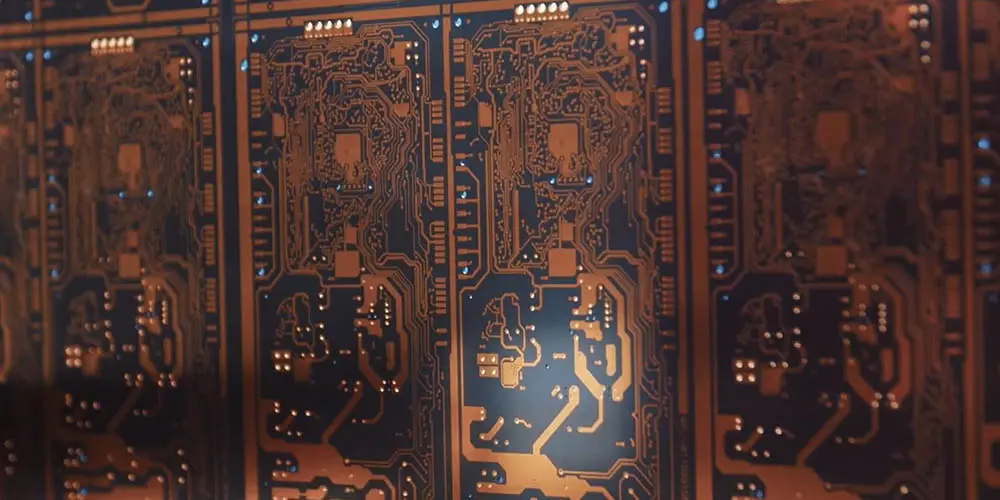
4 - SVILUPPO
Una volta terminata l’insolazione, la protezione sul dry film viene rimossa. Le aree non esposte alla luce UV o al laser non sono indurite e si dissolvono nel bagno di sodio di sviluppo, portando le schede a questo bellissimo colore blu. L’immagine dello strato esterno è ora stampata, pronta a ricevere il rame elettrolitico.
5 - ISPEZIONE OTTICA AUTOMATICA
L’ispezione ottica automatica degli strati esterni confermerà la totale assenza di difetti, siano essi aperture o cortocircuiti elettrici. Come per lo strato interno, il disegno originale del file GERBER serve come modello per la fotocamera ottica. Se la macchina rileva un’incongruenza, un tecnico valuterà il problema.
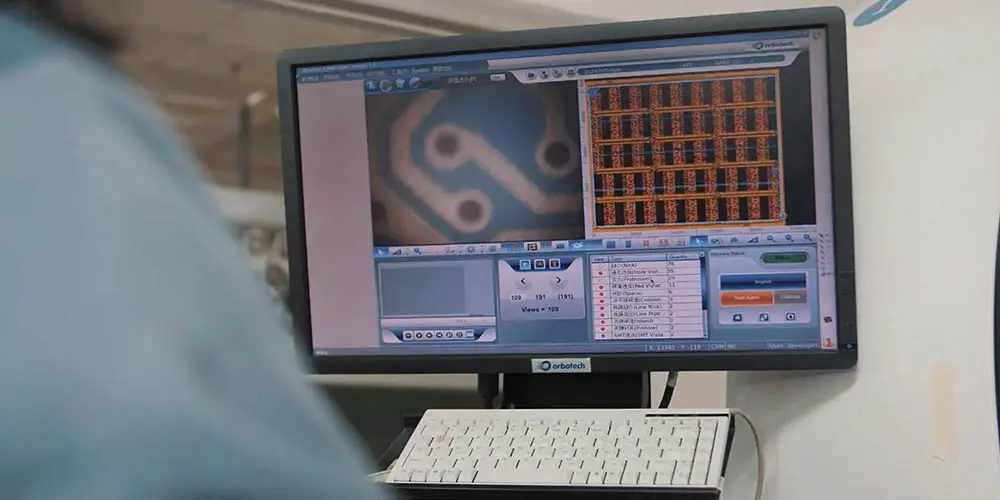
Rame elettrolitico
Che cos’è la deposizione elettrochimica del rame?
Il rame può essere depositato elettroliticamente sulla scheda con due processi: placcatura del pannello e placcatura del pattern.
1 - PLACCATURA DEL PANNELLO
Il rame viene depositato elettroliticamente su tutta la superficie e all’interno dei fori per migliorare la planarità e la distribuzione. Il rame elettrolitico crea l’elettrolisi, ovvero un flusso di corrente elettrica attraverso un liquido che provoca cambiamenti chimici. Dopo diversi bagni di 3 minuti ciascuno, si crea l’elettrolisi, il rame nel bagno agisce come un anodo e le schede come un catodo.
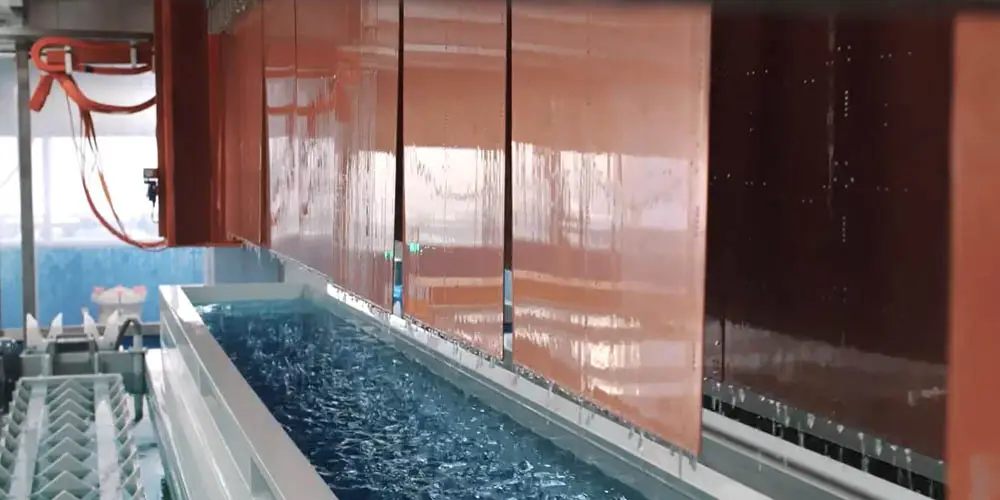
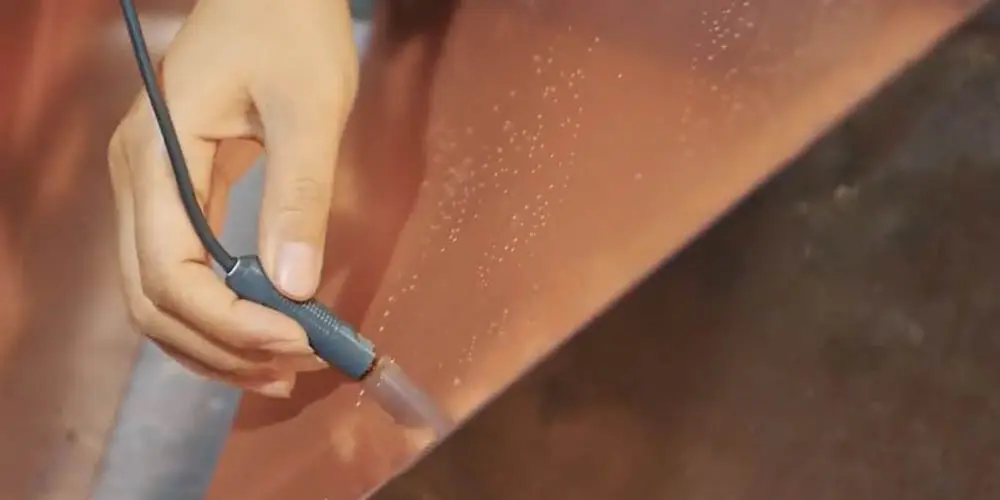
2 - CONTROLLI
La scheda è ora più spessa e più affidabile, con circa 10-13 micrometri di rame. Il passo successivo per queste schede sarà l’imaging dello strato esterno.
3 - PLACCATURA DEI MODELLI - DEPOSIZIONE DI RAME
Il rame viene depositato elettroliticamente, ma in quantità molto maggiori. Per creare una buona connessione e una buona conduttività tra i fori, le schede devono avere almeno 20-25 micrometri di rame all’interno dei fori della parete, secondo gli standard IPC. Il rame, che funge da anodo, si deposita sulle schede durante un bagno di 60 minuti.
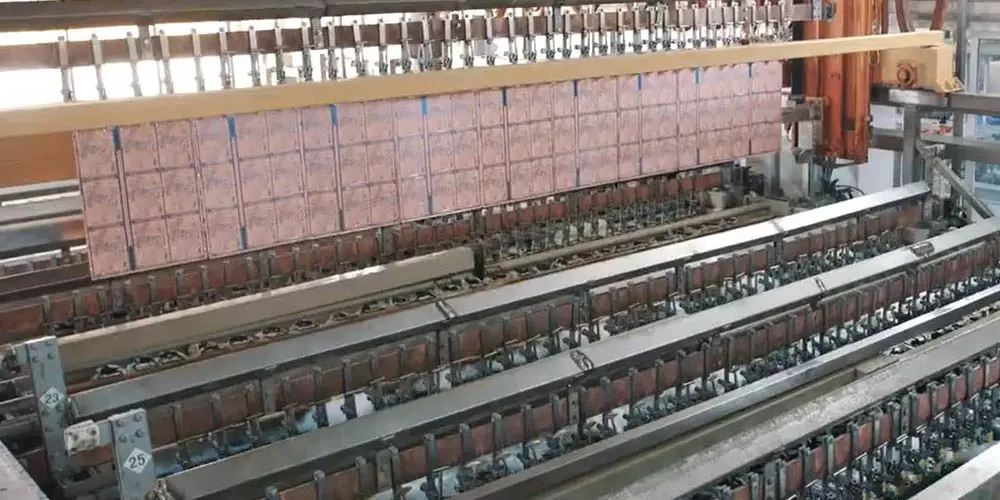
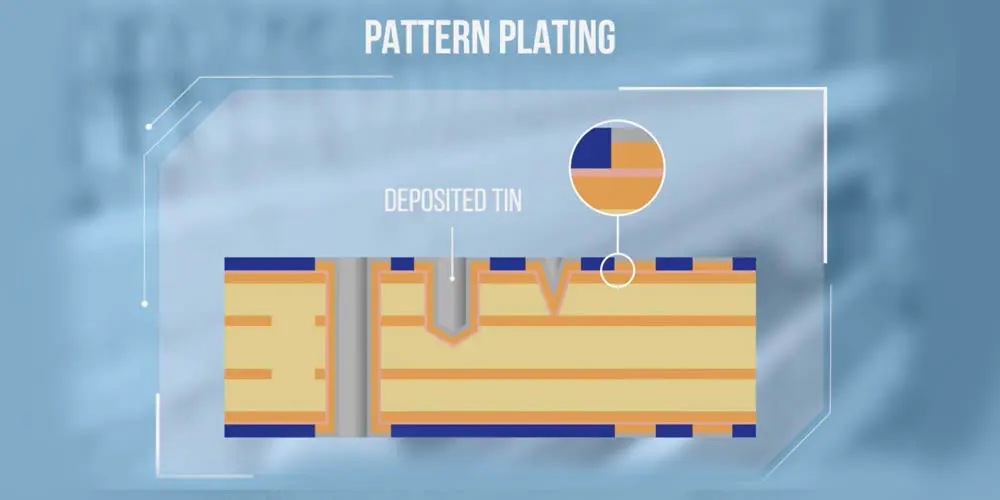
4 - PLACCATURA DI MODELLI - DEPOSIZIONE DI STAGNO
Dopo un bagno di risciacquo, le schede vengono immerse nello stagno elettrolitico che ricopre tutto il rame con uno strato di circa 1 – 3 micrometri. Lo stagno è essenziale per proteggere il rame durante il processo di incisione.
5 - CONTROLLI
Una volta ricoperte completamente, vengono testate con un metodo non distruttivo per verificare lo spessore del rivestimento.
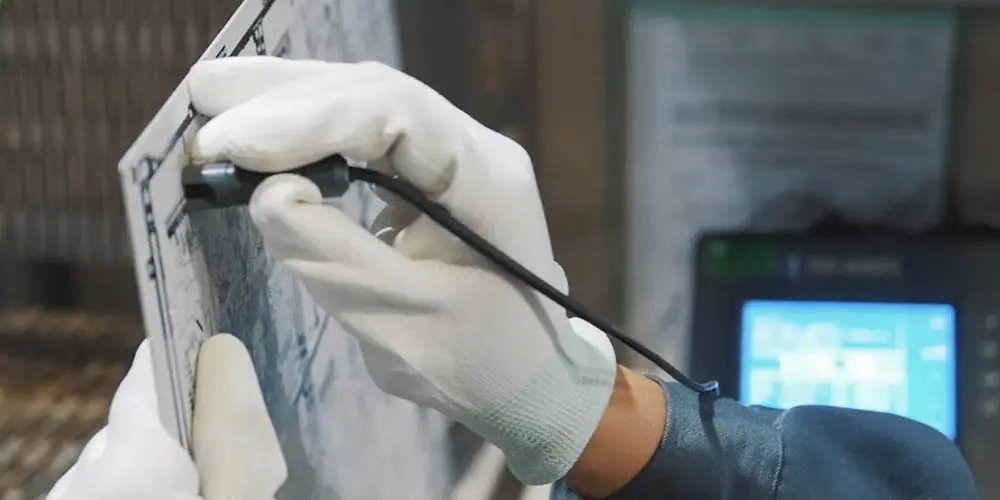
Incisione di PCB
Che cos’è l’incisione?
L’incisione è un processo chimico complesso che rimuove il rame e lo stagno indesiderati sulle schede.
1 - STRIPPAGGIO DEL FILM
La prima fase inizia con il dry film. Tutti i residui vengono sciolti e il film viene rimosso, lasciando esposto il rame indesiderato.
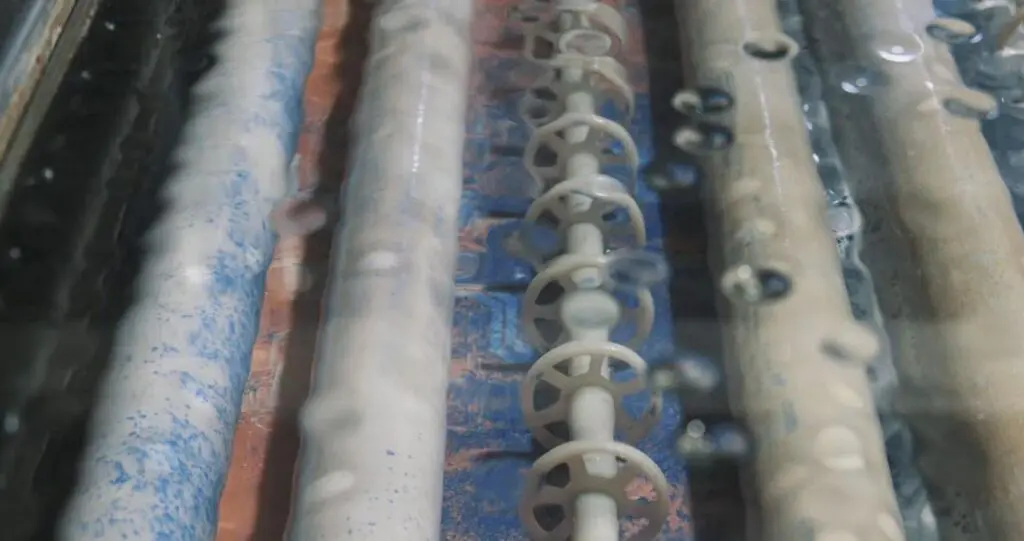
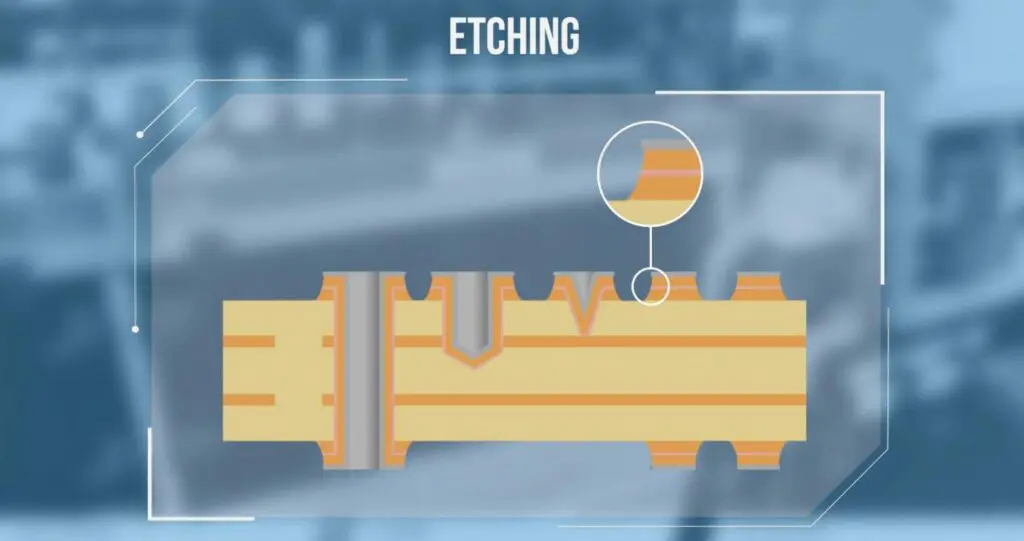
2 - INCISIONE
La fase di incisione inizia in un bagno di soluzione chimica. La sfida consiste nell’evitare la sovraincisione o la sottoincisione che impedirebbero di ottenere una parete diritta. Per quanto riguarda lo strato interno, il rame scoperto viene inciso e definisce il pattern. Qui lo stagno protegge il rame e i fori.
3 - STRIPPAGGIO DELLO STAGNO
Lo stagno viene rimosso chimicamente e strippato. Le aree conduttive e le connessioni sono ora correttamente stabilite.
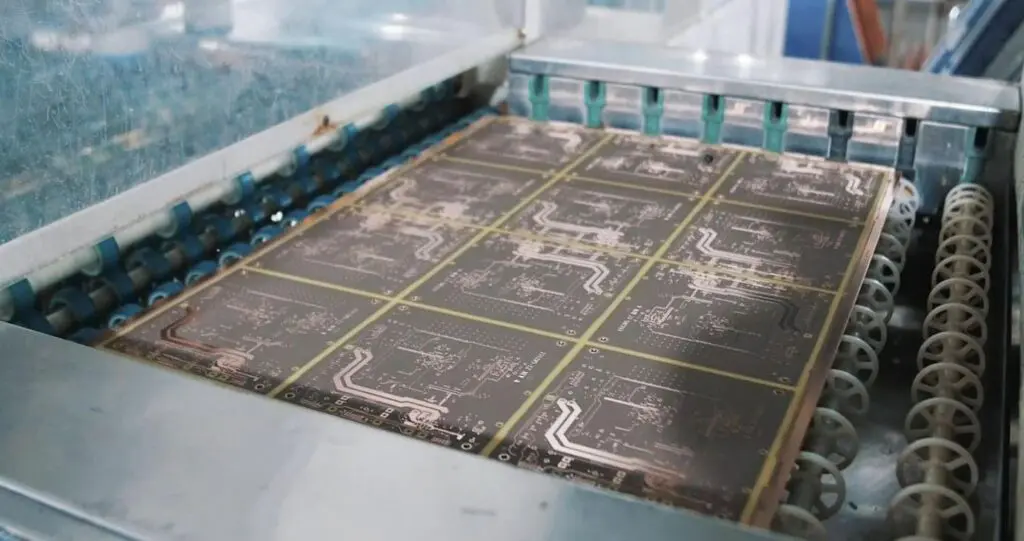
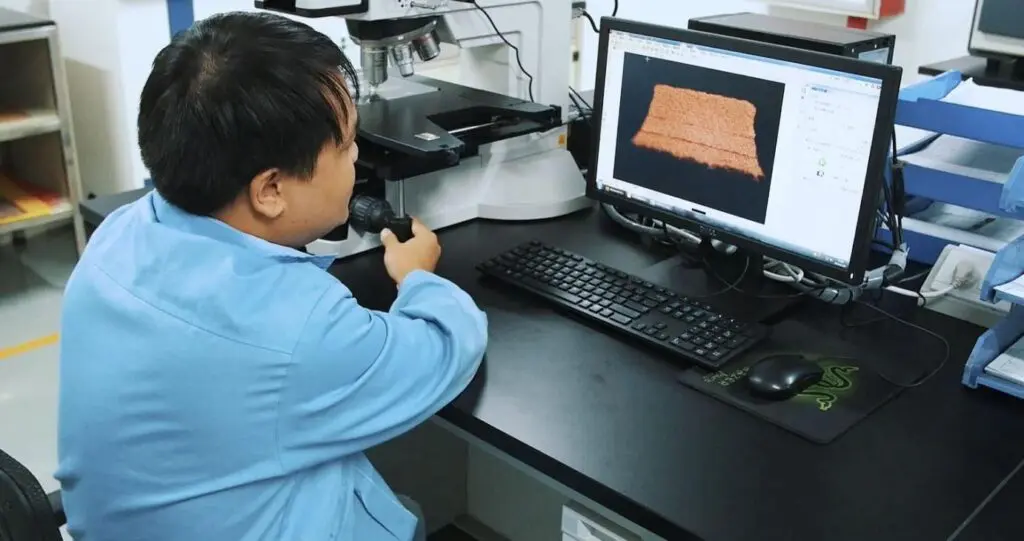
4 - CONTROLLI
Viene eseguito un test di laboratorio per verificare la sovraincisione e la sottoincisione e per assicurarsi che tutti gli strati di rame indesiderati siano stati rimossi, ad eccezione dello strato di sostanza di protezione.
5 - ISPEZIONE OTTICA AUTOMATICA
L’ispezione ottica automatica viene eseguita direttamente dopo l’incisione e confrontata con i dati per evidenziare eventuali incongruenze e garantire l’assenza di difetti. In alcuni casi, un cortocircuito o un’apertura elettrica possono essere riparati in questa fase.
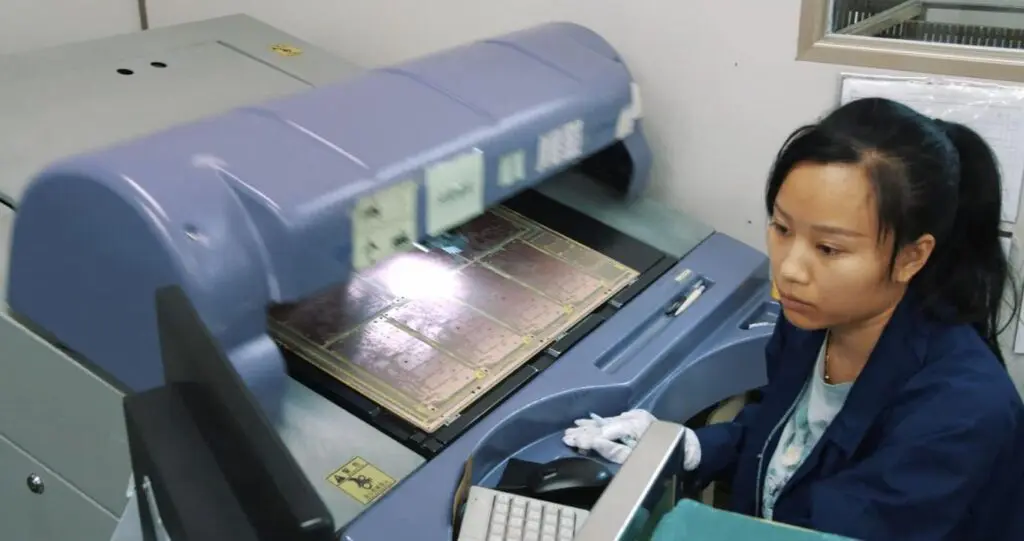
Soldermask per PCB
Perché i PCB hanno bisogno di soldermasks?
La maschera di saldatura presenta due vantaggi. Il primo è quello di evitare l’ossidazione del rame e il secondo è quello di avere un perfetto isolamento tra due tracce di rame durante il processo di assemblaggio. Esistono diversi tipi di maschere di saldatura per circuiti stampati, come quelle liquide epossidiche, liquide fotoimmaginabili (LPI) o a dry film. Immergiamoci in questa storia!
1 - RIVESTIMENTO
Esistono diversi modi per applicare la maschera di saldatura a un PCB: spalmatura a velo, serigrafia o rivestimento per nebulizzazione elettrostatica secondo gli standard IPC. Prima di applicare la maschera di saldatura, le schede devono essere pulite con una preparazione meccanica o chimica in una camera bianca sovrapressurizzata per evitare l’ingresso di polvere dall’esterno.
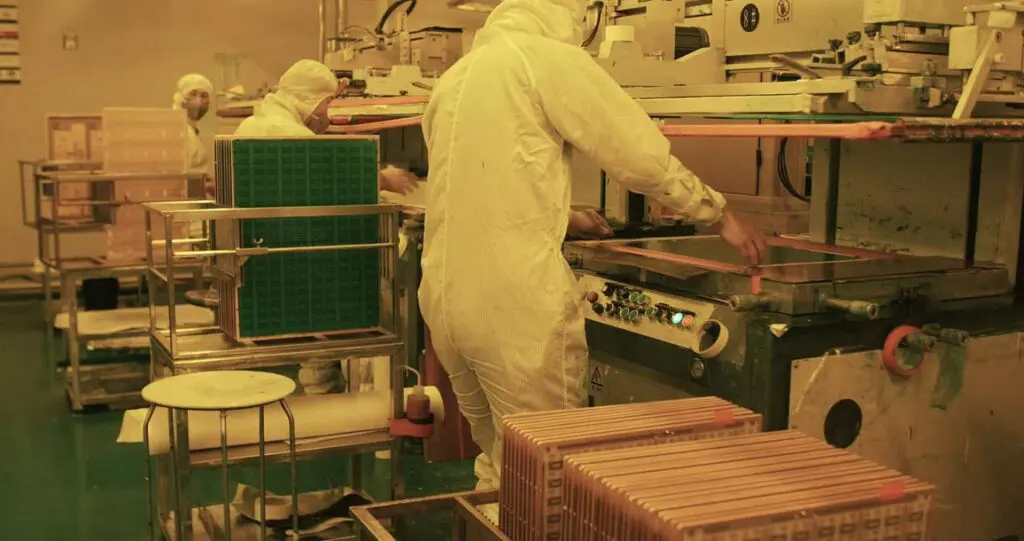
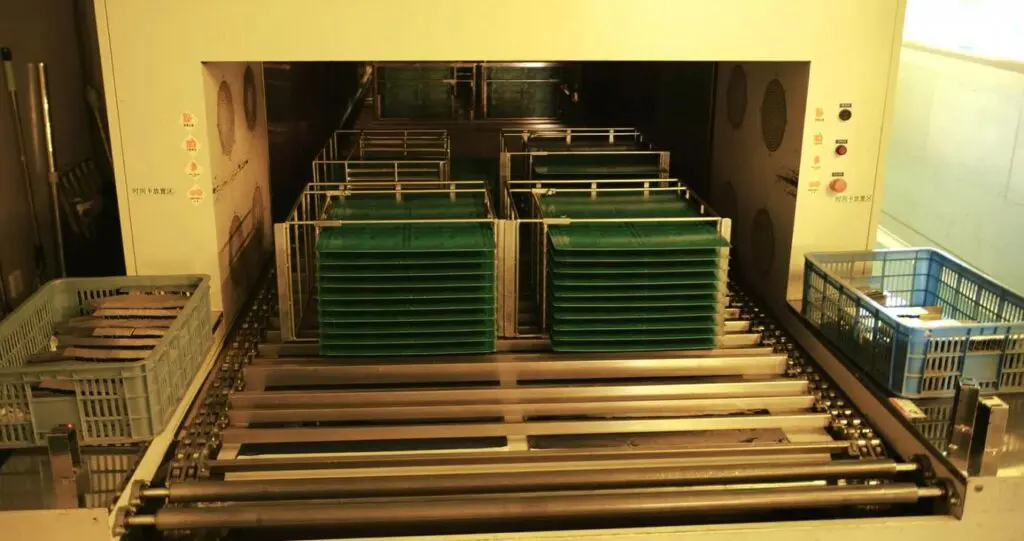
2 - PREINDURIMENTO
Una volta che il pannello è completamente rivestito, deve essere preindurito. Questo passaggio è essenziale e rimuove tutto il solvente dall’inchiostro. Senza questo passaggio, la registrazione non sarà effettuata correttamente.
3 -REGISTRAZIONE/INSOLAZIONE
Per la maschera di saldatura, l’insolazione può essere effettuata con la registrazione con 8 telecamere CCD e il disegno modello (artwork). Le schede ricevono un fascio di luce LED per alcuni secondi per indurire la maschera di saldatura dove il disegno modello è chiaro. L’insolazione può essere effettuata anche tramite LDI, Laser Direct Imaging. Questa volta non è necessaria alcun disegno modello (artwork), perché la macchina espone direttamente i punti selezionati con i fasci di luce e indurisce il punto mirato.
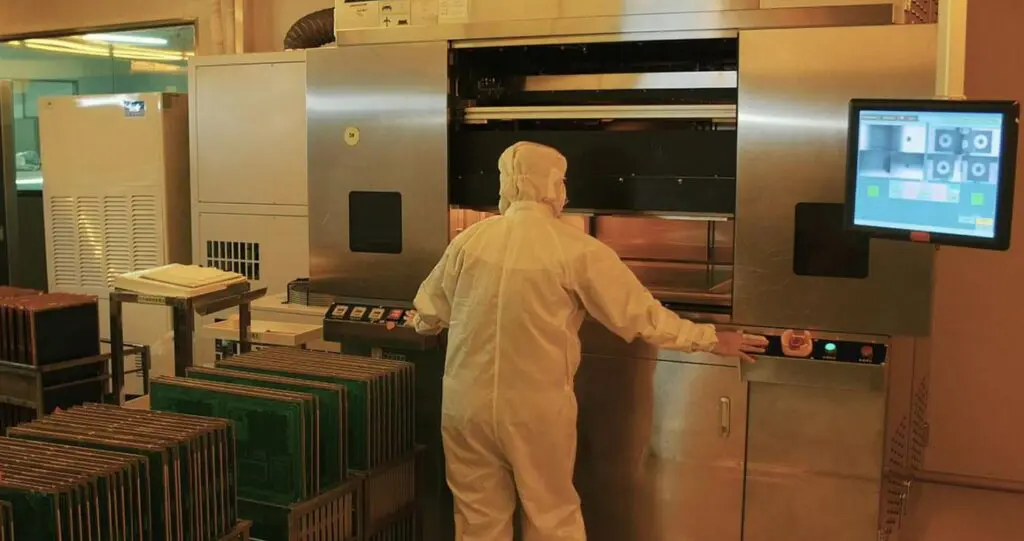
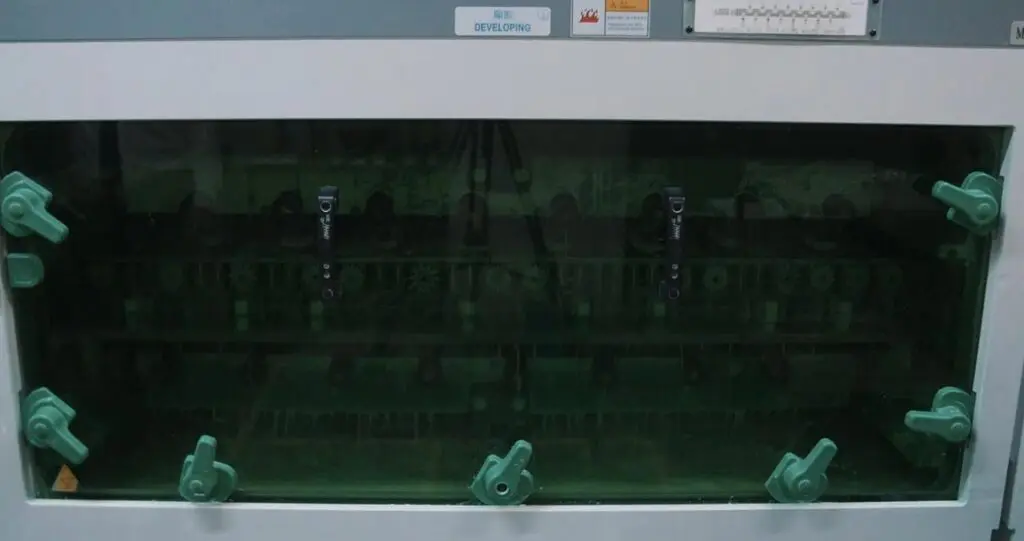
4 - SVILUPPO
Le parti non protette e non indurite dall’insolazione vengono lavate via. Nel nostro esempio, viene rimossa la maschera di saldatura attorno al foro passante meccanico.
5 - CONTROLLO E INDURIMENTO
Dopo la fase di sviluppo, tutte le schede vengono controllate. Infatti, è necessaria un’ispezione per verificare se ci sono immagini difettose, tracce di inchiostro sui pad o attraverso i fori. Infine, le schede vengono esposte ad alta temperatura per un’ora per indurire la maschera di saldatura.
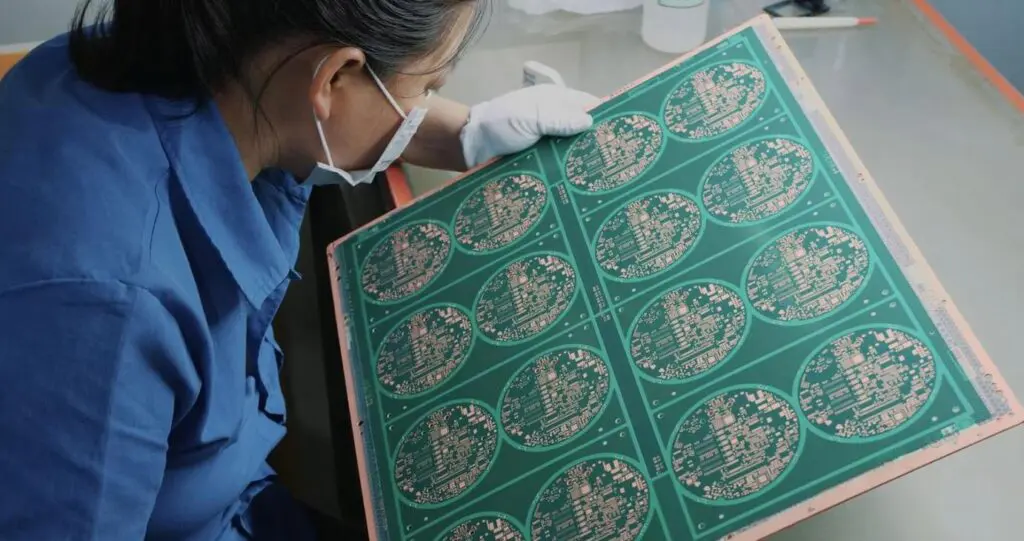
Serigrafia dei PCB
La serigrafia è importante su un PCB?
Il processo di serigrafia stampa tutte le informazioni vitali sul pannello, come i marchi del produttore, i numeri identificativi dell’azienda e le etichette di avvertenza. In questo processo vengono utilizzati principalmente due metodi: la serigrafia e la DLP, acronimo per Direct Legend Printing, con una stampante a getto d’inchiostro. Sembra facile, ma come ogni fase del processo di produzione dei PCB, richiede precisione.
1 - SERIGRAFIA
Come nella maggior parte delle fasi di produzione dei circuiti stampati, il disegno modello (artwork) del file GERBER è essenziale nel processo serigrafico del pattern. Il primo metodo è la serigrafia, nota anche come stampa serigrafica. Che siano manuali o automatici, entrambi i metodi richiedono schermi in poliestere tesi su telai in alluminio. Sia i telai in alluminio che il pannello vengono registrati per garantire un allineamento corretto, per evitare che l’inchiostro di stampa finisca sul pattern in rame e per assicurare che il processo di saldatura non venga influenzato. L’inchiostro viene spinto attraverso lo stencil sul laminato.
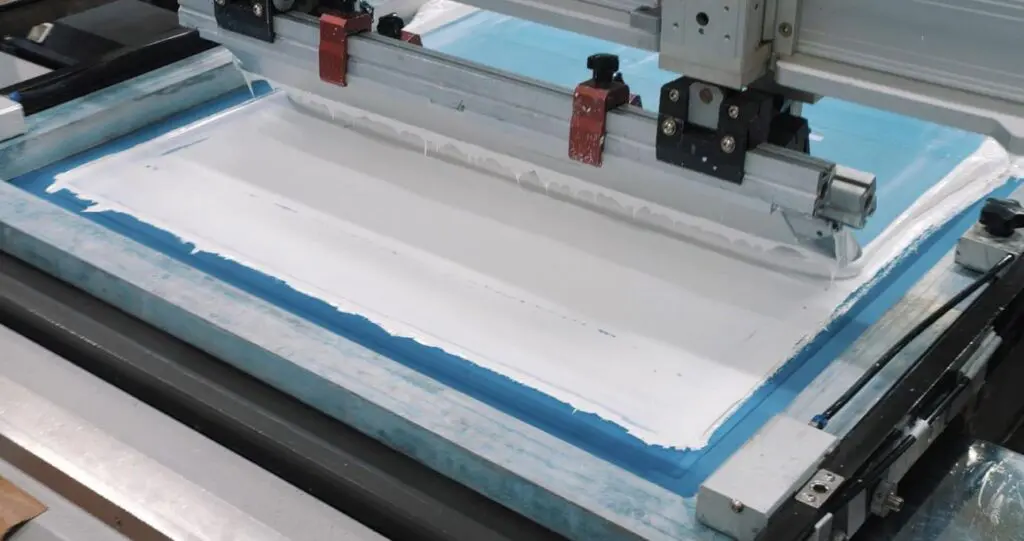
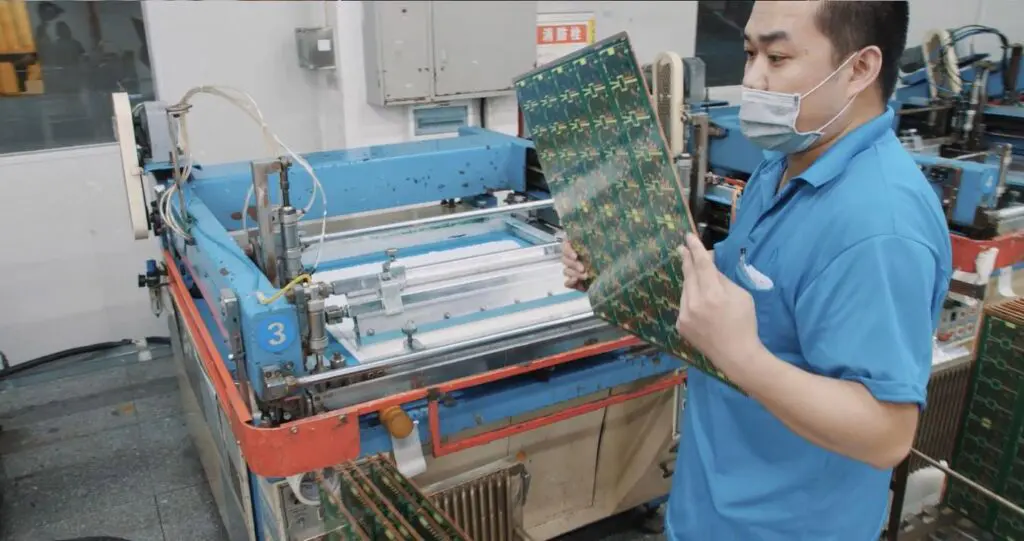
2 - CONTROLLI
Una volta che il PCB è stato serigrafato con le informazioni corrette, l’operatore esegue un’ispezione visiva. In caso di difetto, l’operatore valuterà il problema o rimuoverà la scheda dal processo di produzione
3 - CURING
Se il risultato della serigrafia è buono, le schede vengono indurite per far indurire l’inchiostro.
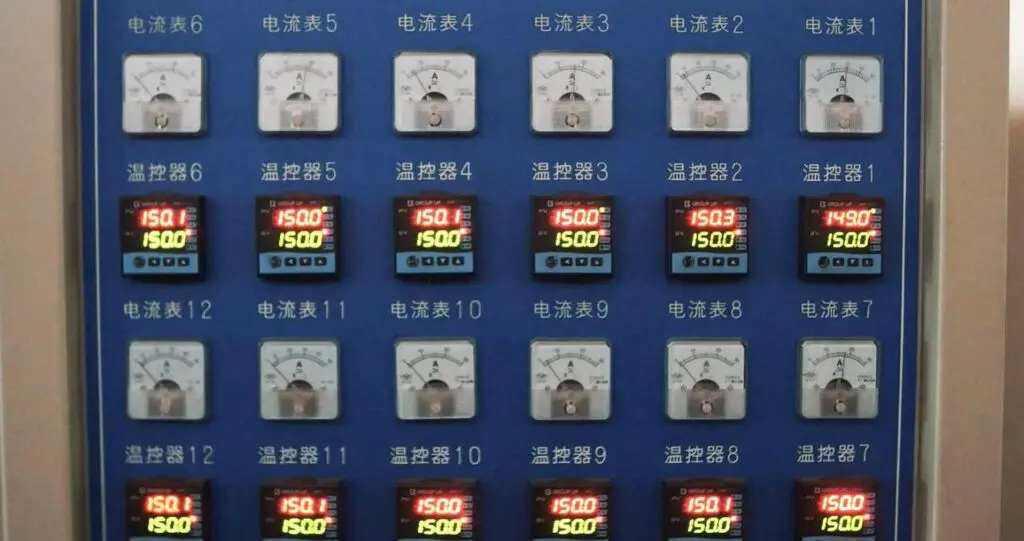
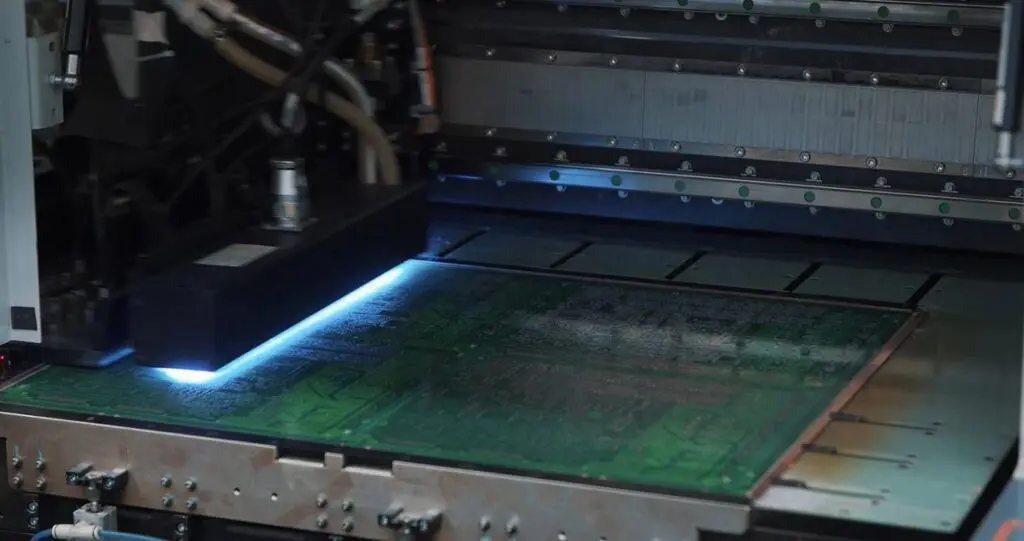
4 - INKJET
Il secondo processo di applicazione del testo serigrafato funziona come una tradizionale stampante a getto d’inchiostro ed è noto come DLP o Direct Legend Printing. La registrazione viene effettuata automaticamente dalla macchina. La stampante a getto d’inchiostro spruzza gocce d’inchiostro sul pannello per generare l’immagine. Queste gocce d’inchiostro vengono indurite direttamente dalle luci UV.
5 - CONTROLLI
L’operatore effettua anche un controllo visivo per verificare che la serigrafia sia eseguita correttamente. Nonostante le apparecchiature più moderne, la DLP è preferibile solo per la prototipazione e i piccoli volumi, mentre la serigrafia è molto più veloce e viene utilizzata per la produzione di massa.
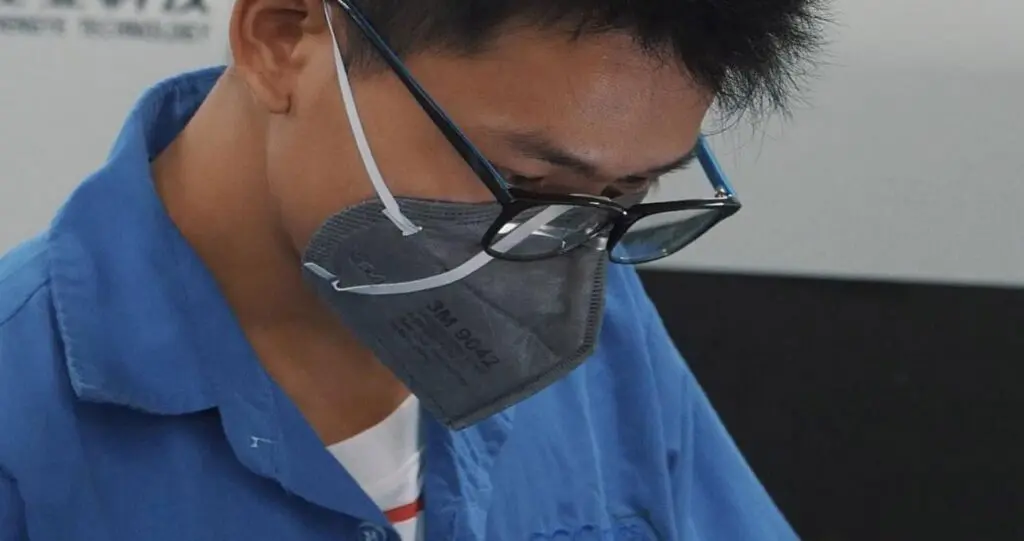
Finitura superficiale dei PCB
Quali sono le finiture superficiali disponibili?
La finitura superficiale è un rivestimento tra un componente e una scheda PCB nuda. Si usa principalmente per due motivi: Garantire la saldabilità durante la fase di popolamento e proteggere il rame dall’ossidazione.
1 - OSP
OSP è l’acronimo inglese di Organic Solderability Preservative (Preservante organico della saldabilità). È una finitura superficiale a base d’acqua. Rispettosa dell’ambiente, le schede vengono pulite prima di essere sottoposte ai bagni per ottenere un’eccellente superficie piana. Questo processo rapido non richiede molte attrezzature, il che lo rende una finitura superficiale economicamente vantaggiosa. L’OSP ha una breve durata di conservazione e può essere sensibile durante la manipolazione. Di conseguenza, il processo di fresatura viene eseguito prima dell’applicazione della finitura superficiale. Per riassumere, la finitura superficiale OSP è ecologica, fornisce una superficie piatta, è una soluzione economica che può essere riattivata. Ci sono anche degli svantaggi, come la breve durata di conservazione, può essere sensibile durante la manipolazione e questa finitura può esporre il rame durante l’assemblaggio finale.
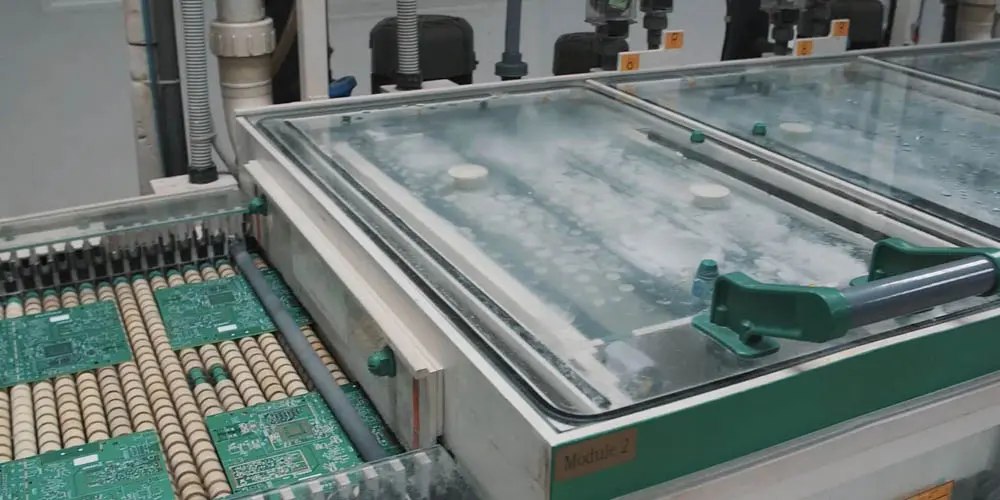
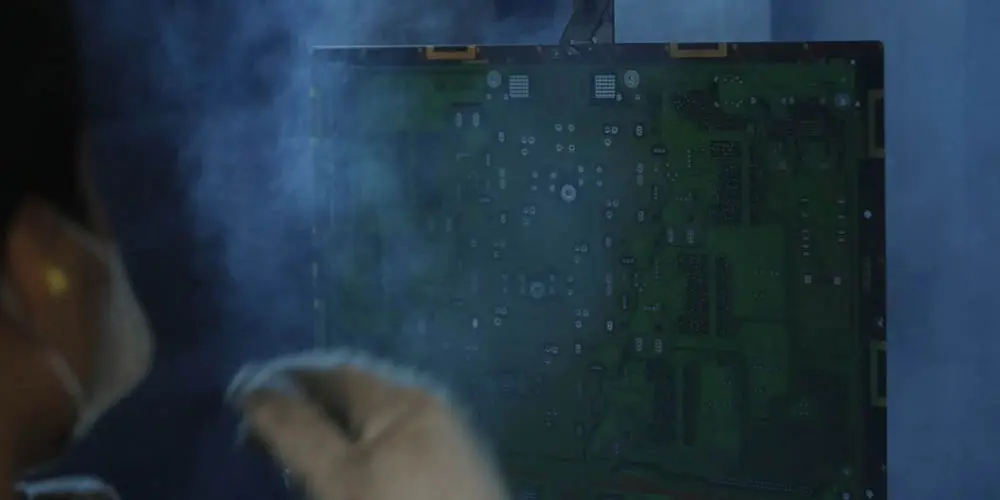
2- LEAD-FREE HASL (HASL SENZA PIOMBO)
HASL senza piombo è l’abbreviazione di Hot Air Solder Leveling (livellamento della saldatura ad aria calda). È stata una delle finiture più popolari fino a pochi anni fa. Anche se questa finitura è robusta, il prezzo basso è legato anche ai suoi limiti. Durante l’applicazione, l’intero pannello viene sottoposto a micro-incisione per pulirlo e poi riceve un rivestimento di disossidante per favorire l’adesione della finitura superficiale. Successivamente, la scheda viene immersa nella saldatura a stagno liquida e viene rimossa utilizzando due coltelli ad aria compressa che soffiano aria compressa calda sulla superficie delle schede. La soluzione senza piombo è un vantaggio indiscutibile per i prodotti ad alta affidabilità. Tuttavia, con un numero sempre maggiore di PCB HDI, questo processo produce superfici irregolari e non è adatto per i componenti a passo fine. In sintesi, la finitura superficiale HASL senza piombo è una tecnologia ampiamente disponibile, una soluzione a basso costo con una buona durata. Ci sono anche degli svantaggi, quali la superficie potenzialmente irregolare, non adatta per i componenti fine pitch e il processo che può divenire uno stress termico per le schede.
3 - ENIG
ENIG sta per Electroless Nickel Immersion Gold (Oro a immersione in nichel chimico). Questo processo richiede l’uso di nastro adesivo per coprire i contorni del circuito, per evitare l’eccessiva deposizione di oro e perché l’ENIG è un processo di finitura costoso. Il pannello viene immerso in diversi bagni, prima viene elettrodepositato uno strato di 3-6 micrometri di nichel per aumentare l’adesione. Quindi, un minimo di 0,05 micrometri di oro viene elettrodepositato anche sul pannello. La finitura a immersione garantisce un’eccellente planarità e l’uso dell’oro assicura una forte saldabilità. In sintesi, la superficie ENIG è ideale per l’incollaggio, ha una forte saldabilità, fornisce una superficie piatta e ha una buona durata. Ci sono anche degli svantaggi, soprattutto il fatto che questa superficie è un processo complesso che non rappresenta una soluzione economicamente vantaggiosa.
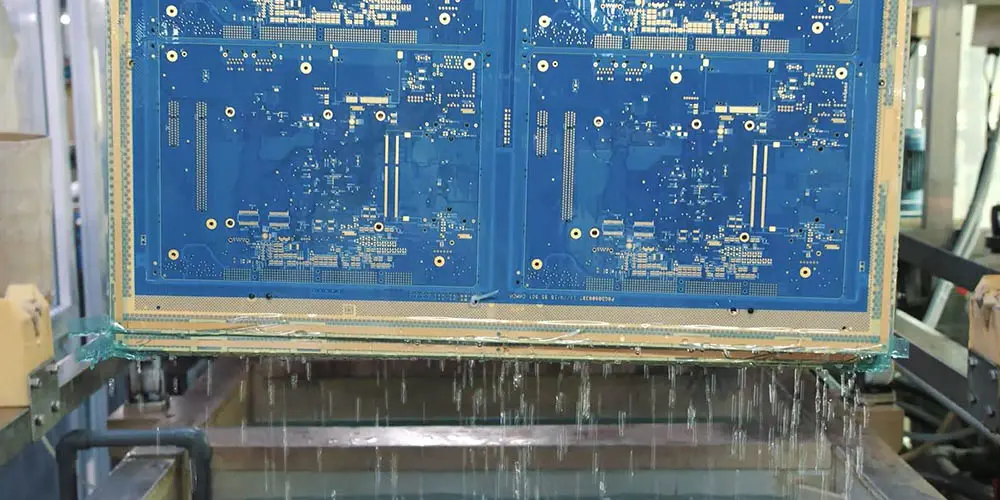
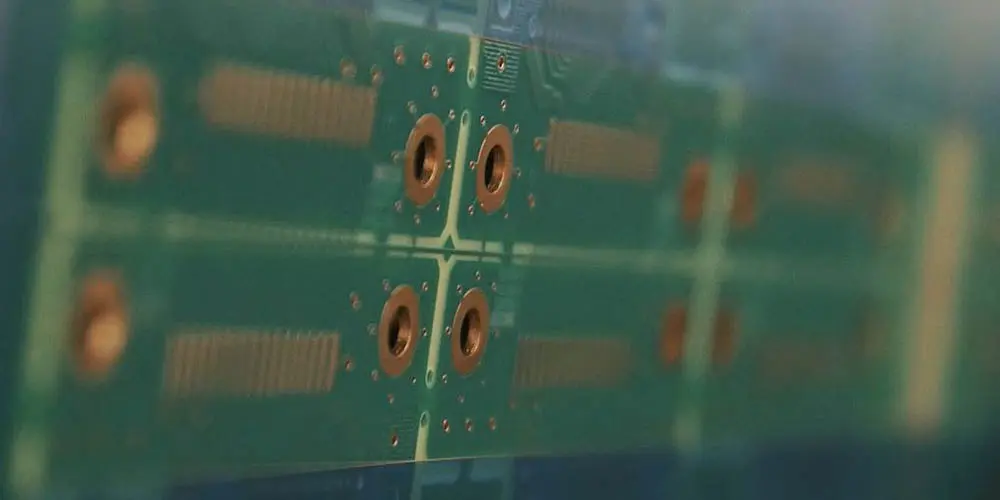
4 - HARD GOLD PLATING (PLACCATURA A ORO DURO)
Per la placcatura a oro duro, l’intero pannello è coperto da nastro adesivo. Viene rimossa solo la parte che richiede l’applicazione di una finitura superficiale. A differenza dell’ENIG, in questo caso lo spessore del rame può variare controllando la durata del ciclo di placcatura. Il nichel viene prima elettrodepositato, poi viene depositato l’oro secondo la richiesta del cliente. Lo spessore dell’oro offre un’eccellente durata di conservazione, ma è anche una delle opzioni di finitura superficiali più costose. In sintesi, la finitura superficiale della placcatura a oro duro ha proprietà meccaniche, un’eccellente durata di conservazione e fornisce una superficie piatta. Ci sono anche degli svantaggi, come il costo elevato, la scarsa saldabilità e la complessità del processo.
5 - IMMERSION TIN (STAGNO A IMMERSIONE)
Lo stagno a immersione è un deposito di finitura metallica.
Le schede vengono immerse in diversi bagni chimici per creare la migliore adesione per lo stagno. L’immersione garantirà una perfetta planarità e lo stagno proteggerà al meglio il rame sottostante. Si tratta di un’opzione economicamente vantaggiosa, ma la forte affinità tra lo stagno e il rame può provocare la formazione di baffi di stagno.
La finitura superficiale dello stagno a immersione è ampiamente disponibile, fornisce una superficie piatta, è una soluzione economica, ha una buona durata e può essere rilavorata.
Ci sono anche degli svantaggi, come la rilavorazione che è limitata, la manipolazione può essere delicata e c’è la possibilità che si formino dei baffi di stagno.
ICAPE Group richiede specificamente per un prodotto di finitura ad alta tecnologia una partnership con fabbriche con sede in Germania per realizzare l’Immersion Tin che si adatta alle aspettative dell’industria automobilistica tedesca.
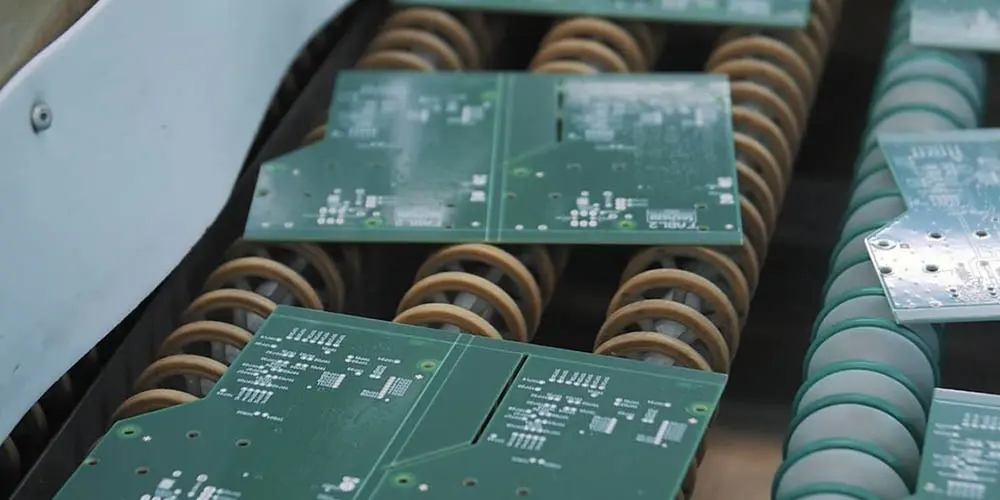
Disposizione dei PCB
Che cos’è il routing dei PCB?
Lo scopo del processo di fresatura, noto anche come profilatura, è quello di tagliare ogni circuito stampato dal pannello di produzione. Infatti, anche se tutte le schede elettroniche si trovano sullo stesso pannello, non appartengono necessariamente tutte allo stesso cliente
1 - PREPARAZIONE
L’operatore impila fino a 4 pannelli, con le stesse modalità del processo di perforazione. In questo caso, il processo di fresatura richiede una fresatrice e punte con un numero diverso di teste: 1, 2, 4 o 6 teste.
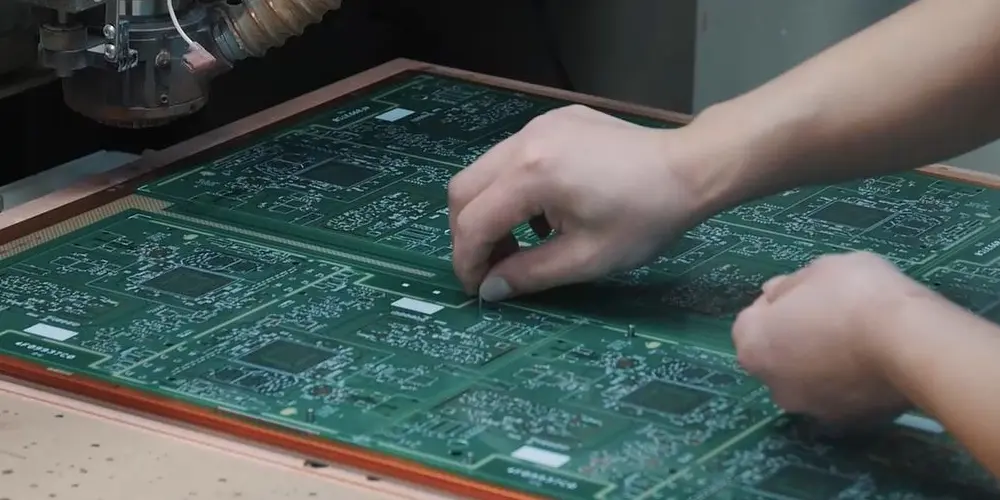
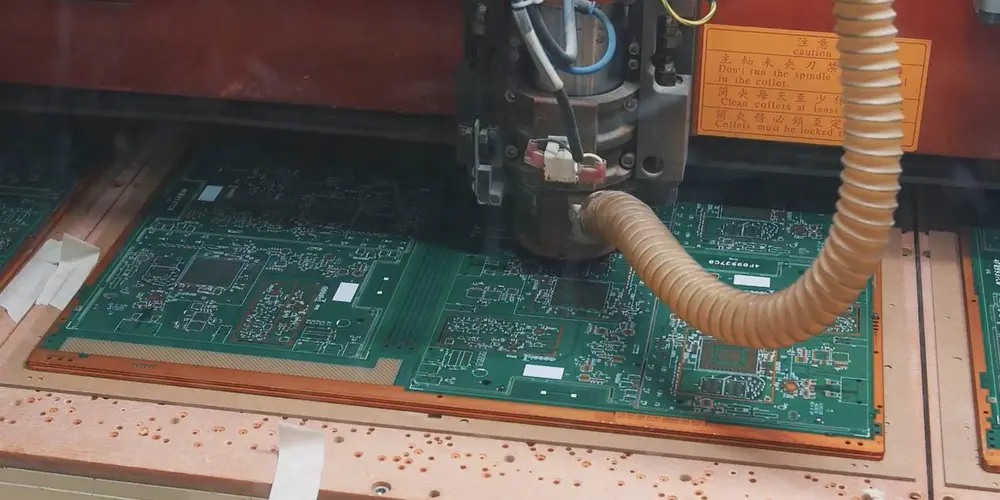
2 - FRESATURA
Durante questo processo vengono creati i contorni interni ed esterni del PCB. Allo stesso tempo, le schede vengono pulite per garantire che non rimangano polveri a seguito di questa operazione. Alla fine del ciclo, l’operatore rimuove tutti i pezzi dal tavolo e le schede dei circuiti sono ora depannellizzate. A seconda della richiesta del cliente, le schede possono essere fresate anche senza essere depannellizzate
3 - CONTROLLI
L’operatore controlla le dimensioni del processo di fresatura con una telecamera ottica per verificare che i contorni interni ed esterni siano stati fresati correttamente e non abbiano alterato il circuito.
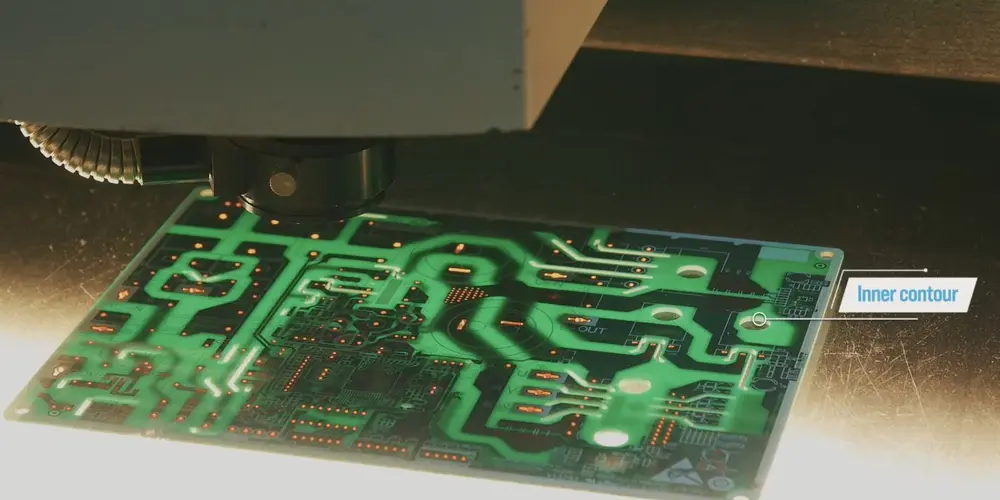
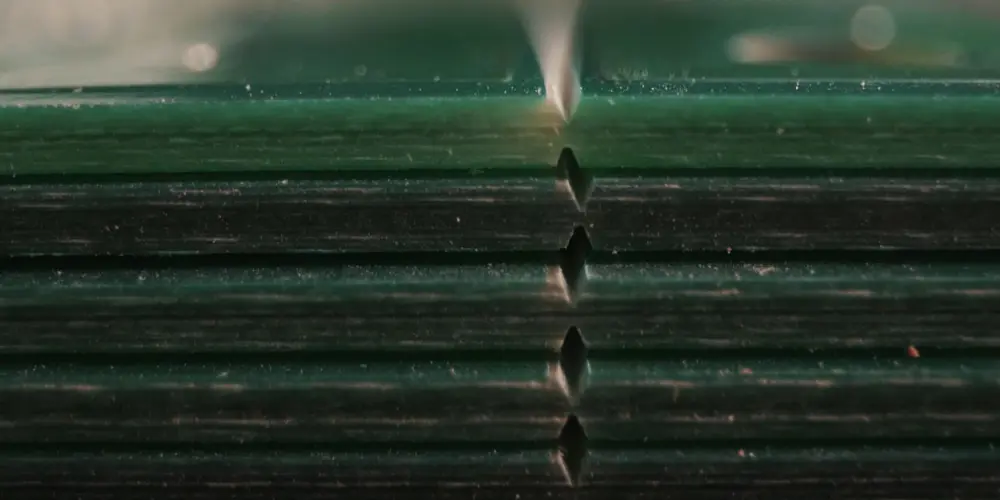
4 - TAGLIO A V
Dopo la fresatura, il V-Scoring o taglio a V viene utilizzato per pretagliare il PCB sul pannello del cliente, in modo che le schede possano essere separate dopo la fase di popolamento. Questo è l’obiettivo principale di questa fase. Le schede sono poi facili da staccare.
5 - CONTROLLI
Una volta completata, i controlli vengono eseguiti con un tester per misurare la profondità del taglio a V secondo il file GERBER.
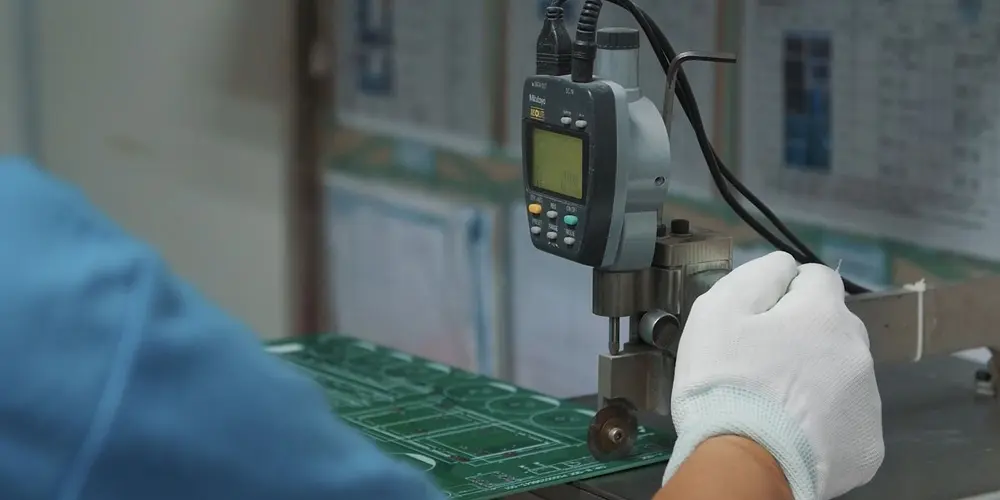
Test elettrici
Come controllare le aperture e i cortocircuiti su un PCB?
Questi test vengono eseguiti per garantire l’assenza di cortocircuiti e aperture sulle schede. Esistono due tipi di macchine con vantaggi diversi: la “flying probe” (sonda mobile) e il “bed of nails” (letto d’aghi).
1 - FLYING PROBE (SONDA MOBILE)
Il file GERBER viene letto dalla macchina, l’operatore posiziona le schede nel pannello o da solo. Poi le 4, 6 o 8 teste, distribuite su ogni lato, iniziano il loro lavoro: invia la carica elettrica al circuito, mentre i pad di contatto vengono toccati continuamente per assicurarsi che non vi siano circuiti aperti o cortocircuiti. In questo caso, un operatore interverrà per risolvere il problema.
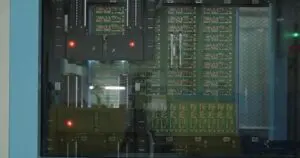
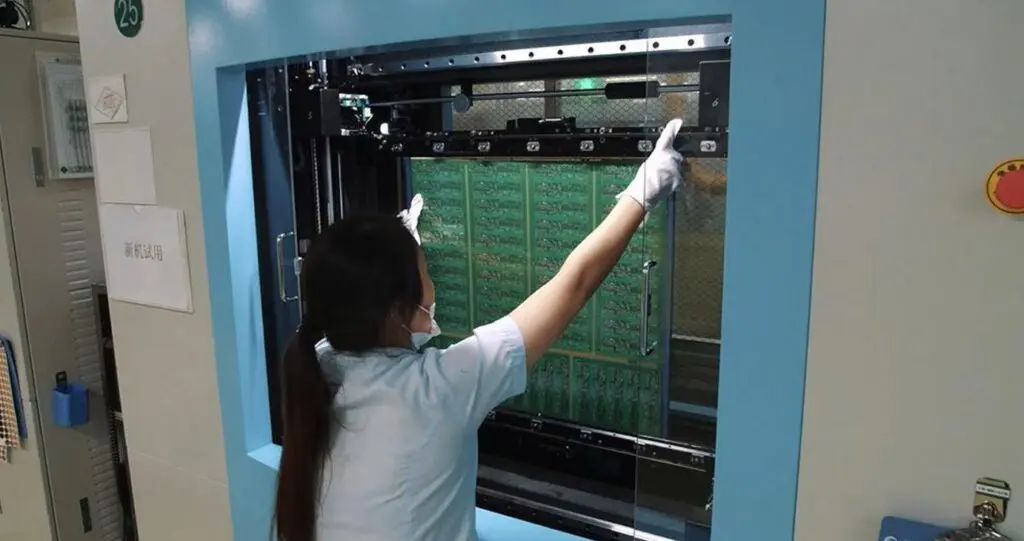
2- VANTAGGI E SVANTAGGI
L’utensileria è economicamente vantaggiosa e viene utilizzata soprattutto per la prototipazione e le piccole serie. È adatta anche per i circuiti stampati HDI, ma la principale limitazione è quella di cambiare ogni volta i circuiti stampati manualmente, prolungando di molto il ciclo operativo.
3 - BED OF NAILS (GRIGLIA DI PUNTI)
Il test della griglia universale, noto anche come Bed of nails (griglia di punti) richiede un supporto di prova. Il supporto di prova è progettato sulla base del file GERBER, quindi è diverso per ogni PCB. L’operatore deve inserire numerosi pin di varie dimensioni per coprire tutta l’area di prova. La preparazione è estremamente costosa e noiosa! I fori sono allineati ai punti di test del PCB e tutti i punti di test vengono controllati contemporaneamente, il che rende questa operazione molto veloce e affidabile.
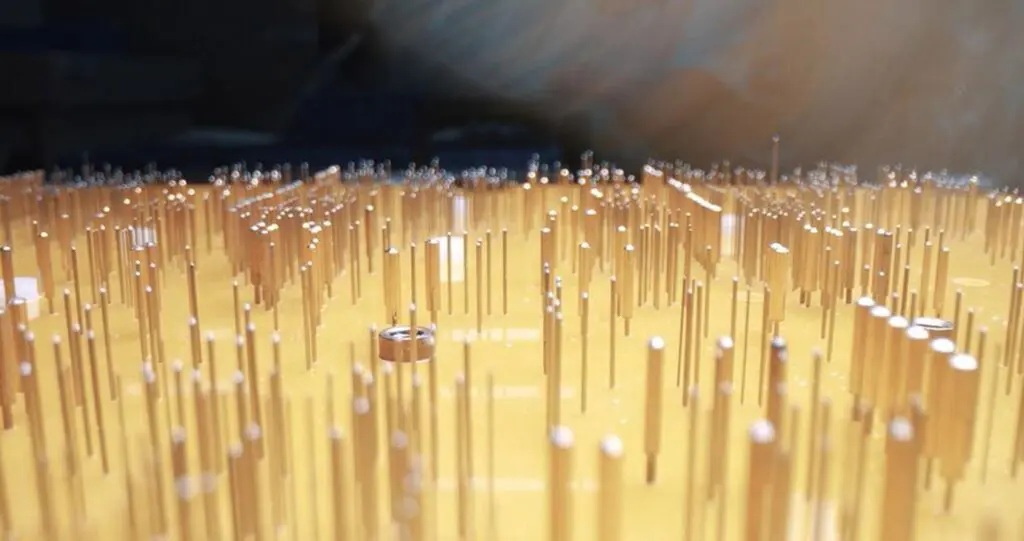
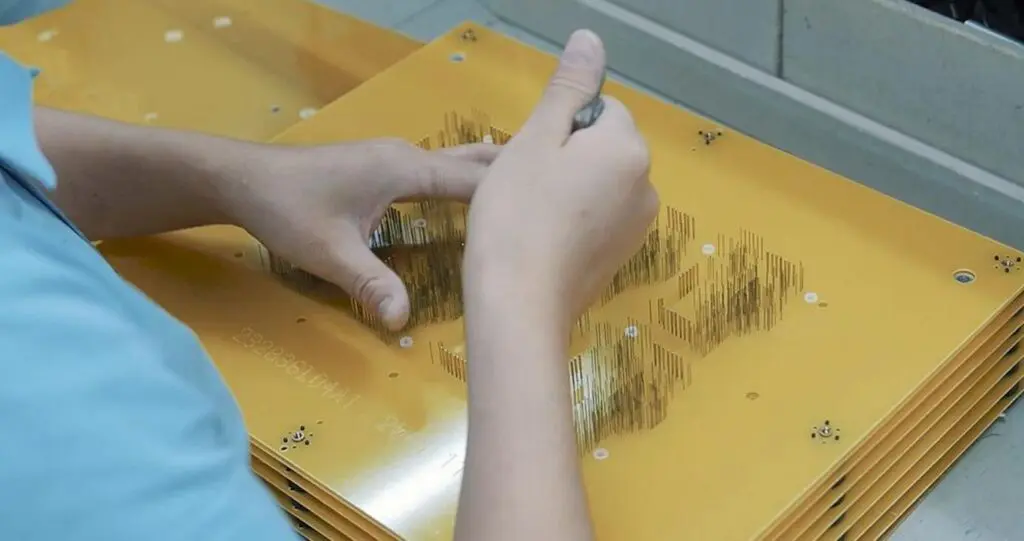
4- VANTAGGI E SVANTAGGI
Come per la sonda mobile, il Bed-Of-Nails ha i suoi vantaggi e svantaggi, questo test elettrico è perfetto per la produzione di massa per la sua velocità di elaborazione tra ogni PCB. Tuttavia, occorre tenere conto dei costosi utensili, della noiosa preparazione e dei limiti di densità.
5 - TEST COMPLETATI
Ora che il test elettrico è stato completato, siamo sicuri che il circuito è corretto. Il prossimo passo sarà l’ispezione finale.
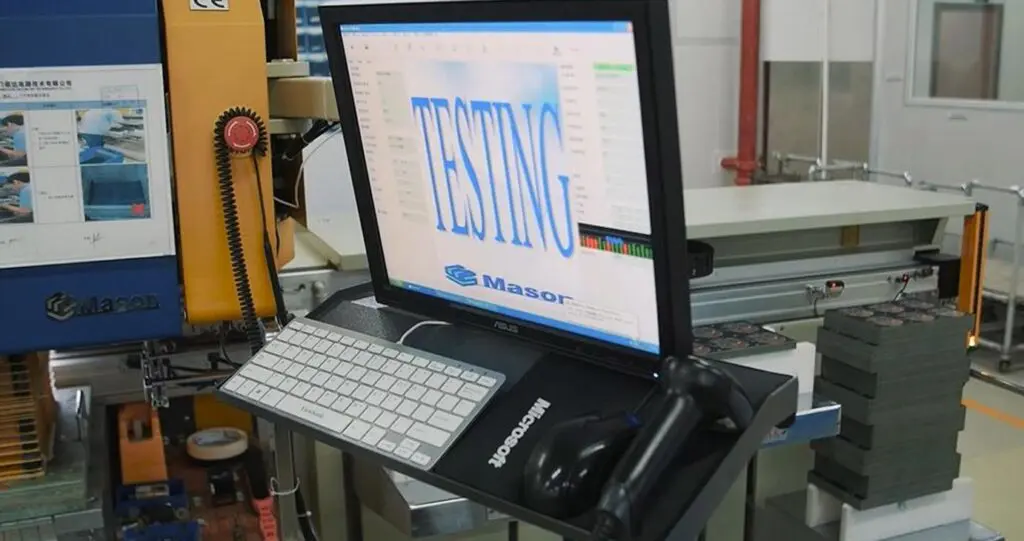
Ispezione finale
Quanto sono importanti le ispezioni finali dei PCB?
Si tratta di una fase cruciale del processo di produzione. Il fornitore controlla l’intera scheda, dall’aspetto funzionale a quello estetico. E controlla tutto rispetto ai requisiti di ICAPE e naturalmente anche agli standard IPC. Inoltre, abbiamo anche un controllore ICAPE in loco che controllerà tutto durante il processo, nonché prima dell’imballaggio e della spedizione.
1 - ISPEZIONE AUTOMATICA
Ogni scheda passa attraverso la macchina per l’ispezione visiva automatica (AVI). Questa macchina controlla il PCB più velocemente degli occhi umani e rileva le incongruenze rispetto al file GERBER. Quindi, la scheda viene posizionata sul verificatore automatico di fori per rilevare se alcuni fori hanno dimensioni irregolari.
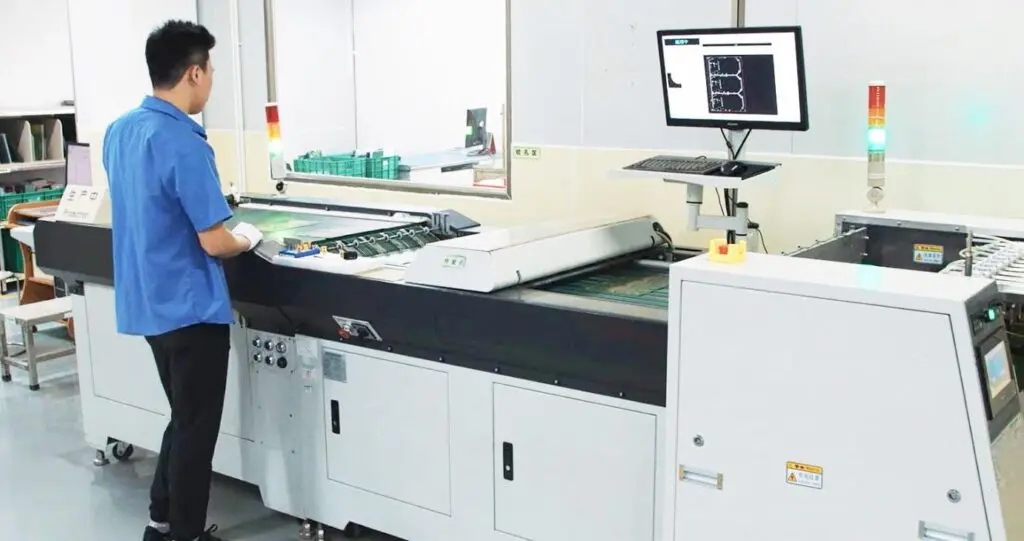
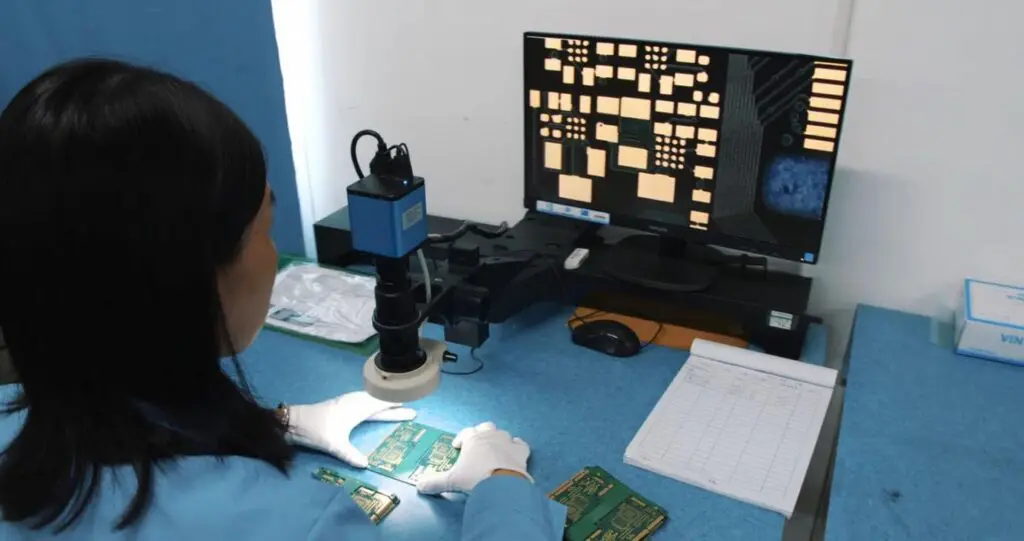
2 - ISPEZIONE DEL FORNITORE
Tutte i PCB sono controllati visivamente da ispettori attenti a controllare ogni specifica. Le valutazioni effettuate dalle nostre fabbriche partner sono monitorate dagli ispettori interni di ICAPE Group, che sono costantemente presenti in queste fabbriche.
3 - TEAM QC E QA
I nostri team di Controllo Qualità (QC) e di Assicurazione Qualità (QA) si recano presso i nostri partner di fabbrica per eseguire personalmente i controlli finali. L’assicurazione della qualità è orientata al processo e previene i difetti proteggendo i processi utilizzati per gestire e creare PCB consegnabili. Il controllo qualità è orientato al prodotto e determina che il risultato finale sia quello atteso.
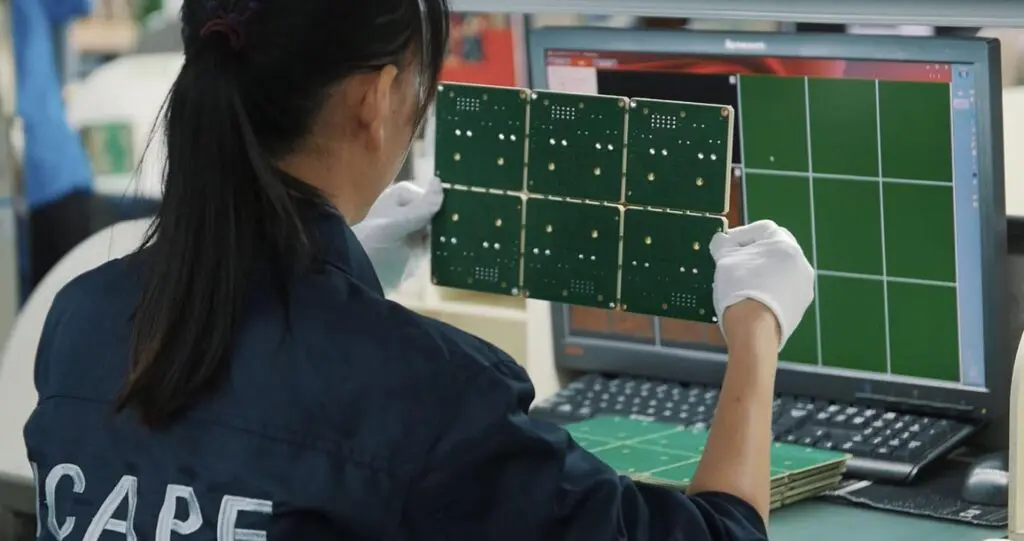
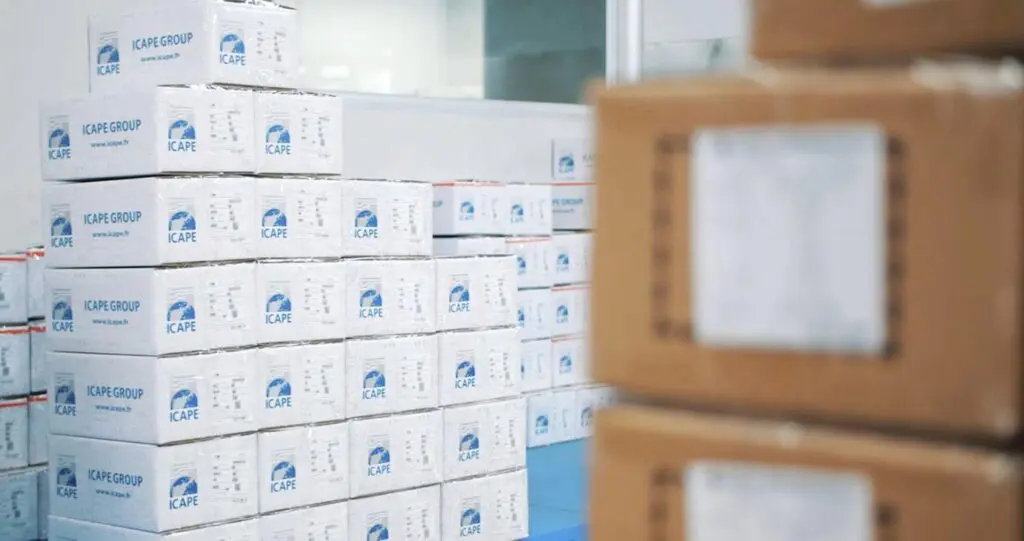
4 - LABORATORIO ICAPE
Il nostro laboratorio è in grado di eseguire numerosi test come l’analisi delle micro sezioni, il controllo del deposito di rame sulla superficie del foro, il controllo dei residui di contaminazione ionica, il controllo della placcatura superficiale, la rugosità, il controllo dell’impedenza del PCB e l’integrità del segnale. È inoltre possibile eseguire test di invecchiamento e shock termico sul PCB per verificarne l’affidabilità in condizioni difficili.
5 - IMBALLAGGIO
Una volta completata l’ispezione, le schede vengono lavate in acqua deionizzata per rimuovere la polvere e i contaminanti che possono essere rimasti sul PCB. Successivamente, le schede vengono accuratamente imballate in confezioni sottovuoto. Viene aggiunta l’etichetta di spedizione e sono pronte per la spedizione. I PCB possono essere spedite in base alla modalità di trasporto richiesta, che può essere DDP, DAP, via aerea, via treno o via nave.
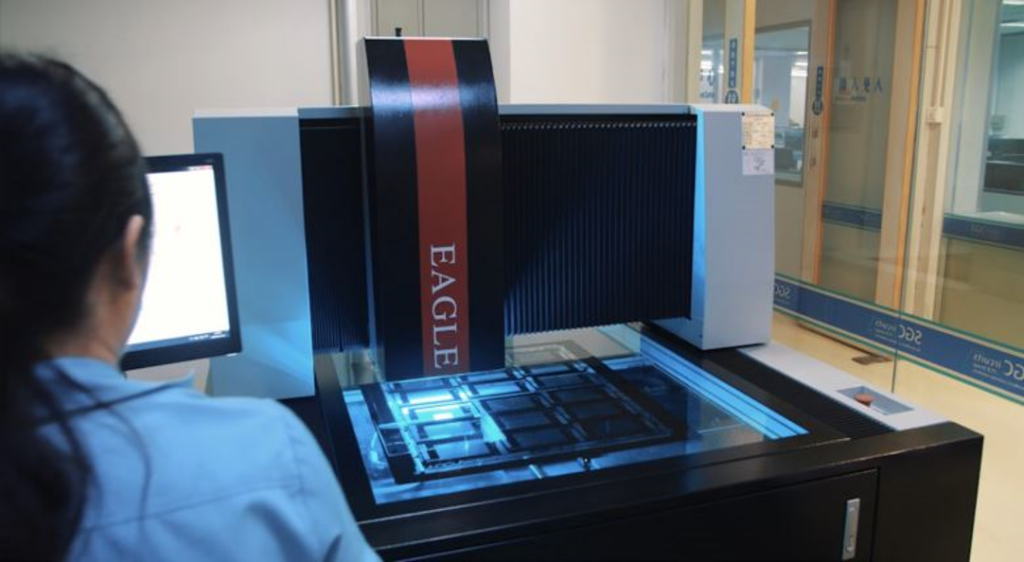