高密度相互接続(HDI)PCBマイクロビアの初歩
微細な世界の驚異
プリント基板(PCB)は、数十年に渡って、現代の電気機器の中枢を成してきました。 テクノロジーが発達するに従い、より小さく、軽く、効率性の高い機器が求められるようになりました。 PCBマイクロビアは、それらの要求に応える、重要な役割を果たします。 この包括的なガイドでは、PCBマイクロビア、各タイプ、製造工程、適用、主な開発のポイントについて、詳しく解説しています。 ベテランのPCB設計者も、テクノロジーに関心がある一般人も、この記事を読むことで、未来の電子製品を稼働させる、微細な世界の驚異を知ることができるでしょう。
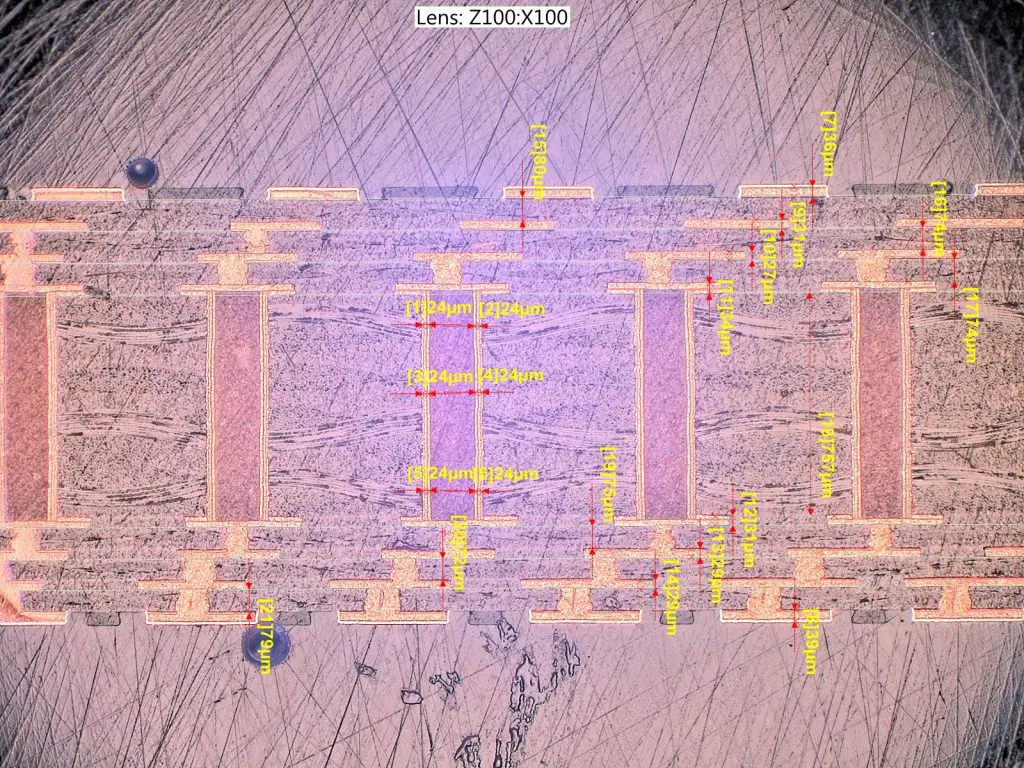
PCBマイクロビアとは何でしょうか。
マイクロビアは、PCBの一層あるいは複数の層を貫通する、主に0.1mmから0.15mmの小さな穴です。 これら極微の精密部が、基板の複層間(レイヤー)での信号と電力接続を担い、高密度の相互接続を可能にします。
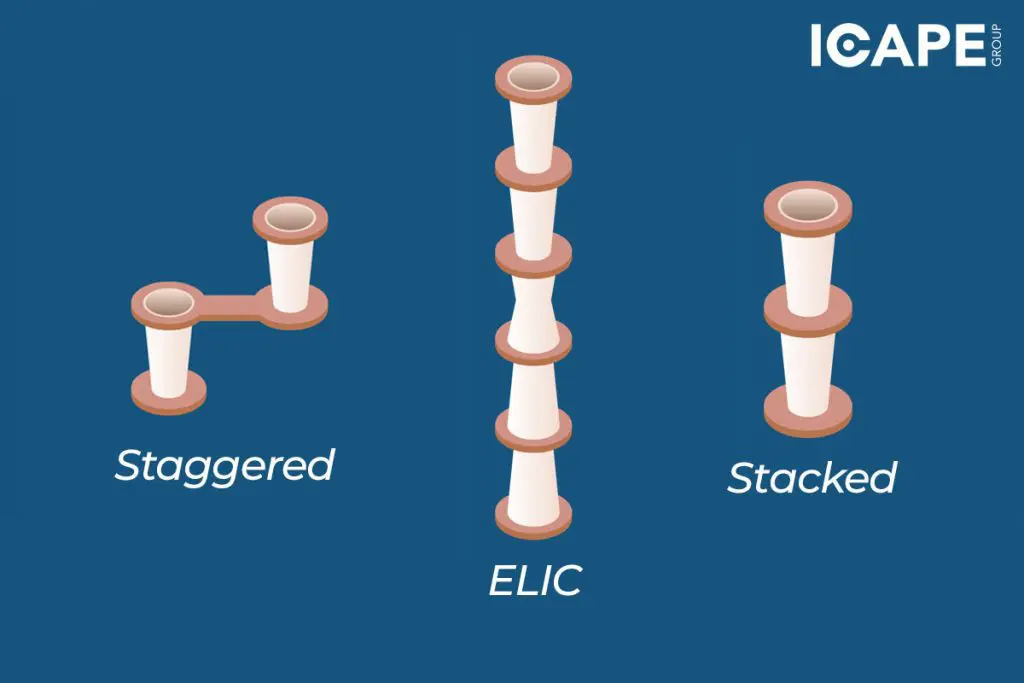
ビアとマイクロビアについて
ビア・ホールは、PCBの各層間に電気あるいはサーマル相互接続をするために使われます。 基本的に、以下の4つのタイプのビア・ホールが存在します。
- スルービア・ホール – 機械的にドリルされ、全ての層を貫通する、ビア・ホ―ル。
- 埋め込みビア・ホール – 機械的にドリルされた穴が、2つあるいはそれ以上の内装基盤を接続します。
- ブラインドビア・ホール – 機械的にドリルされた穴が、外装基盤と1つあるいはそれ以上の内装基盤を接続します。
- マイクロビア – マイクロビアは、基板の1層と重なる層を接続するためにレーザーで開ける穴のことです。 (マイクロビアを機械的にドリルで開けることは可能ですが、レーザーを使用することで技術的に簡素化され、コスト削減にもなります。) 一般的なマイクロビアのサイズは、80-100µm の幅に、60-100µmの深さです。 アスペクト比とは、銅層の誘導体と穴の直径の比率のことです。 殆どのサプライヤーは、0.6: 1 から 1: 1 のアスペクト比を要求し、0.8: 1 の比率が最も適用されます (例えば、誘導体80umにレーザードリル直径0.1mm)。新世代のレーザードリル機は、40-50umものサイズのビアを開けることができ、中には基板の両側から同時に開ける能力を持つものもあります。それにより、薄い誘導体をラミネート前に穴あけできるようになります。 この技術は特に、PCBのような、IC基板の生産に役立ちます。
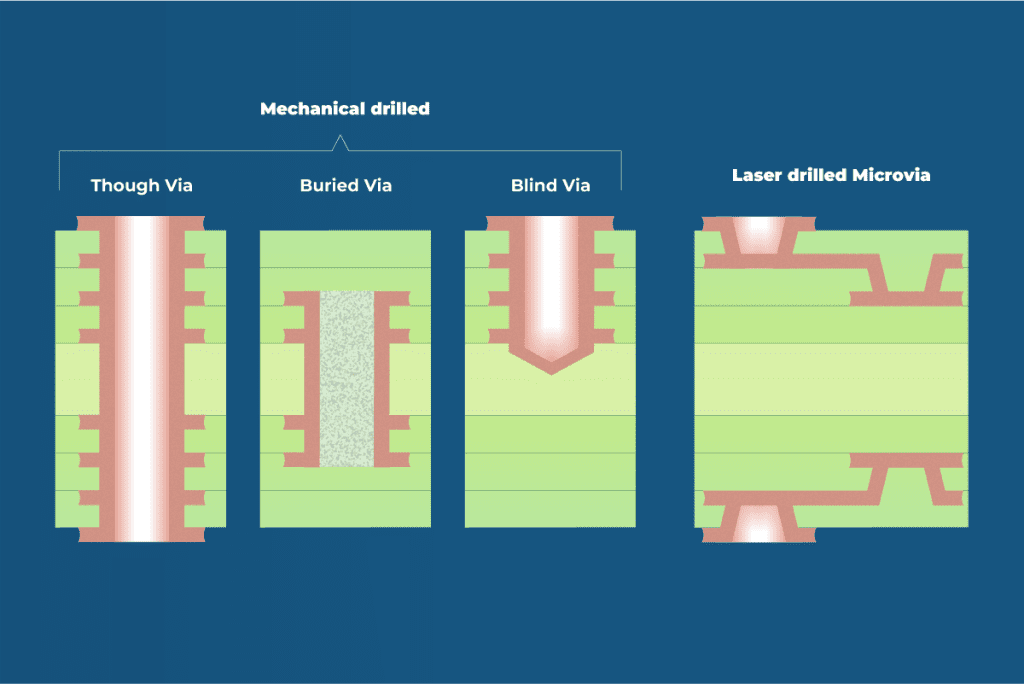
HDI PCBビルドアップとHDI製造工程
メッキスルーホール(PTH)のある機標準的はPCBは、ラミネート1回、機械的ドリル1回、穴洗浄1回、無電解銅メッキ1回、電解銅メッキ1回のみを要します。 HDIの構造は、それらの工程を複数回繰り返して作り上げられます。
全てのHDI PCBは、内装基板構造の構築と、最後の層が構築されるまでラミネート・ドリル・洗浄・めっきの繰り返し工程を経て作られます。 いくつかの例を見ていきましょう。
IPC-2226 タイプ 1 の構築は、ラミネート1回、機械的ドリル1回、片側あるいは両側からのレーザードリル1回、穴洗浄1回、無電解銅メッキ1回、電解銅メッキ1回のみを要します。 これは1ステップHDIとも呼ばれます。
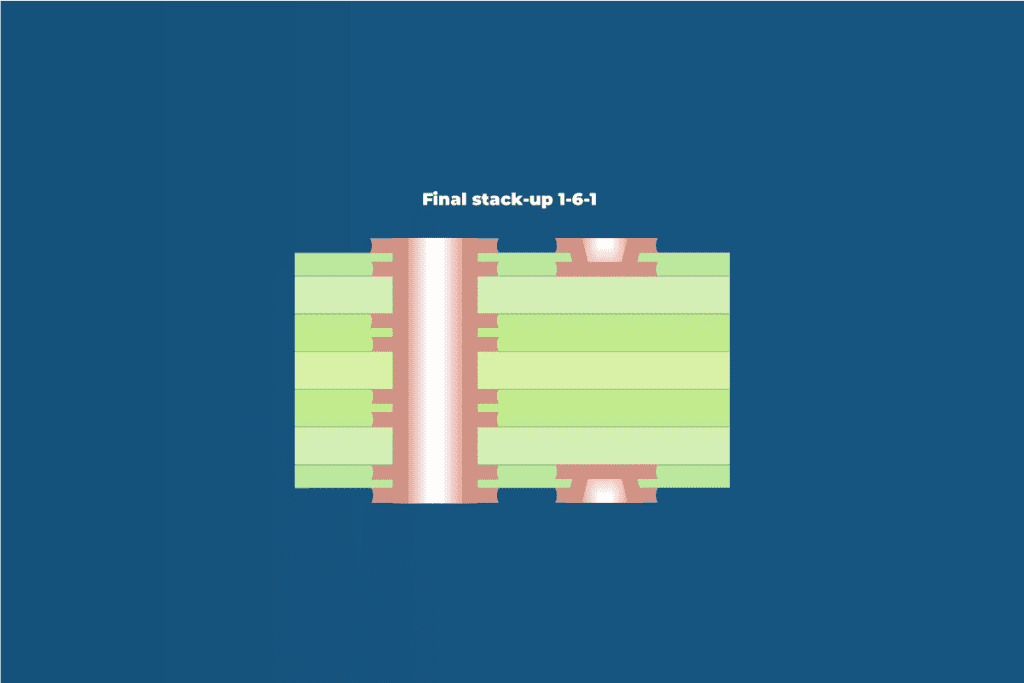
1ステップHDIがコンポーネントピッチあるいはPCB密度全体に対応できない場合は、配線密度を上げるため埋め込みビアを追加することができます。 IPC-2226 タイプ 2 の構築は、ラミネート2回、機械的ドリル2回、片側あるいは両側からのレーザードリル2回、穴洗浄2回、無電解銅メッキ2回、電解銅メッキ2回、レジン充填1回を要します。 これは2ステップHDIとも呼ばれます。
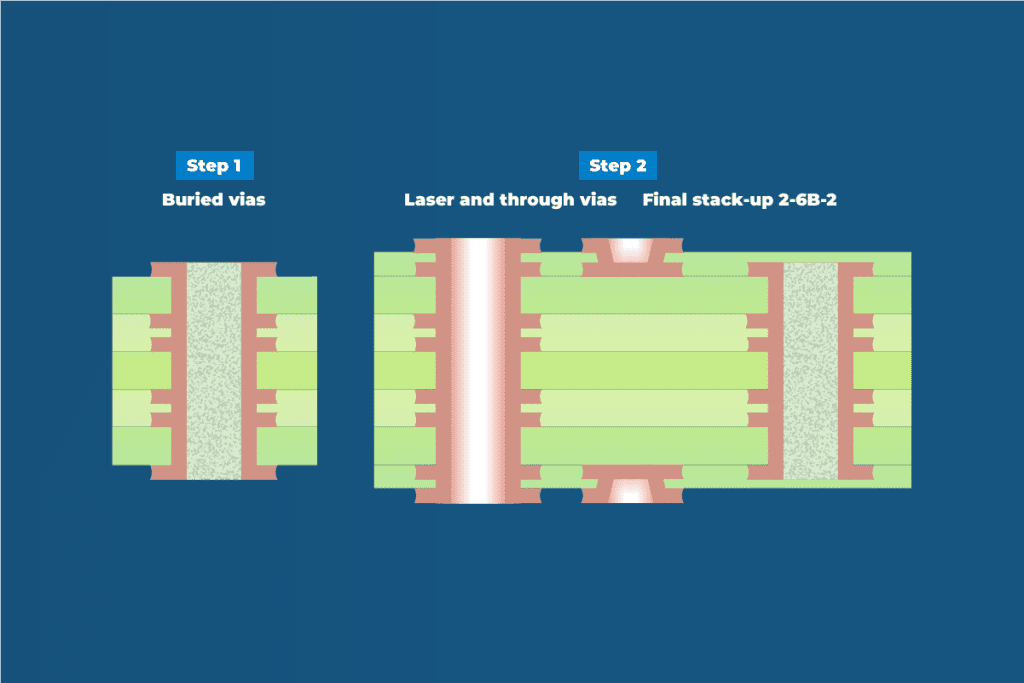
タイプ2の構造がコンポーネントピッチあるいはPCB密度全体に対応できない場合は、レーザービアと埋め込みビアを追加することができます。 タイプ3の構造には、少なくとも2ステップのマイクロビアが含まれます。 IPC-2226 タイプ 3 の構築は、ラミネート3回、機械的ドリル2回、レーザードリル4回、穴洗浄3回、無電解銅メッキ3回、電解銅メッキ3回、レジン充填1回を要します。 これは3ステップHDIとも呼ばれます。
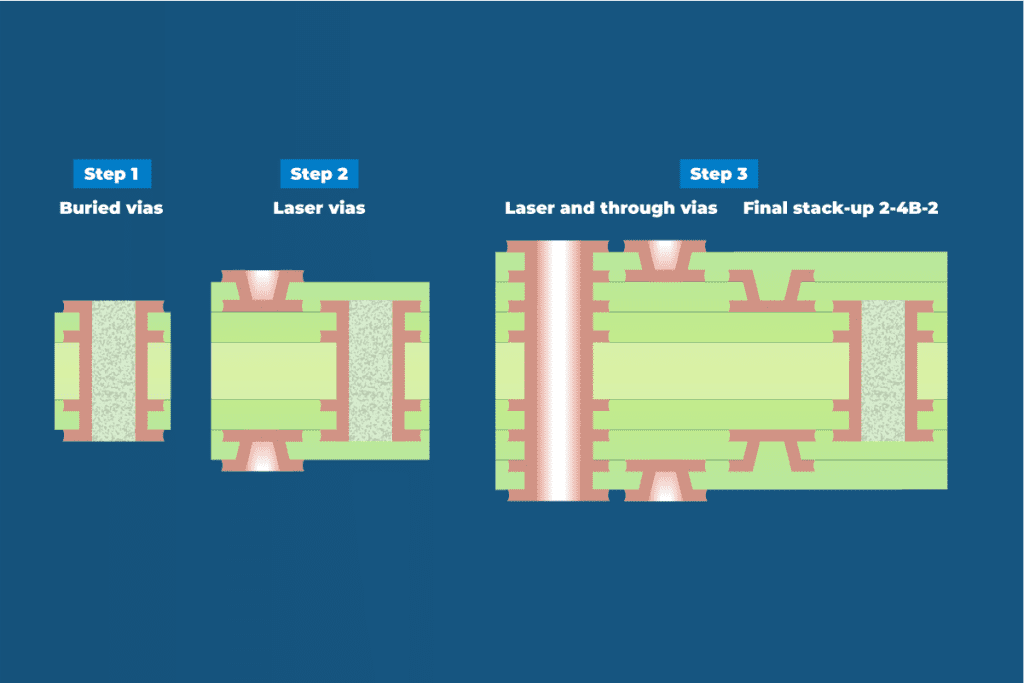
HDIステップ開発
BGAピッチについて、初期のBGA部品は1.2㎜、多層基板でスルーホールビアのみの場合は1.0と0.8㎜でドッグボーンパターンを形成した場合、相互接続とファンアウトの達成に十分でした。 こんにち、BGA部品は0.5 mm以下のピッチでのみ製造されています。この条件でファンアウト実現には、レーザードリルのビアを用いたHDIテクノロジーが不可欠です。 携帯電話の業界では、0.2㎜ピッチのBGA部品を使い始める製造者もいます。
この進歩により、生産能力とHDI PCB製造機器の限界が刷新されてきました。
最も複雑なHDI設計には、0,4-0,5mmピッチのBGA、PCBの両側を加工した2から4のマイクロビアステップが導入されています。しかし、一部の製造業者は、5あるいは6マイクロビアステップと部品の微細化を開発し、更にその限界を追及しています。こうして各層がマイクロビアベースのHDI層である、ELIC(Every Layer Interconnection、HDI任意層プリント回路基板とも呼ばれる)が開発されました。
スタックあるいはスタッガード マイクロビア/埋め込みビア
パッドサイズあるいは設計密度が関連するBGA部品ピッチにより、スタックあるいはスタッガード マイクロビア/埋め込みビア、そしてビアの銅充填をどの工程で使うかが決まってきます。 各工程を追加する毎に、PCBのコストが上がります。 ワイヤー回路を緻密に構築し、適したHDI層とビアの組み合わせを選択することで、コスト削減が可能です。 ICAPEは、その鑑識と実践例により、お客様のテクノロジーをサポートし、アドバイスを提供します。
お客様のPCBコストを最適化するには、適格なビア組み合わせとステップ組み合わせが欠かせません。
以下のように1-6B-1構造のマイクロビアに2-4(6B)-2構造を追加した時のコストは、2-4B-2構造よりもずっとコスト効率が高いのです。 1-6B-1と2-4(6B)-2は両方とも2ステップHDIですが、2-4B-2は3ステップHDIです。
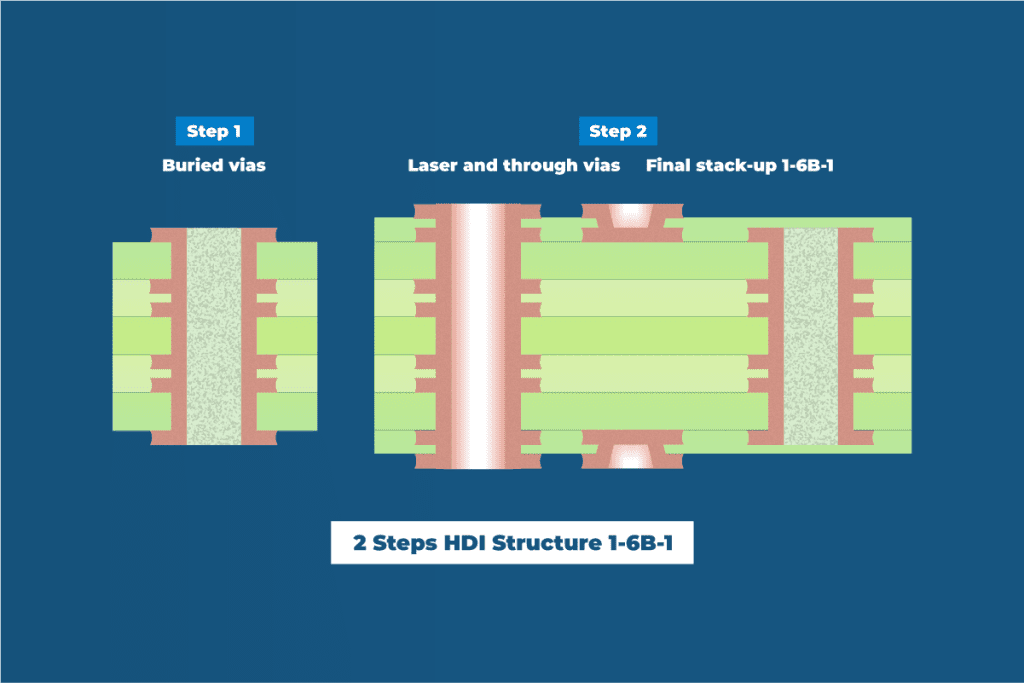
1-6B-1から2-4(6B)-2に以降する場合に加わるのは、2回のレーザードリルのみです。
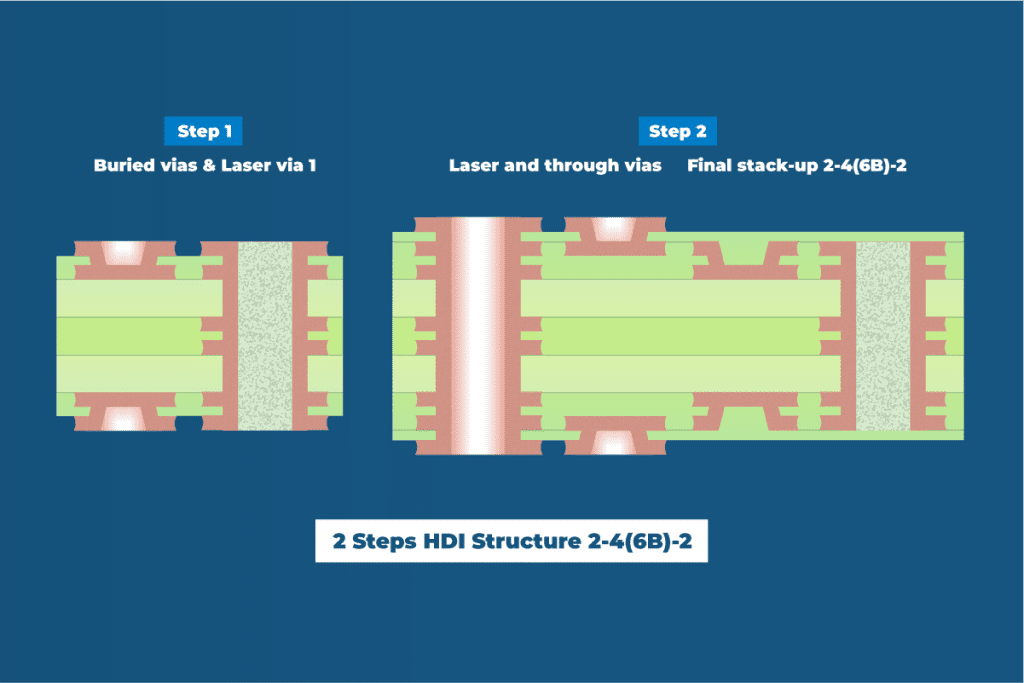
ただし1-6B-1から2-4B-2へは、レーザードリル2回、ラミネート1回、穴洗浄1回、無電解銅メッキ1回、電解銅メッキ1回の工程が加わります。
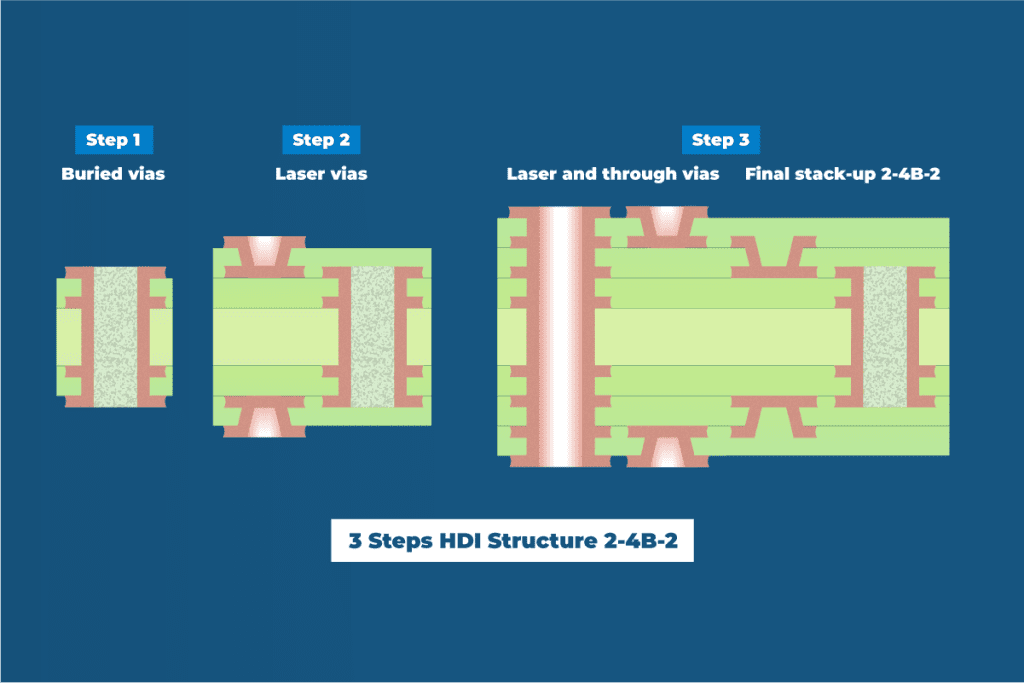
スタックとスタッガード ビアの選択
スタックマイクロビアにより、ローピッチBGAで高密度回路とファンアウトの場所が確保できますが、PCBコストは上がります。 スタックマイクロビアは、設計上の理由でスタッガードビアに充分なスペースが確保できない場合にのみ、採用されます。 埋め込みビアに重ねられたスタックマイクロビアは、銅線上に無電解めっき膜を追加する必要があり、マイクロビアに重ねられた場合は、内側基盤のマイクロビアに銅めっきによって充填する必要があります。
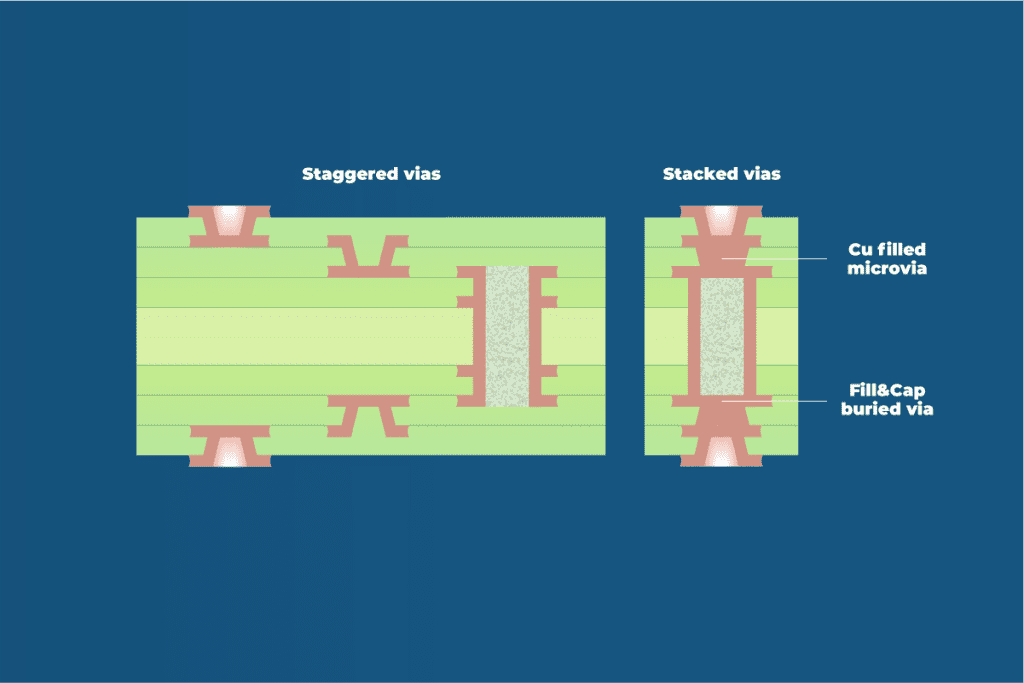
銅の電気めっきによる充填について
BGAパッドあるいはそれに相当する小さなはんだ付けパッドは、銅の電気めっきによる充填ではんだ付けの端の隙間を防ぐのに有用ですが、銅の電気めっきはPCBコストを上げます。 パッド付きマイクロビアを設計すれば、銅の電気めっき充填は必要でなくなります。
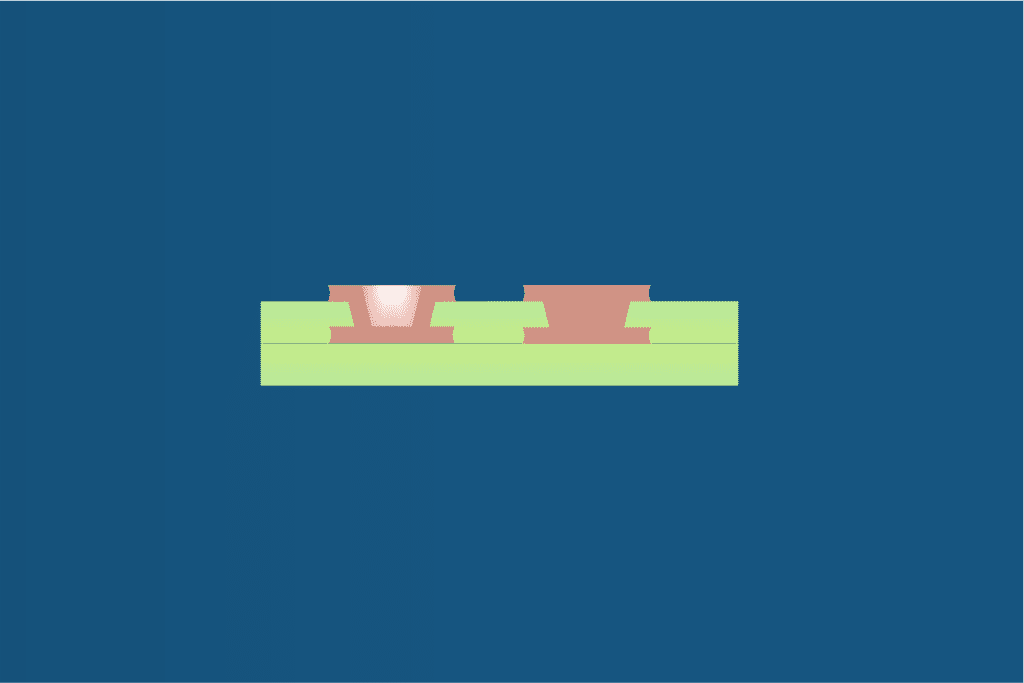
全体設計にマイクロビアを導入
もし、ワイヤー回路密度あるいは部品ファンアウト上の理由から、レーザードリルマイクロビアと埋め込みビアが必要である場合、機械的にドリルされたスルービア全てをレーザードリルのマイクロビアに替えることで、製造コストと時間を節約することができます。
レーザードリル工程の方が、機械的にドリスする工程よりも、穴単位のコストがより低く、素早くできます。 各HDIステップに工程が追加されるため、基本的な多層構造よりもHDI PCBの方が価格は高くなります。 HDIのステップ工程にかかるコストは、BGA回路をファンアウトするいくつかのマイクロビア採用と変わらず、全スルーホールビアをマイクロビアと埋め込みビアで替える場合も同様です。 この例では、スルーホールビアを全てやめることで、機械的ドリルの工程時間とコストが削減できます。
PCB全体でスルーホールビアを他に切り替えると、以下の複数の利点があります。
– スペースが確保できるため、ワイヤー回路がより効率よく設計でき、各部の密度が上がって全体的に部品が小さく、軽くなります。
– 穴を開ける部分が減るため、信号経路が短くなり、伝達ラインが減り、シグナル・インテグリティを向上させ、インピーダンスが制御でき、GNDとVCC基準面の機能性を改善します。
– スタブによる信号反射を避ける目的の、スルーホールのバックドリリングが要りません。
– スルーホールビアのないHDI PCBは、はんだ付けによる高温ストレスに対し、より高い耐久性を示します。
機械的ドリルビアとレーザードリルビアはどのように製造されているのでしょうか。
それには、ICAPE PCB Manufacturing Journey(PCB製造工程)の、ドリルリングを扱っている第五エピソードをご覧ください。
より小さく、軽い部品に多くの機能性を組み込める、HDIレーザーマイクロビアは、電子産業に革命を引き起こしました。 テクノロジーは進化し続けるため、高密度相互接続と高度なアプリケーションに新しい可能性を生み出す、PCB設計の革新にあたり、将来もマイクロビアはその最先端を占めることでしょう。 マイクロビアのタイプ、製造工程、設計の留意点を理解することで、PCB設計者はその利点を、未来に向けた斬新な電子機器開発に活かすことができます。
登録して、次回のHDIテクノロジーをテーマにしたICAPEウェビナーに参加し、あなたの設計と構造を最適化する、多くの知識とヒントを共有しあいましょう。