生产方面的挑战
随着电子产品的进步和小型化,对高密度互连印刷电路板的需求急剧增加,但增加印刷电路板的密度则是一项涉及从设计到生产的全方位挑战。 迹线之间的间距最大为65μm。 高密度互连印刷电路板至少包含4层,最多可达24层,通过孔和过孔相互连接,从而令设计规则和生产流程异常复杂。
如果说这类印刷电路板在设计方面对工程师的软件是一项挑战,那么生产方面的主要问题之一就是确保电镀孔的可靠性。 主要问题在于过孔和电镀工艺。 为了保证良好的孔电镀完整性,盲孔的深宽比限制为1: 0.8,高级比值为1:1。 标准胶片还含有玻璃纤维,而玻璃纤维对于激光钻孔来说太厚。 胶片中包含的玻璃会改变激光方向,并造成激光通孔形状质量欠佳或错误。
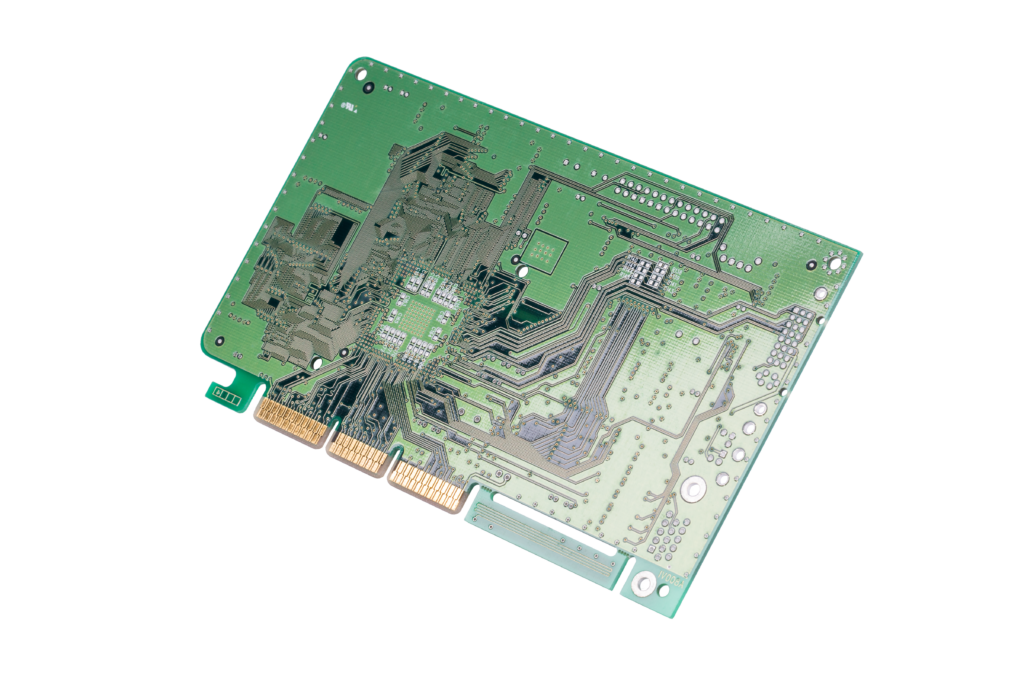
主要能力
HDI | 功能 |
---|---|
层数 MIN & MAX | 4-24L |
HDI 构建 1+N+1, 2+N+2 | 3+N+3 及任意层 |
材料 FR4, ..., ETC. | 见表 |
铜重量 MIN & MAX | 0.5 盎司~6 盎司 |
最小轨道和间隙 MM | 65/65μm |
最小和最大 MIN & MAX | 0.4-2.8mm |
尺寸 MAX | 0.457*508 毫米 |
表面处理 OSEP, ENIG, ETC. | HASL、HASL LF、ENIG、浸锡、OSP、浸银、电镀硬金/软金、金手指、选择性 OSP、ENEPIG |
机械钻孔 MIN | 0.15mm |
激光钻孔 MIN | 0.076 毫米 |
增强 HDI PCB 设计和可靠性
构建必须使用更薄的基底铜才能获得良好的轨道清晰度。 (许多电镀工艺增加了总铜材厚度)。 基底铜的选择也可能影响高频应用的信号传播。 更薄的胶片、更薄的基底铜、更薄的印刷电路板是高密度互连印刷电路板的发展趋势。
通孔是敏感元件。 过孔在组装过程中就像铆钉一样。 RoHS程序会对材料以及通孔施加高热应力。 材料在Z轴上的膨胀对通孔施加压力。 业界的趋势是不断减小通孔直径并提高可靠性。 此外,印刷电路板的组装过程使热阻块的数量成倍增加。 由于这种新情况,减少组装过程中施力的唯一方法是采用更稳定的FR4。 如果我们想限制组装过程中和恶劣环境中的破孔现象,则必须使用低热膨胀系数(CTE)材料。
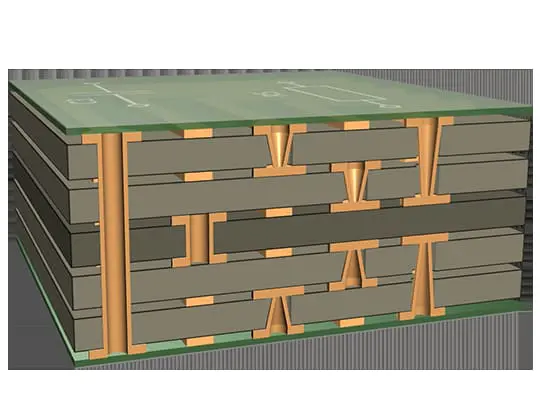