CAF: Zrozumienie znaczenia przewodzącego włókna anodowego (CAF) dla płytek PCB
Przyjrzyjmy się jednemu z fascynujących, ale niepożądanych aspektów płytek PCB, zwanemu przewodzącym włóknem anodowym (CAF). Przewodzące włókno anodowe (CAF) powoduje wzrost ilości miedzi elektromigracyjnej pomiędzy dwoma przewodnikami. W tym artykule opiszemy, jak powstają płytki PCB i co powoduje CAF, w szczególności w przypadku płytek wielowarstwowych o zwiększonej gęstości, a także, jakie są dostępne środki zapobiegające lub ograniczające ryzyko CAF.
Zrozumienie procesu produkcji płytek PCB
Zanim omówimy zjawisko CAF, musimy zrozumieć, jak powstają płytki PCB. W konstrukcjach wielowarstwowych otwory platerowane tworzą połączenia pomiędzy poszczególnymi warstwami w stosie. Po wywierceniu i oczyszczeniu otworów na powierzchnię płytki drukowanej i otwory nakładana jest cienka warstwa chemicznej miedzi lub podobnego materiału przewodzącego przed ostatecznym pokryciem miedzią galwaniczną.
Co to jest CAF?
Wada w postaci przewodzącego włókna anodowego to wzrost ilości miedzi elektromigracyjnej między dwoma punktami na płytce drukowanej. Wada CAF zmniejsza rezystancję i ostatecznie tworzy zwarcie między dwoma przewodnikami miedzianymi o przeciwnej biegunowości.
Wada CAF może wystąpić między przewodami w następujących postaciach: styk otworu platerowanego z innym otworem platerowanym, otworu platerowanego ze ścieżką lub ścieżki ze ścieżką. Najczęstsze rodzaje uszkodzeń występują między platerowanymi otworami oraz między otworami a ścieżkami.
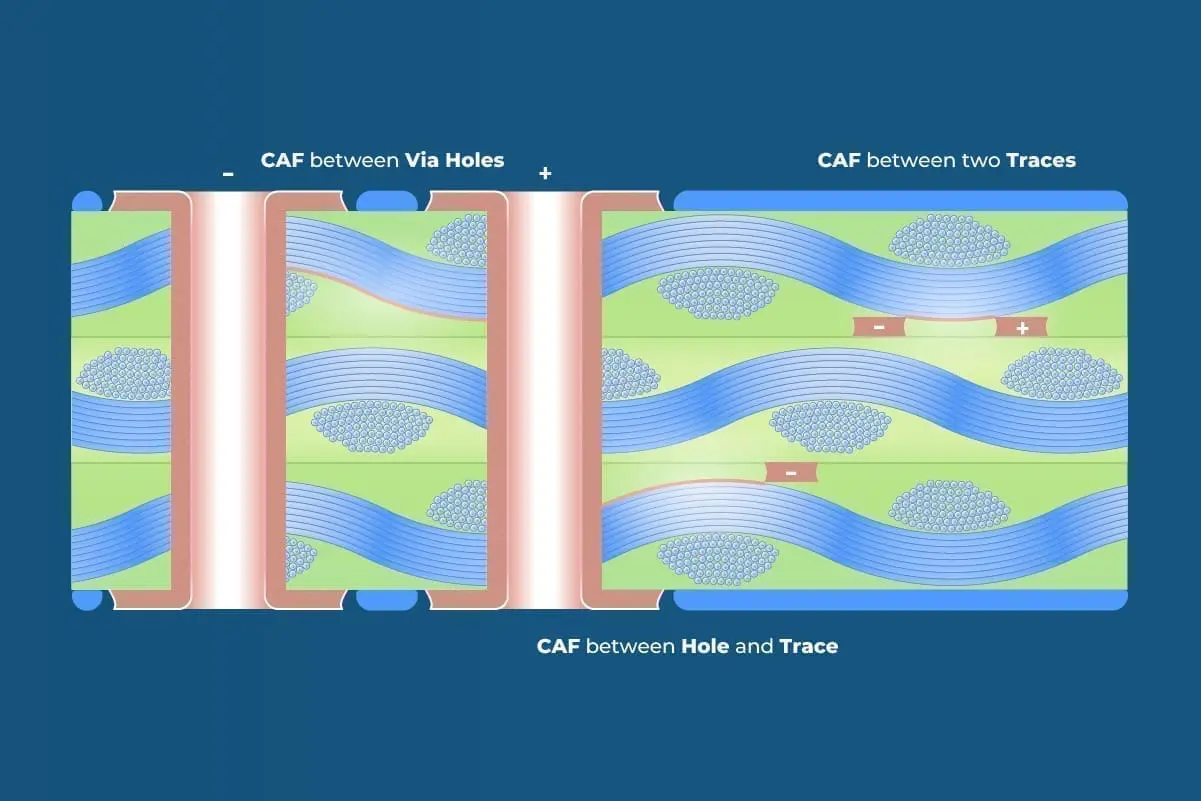
Wada CAF powstaje w dwóch etapach:
Pierwszym etapem jest degradacja powierzchni styku żywicy z tkaniną szklaną. Główne znane czynniki mające wpływ na ten pierwszy etap to wilgotność i temperatura na płytce PCB. Wypiekanie/suszenie płytki PCB wydaje się mieć odwracalny wpływ na ten pierwszy etap. Zwiększa to znaczenie utrzymywania płytek PCB w suchych warunkach podczas procesu montażu płytek, a także w całym okresie użytkowania.
Drugim etapem jest wzrost elektromigracji miedzi między przewodnikami, który może rozpocząć się po degradacji granicy faz żywica/szkło. Znane główne czynniki wpływające na ten drugi etap to odległość między dwoma przeciwnie spolaryzowanymi przewodnikami miedzianymi, rozmieszczenie/kąt między otworami w zależności od kierunku włókna szklanego, polaryzacja napięcia, wilgotność, temperatura i stężenie pH. Warunki migracji jonów Cu z przewodnika naładowanego + do przewodnika naładowanego – naładowany przewodnik wzdłuż granicy między żywicą a włóknami szklanymi można porównać do warunków procesu galwanicznego powlekania Cu. Tworzenie się migracji miedzi jest nieodwracalne i nie ma na nie wpływu wypiekanie/suszenie po wystąpieniu zjawiska CAF.
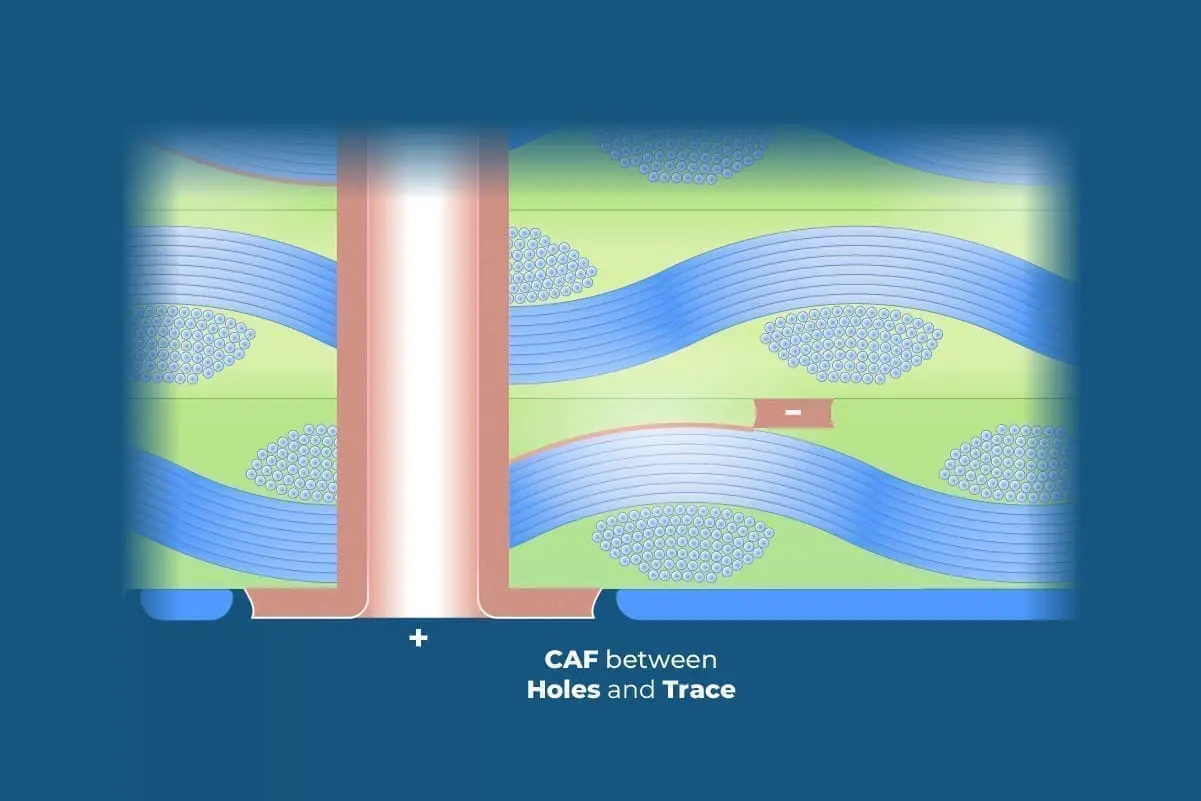
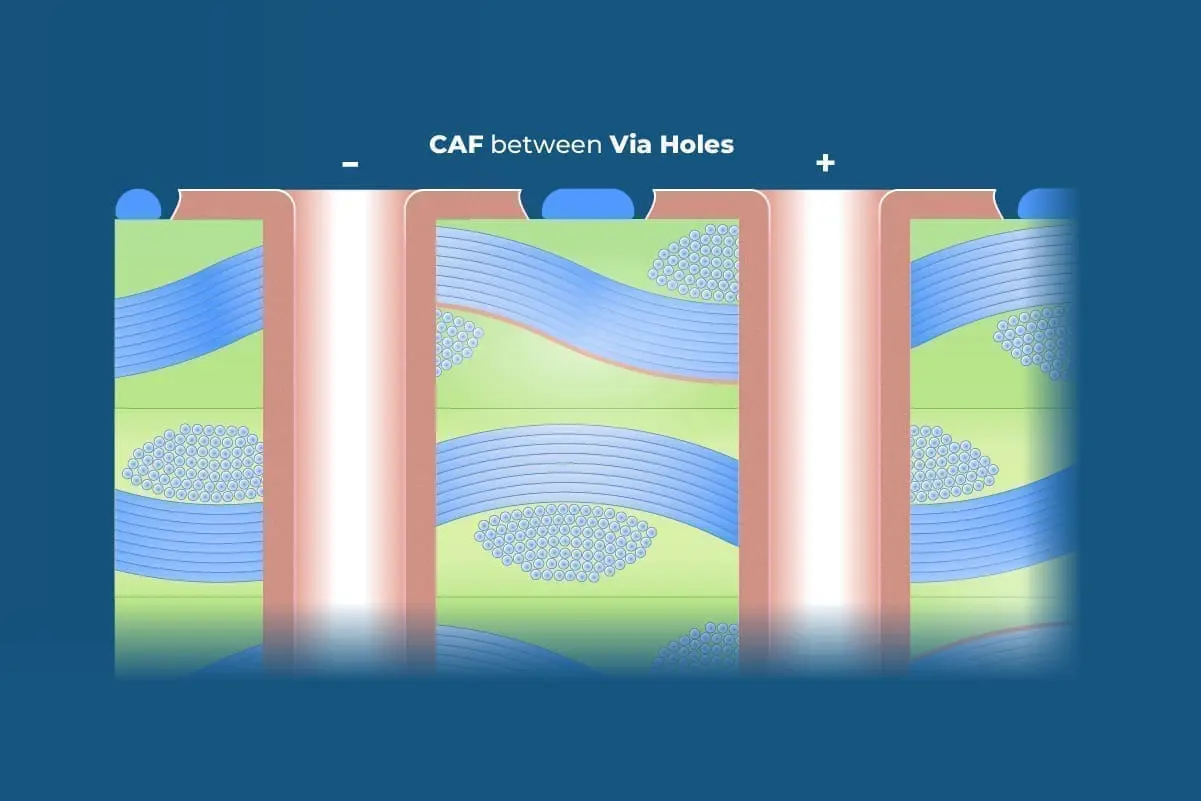
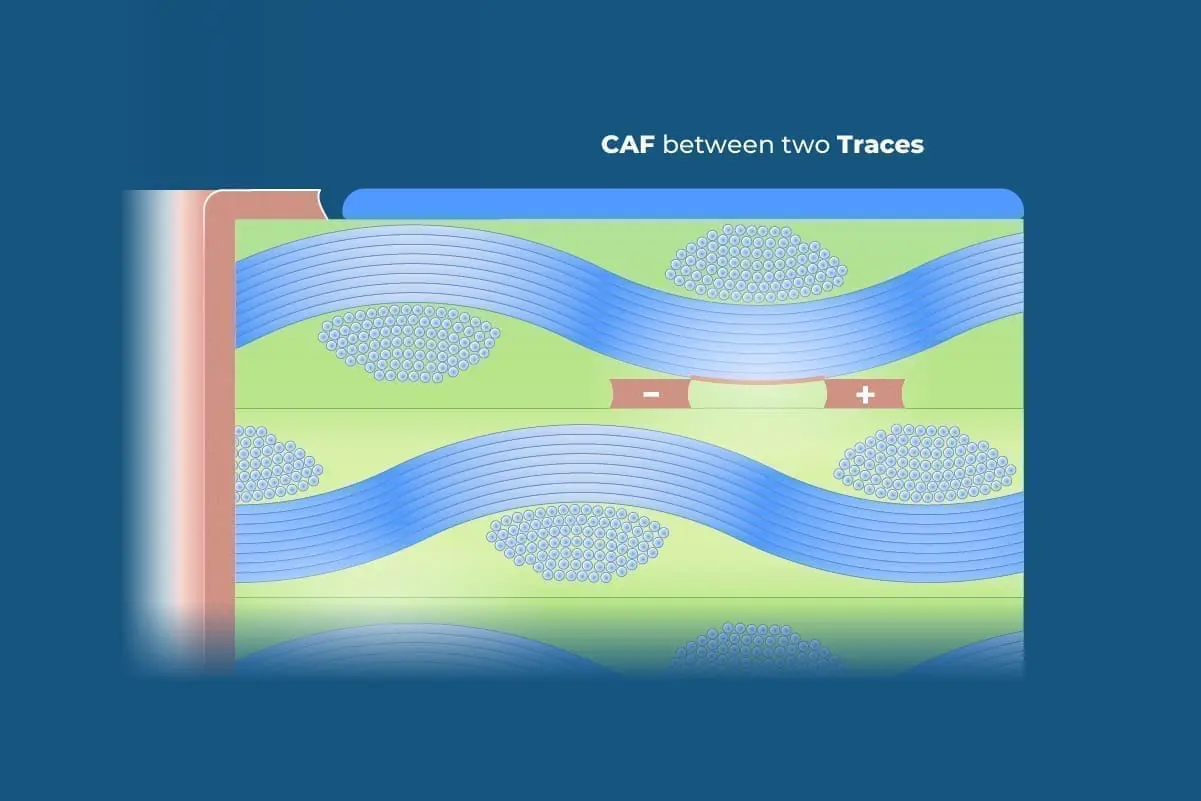
Zapobieganie wystąpieniu wady CAF
Wybór materiałów: Zmniejszenie ryzyka wystąpienia CAF poprzez wybór wysokiego wskaźnika Tg i materiał odporny na CAF.
Projektowanie: należy usunąć niepołączone pady z warstw wewnętrznych, ale zachować odległość izolacyjną tak jakby na warstwie wewnętrznej znajdowały się pady. Zmniejszy to ryzyko wystąpienia wady CAF poprzez zwiększenie odległości Cu-Cu. O ile to możliwe należy unikać przelotek napięciowych obok przelotek uziemiających. Jeśli jest to jednak nieuniknione, nie należy umieszczać przelotek w jednej linii z tkaniną szklaną. Powinny one zostać umieszczone pod kątem 45°, aby zapobiec tworzeniu się CAF wzdłuż włókien szklanych. Ponadto zaleca się zwiększenie odstępów między takimi przelotkami.
Produkcja płytek drukowanych: Producent powinien skupić się na ograniczeniu/uniknięciu pustych przestrzeni podczas procesu laminowania. Parametry posuwu/prędkości wiertła muszą być zrównoważone, aby zapobiec degradacji styku żywica/szkło na wczesnych etapach. Przed powlekaniem Cu należy dokładnie usunąć pozostałości po odmazywaniu, aby zapobiec przedostawaniu się kwasu do obszarów między FR4 a ścianą otworu pokrytą Cu.
Montaż płytek drukowanych: Przed rozpoczęciem procesu lutowania należy upewnić się, że płytki PCB są suche. Wilgoć znajdująca się wewnątrz płytki PCB może podczas lutowania zamienić się w parę i spowodować mikroskopijne rozwarstwienie, które z czasem może prowadzić do wady CAF.
Czyszczenie po montażu: Po montażu należy dokładnie wyczyścić płytkę PCB, aby usunąć wszelkie zanieczyszczenia, które mogą spowodować CAF.
Powłoka ochronna płytki drukowanej: Należy nałożyć powłokę ochronną na płytkę, aby chronić ją przed wilgocią, solą i innymi szkodliwymi substancjami przez cały okres użytkowania.
Podsumowanie
Wada CAF może wystąpić w przypadku wszystkich typów płytek PCB z technologią FR4, ale jak wspomniano powyżej, istnieją pewne warunki, które przyspieszają to zjawisko, przez co niektóre zastosowania są bardziej podatne na CAF niż inne. Wydaje się, że największe zagrożenie występuje w przypadku płytek drukowanych wysokoprądowych i o dużej gęstości okablowania, szczególnie jeśli są one narażone na działanie wysokiej temperatury i wilgotności roboczej.
Jednak znajomość warunków jest pierwszym krokiem do zapobiegania CAF:
- użycie materiału odpornego na CAF
- zaprojektowanie ze szczególnym uwzględnieniem odstępów i rozmieszczenia przelotek GND i VCC
- wybór dostawcy z dobrą kontrolą procesu
- zapewnienie suchych warunków przed lutowaniem
- wyczyszczenie płytek drukowanych po montażu
- zastosowanie powłoki ochronnej do ochrony układów płytek drukowanych wykorzystywanych w trudnych warunkach środowiskowych
Aby uzyskać więcej informacji, zapraszamy do kontaktu z ICAPE Group.
Autor: Erik Pedersen/Jordan Labbe