Płytki drukowane MANUFACTURING
Proces
Wszystkie procesy produkcyjne zostały przedstawione krok po kroku. Podążaj za zespołami ICAPE Group w naszych fabrykach płytek drukowanych, aby odkryć sekrety produkcji płytek.
Jak powstają płytki drukowane krok po kroku?
W skomplikowanym świecie elektroniki sercem innowacji jest płytka drukowana (PCB). Te niewielkie, ale jak ważne komponenty służą jako szkielet urządzeń elektronicznych, umożliwiając sprawny przepływ sygnałów elektrycznych. Czy zastanawialiście się kiedyś nad fascynującą podróżą, jaką odbywa płytka PCB od momentu powstania do integracji? Nasz artykuł, który niebawem się ukaże, zagłębia się w kompleksowy proces produkcji płytek drukowanych, przedstawiając każdy krok z precyzją i przejrzystością. Od początkowej fazy projektowania po skomplikowane procesy wytrawiania i montażu… przeprowadzimy Cię przez skomplikowaną sieć technik i technologii, które przekształcają surowce w gotowe płytki drukowane. Niezależnie od tego, czy jesteś doświadczonym inżynierem, ciekawym świata entuzjastą, czy kimś po prostu osobą zafascynowaną magią kryjącą się za elektronicznymi gadżetami, dołącz do nas w tej wycieczce przez fascynujący świat produkcji płytek drukowanych. Przygotuj się, by doświadczyć alchemii, która zamienia miedź, włókno szklane i lut w wyrafinowane obwody zasilające urządzenia, z których codziennie korzystamy.
Inżynieria przedprodukcyjna
Jak zaprojektować płytkę drukowaną?
Wszystko zaczyna się od działu inżynieryjnego. Otrzymują plik GERBER, sprawdzają go i porównują z zamówieniem, standardami IPC i możliwościami dostawcy.
1 – Sprawdzanie plików GERBER
Inżynierowie ICAPE Group przeprowadzają przegląd Design For Manufacturability (DFM), sprawdzają dane, warstwy miedzi, rysunki mechaniczne, specyfikacje oraz linię i przestrzenie między ścieżkami. Po zakończeniu tworzymy plik o nazwie „Kwestie techniczne”, jeśli to konieczne.
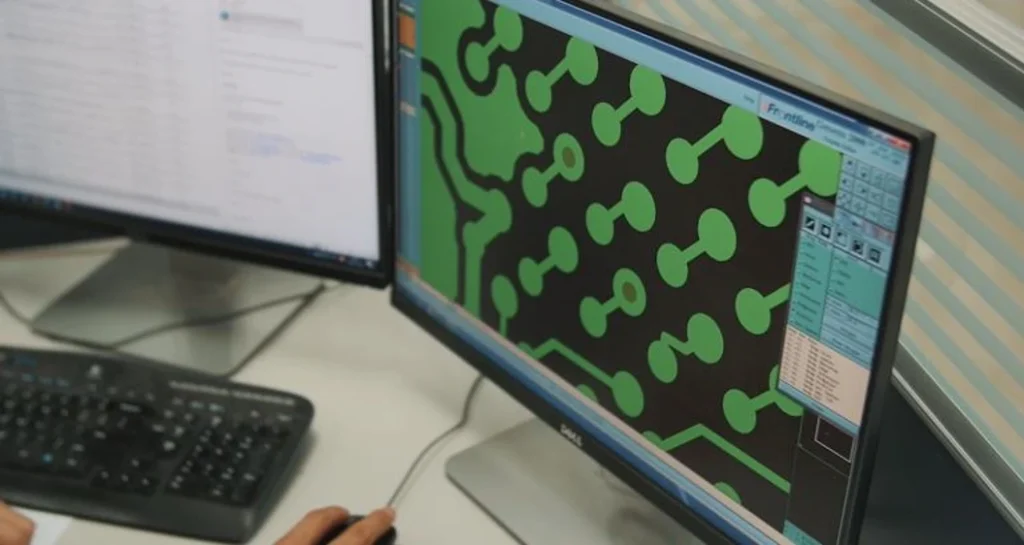
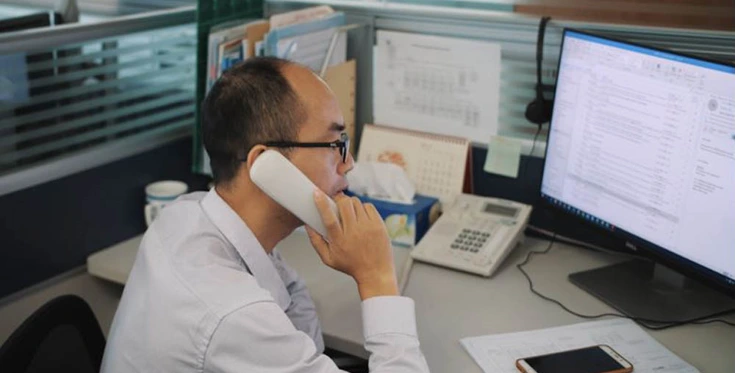
2 – Przegląd DFM
Plik ten jest przesyłany do klienta w celu zaproponowania potencjalnych rozwiązań lub ulepszeń. Mogą to być różne metody panelizacji, typy mask lutowniczych, designu, materiału bazowego, marki lub specyfikacji. Może to również obejmować różne technologie, które są wykonalne i opłacalne w wybranych fabrykach partnerskich zgodnie ze standardami IPC.
3 – Ocena fabryki partnerskiej DFM
Następnie do akcji wkracza nasza fabryka partnerska. Odbiera dane i przystępuje do drugiego przeglądu DFM, łącząc projekty obwodów na panelu produkcyjnym.
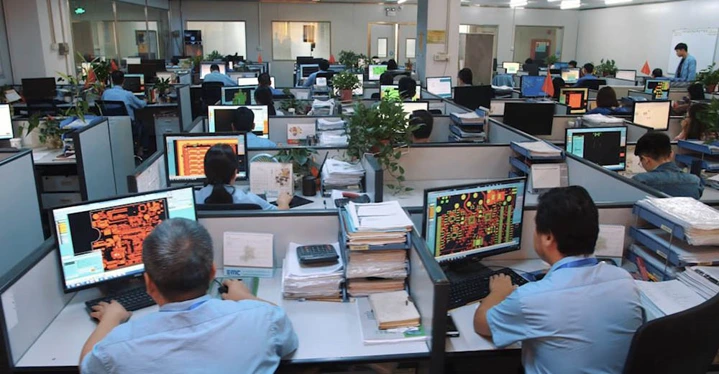
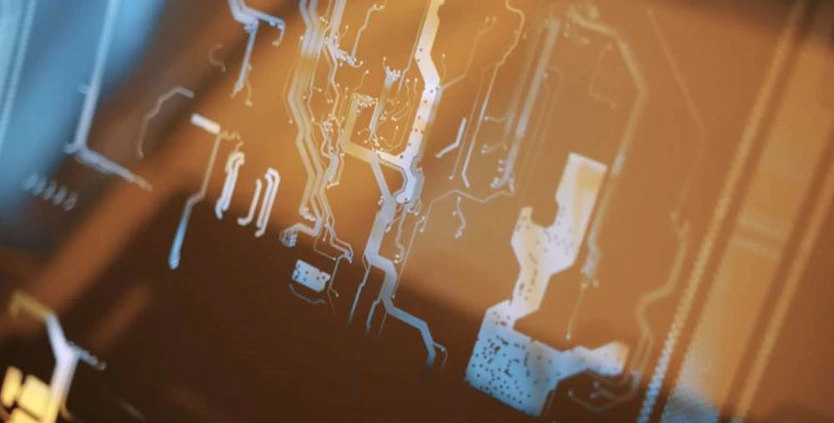
4 – Drukowanie grafiki
Proces druku projektu polega na weryfikacji i przeniesieniu każdej warstwy płytki drukowanej do maszyny drukującej. Dla każdej warstwy płytki drukowanej, takiej jak warstwy wewnętrzne, zewnętrzne, maska lutownicza, druk oznaczeń oraz specjalne warstwy, takie jak przelotki, maska zrywalna, warstwa węglowa itp., tworzony jest osobny projekt. Ten sam projekt może być używany dla tysięcy paneli.
Materiały podstawowe
Jak wybrać i przygotować materiały bazowe?
Dowiedz się, jak przechowywane i przygotowywane są panele przed przejściem przez kolejne etapy procesu produkcyjnego!
1 – PRZECHOWYWANIE
Wszyscy producenci płyt PCB korzystają z dostarczanych surowców, takich jak prepregi i folie miedziane, które są dostarczane przez ICAPE Group zgodnie z naszymi wymaganiami technicznymi. Wszystkie te surowce są starannie przechowywane zgodnie z ich rodzajem, całkowitą grubością, grubością miedzi oraz marką.
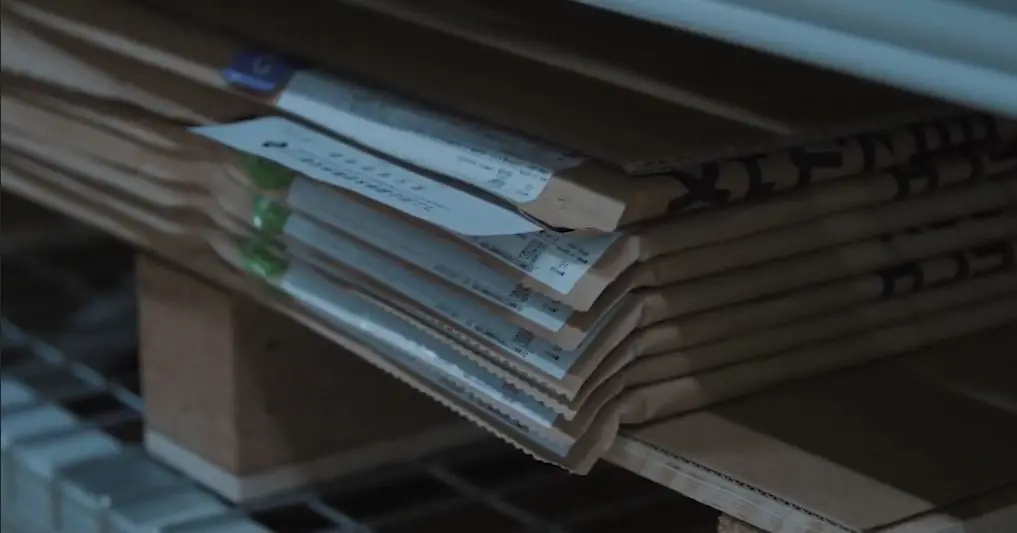
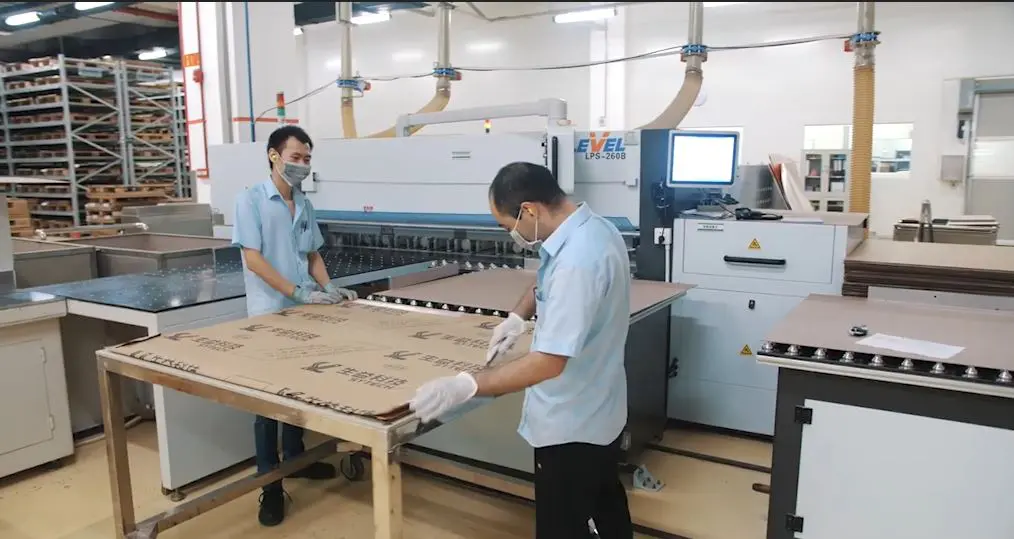
2 – PRZYGOTOWANIE ZAMÓWIENIA
Po wybraniu odpowiednich materiałów z magazynu zgodnie z zamówieniem fabryka przystępuje do rozpakowania paneli i przygotowania ich do przejścia przez proces produkcji.
3 – KONTROLE
Kontrola każdej partii jest kluczowym punktem. Miedź i całkowita grubość są dokładnie sprawdzane za pomocą precyzyjnych narzędzi, aby upewnić się, że spełniają potrzeby klientów stosownie do tworzonej technologii.
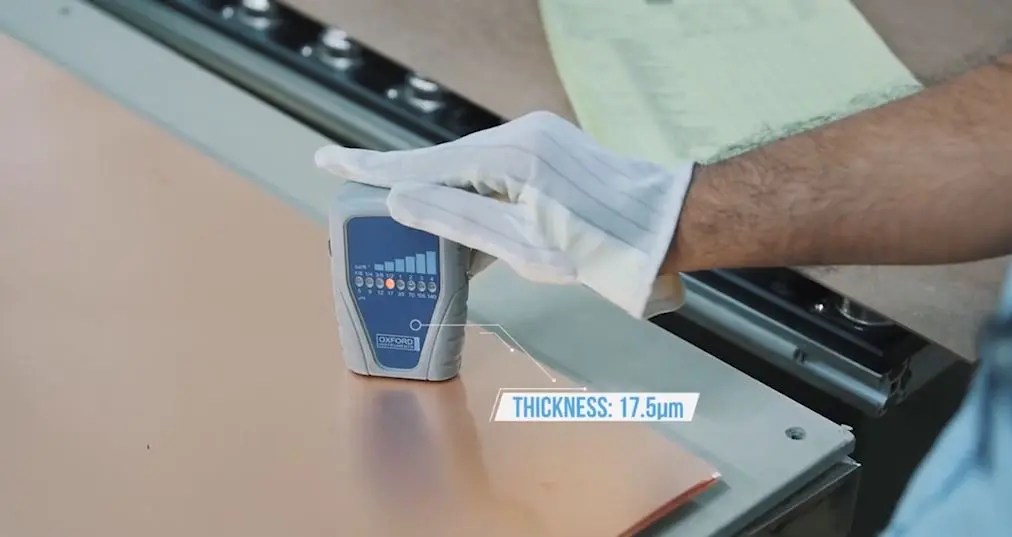
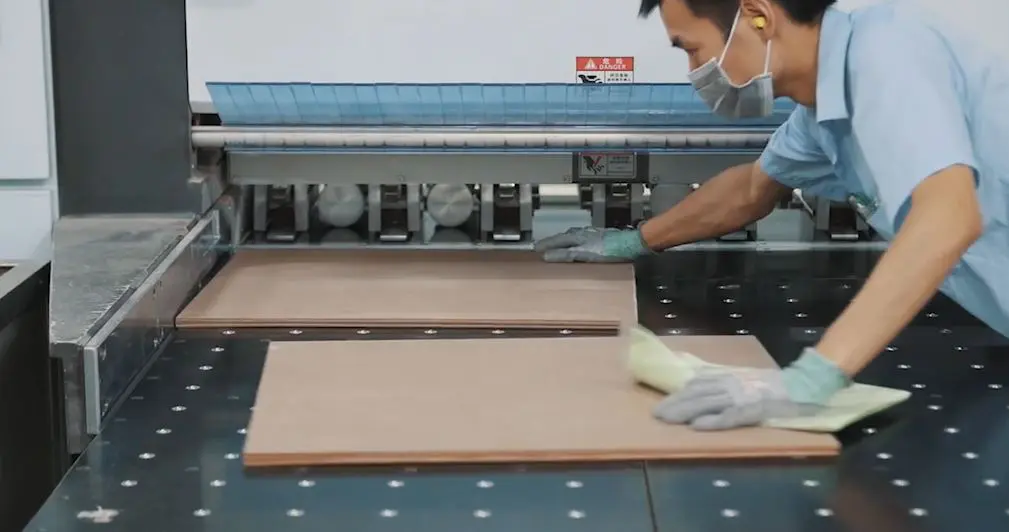
4 – CIĘCIE
Panel musi zostać przycięty do rozmiaru produkcyjnego. Obecnie wykończenie krawędzi panelu i jego geometria są bardzo ważne dla rejestracji CCD oraz z punktu widzenia sprzętu do obsługi.
5 – WYKOŃCZENIE ROGÓW
Większość firm zaokrągliła rogi paneli, aby zmniejszyć ryzyko zarysowań i zabezpieczyć obsługę na kolejnych etapach procesu produkcyjnego.
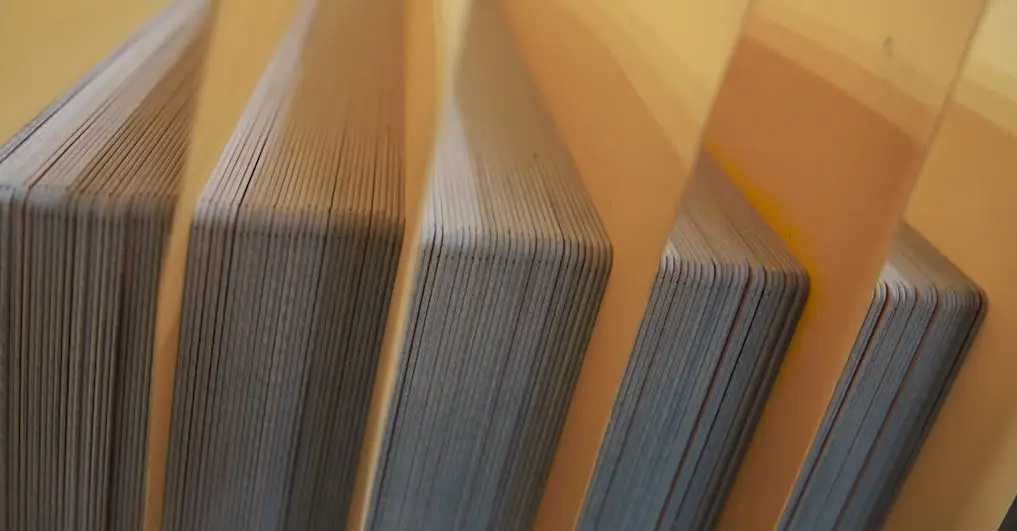
Inner Layer
The inner layer
The inner layer imaging is a very technical step of the process which happens in a clean and yellow room. Why ? Because the dry film is UV sensitive and to avoid any shorts and opens on the inner layer, a level between 3000 and 4000 dust particles per cubic meters must be reached.
1 - CLEANING
The cleanroom uses overpressure to protect and remove any dust coming from outside of the cleanroom. Before entering the cleanroom, the panels are cleaned. Depending on the thickness of the inner layers, the processes are different. For layers thinner than 500 micrometers, the chemical process is used. For thicker layers, the mechanical process is preferred.
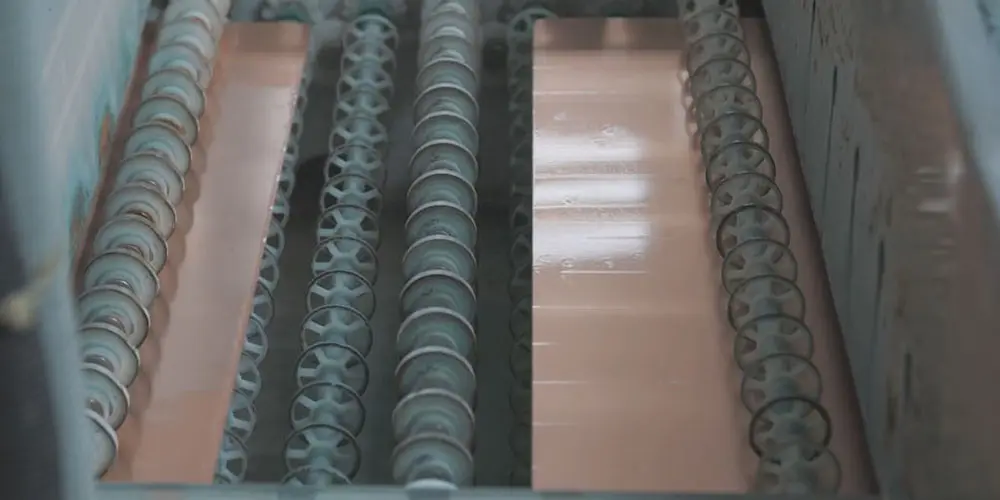
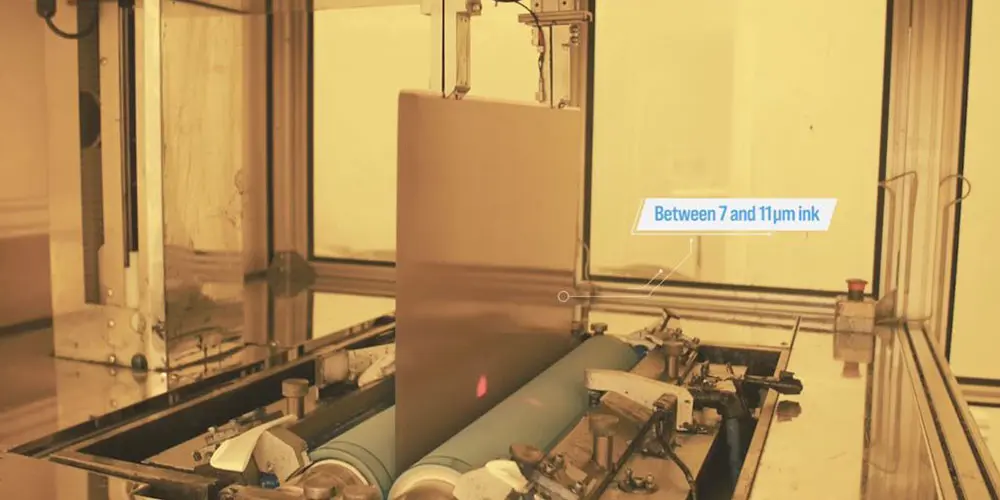
2 - ENDUCTION
When panels arrive in the cleanroom, they are heated, then the photoresist film or the ink ( beteween 7 and 11 µm) is automatically applied onto the panel.
3 - REGISTRATION AND INSOLATION
The boards are registered at +/- 15 to 30 micrometers with 2 or 4 CCD Cameras. A vacuum is created, then a blast of UV light is applied with an average of 1 to 20 seconds depending on the process: this is the insolation. The boards are polymerized and ready to be developed.
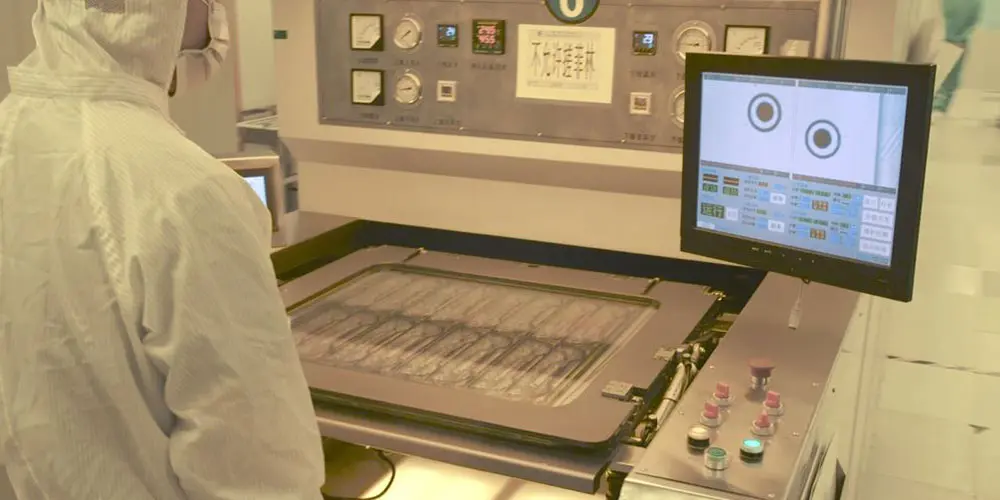
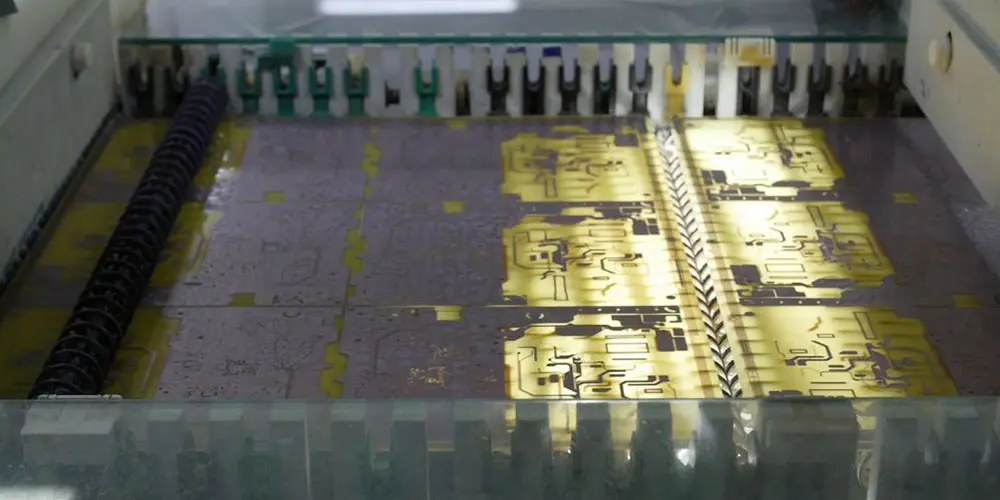
4 - DEVELOPING AND ETCHING
For the development phase, the board is washed with an alkaline solution which removes the photoresist left unhardened. From there, we can see the inner layer image for the first time. Etching is the critical step in layer imaging. The unprotected copper is removed and defines the pattern. After stripping the ink, the photoresist film is now completely removed.
5 - AUTOMATIC OPTICAL INSPECTION (AOI)
After the Multilayer lamination, it is impossible to correct errors occurring on the inner layers. The Automatic Optical Inspection will confirm a total absence of defects. The original design from the GERBER file serves as a model. If the machine detects any inconsistencies, a technician will assess the problem.
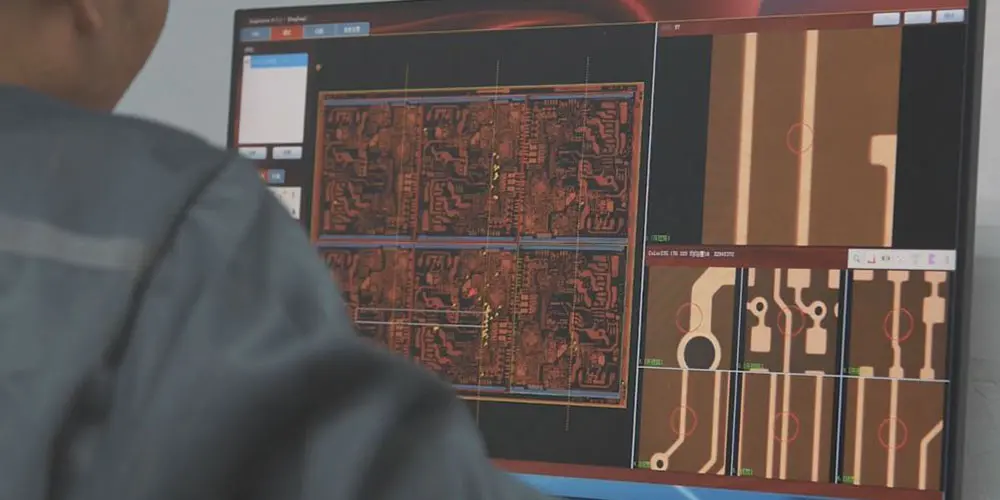
Laminowanie
Co to jest laminowanie płytek drukowanych?
Dołącz do nas i poznaj etap laminowania w procesie produkcji obwodów drukowanych! Po etapie obrazowania warstwy wewnętrznej, płytki przechodzą proces rejestracji i laminowania. Dołącz do naszej wycieczki po fabryce HDI w Chinach!
1 – PRZYGOTOWANIE
Panele są one dokładnie czyszczone w celu usunięcia skorodowanej powierzchni miedzianej, potencjalnych odcisków palców oraz pozostałości suchej powłoki, węglanu i pozostałości środków przeciwpieniących po usunięciu suchej powłoki.
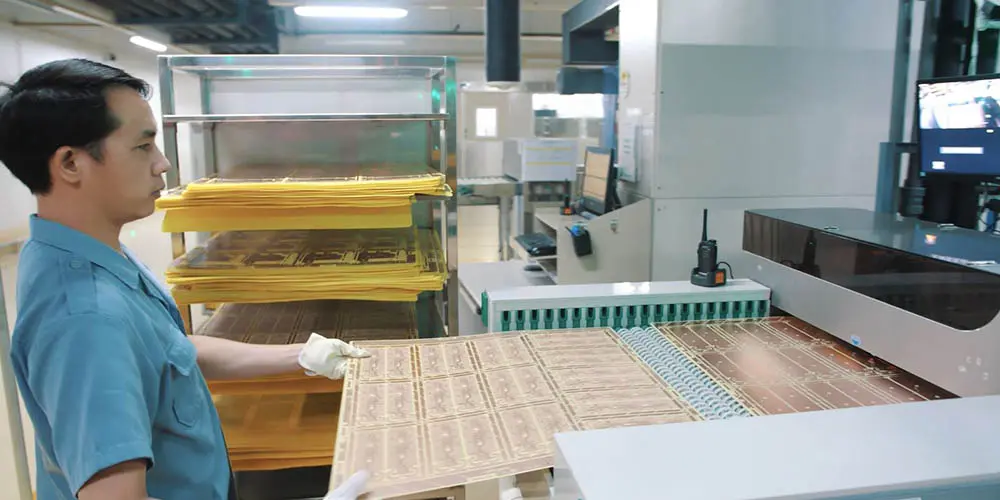
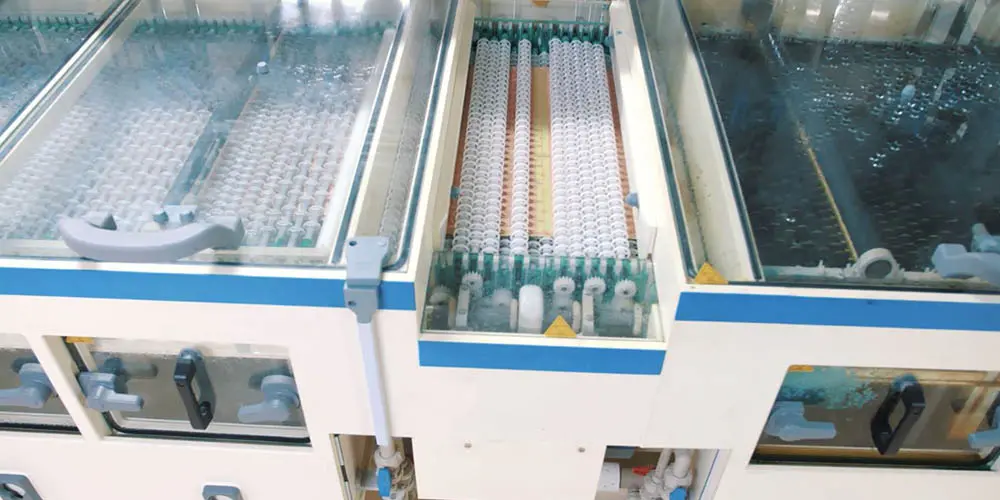
2 – MIKROWYTRAWIANIE
Mikrowytrawianie jest kluczowym procesem, który umożliwia uzyskanie równomiernej i odpowiedniej warstwy tlenku brązu lub czerni na powierzchni płytki. Poprzez ten proces, grubość warstwy miedzi zostaje zmniejszona do zakresu od 0,2 do 1 mikrometra.
3 – CZARNY TLENEK
Obróbka za pomocą brązowego lub czarnego tlenku ma na celu zapewnienie lepszej przyczepności żywicy epoksydowej oraz zapobieżenie problemom, takim jak rozwarstwienie.
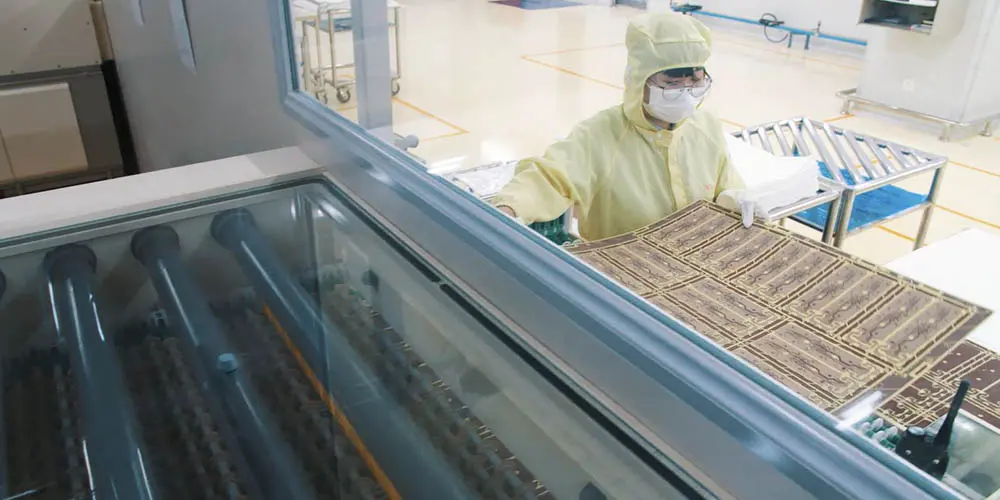
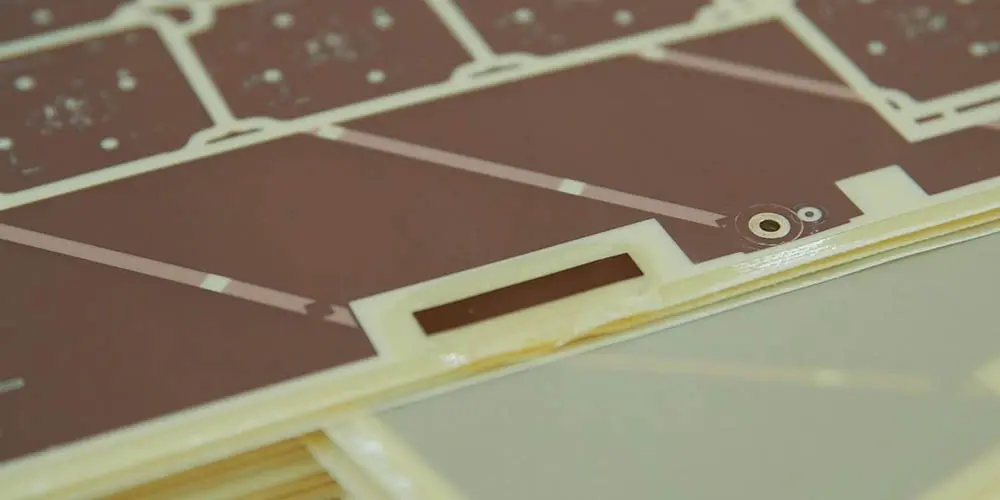
4 – UMIESZCZENIE WARSTWY WEWNĘTRZNEJ
Operator umieszcza warstwę wewnętrzną i prepreg na maszynie klejącej, co pozwala na połączenie ich w stos. Po sklejeniu przechodzimy do użycia nitów. Proces nitowania ma na celu zakończenie rejestracji i połączenie warstwy wewnętrznej z prepregiem. Dzięki temu stos nie będzie się przesuwał podczas procesu laminowania.
5 – UKŁADANIE W STOS
Folia miedziana jest umieszczona pomiędzy łatą ze stali nierdzewnej a prepregiem. Stal nierdzewna tworzy twardą i płaską powierzchnię, a folia miedziana uzupełnia całość. W rezultacie panel składa się z górnej i dolnej części z folii miedzianej oraz prepregu, które otaczają warstwę wewnętrzną.
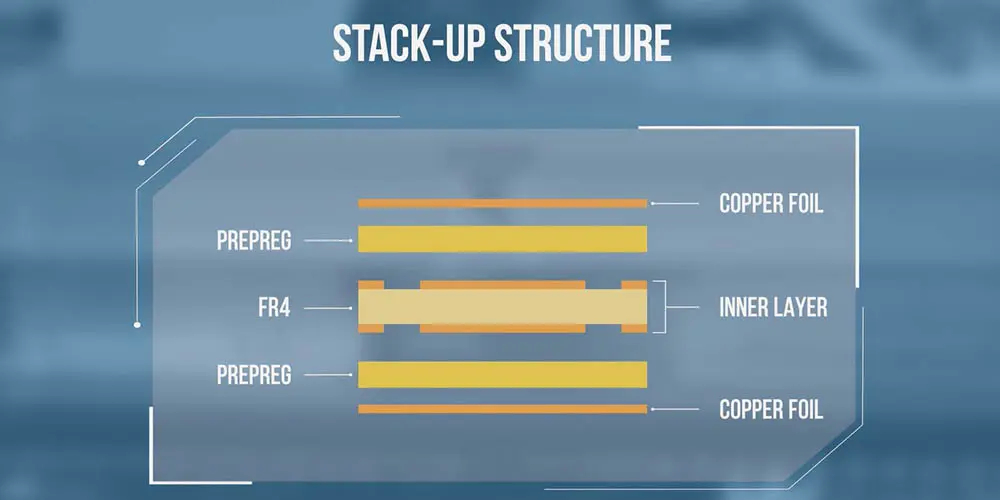
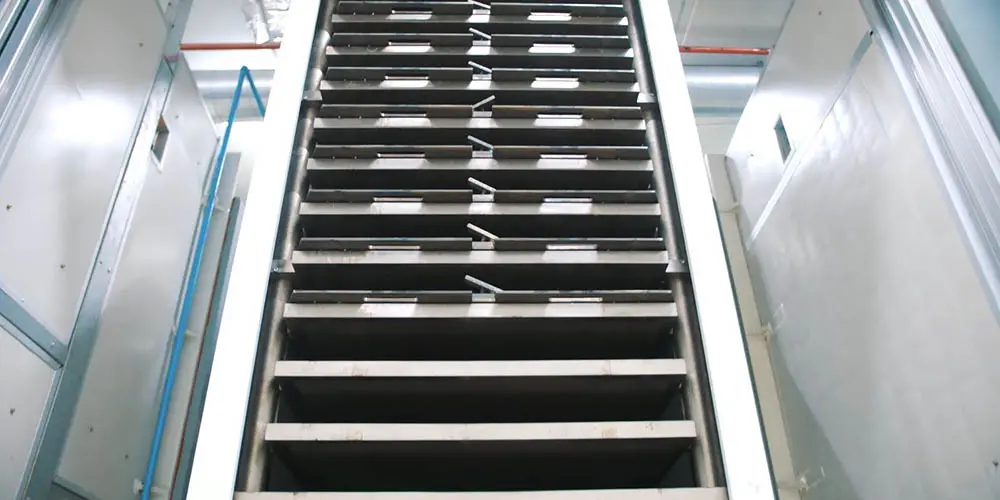
6 – LAMINOWANIE
Układ jest poddawany ekstremalnym temperaturom w zależności od arkuszy danych materiałów. Wewnątrz maszyny do laminowania panuje ciśnienie wynoszące 180 ton na metr kwadratowy, a proces trwa do 2 godzin. Po poddaniu wysokiemu ciśnieniu i temperaturze warstwy łączą się, tworząc jedną płytę, która jest następnie przenoszona do prasy chłodzącej. Po tym procesie panele są wyjmowane z formy.
7 – WYKONANIE OTWORÓW
Nowe płytki zostaną opatrzone otworami przy użyciu urządzenia rentgenowskiego. Następnie otwory te zostaną oczyszczone z zadziorów, sfazowane i zaokrąglone na rogach.
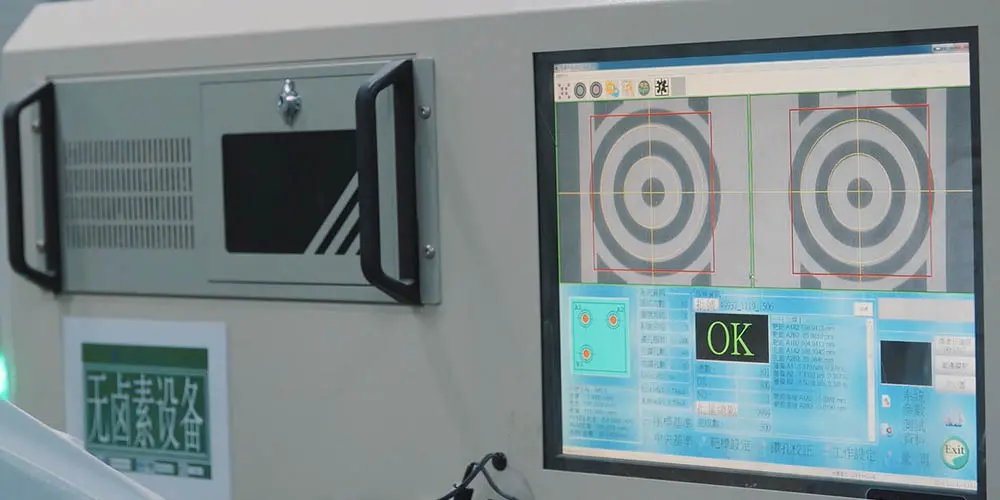
Wiercenie
Jak wymagający jest proces wiercenia?
Piąty odcinek naszej serii podróży z płytką PCB skupia się na jednym z najbardziej spektakularnych procesów: wierceniu! Ten etap nie tylko robi wrażenie swoją spektakularnością, ale jest również nieodwracalny! Musi być bardzo starannie wykonany, ponieważ nawet niewielki błąd może prowadzić do dużych strat. Odkryj różne etapy tego procesu (wiercenie mechaniczne lub laserowe, minimalna średnica, a nawet kontrola), podążając za naszymi dwoma ekspertami ICAPE Group w jednej z naszych fabryk partnerskich w Chinach.
1 – PRZYGOTOWANIE
W celu zapewnienia lepszej dokładności i kontroli termicznej stosuje się specjalne materiały, takie jak aluminium, drewno lub melamina na szczycie i na dole stosu.
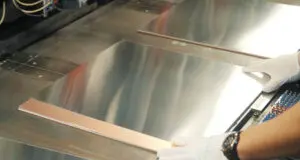
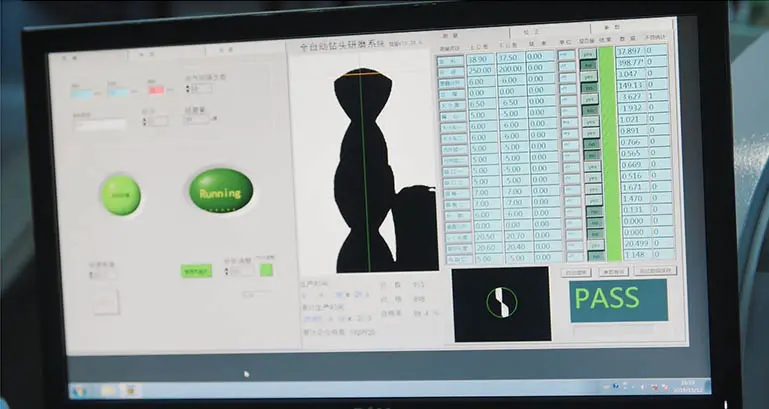
2 – KONTROLA NARZĘDZI
W przypadku procesu wiercenia płytek PCB istotne jest, aby narzędzia wiertarskie były idealnie wyprofilowane i spełniały odpowiednie wymagania dotyczące liczby otworów, które można nimi wykonać. W przypadku zaawansowanych technologicznie płytek PCB używane są tylko nowe wiertła. Natomiast w przypadku standardowych płytek drukowanych wiertła mogą być ostrzone do trzech razy i dopiero potem wymienione.
3 – WIERCENIE MECHANICZNE
W zależności od serii proces wiercenia płytek PCB może obejmować różne konfiguracje. W przypadku produktów zaawansowanych technologicznie wiertarka obsługuje jeden panel na raz. Jednak w przypadku innych serii możliwe jest jednoczesne wiercenie nawet do czterech paneli, przy użyciu od jednej do sześciu głowic wiercących, w zależności od ich grubości. W przeszłości, w latach 90., minimalna średnica wierconych otworów wynosiła 400 mikrometrów. Obecnie jesteśmy w stanie wiercić otwory o minimalnej średnicy 150 mikrometrów.
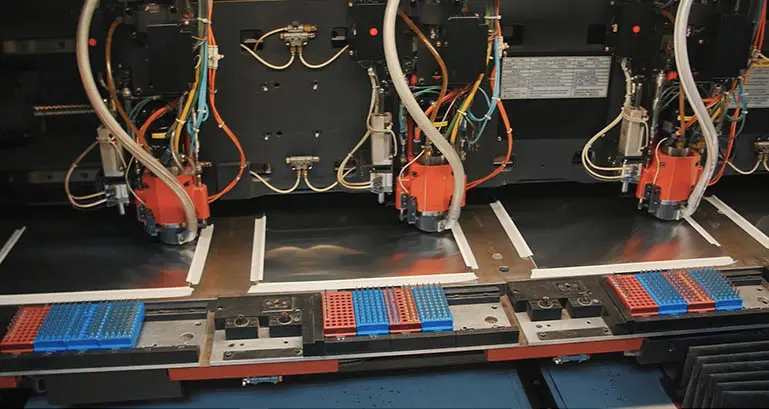
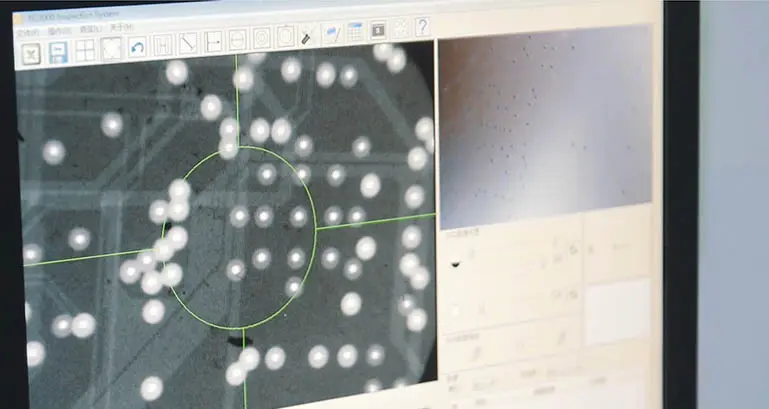
4 – KONTROLE
Aby pomóc w kontroli wizualnej, na krawędzi każdej płyty wiercone są wszystkie otwory o różnych rozmiarach, które są poddawane inspekcji po etapie wiercenia. Panele są również automatycznie sprawdzane za pomocą maszyny do weryfikacji otworów. W celu kontroli wewnętrznej płyty przechodzą przez maszynę rentgenowską, która sprawdza całe ułożenie w stosunku do warstwy wewnętrznej.
5 – WIERCENIE LASEROWE
Wiertarka laserowa może wykonywać otwory przelotowe o średnicy od 50 do 150 mikrometrów. W procesie wiercenia laserowego wykorzystuje się głównie dwa rodzaje laserów: laser UV lub CO2, a czasami oba z nich, w zależności od konkretnego procesu. W przypadku wiercenia laserowego nie ma górnego ani dolnego materiału, dlatego możliwe jest wiercenie tylko jednego panelu na raz. Laser zatrzymuje się, gdy dotyka warstwy miedzi na warstwie N-1. W procesie wiercenia laserowego istnieją dwie główne kontrole – sprawdza się, czy wywiercone otwory spełniają wymagane wymiary i są czyste.
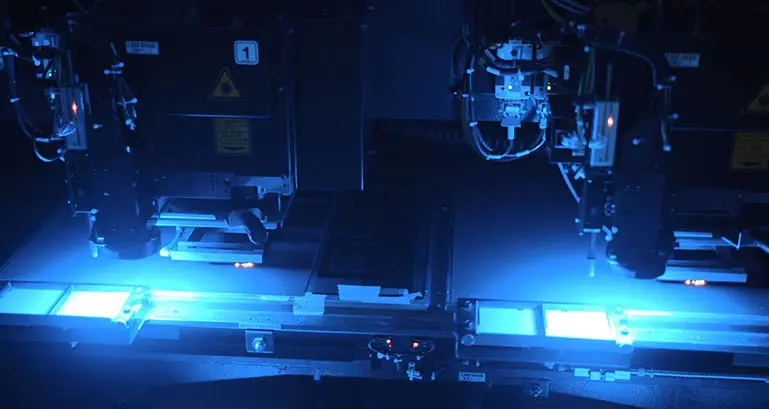
Miedź chemiczna i bezprądowa
Jak osadzić miedź na płytce drukowanej?
Chemiczne osadzanie miedzi, nazywane również miedziowaniem bezprądowym, tworzy połączenie elektryczne między warstwą wewnętrzną i zewnętrzną.
1 – STANDARDOWE CZYSZCZENIE
Przed nałożeniem miedzi chemicznej płytka musi być czysta. W przypadku standardowego procesu czyszczenie pozwoli na usunięcie wszelkich pozostałości po wierceniu.
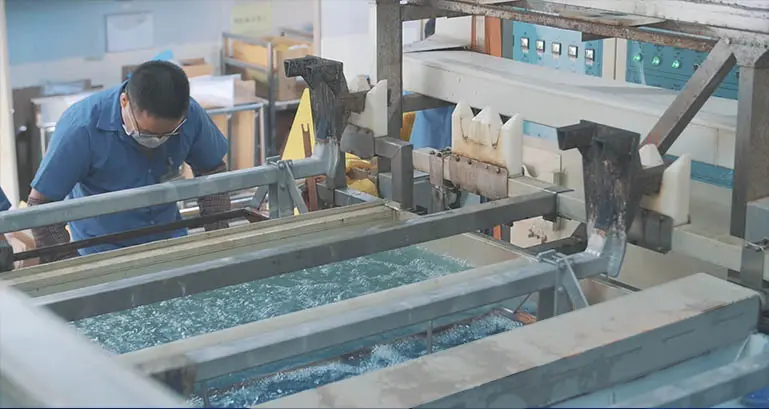
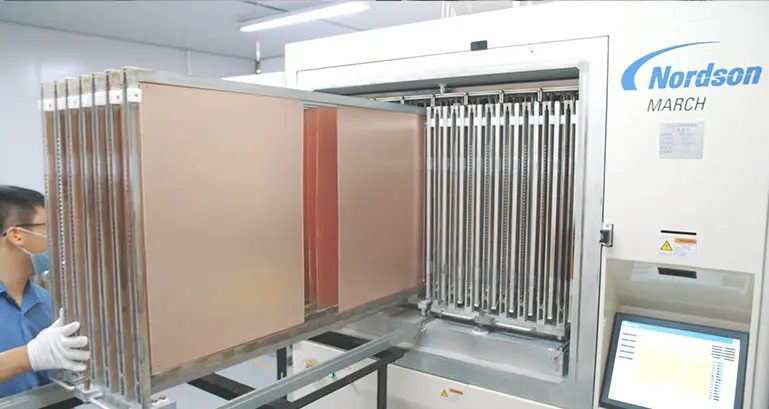
2 – CZYSZCZENIE PLAZMOWE
W przypadku produktów zaawansowanych technologicznie preferowany jest proces czyszczenia plazmowego. Czyszczenie plazmowe jest w stanie usunąć twardsze pozostałości, takie jak poliimidy, High Tg-FR4, teflon i materiały mikrofalowe RF. Ten opcjonalny proces zapewnia doskonałą chropowatość i zwilżalność, które są kluczowe dla późniejszego chemicznego osadzania miedzi.
3 – POWLEKANIE PALLADEM
Aby uzyskać przewodzące otwory, można zastosować różne obróbki chemiczne w zależności od konkretnej technologii PCB. Jedna z metod polega na użyciu palladu, miedzi, grafitu lub polimeru. W przypadku powlekania palladem płytki są zanurzane w kąpieli palladowej, znanej również jako kąpiel aktywacyjna, w celu osadzenia cienkiej warstwy palladu na powierzchni.
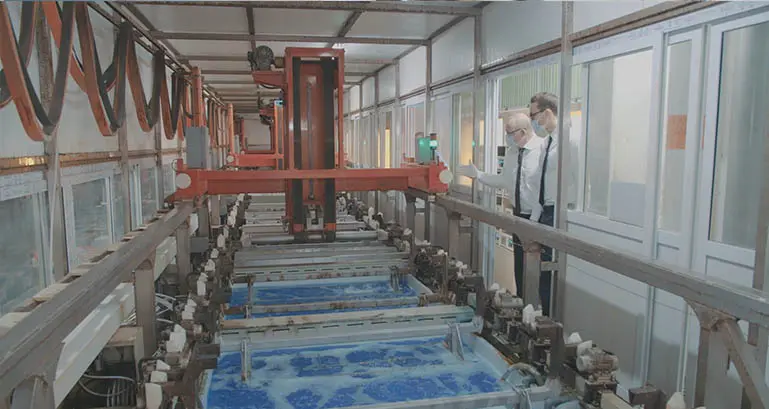
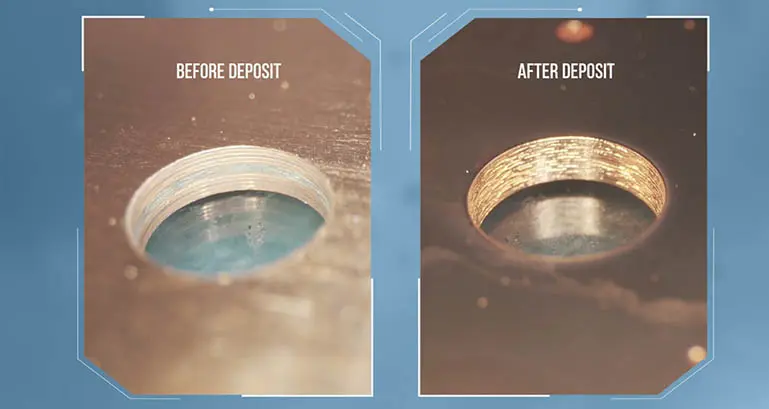
4 – MIEDZIOWANIE
Panele są stale przemieszczane w kąpieli, aby usunąć potencjalne pęcherzyki powietrza, które mogły powstać wewnątrz otworów. Pallad działa w sposób chemiczny, dzięki czemu od 1 do 3 mikrometrów chemicznej miedzi jest przyciągane do całej powierzchni panelu i niedawno wywierconych otworów.
5 – KONTROLE
Kontrola jest przeprowadzana na końcu tego procesu, głównie przeprowadzany jest test podświetlenia w celu sprawdzenia porowatości i powłoki miedzi.
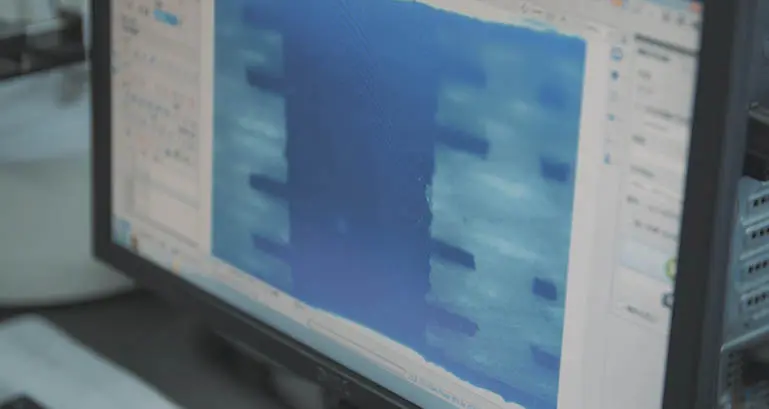
Obrazowanie warstwy zewnętrznej
Jak stworzyć idealny obraz warstwy zewnętrznej?
Obrazowanie warstwy zewnętrznej jest podobne do obrazowania warstwy wewnętrznej, jednak ze względu na obecność otworów i chropowatość powierzchni proces ten jest bardziej złożony. Zobaczmy, jak przebiega ten spektakularny etap procesu produkcji PCB!
1 – PRZYGOTOWANIE I LAMINOWANIE
Przed rozpoczęciem powierzchnia płytki PCB musi zostać odpowiednio przygotowana. Do płytek o grubości mniejszej niż 500 mikrometrów stosuje się proces czyszczenia chemicznego. W przypadku grubszych płytek preferowany jest proces czyszczenia mechanicznego przy użyciu szczotek ściernych. Następnie płytki są podgrzewane, aby zapewnić lepszą przyczepność warstwy fotorezystu. Po przygotowaniu powierzchni płytki są poddawane automatycznemu procesowi laminacji na osiach X i Y. Krawędź jest cięta bezpośrednio przez maszynę.
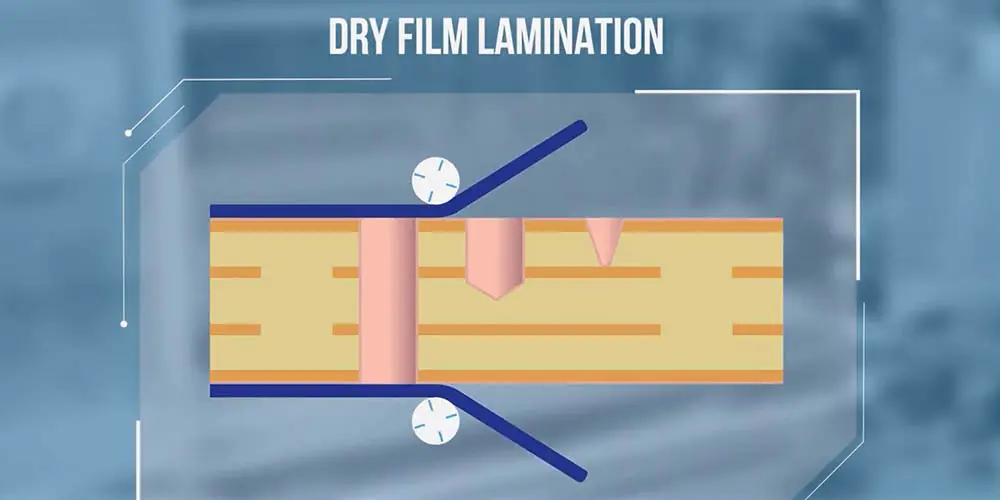
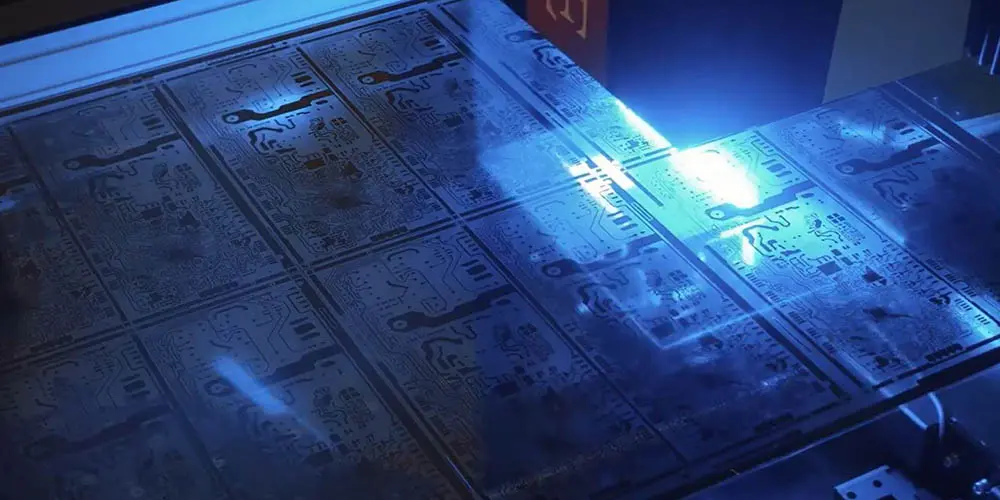
2 – POZYCJONOWANIE I NAŚWIETLANIE UV
W przypadku półautomatycznego izolowania grafika jest ponownie sprawdzana przed ponownym wprowadzeniem do maszyny. Proces rejestracji odbywa się optycznie za pomocą 2 lub 4 kamer CCD, które porównują pozycję wzoru z pozycją otworów. Po potwierdzeniu dokładnej rejestracji zastosowana jest próżnia, a następnie płytka jest poddawana działaniu światła UV przez okres od 1 do 20 sekund. Światło UV powoduje polimeryzację fotorezystu, co tworzy obraz wzoru obwodu na płytce.
3 – POZYCJONOWANIE I NAŚWIETLANIE LASEROWE
W przypadku produktów wysokiej klasy i materiałów o dużej gęstości stosuje się bezpośrednie obrazowanie laserowe. Ta maszyna jest w pełni automatyczna, co oznacza, że proces ładowania, rejestracji za pomocą 4 kamer CCD i przesyłania obrazu warstwy odbywa się w ciągu kilku sekund. Obrazowanie laserowe jest szczególnie ważne, gdy wymagane są dokładne tolerancje i ścisła rejestracja, taka jak 50 mikrometrów lub mniej.
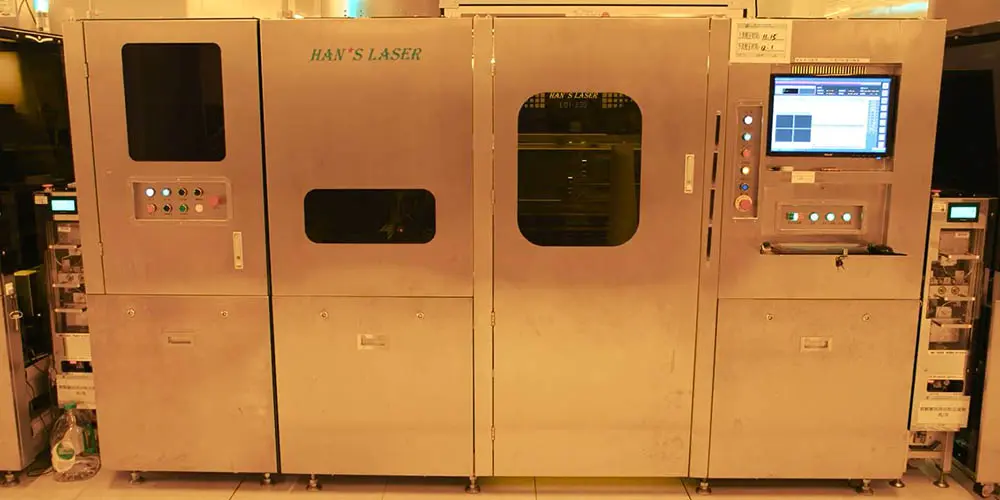
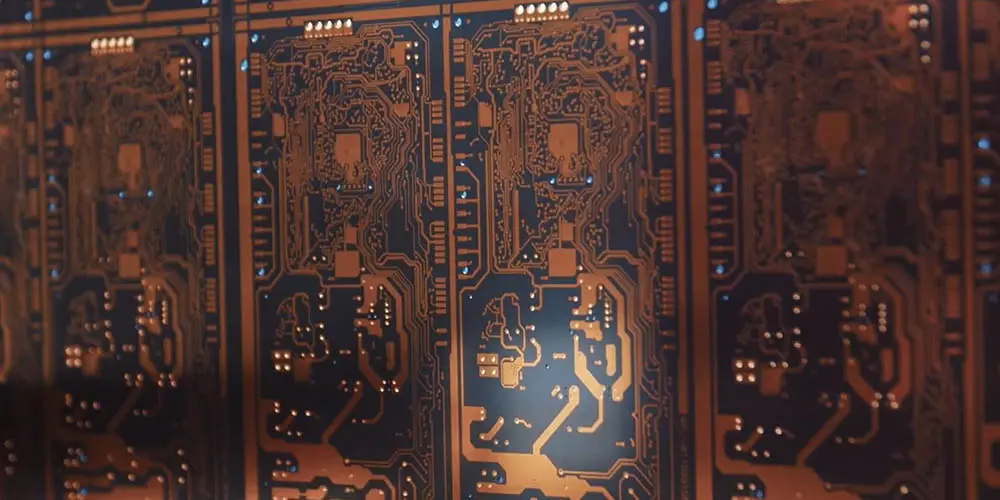
4 – ROZWÓJ
Po zakończeniu procesu nasłonecznienia usuwana jest warstwa ochronna na suchej folii. Obszary, które nie były wystawione na działanie światła UV lub lasera, pozostają nieutwardzone. Te obszary zostaną rozpuszczone w kąpieli sodowej, co doprowadzi do odsłonięcia pięknej niebieskiej barwy płytki. Obraz warstwy zewnętrznej jest teraz wydrukowany i gotowy do przyjęcia miedzi elektrolitycznej.
5 – AUTOMATYCZNA INSPEKCJA OPTYCZNA
Automatyczna inspekcja optyczna warstw zewnętrznych ma na celu potwierdzenie braku wad, takich jak przerwy elektryczne lub zwarcia. Podobnie jak w przypadku warstwy wewnętrznej oryginalny projekt z pliku GERBER służy jako model dla kamery optycznej. Jeśli zostanie wykryty problem, technik oceni go.
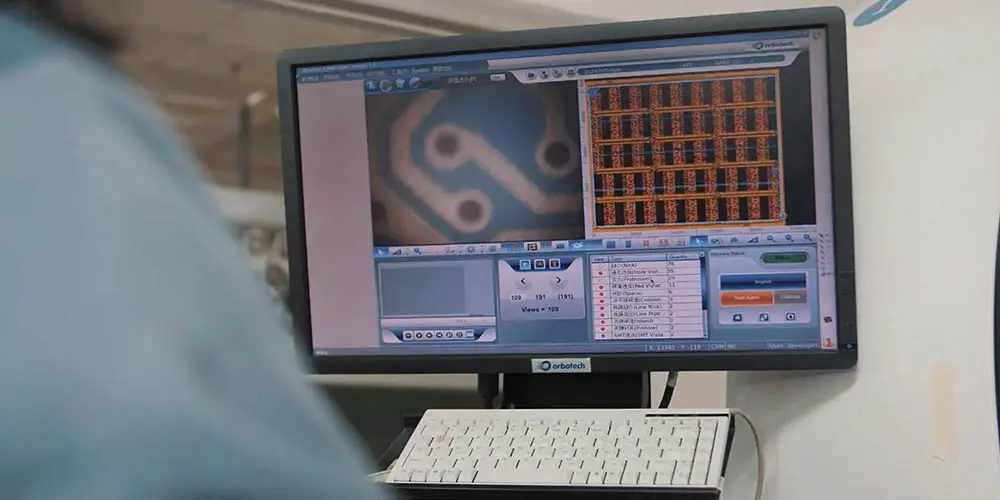
Miedź elektrolityczna
Co to jest elektrolityczne osadzanie miedzi?
Miedź może być osadzana elektrolitycznie przy użyciu dwóch procesów: procesu panelowego i procesu wzorcowego.
1 – POWLEKANIE PANELI
Miedź jest osadzana elektrolitycznie na całej powierzchni płytki oraz wewnątrz otworów w celu poprawy równości i rozprowadzenia miedzi. Miedź elektrolityczna powoduje elektrolizę, czyli przepływ prądu elektrycznego przez roztwór, co prowadzi do reakcji chemicznych. Po kilku krokach trwających po 3 minuty każdy ma miejsce elektroliza, gdzie miedź w roztworze działa jako anoda, a płytki pełnią rolę katody.
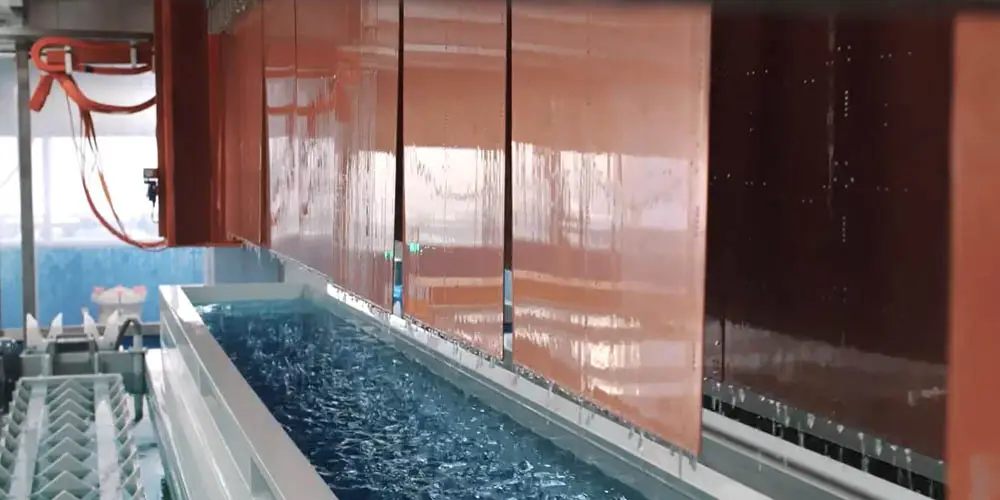
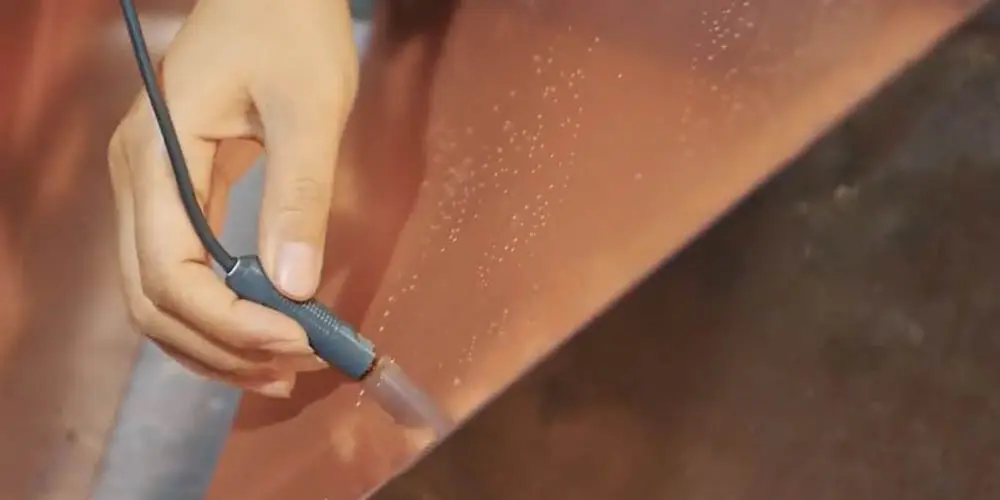
2 – KONTROLA
Miedź jest teraz grubsza i bardziej niezawodna – jej grubość wynosi od 10 do 13 mikrometrów. Następnym krokiem będzie obrazowanie warstwy zewnętrznej.
3 – POWLEKANIE – OSADZANIE MIEDZI
Miedź jest osadzana elektrolitycznie, ale w znacznie większych ilościach. Aby zapewnić odpowiednie połączenie i dobrą przewodność między otworami, płytki wymagają przynajmniej 20 do 25 mikrometrów miedzi wewnątrz ścianek otworów zgodnie ze standardami IPC. Podczas kąpieli trwającej 60 minut miedź, działająca jako anoda, osadza się na powierzchni płytek.
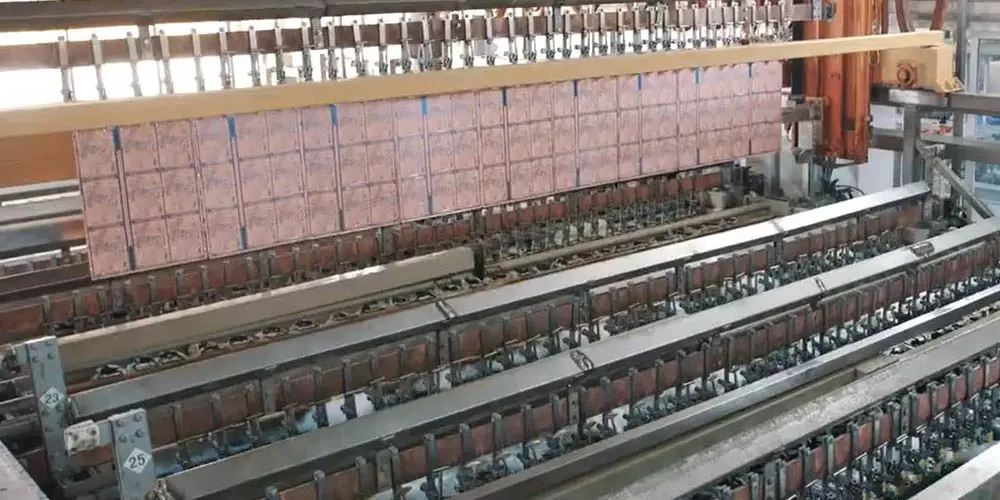
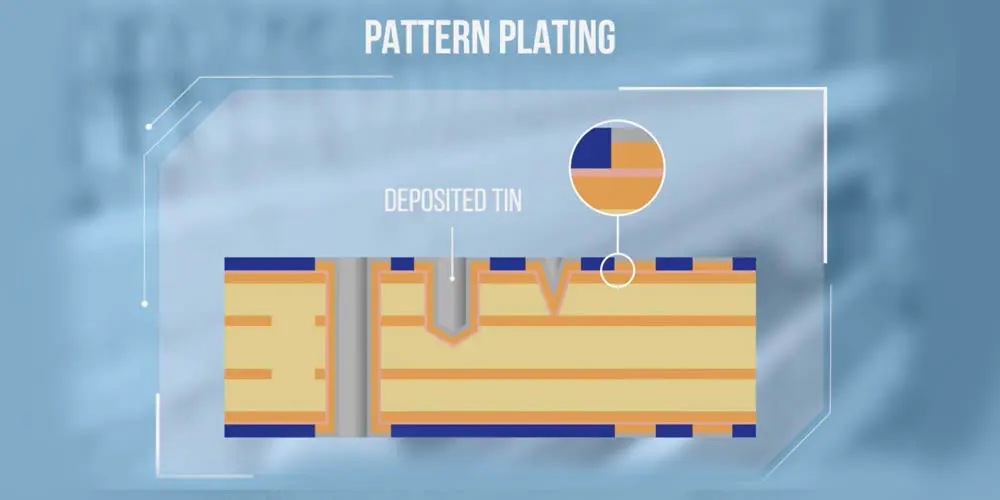
4 – POWLEKANIE – OSADZANIE CYNY
Po kąpieli płuczącej płytki są zanurzane w cynie elektrolitycznej, która pokrywa całą miedź warstwą o grubości od 1 do 3 mikrometrów. Cyna jest niezbędna do ochrony miedzi podczas procesu wytrawienia.
5 – KONTROLA
Po całkowitym pokryciu są one testowane metodą nieniszczącą w celu sprawdzenia grubości powłoki.
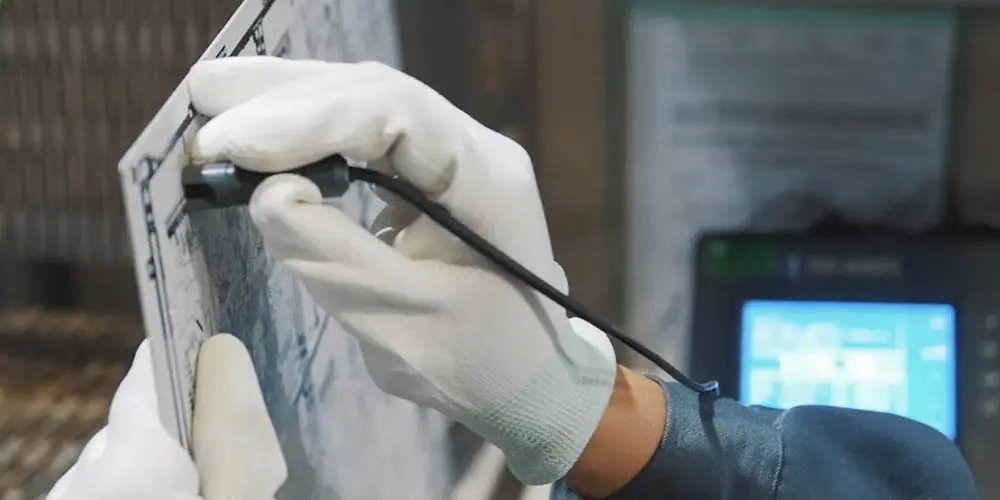
Wytrawianie płytek drukowanych
Co to jest wytrawianie?
Wytrawianie to złożony proces chemiczny, który usuwa niepożądaną miedź i cynę z płyt.
1 – USUWANIE FOLII
Pierwszym krokiem jest usunięcie suchej folii. Wszystkie pozostałości są rozpuszczane, a folia jest usuwana, odsłaniając niechcianą miedź.
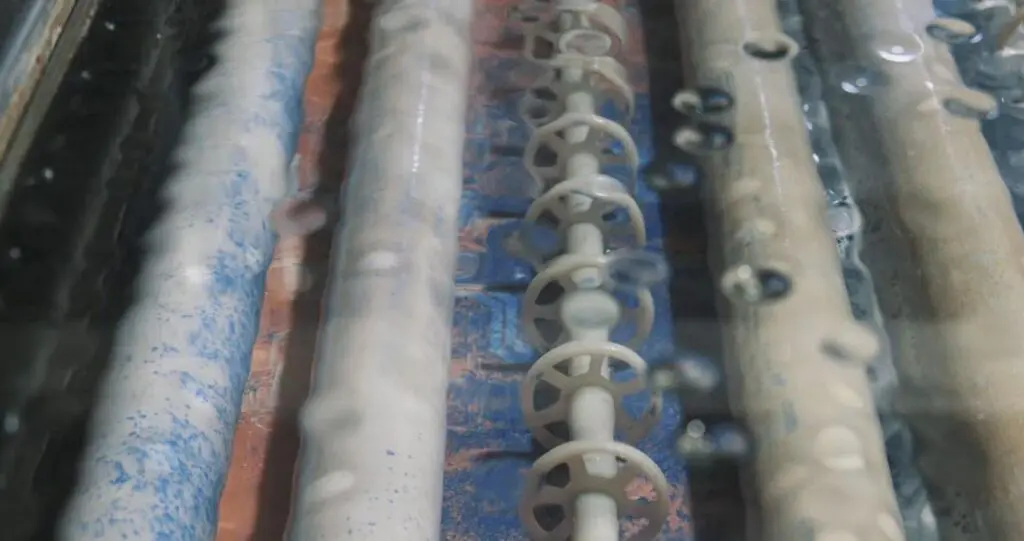
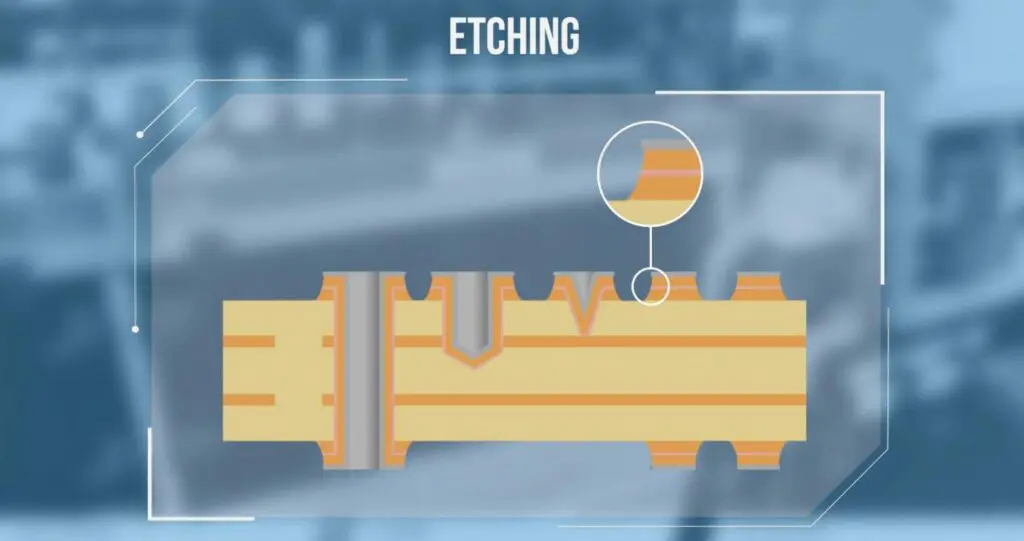
2 – WYTRAWIANIE
Etap wytrawiania rozpoczyna się od kąpieli w roztworze chemicznym. Wyzwaniem jest uniknięcie nadmiernej lub niedostatecznej obróbki chemicznej, która mogłaby uniemożliwić uzyskanie prostych ścianek. Co do warstwy wewnętrznej, odsłonięta miedź jest wytrawiana i kształtuje się wzór. W tym przypadku cyna chroni miedź i otwory.
3– CYNOWANIE
Cyna jest usuwana chemicznie. Obszary przewodzące i połączenia są teraz odpowiednio określane.
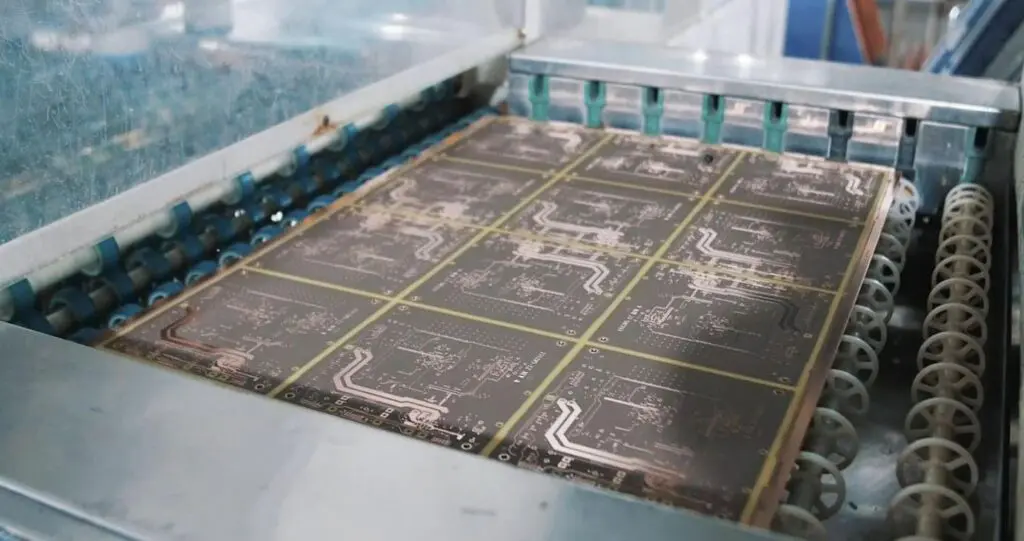
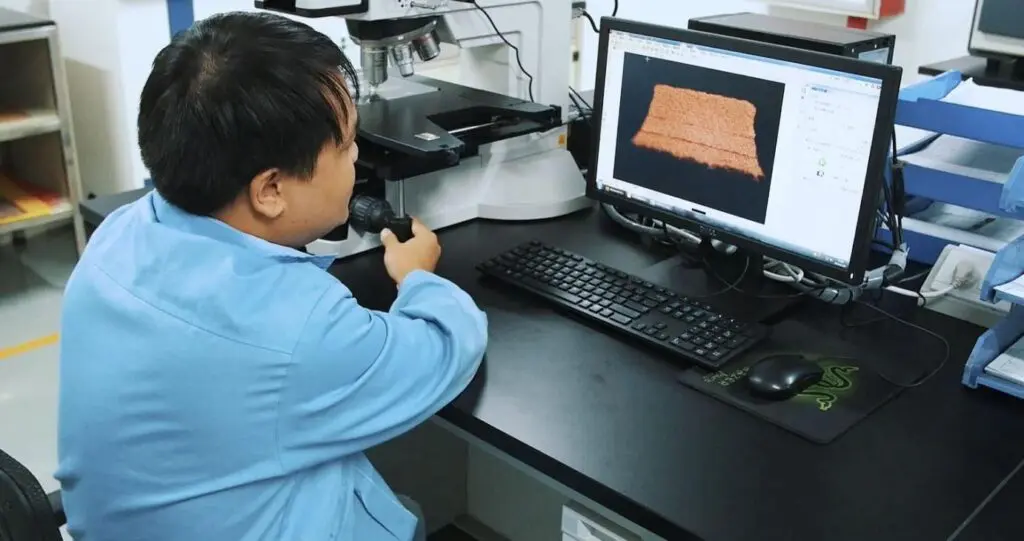
4 – KONTROLA
Test laboratoryjny jest przeprowadzany w celu wykrycia nadmiernego lub niedostatecznego wytrawienia oraz upewnienia się, że wszystkie niepożądane warstwy miedzi zostały usunięte z wyjątkiem warstwy rezystywnej.
5 – AUTOMATYCZNA INSPEKCJA OPTYCZNA
Automatyczna inspekcja optyczna jest przeprowadzana bezpośrednio po wytrawieniu i porównywana z danymi, aby wykryć wszelkie niespójności i zagwarantować brak wad. W niektórych przypadkach na tym etapie można naprawić zwarcie lub przerwę elektryczną.
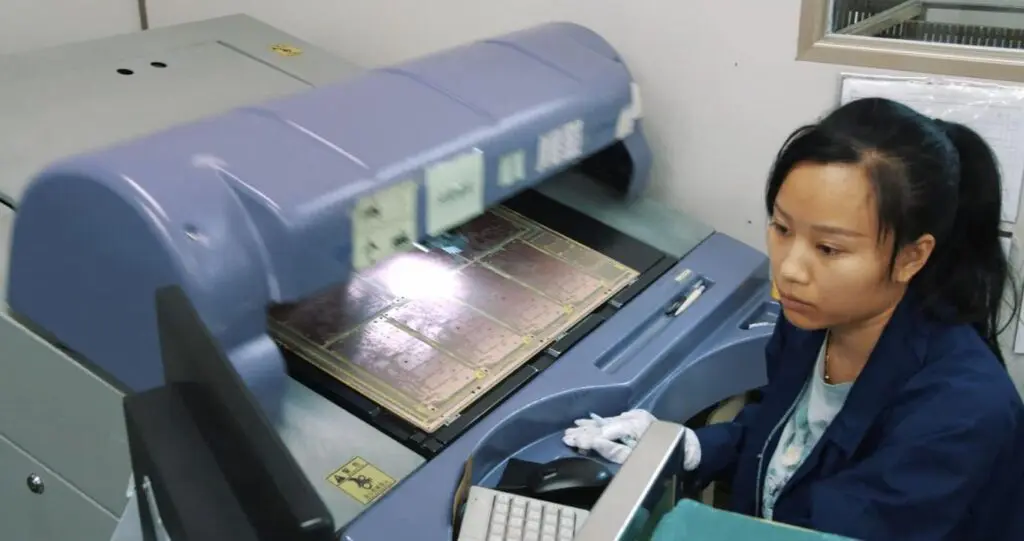
Maska lutownicza do płytek drukowanych
Dlaczego płytki drukowane potrzebują maski lutowniczej?
Maska lutownicza ma dwa zastosowania. Pierwszym z nich jest uniknięcie utleniania miedzi, a drugim uzyskanie idealnej izolacji między dwiema ścieżkami miedzianymi podczas procesu montażu. Istnieją różne rodzaje maski lutowniczej PCB, takie jak płynna epoksydowa maska lutownicza, płynna fotoobrazowa maska lutownicza (LPI) lub ducha folia. Zobaczmy!
1 – POWLEKANIE
Istnieją różne sposoby nakładania maski lutowniczej na płytkę drukowaną, takie jak nakładanie za pomocą kurtyny, sitodruk lub powlekanie metodą elektrorozpylania, zgodnie ze standardami IPC. Przed nałożeniem maski lutowniczej, płytki muszą być poddane czyszczeniu mechanicznemu lub chemicznemu w pomieszczeniu czystym o podwyższonym ciśnieniu, aby zapobiec przedostawaniu się zanieczyszczeń z zewnątrz.
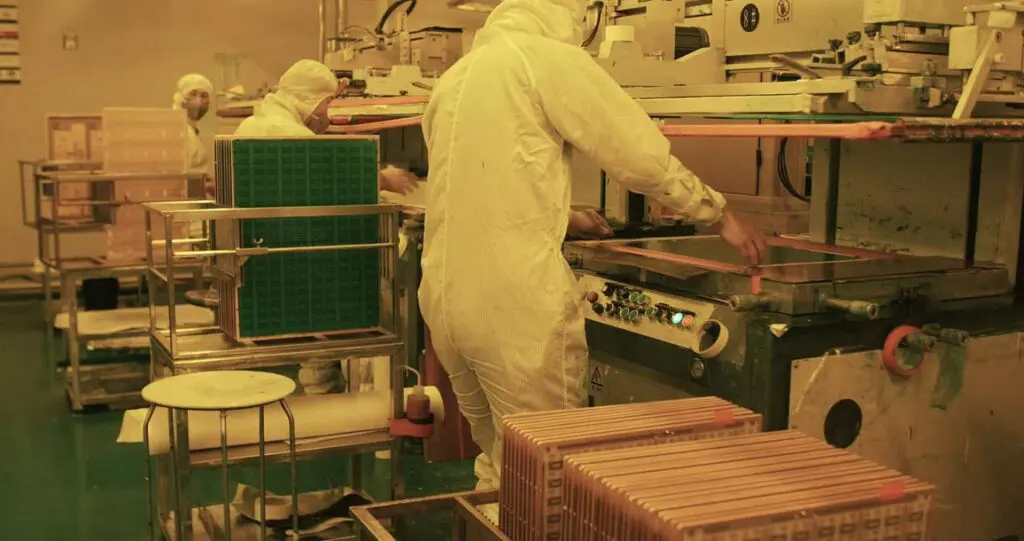
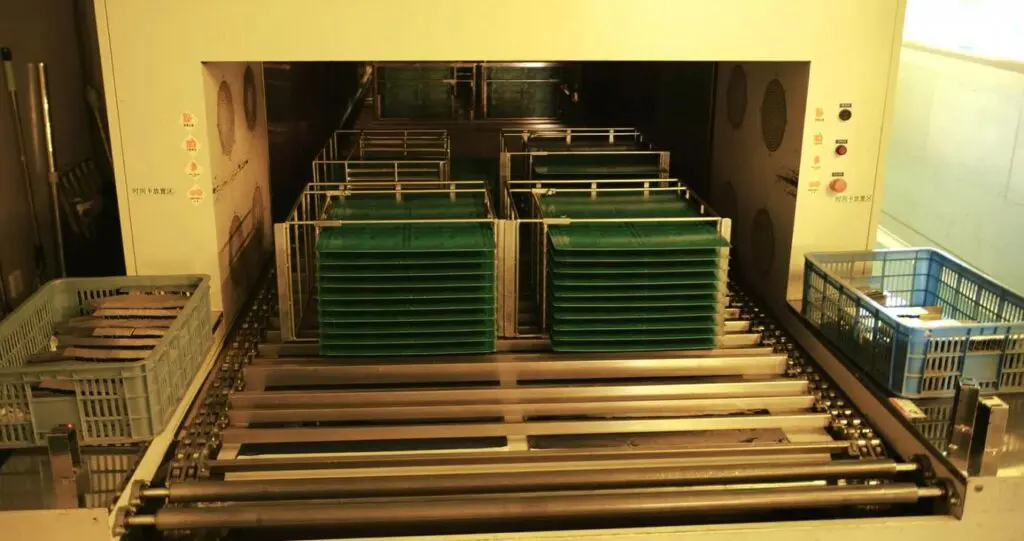
2– UTWARDZANIE WSTĘPNE
Po całkowitym pokryciu panelu należy go wstępnie utwardzić. Ten krok jest niezbędny i usuwa cały rozpuszczalnik z atramentu. Bez tego kroku rejestracja nie zostanie przeprowadzona prawidłowo.
3 – REJESTRACJA/IZOLACJA
Maska lutownicza może być naświetlana przy użyciu technik rejestracji obejmujących 8 kamer CCD i grafikę. Płytki są naświetlane krótkim impulsem światła LED, aby utwardzić maskę lutowniczą w obszarach, w których grafika jest widoczna. Alternatywnie można zastosować bezpośrednie obrazowanie laserowe (LDI), eliminując potrzebę tworzenia grafiki, ponieważ maszyna bezpośrednio naświetla i utwardza określone miejsca za pomocą skupionych wiązek światła.
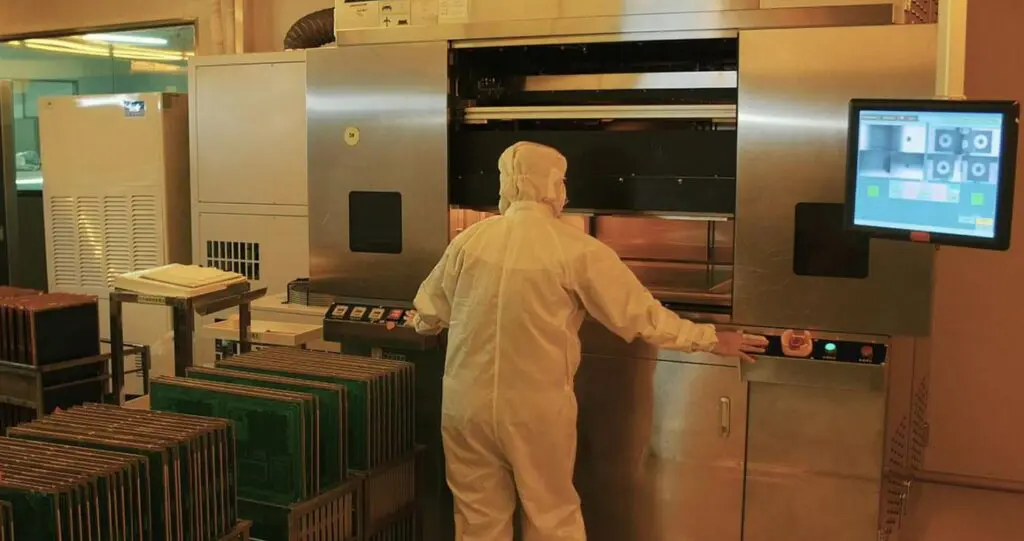
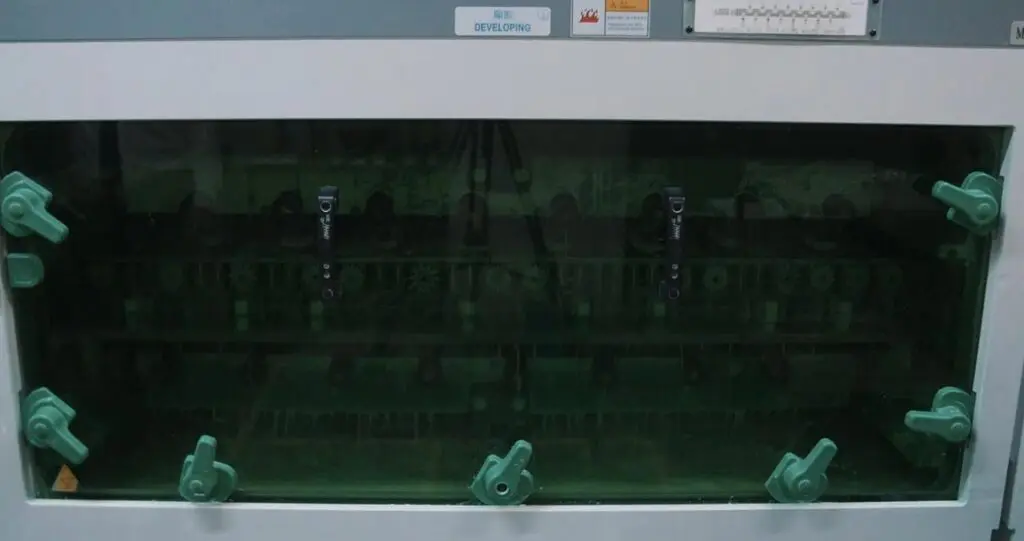
4 – ROZWÓJ
Obszary, które nie zostały zabezpieczone i utwardzone podczas procesu nasłoneczniania, są zmywane. W tym przykładzie usunięto maskę lutowniczą wokół mechanicznego otworu przelotowego.
5 – KONTROLA I UTWARDZANIE
Po zakończeniu fazy rozwoju wszystkie płytki są kontrolowane. Kontrola ta jest niezbędna do wykrycia wszelkich wadliwych obrazów, śladów atramentu na padach lub przez otwory. Po zakończeniu inspekcji płytki są poddawane działaniu wysokiej temperatury przez godzinę w celu utwardzenia maski lutowniczej.
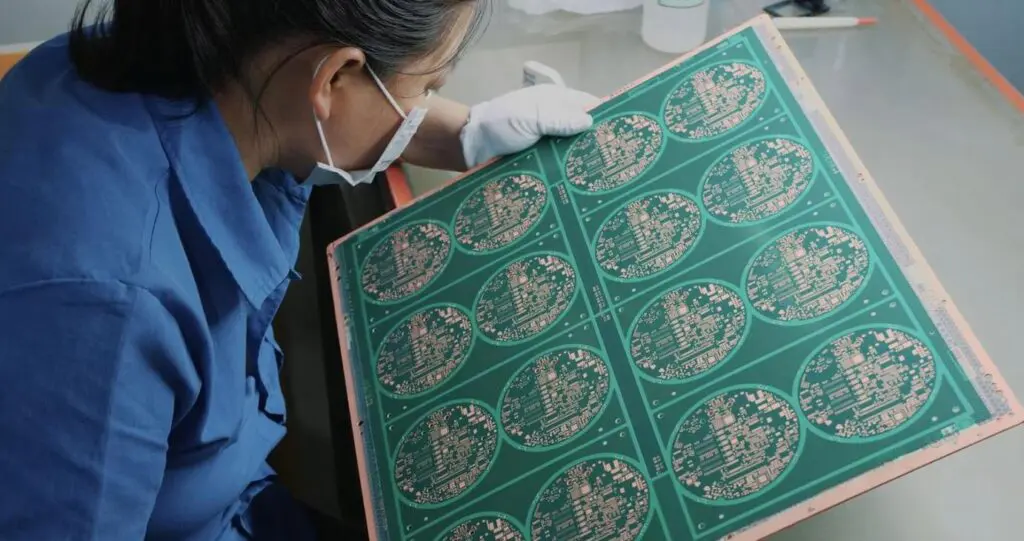
Druk sitowy na płytkach drukowanych
Czy druk sitowy na płytce drukowanej jest ważny?
Podczas druku sitowego na tablicy drukowane są wszystkie istotne informacje, takie jak oznaczenia producenta, numery identyfikacyjne firmy i etykiety ostrzegawcze. W procesie tym wykorzystywane są głównie dwie metody: sitodruk, znany również jako druk sitowy, oraz DLP, czyli Direct Legend Printing na drukarce atramentowej. Proces ten wygląda na prosty, ale jak każdy etap produkcji PCB, wymaga precyzji.
1– SITODRUK
W procesie sitodruku, grafika z pliku GERBER odgrywa kluczową rolę, podobnie jak na innych etapach produkcji PCB. Powszechnie stosowaną metodą jest sitodruk, znany również jako serigrafia. Niezależnie od tego, czy jest wykonywany ręcznie, czy automatycznie, sitodruk polega na użyciu sit poliestrowych, które są rozciągnięte na aluminiowych ramach. Aby zapewnić precyzyjne wyrównanie i zapobiec rozmazywaniu się tuszu na miedzianym wzorze lub wpływaniu na proces lutowania, zarówno aluminiowe ramy, jak i panel są starannie rejestrowane. Atrament jest następnie nakładany na laminat poprzez przepchnięcie go przez szablon utworzony przez sito.
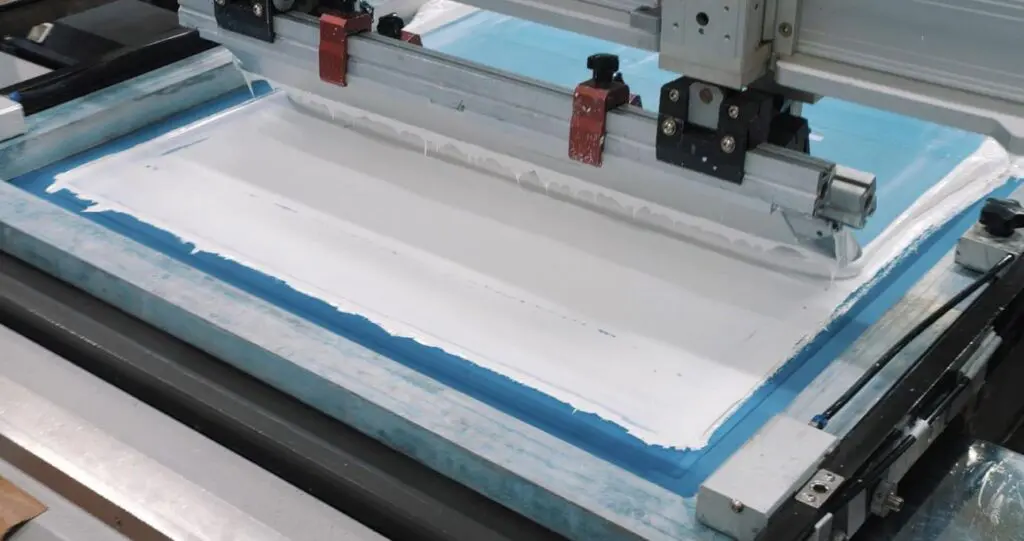
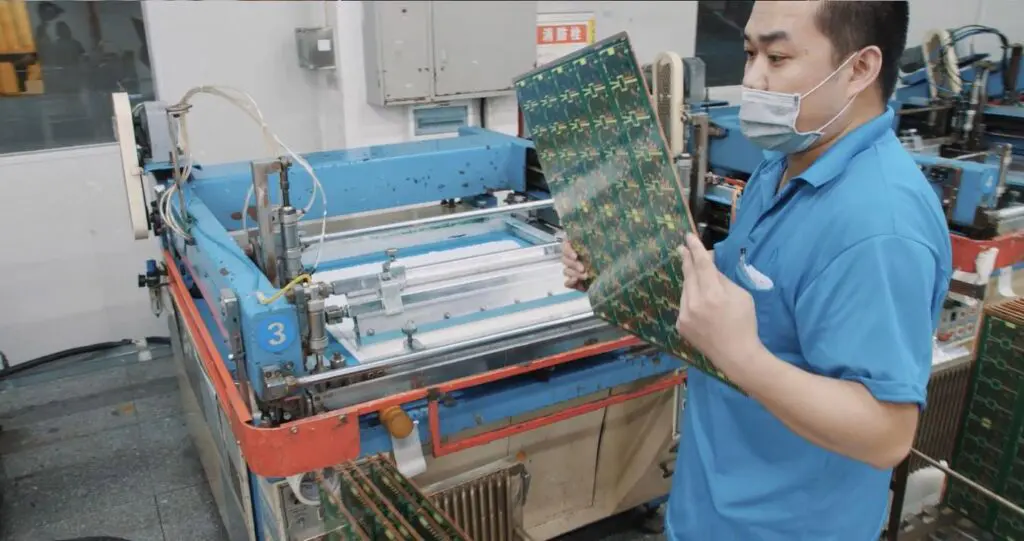
2 – KONTROLA
Po naniesieniu prawidłowych informacji na płytkę drukowaną, operator przeprowadza kontrolę wizualną. W przypadku usterki operator oceni problem lub usunie płytkę z procesu produkcyjnego
3 – UTWARDZANIE WSTĘPNE
Po udanym procesie sitodruku, płytki przechodzą etap utwardzania w celu zestalenia tuszu.
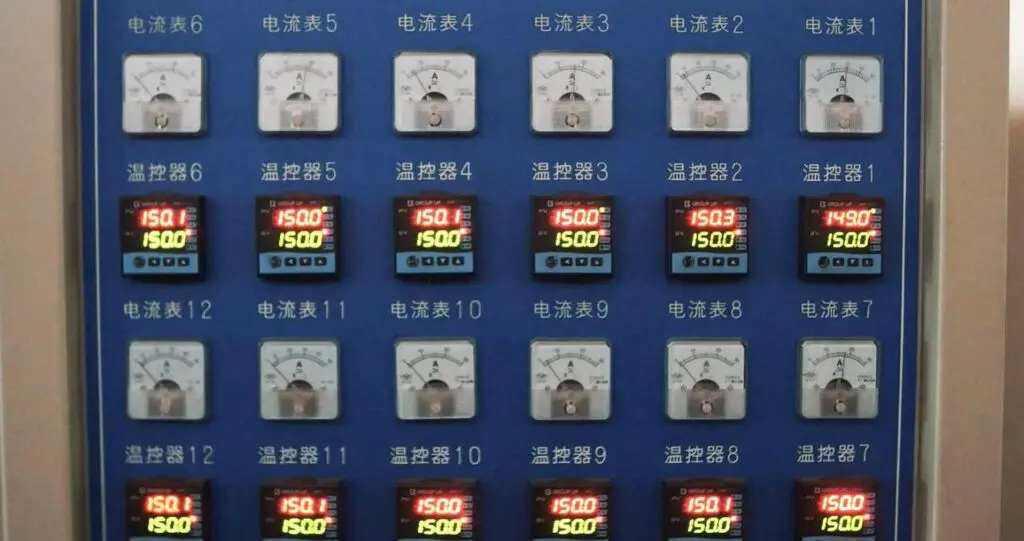
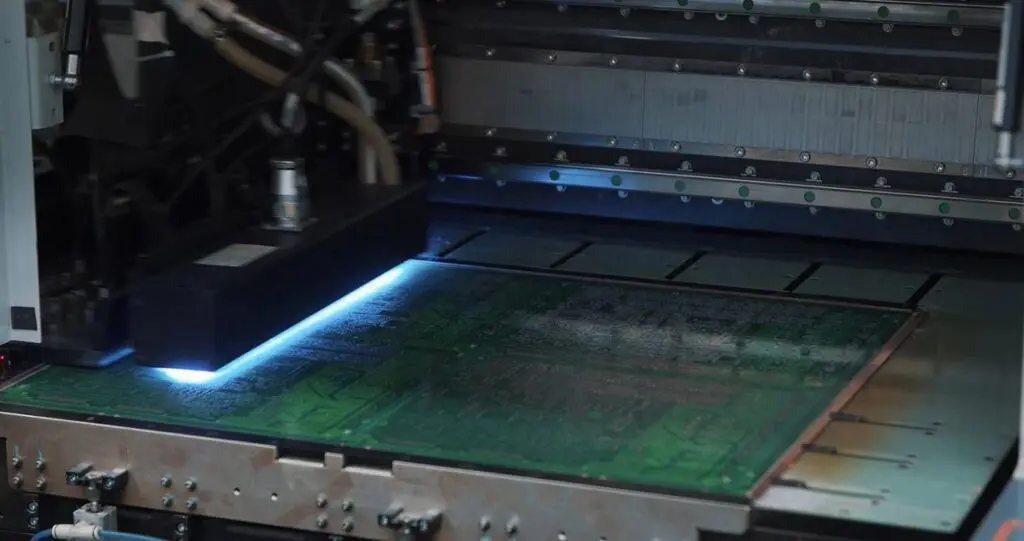
4 – DRUKARKA ATRAMENTOWA
Drugą metodą nanoszenia tekstu jest DLP lub Direct Legend Printing, który działa podobnie do konwencjonalnej drukarki atramentowej. Rejestracja jest wykonywana automatycznie przez urządzenie. Drukarka atramentowa rozpyla kropelki atramentu na panelu w celu wygenerowania obrazku. Kropelki atramentu są bezpośrednio utwardzane przez lampy UV.
5 – KONTROLA
Operator przeprowadza również kontrolę wizualną, aby upewnić się, że tekst jest prawidłowo wydrukowany. Pomimo tego, że jest bardziej nowoczesny, DLP jest preferowany tylko do prototypowania i małych serii, podczas gdy sitodruk jest znacznie szybszy i używany do masowej produkcji.
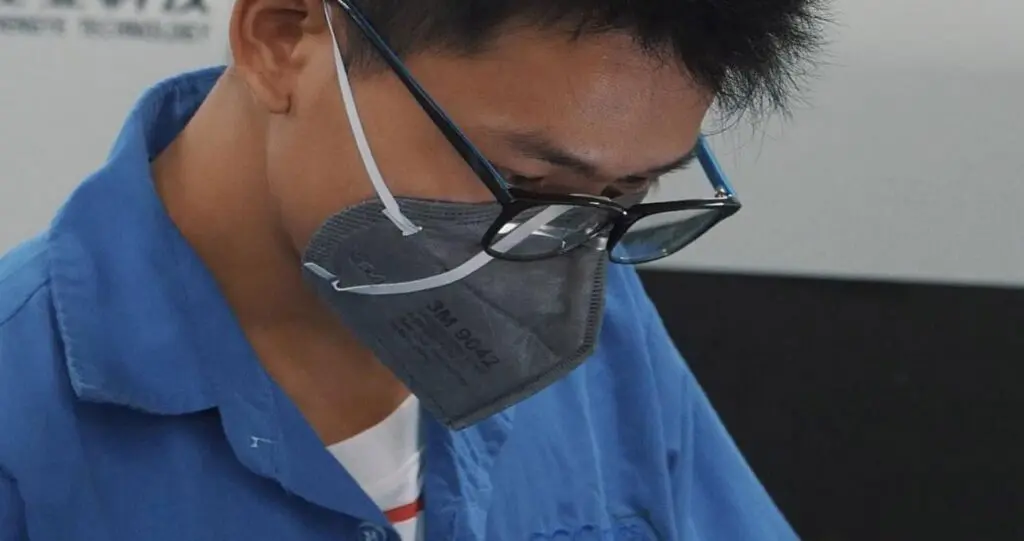
Wykończenie powierzchni płytek drukowanych
Jakie wykończenia powierzchni są dostępne?
Wykończenie powierzchni odnosi się do nakładania powłoki ochronnej między komponentami a gołą płytką PCB. Służy ona dwóm głównym celom: Zapewnia lutowność podczas fazy wypełniania i chroni miedź przed utlenianiem.
1 – Organic Solderability Preservative.
OSP to skrót od Organic Solderability Preservative. Jest to wykończenie powierzchni na bazie wody. OSP jest znany ze swojej przyjazności dla środowiska. Płytki są dokładnie czyszczone przed kąpielą, co skutkuje doskonałą płaską powierzchnią. Ten wydajny proces wymaga minimalnej ilości sprzętu, co czyni go opłacalnym wyborem do wykańczania powierzchni. OSP ma jednak ograniczony okres trwałości i może być wrażliwy podczas obróbki. W związku z tym proces frezowania jest zwykle wykonywany przed nałożeniem wykończenia powierzchni OSP. Mówiąc krótko, wykończenie powierzchni OSP oferuje korzyści dla środowiska i zapewnia płaską powierzchnię. Jest to ekonomiczne rozwiązanie, które w razie potrzeby można ponowić. Niemniej jednak ważne jest, aby wziąć pod uwagę krótki okres trwałości i wrażliwość podczas obróbki, a także możliwość narażenia miedzi podczas końcowego montażu.
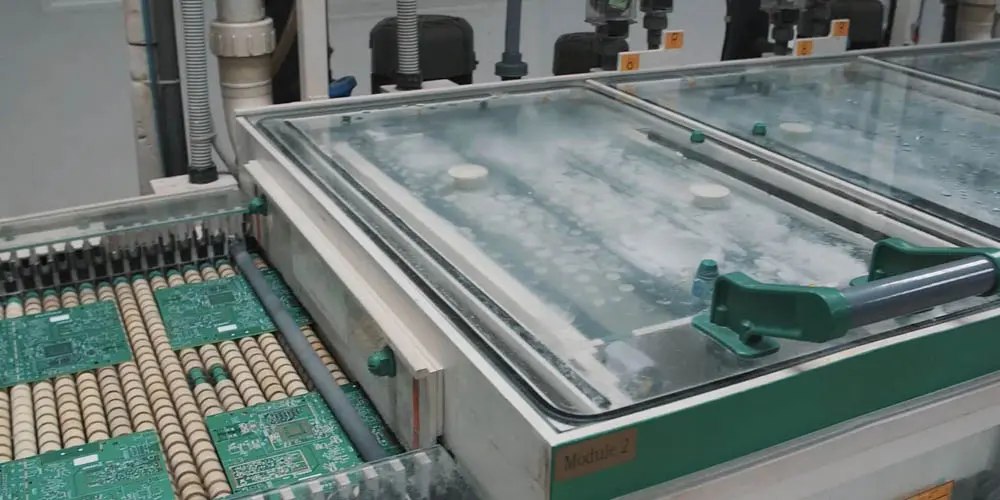
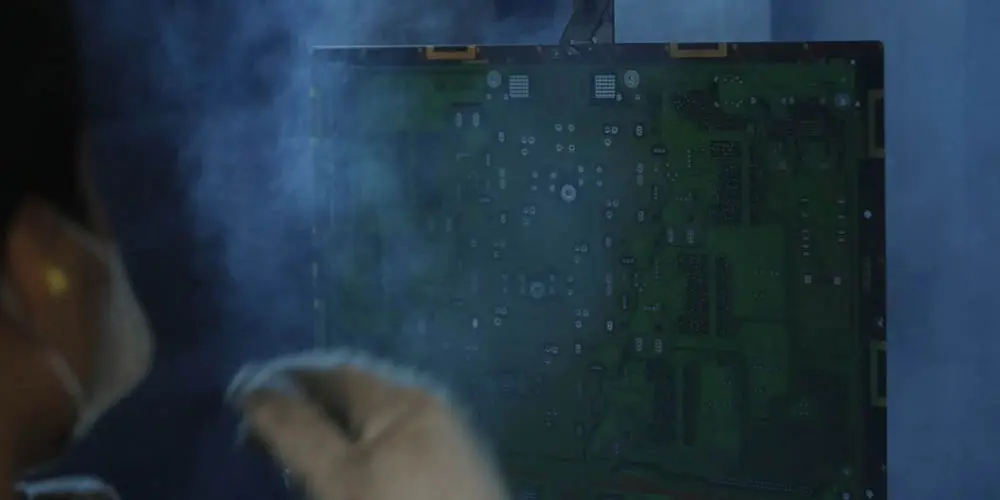
2 – HASL BEZOŁOWIOWY
HASL bezołowiowy to skrót od Hot Air Solder Leveling. Metoda ta była niegdyś popularnym wyborem do wykańczania powierzchni w produkcji PCB. Pomimo swojej solidności, jego przystępna cena wiąże się również z pewnymi ograniczeniami. Proces rozpoczyna się od mikrowytrawiania całego panelu, aby zapewnić czystą powierzchnię płytki. Następnie nakładana jest powłoka topnika, aby ułatwić przyczepność wykończenia powierzchni. Następnie płytka jest zanurzana w ciekłym lutowiu cynowym, a nadmiar lutowia jest usuwany za pomocą gorącego sprężonego powietrza wdmuchiwanego na powierzchnię. Zastosowanie HASL bezołowiowego zapewnia wyraźne korzyści dla produktów o wysokiej niezawodności. Jednak w przypadku coraz bardzie popularnych płytek HDI proces ten powoduje nierówne powierzchnie i nie nadaje się do komponentów o drobnej podziałce. Podsumowując, bezołowiowe wykończenie powierzchni HASL jest powszechnie dostępną technologią, tanim rozwiązaniem o dobrej trwałości. Należy jednak zauważyć, że może ono powodować nierówne powierzchnie, nie jest idealne dla komponentów o drobnej podziałce i może narażać płyty na naprężenia termiczne.
3 – ENIG
ENIG oznacza Electroless Nickel Immersion Gold Proces ten wymaga pokrycia konturów obwodu taśmą, aby uniknąć nadmiernego osadzania się złota, a także dlatego, że ENIG jest kosztownym procesem wykończeniowym. Panel jest zanurzany w kilku kąpielach. Początkowo elektrolitycznie osadzana jest warstwa 3-6 mikrometrów niklu w celu zwiększenia przyczepności. Następnie na panel nakładana jest elektrolitycznie warstwa złota o grubości co najmniej 0,05 mikrometra. Ten proces zanurzeniowy zapewnia doskonałą płaskość, podczas gdy warstwa złota zapewnia silną lutowność. Podsumowując, wykończenie powierzchni ENIG dobrze nadaje się do łączenia, oferuje wysoką lutowność, zapewnia płaską powierzchnię i ma dobry okres trwałości. Należy jednak zauważyć, że to wykończenie powierzchni jest złożonym i kosztownym procesem, co jest jedną z jego głównych wad.
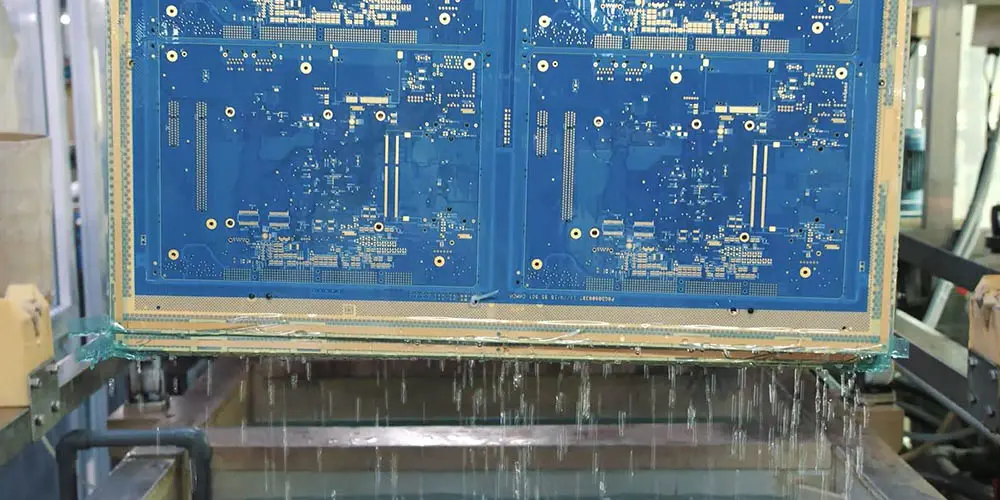
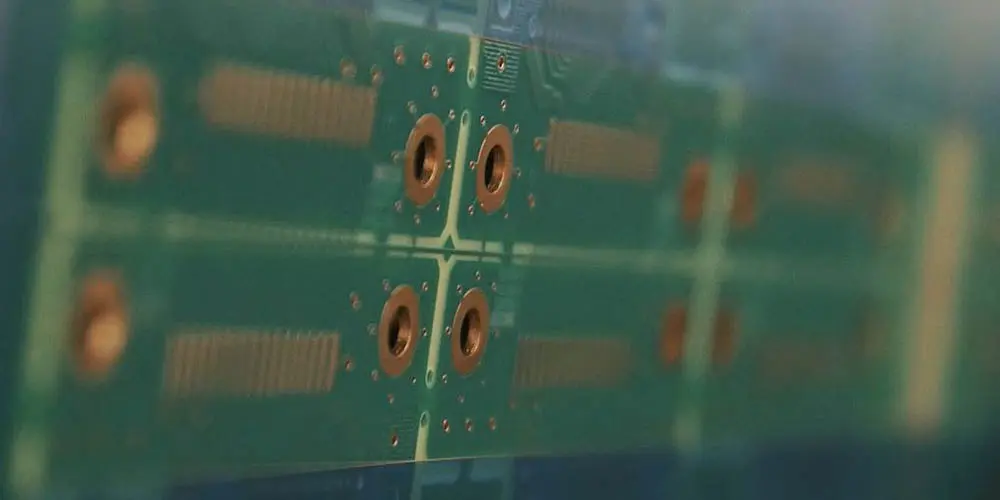
4 – TWARDE ZŁOCENIE
W przypadku twardego złocenia cały panel jest pokryty taśmą, a odsłonięte pozostają tylko obszary wymagające wykończenia powierzchni. W przeciwieństwie do ENIG grubość miedzi można kontrolować poprzez regulację czasu trwania cyklu powlekania. Proces rozpoczyna się od osadzenia elektrolitycznego warstwy niklu, po którym następuje osadzenie złota w oparciu o specyfikacje klienta. Grubość złota zapewnia doskonałą trwałość, ale jest również jedną z najdroższych opcji wykończenia powierzchni. Podsumowując, powłoka twardego złota oferuje właściwości mechaniczne, doskonałą trwałość i płaską powierzchnię. Należy jednak zauważyć, że wiąże się to z wysokimi kosztami, może mieć słabą lutowność i wymaga złożonego procesu.
5 – CYNA ZANURZENIOWA
Cyna zanurzeniowa to metaliczne wykończenie powierzchni, które obejmuje
zanurzanie płyt w różnych kąpielach chemicznych w celu zapewnienia optymalnej przyczepności warstwy cyny. Ten proces zapewnia płaską powierzchnię oraz skuteczną ochronę znajdującej się pod spodem miedzi. Jest to opłacalna opcja, ale silne powinowactwo między cyną a miedzią może prowadzić do powstawania wąsów cynowych.
Pomimo tej wady, wykończenie powierzchni cyną zanurzeniową jest powszechnie dostępne, zapewnia płaską powierzchnię, jest opłacalne i ma dobry okres trwałości. Dodatkowo w razie potrzeby nadaje się do ponownej obróbki.
Liczba przeróbek, którym można go poddawać, jest jednak ograniczona. Ponadto należy zachować ostrożność podczas obchodzenia się z cyną, ponieważ może być ona wrażliwa. Należy również wziąć pod uwagę możliwość powstawania wąsów cynowych.
ICAPE Group współpracuje z niemieckimi fabrykami w celu opracowania zaawansowanych technologicznie produktów wykończeniowych, w tym cyny zanurzeniowej, które spełniają oczekiwania niemieckiego przemysłu motoryzacyjnego.
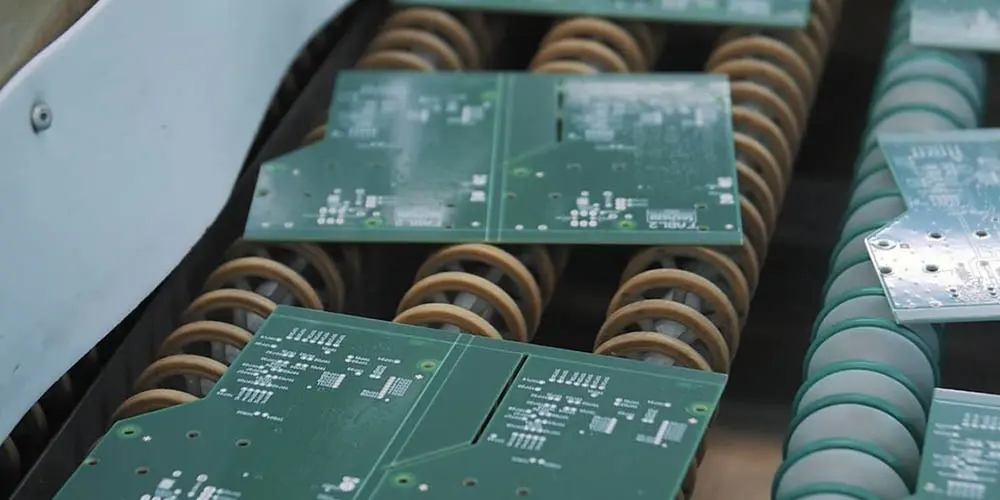
Trasowanie płytek drukowanych
Co to jest trasowanie płytek drukowanych?
Celem procesu trasowania, znanego również jako profilowanie, jest wycięcie każdej płytki drukowanej z panelu produkcyjnego. Nawet jeśli wszystkie płytki drukowane znajdują się na tym samym panelu, niekoniecznie wszystkie należą do tego samego klienta
1 – PRZYGOTOWANIE
Operator układa do 4 paneli w taki sam sposób, jak w przypadku procesu wiercenia. W tym przypadku proces frezowania wymaga frezarki i bitów z różną liczbą głowic: 1, 2, 4 lub 6 głowic.
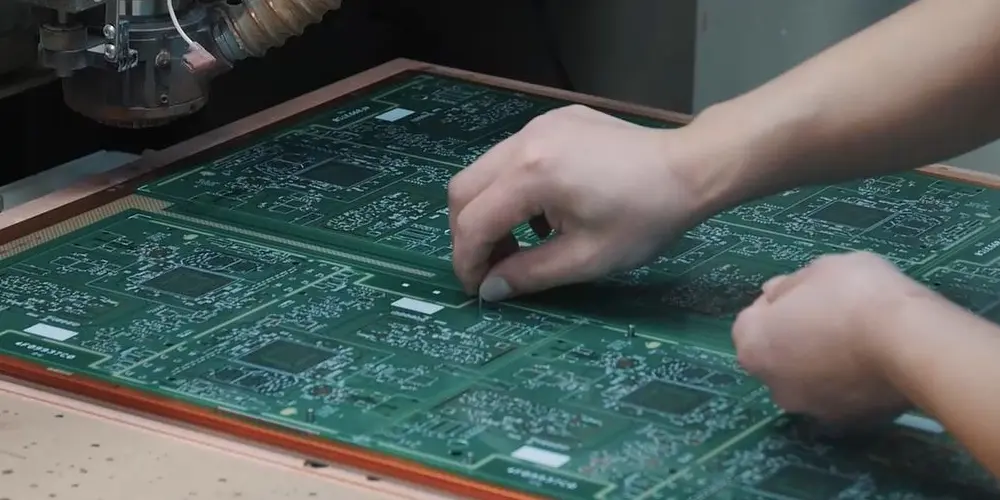
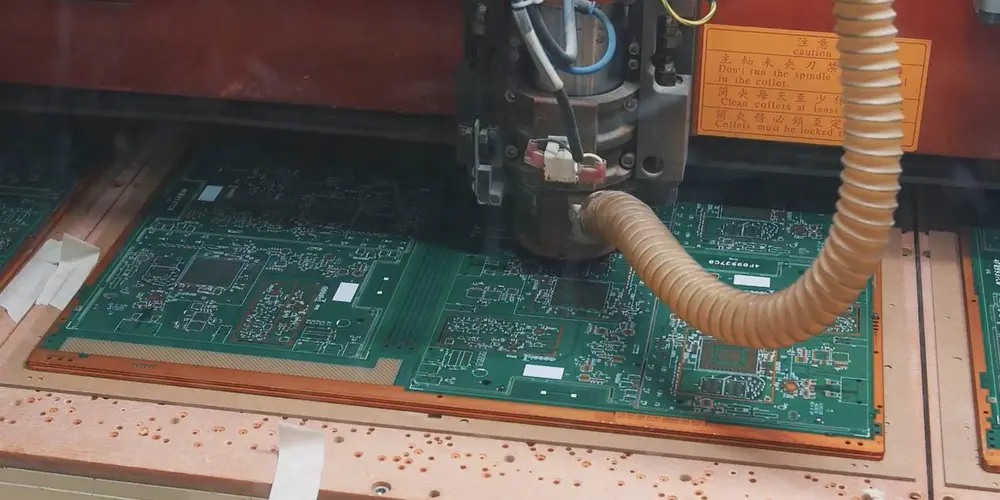
2 – TRASOWANIE
Podczas tego procesu tworzone są wewnętrzne i zewnętrzne kontury PCB. W tym samym czasie płytki są czyszczone, aby zapewnić, że w wyniku tej operacji nie pozostanie żaden pył. Po zakończeniu całego procesu operator zdejmuje wszystkie części ze stołu, a płytki drukowane są teraz depanelizowane. W zależności od życzenia klienta, płytki mogą być również frezowane bez depanelizowania.
3 – KONTROLA
Operator wykorzystuje kamerę optyczną do monitorowania wymiarów procesu frezowania, zapewniając, że wewnętrzne i zewnętrzne kontury zostały dokładnie wyfrezowane bez wpływu na obwód.
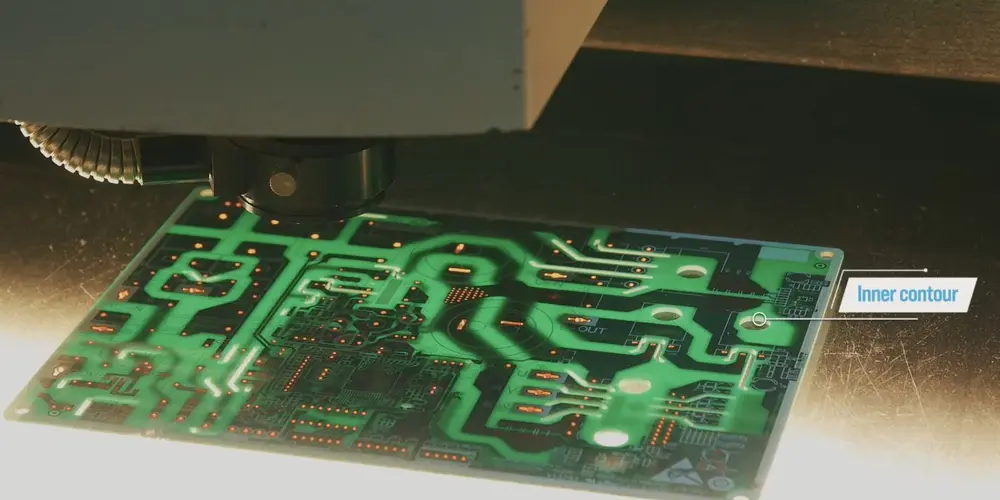
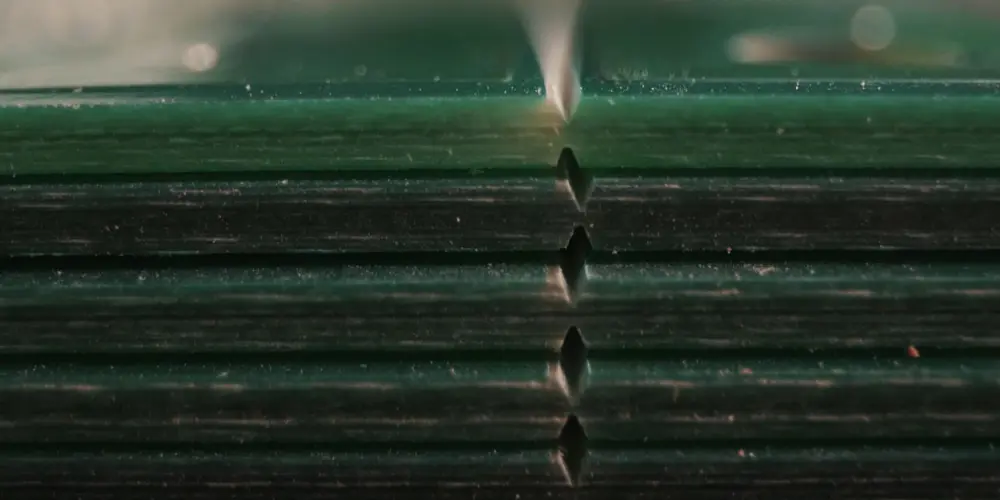
4 -– V-CUT
Po procesie trasowania, V-Cut lub V-Scoring jest stosowany do wstępnego cięcia PCB na panelu klienta, umożliwiając łatwe oddzielenie poszczególnych płytek po etapie montażu. Jest to główny cel tego kroku. Płyty można następnie łatwo oddzielić.
5 – KONTROLA
Po zakończeniu procesu V-Cut przeprowadzane są kontrole jakości przy użyciu testera V-Cut w celu pomiaru głębokości V-Cut zgodnie ze specyfikacją pliku GERBER.
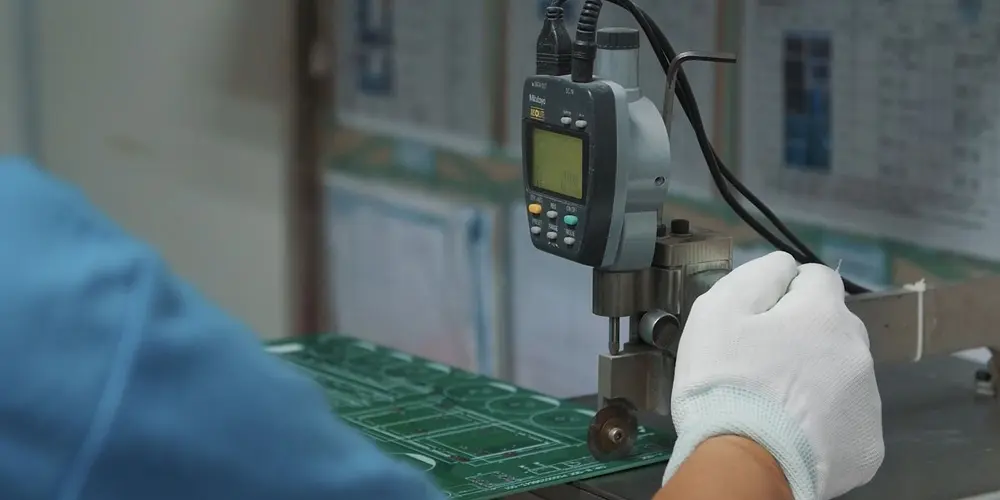
Testy elektryczne
Jak kontrolować przerwy i zwarcia na płytce drukowanej?
Testy te są przeprowadzane w celu upewnienia się, że na płytkach drukowanych nie ma zwarć i przerw. Istnieją dwa rodzaje maszyn o różnych zaletach: „latająca sonda” oraz „łoże gwoździ”.
1 – LATAJĄCA SONDA
Maszyna odczytuje plik GERBER, a operator umieszcza płytki w panelu lub pojedynczo. Następnie zestaw 4, 6 lub 8 głowic umieszczonych po każdej stronie inicjuje procedurę testowania. Głowice te przykładają ładunek elektryczny do obwodów, utrzymując ciągły kontakt z każdą płytką stykową w celu sprawdzenia braku jakichkolwiek przerw lub zwarć. W przypadku wykrycia jakichkolwiek problemów, operator interweniuje w celu ich rozwiązania.
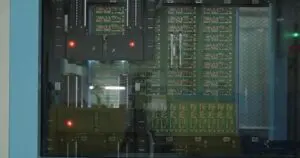
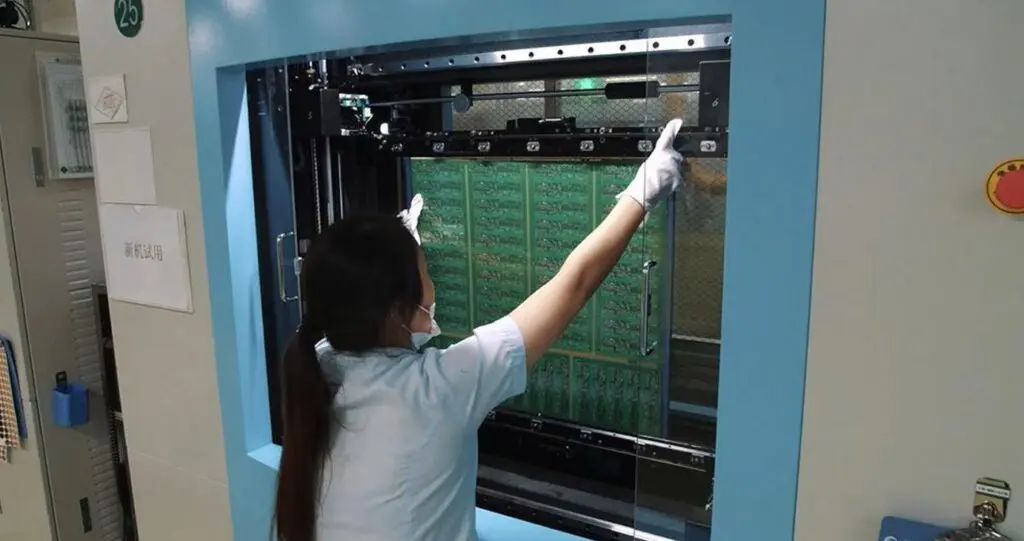
2 – WADY I ZALETY
Oprzyrządowanie jest opłacalne, najczęściej używane do prototypowania i małych serii. Nadaje się również do PCB HDI, ale głównym ograniczeniem jest ręczna zmiana płytek drukowanych za każdym razem, co wydłuża cykl pracy.
3 – ŁÓŻKO GWOŹDZI
Łóżko gwoździ, znane również jako uniwersalny test siatki, wymaga użycia specjalistycznego oprzyrządowania testowego. Oprzyrządowanie to jest projektowane na zamówienie w oparciu o plik GERBER, co oznacza, że jest unikalne dla każdej testowanej płytki PCB. Operator jest odpowiedzialny za staranne umieszczenie wielu pinów o różnych rozmiarach na uchwycie, aby pokryć wszystkie obszary testowe. Proces przygotowania do tego testu może być zarówno kosztowny, jak i czasochłonny! Jednak po wyrównaniu pinów z punktami testowymi na płytce drukowanej wszystkie punkty testowe mogą być sprawdzane jednocześnie. Dzięki temu proces testowania jest szybki i wysoce niezawodny.
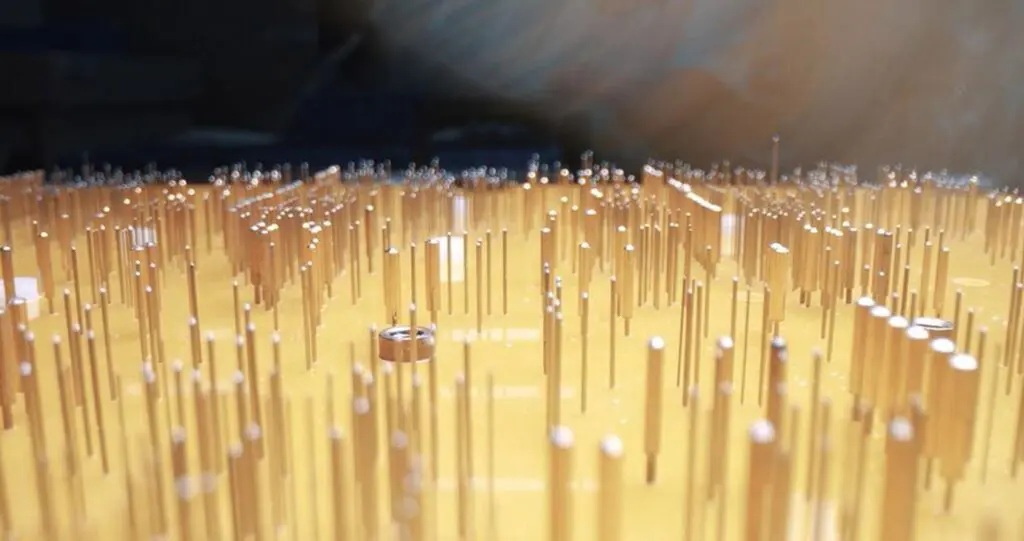
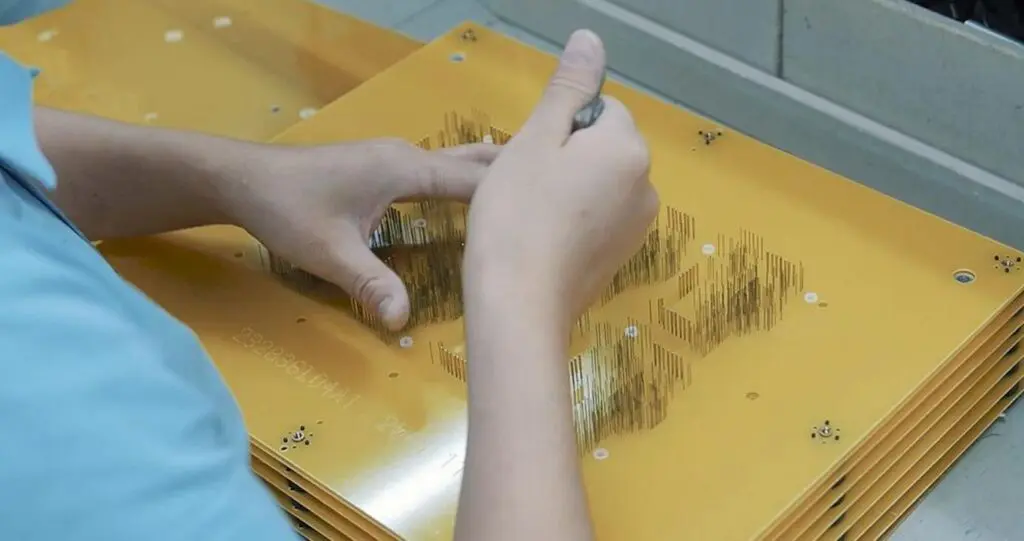
4 – WADY I ZALETY
Test typu łóżko gwoździ podobnie jak test latającej sondy, ma swoje zalety i wady. Ten test elektryczny szczególnie dobrze nadaje się do masowej produkcji ze względu na szybkość przetwarzania między każdą płytką drukowaną. Niemniej należy wziąć pod uwagę kosztowne oprzyrządowanie, czasochłonny proces przygotowania i ograniczenia narzucone przez gęstość PCB.
5 – TESTY KOŃCOWE
Gdy test elektryczny został zakończony, mamy pewność, że obwód jest prawidłowy. W następnej kolejności odbędzie się inspekcja końcowa.
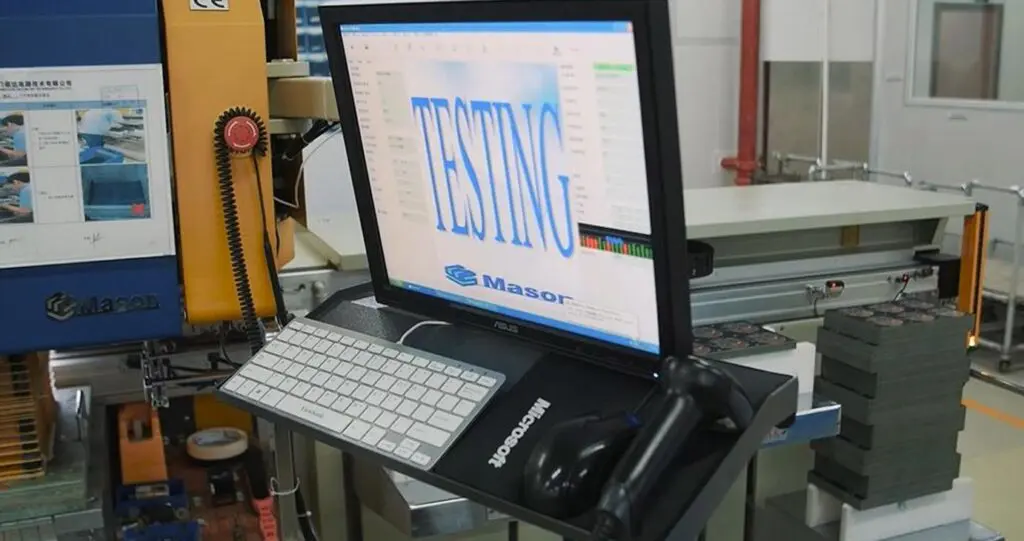
Kontrola końcowa
Jak ważne są kontrole końcowe płytek drukowanych?
Jest to kluczowy krok w procesie produkcji. Dostawca przeprowadza kompleksową kontrolę, obejmującą zarówno funkcjonalne, jak i estetyczne aspekty płytki. Porównuje wyniki z wymaganiami ICAPE i standardami IPC. Dodatkowo kontroler ICAPE na miejscu nadzoruje cały proces, przeprowadzając kontrole na różnych etapach, w tym przed pakowaniem i wysyłką.
1 – AUTOMATYCZNA INSPEKCJA
Każda płytka przechodzi przez maszynę do automatycznej inspekcji wizualnej (AVI). Sprawdza ona PCB szybciej niż ludzkie oczy i wykrywa niespójności w porównaniu z plikiem GERBER. Następnie płytka jest umieszczana na automatycznym urządzeniu do sprawdzania otworów w celu wykrycia ewentualnych nieregularnych rozmiarów.
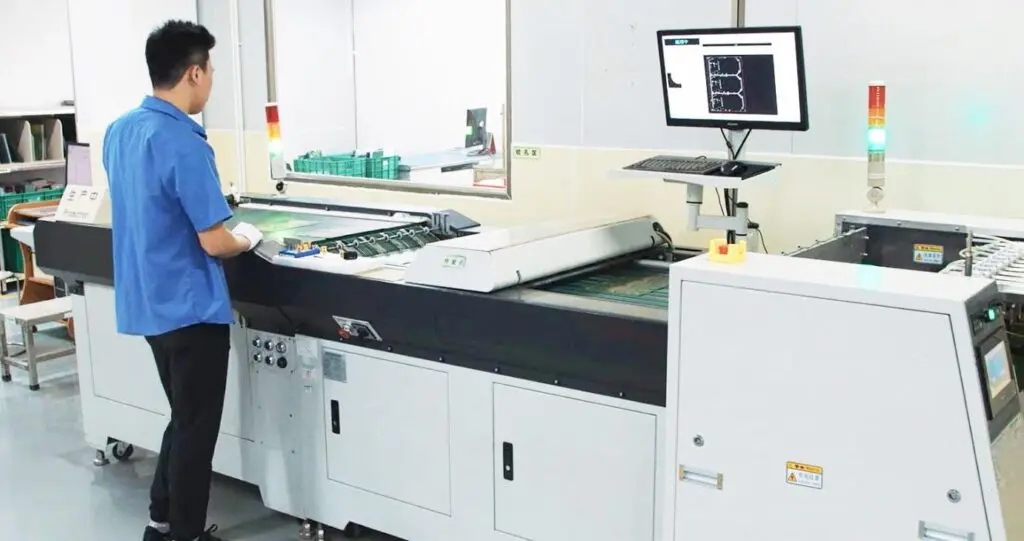
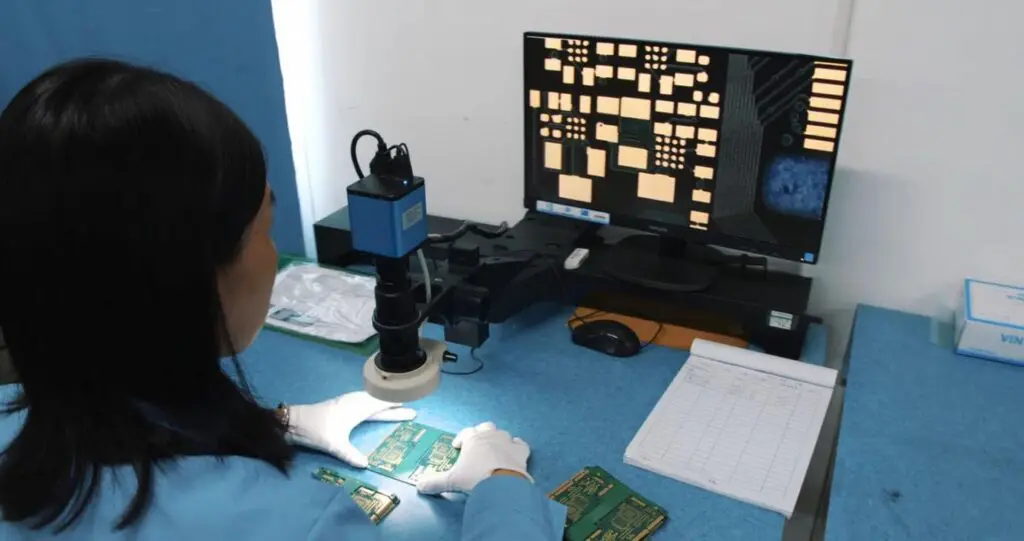
2 – KONTROLA DOSTAWCY
Wszystkie płytki są wizualnie sprawdzane przez wnikliwych inspektorów w celu kontroli każdej specyfikacji. Oceny przeprowadzane przez nasze fabryki partnerskie są monitorowane przez wewnętrznych inspektorów ICAPE Group, którzy są stale obecni na miejscu.
3 – ZESPOŁY PQC I QA
Nasze zespoły kontroli jakości (QC) oraz zespoły zapewnienia jakości (QA) udają się do fabryk partnerskich, aby samodzielnie przeprowadzić końcowe kontrole. Zapewnienie jakości jest zorientowane na proces i zapobiega defektom poprzez zabezpieczenie procesów wykorzystywanych do zarządzania i tworzenia gotowych PCB. Kontrola jakości jest zorientowana na produkt i określa, czy wynik końcowy jest zgodny z oczekiwaniami.
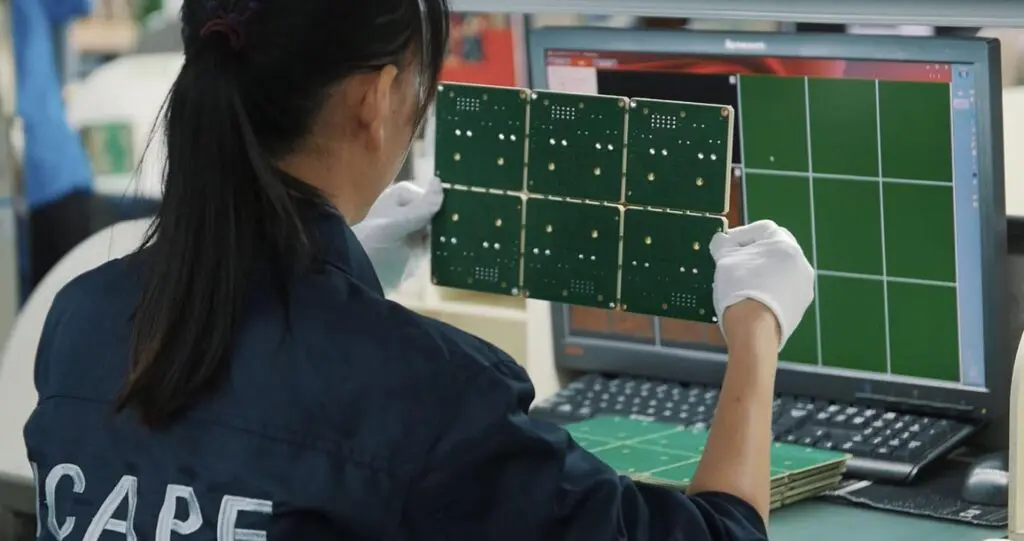
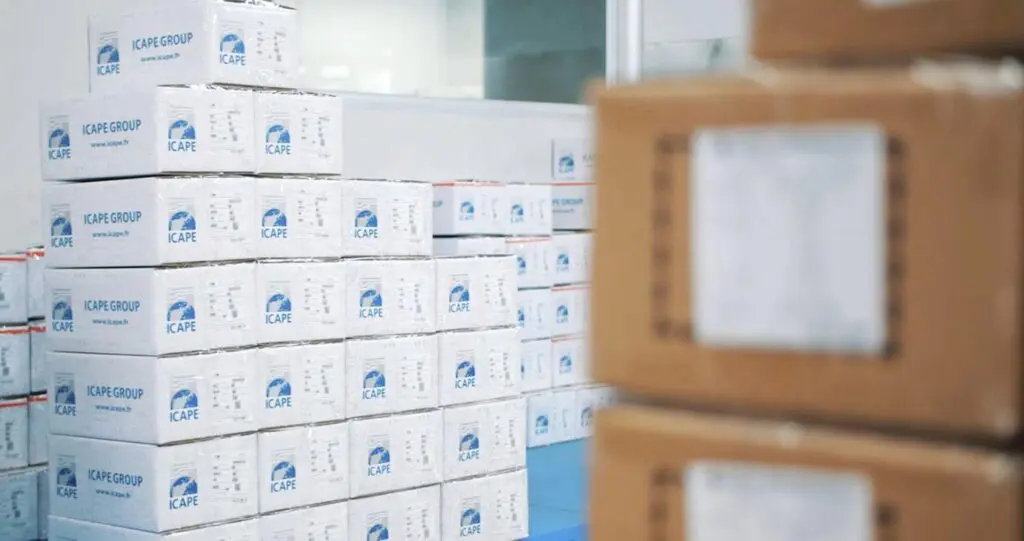
4 – LABORATORIUM ICAPE
Nasze laboratorium jest w stanie przeprowadzić wiele testów, takich jak analiza mikroprzekrojów, kontrola osadu miedzi na powierzchni otworu, sprawdzanie pozostałości zanieczyszczeń jonowych, kontrola poszycia powierzchni, chropowatość, kontrola impedancji PCB i integralności sygnału. Na płytce PCB można również przeprowadzić test starzenia i szok termiczny, aby zweryfikować jej niezawodność w trudnych warunkach.
5 – OPAKOWANIE
Po zakończeniu inspekcji, płytki są myte w dejonizowanej wodzie w celu usunięcia ewentualnego kurzu i zanieczyszczeń. Następnie płytki są starannie pakowane w opakowania próżniowe. Dodawana jest etykieta wysyłkowa i płytki są gotowe do wysyłki. Płytki mogą być wysyłane przy użyciu różnych środków transportu w zależności od życzenia klienta, takich jak DDP, DAP, samolotem, pociągiem lub statkiem.
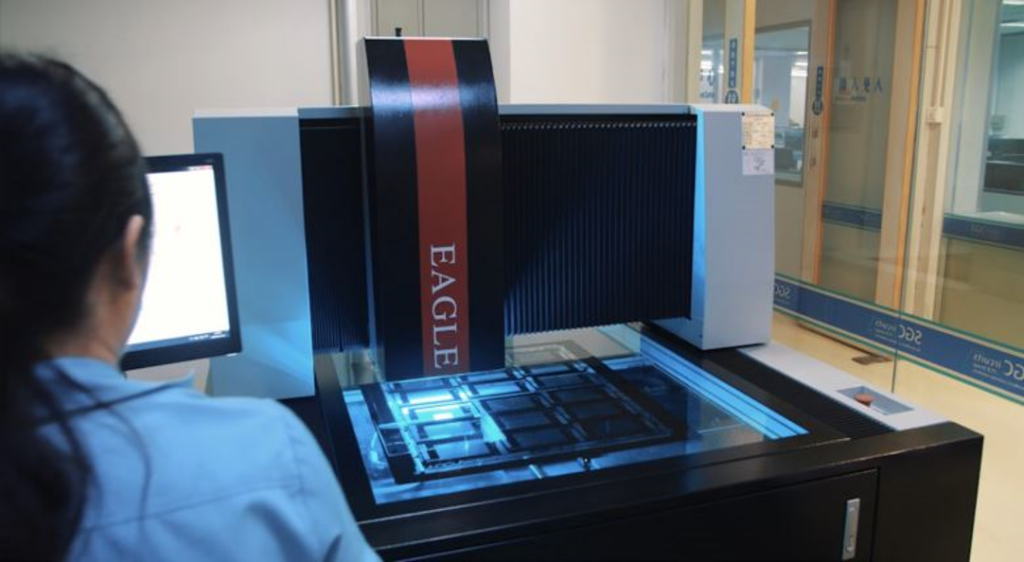