高密度互连印刷电路板微孔介绍
揭示微型奇迹的奥秘
印刷电路板(PCB)在几十年来一直是现代电子设备的支柱。 随着技术的进步,人们对更小、更轻、更高效的设备需求不断增长。 印刷电路板微孔在满足这些需求方面起着重要作用。 本综合指南将介绍印刷电路板微孔世界,探讨它们的类型、制造工艺、应用和基本设计注意事项。 无论您是经验丰富的印刷电路板设计师还是充满好奇心的印刷电路板爱好者,本文都将帮助您了解为未来电子产品提供动力的微型奇迹。
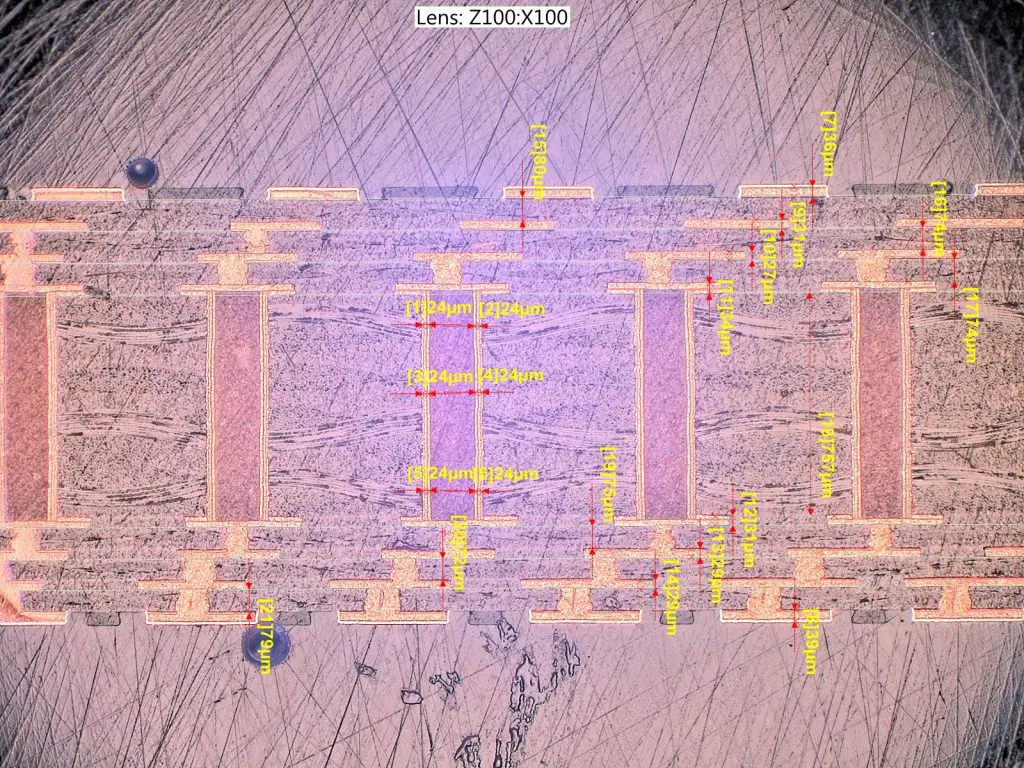
什么是印刷电路板微孔?
微孔是穿过印刷电路板一层或多层的微小孔洞,它的直径通常为0.1mm至0.15mm。 这些微观奇迹作为电路板不同层之间信号或电源连接的通道实现了高密度互连。
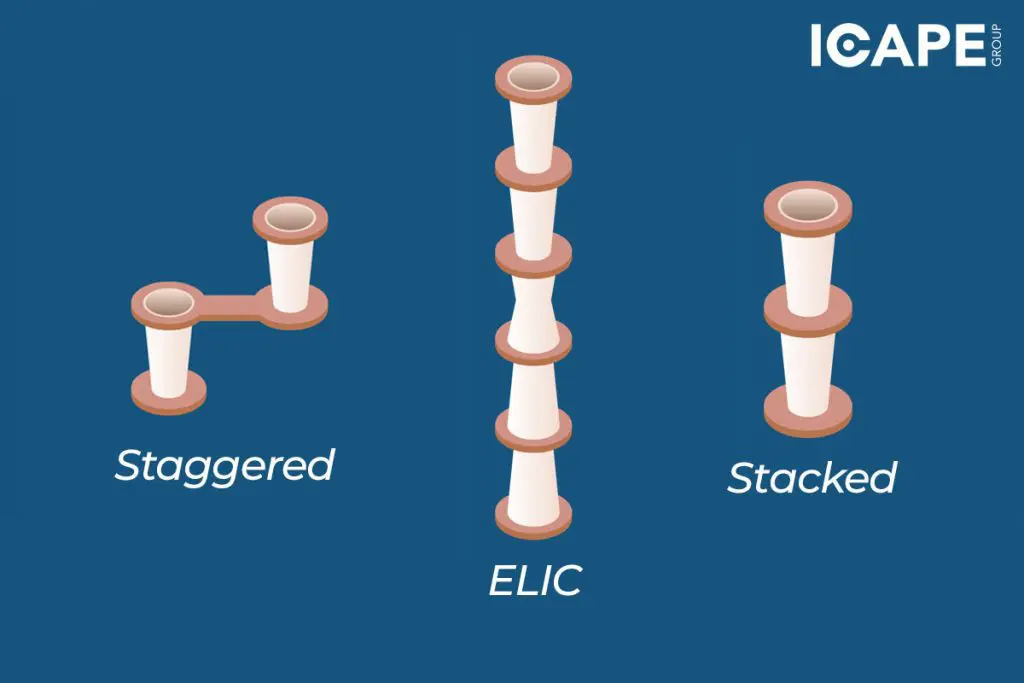
什么是过孔和微孔?
过孔用于在印刷电路板各层之间建立电气或热互连。 过孔基本上分4种类型:
- 通孔 – 穿过堆叠中所有层的机械钻孔。
- 埋孔 – 互连2个或多个内层的机械钻孔。
- 盲孔 – 将外层与1个或多个内层互连的机械钻孔。
- 微孔 – 将堆叠中的一层与下一层互连的激光钻孔。 (原则上可以通过机械方式钻出微孔,但利用激光实现微孔则更容易且更具成本效益。) 最常见的微孔尺寸为80-100μm,深度为60-100μm。 纵横比是隔离铜层的电介质与孔直径之间的关系。 大多数供应商要求纵横比为 0.6: 1 至 1 : 1,最常见的纵横比为 0.8 : 1(即 电介质80um激光钻孔直径0.1mm)。新一代激光钻孔机可以钻出直径小至40-50um的过孔,其中一些甚至能够从材料的两侧同时钻孔,由此可以实现在层压过程前对较薄的电介质进行激光钻孔。 这在印刷电路板等IC基板的生产过程中特别实用。
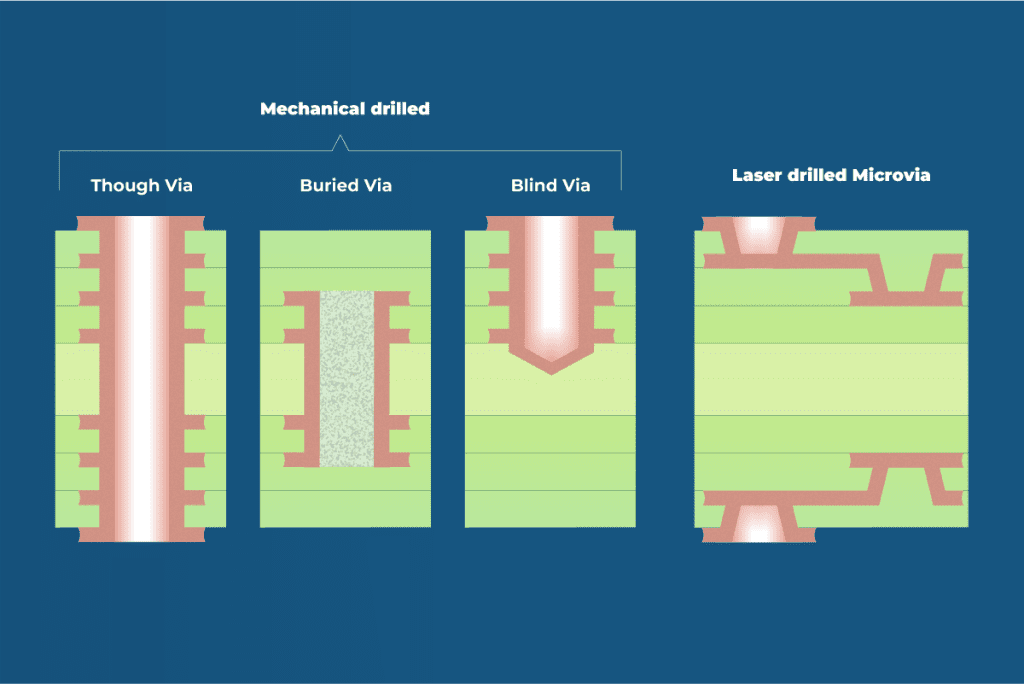
高密度互联堆叠结构和高密度互联步骤
具有电镀通孔(PTH)的标准印刷电路板仅需要1次层压、1次机械钻孔、1次孔清洁、1次化学镀铜和1次电镀铜。 高密度互联结构可能需要多次重复这些步骤。
所有高密度互联印刷电路板都从中间内层结构的构建开始,重复层压、钻孔、清洁和电镀步骤,直到完成最终的叠层。 下面我们将介绍一些示例。
1型IPC-2226高密度互联印刷电路板结构仅需要1次层压、1次机械钻孔、一侧或两侧激光钻孔、1次孔清洁、1次化学镀铜和1次电镀铜。 这也称为1步高密度互联。
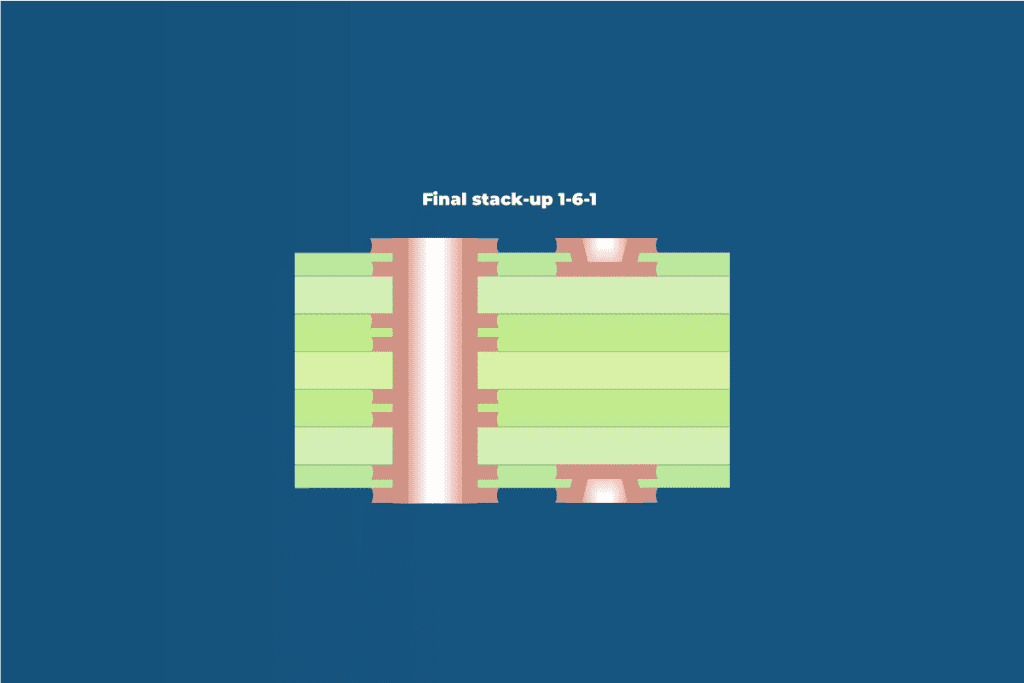
当1步高密度互联不足以支持元件间距或一般印刷电路板的密度时,可以添加额外的埋孔以增加布线密度。 2型IPC-2226高密度互联印刷电路板结构需要2次层压、2次机械钻孔、一侧或两侧激光钻孔、2次孔清洁、2次化学镀铜、2次电镀铜和1次树脂填充。 这也称为2步高密度互联。
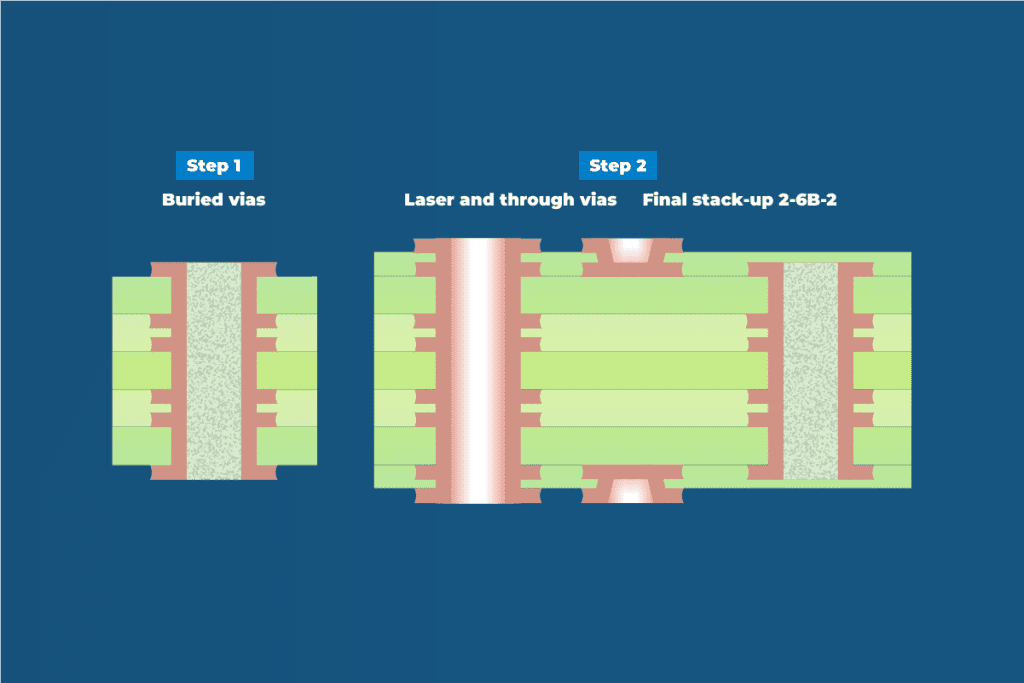
当2型结构不足以支持元件间距或一般印刷电路板的密度时,可以应用额外的激光过孔和埋孔。 3型结构包含至少2步微孔。 下面所示的3型IPC-2226高密度互联印刷电路板结构至少需要3次层压、2次机械钻孔、4次激光钻孔、3次孔清洁、3次化学镀铜、3次电镀铜和镀层以及1次树脂填充。 这也称为3步高密度互联。
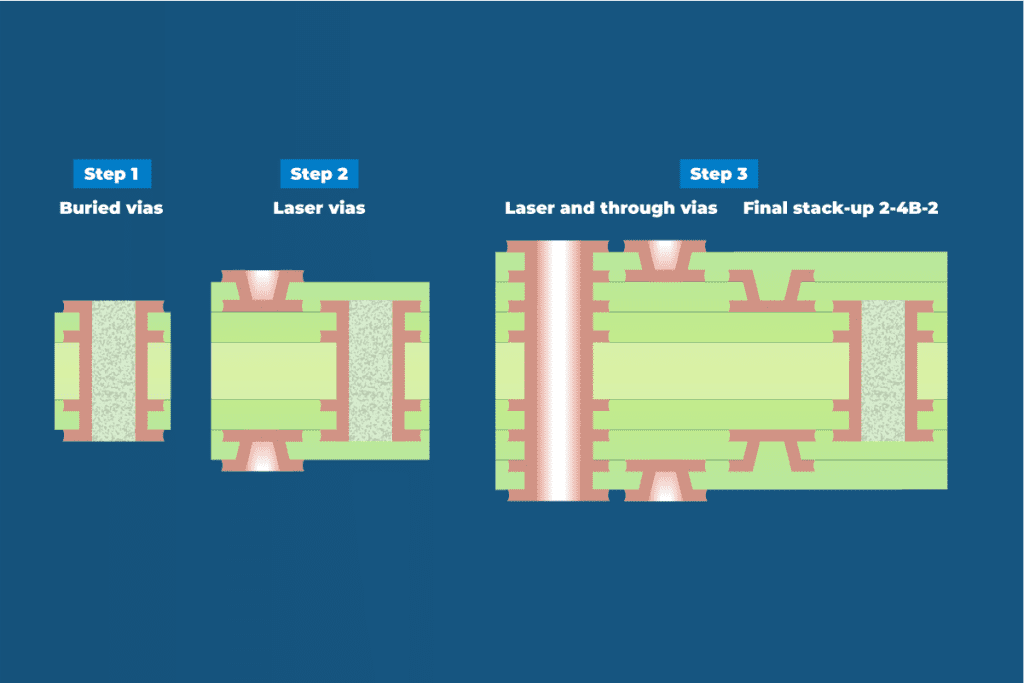
高密度互联步骤的发展
BGA器件间距已从最初的BGA组件上的1.2mm发展到1.0和0.8mm,其中仅包含过孔技术的多层足以创建互连,并且可以通过“狗骨”设计实现扇出。 如今,大多数BGA器件的间距仅为0.5mm或更低,这意味着采用激光钻孔的高密度互联技术是制造扇出的必要条件。 在手机行业,制造商甚至已经开始使用0.2mm间距的BGA器件。
这一发展突破了高密度互联印刷电路板的生产能力及相关生产设备的限制。
大多数包含间距为0.4-0.5mm的BGA器件的复杂高密度互联设计可以在印刷电路板的每侧最多使用2-4个微通孔步骤进行布线,但一些供应商已经掌握了5、6个或更多微通孔步骤,并且组件小型化的发展趋势不断朝着每层互连(ELIC)的目标突破限制,这也称为任意层高密度互联,其中堆叠的过孔可通过堆叠的任意层进行布线。
堆叠或交错微孔/埋孔
BGA的元件间距及其焊盘尺寸或设计密度将决定何时使用堆叠或交错微通孔/埋孔或何时使用填铜过孔。 每个额外的工艺都会增加印刷电路板的总体成本。 严格执行布线以及选择最佳高密度互联堆叠和过孔组合通常有助于降低成本。 ICAPE希望通过事实和专业建议支持您的技术见解:
选择最适合的过孔组合和步骤组合对于优化印刷电路板的制造成本是非常重要的。
在1-6B-1结构中添加微孔层以创建如下所示的2-4(6B)-2结构,此加工流程所需的额外成本远低于2-4B-2结构的制造成本。 1-6B-1和2-4(6B)-2都是2步高密度互联结构,但2-4B-2是3步高密度互联。
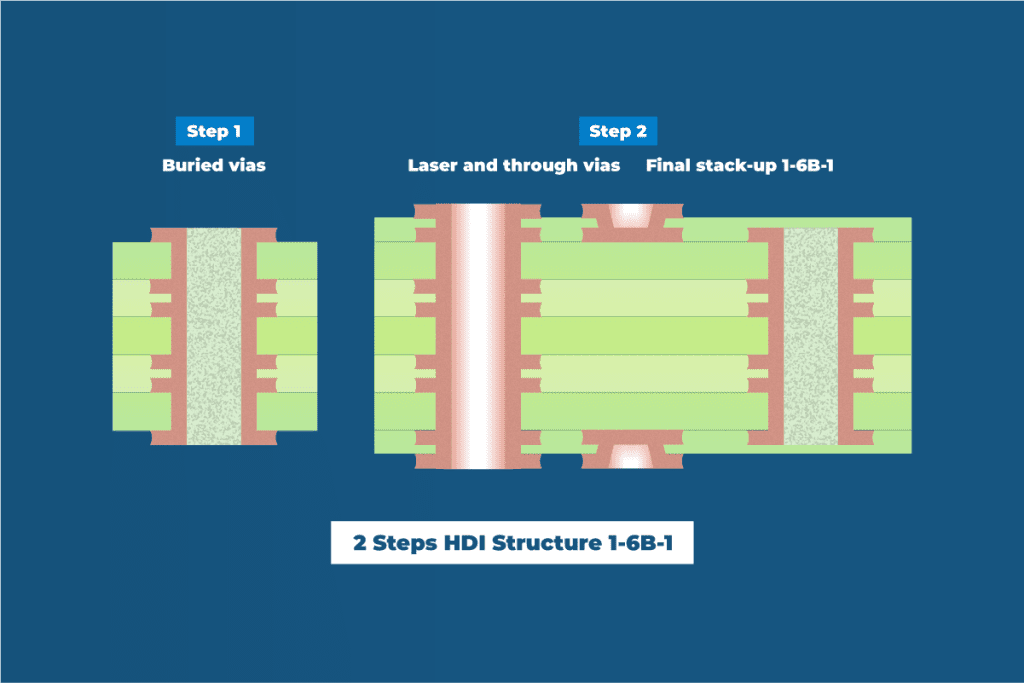
从1-6B-1结构到2-4(6B)-2结构所添加的唯一额外流程是2次激光钻孔。
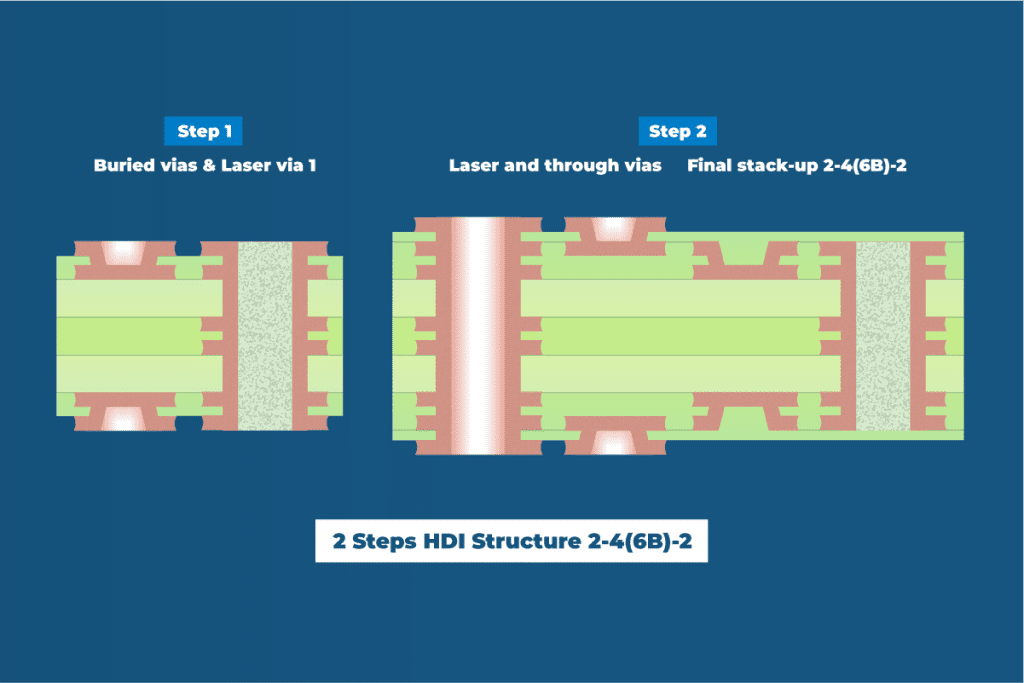
从1-6B-1结构到2-4B-2结构需要额外的高密度互联步骤,包括额外的2次激光钻孔、1次额外的层压、1次额外的孔清洁、1次额外的化学电镀和1次额外的电镀。
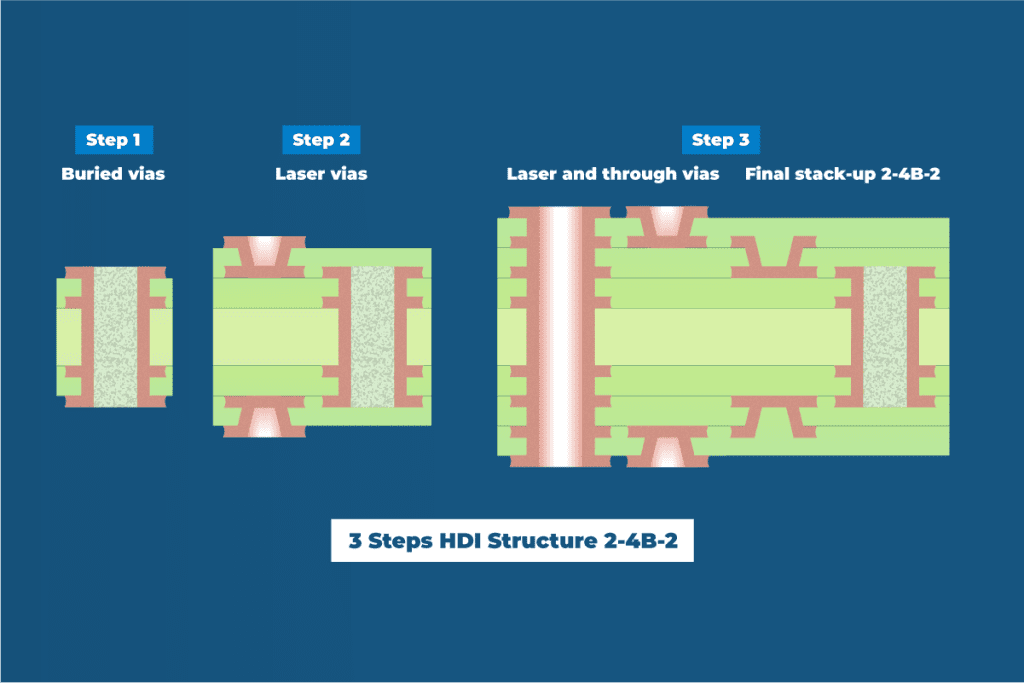
堆叠,还是交错过孔?
堆叠微孔为低间距BGA器件的高密度布线和扇出创造了更多空间,但它增加了印刷电路板的成本。 只有在没有足够设计空间来使用交错过孔时,才应使用堆叠微孔。 在埋孔上的堆叠微孔需要对埋孔进行额外的铜帽电镀工艺,而在微孔上的堆叠微孔则需要对内层微孔进行额外的铜填充。
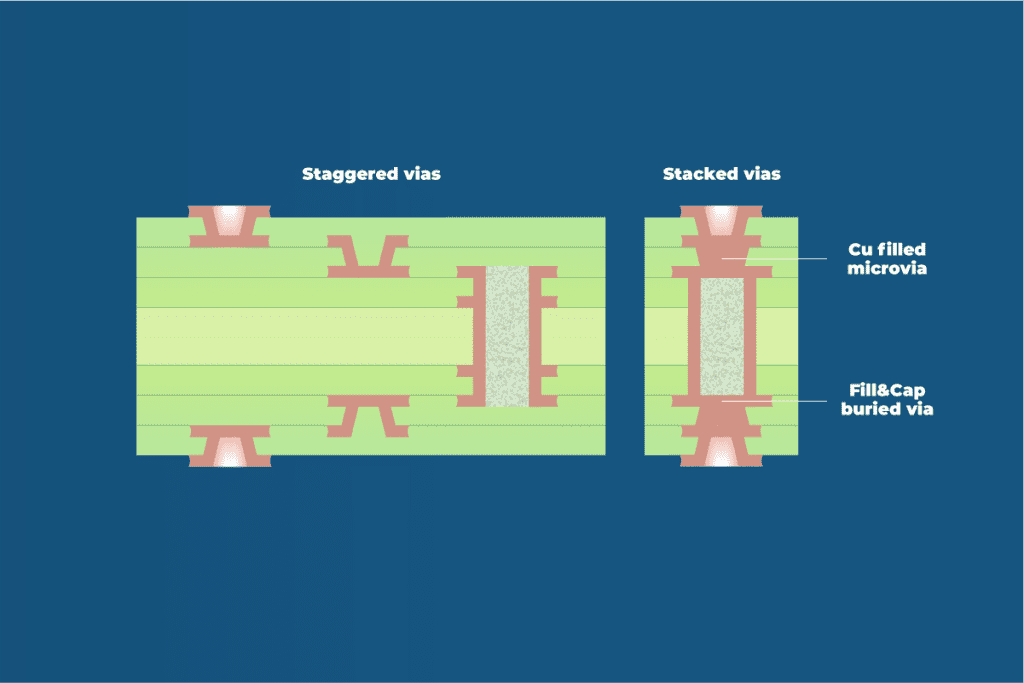
铜填充微孔?
铜填充有助于BGA焊盘或类似小焊盘中的微孔设计,因为这将消除焊点中出现气孔的可能性,但铜填充会增加印刷电路板的成本。 焊盘中没有微孔的设计则不需要铜填充。
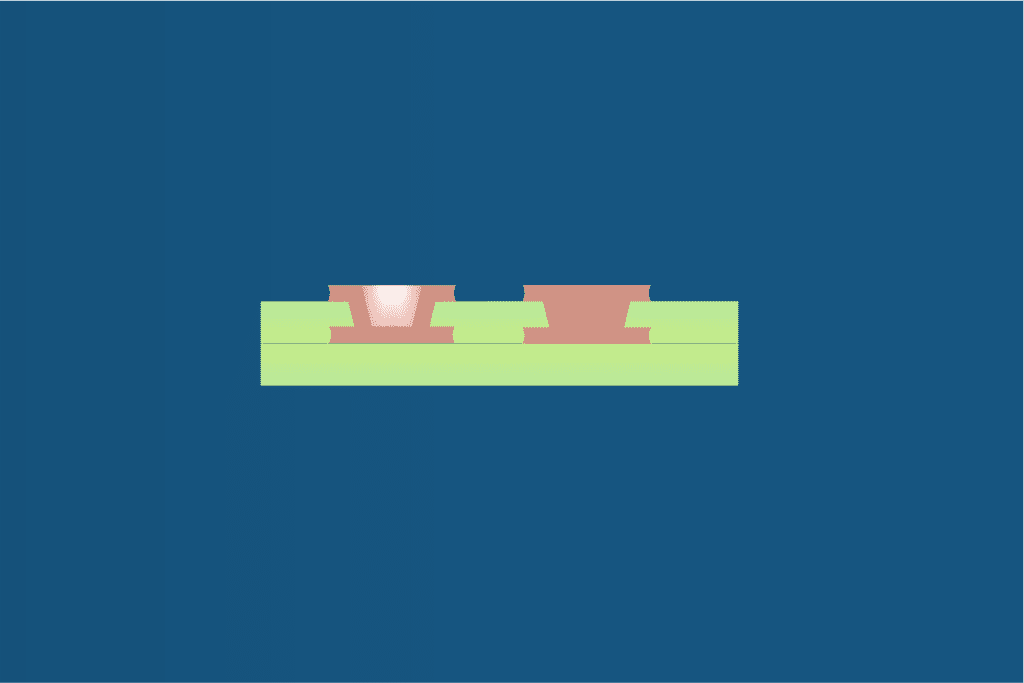
完整设计中的微孔集成
当由于布线密度或元件扇出而需要使用带有激光钻孔微孔和埋孔的高密度互连技术时,用激光钻孔微孔和埋孔替换所有机械钻孔是很重要的,因为这会降低制造成本和生产时间。
与孔对孔的成本相比,激光钻孔工艺比机械钻孔更快捷、更便宜。 与标准多层板相比,高密度互联印刷电路板的价格较高,这与每个高密度互联步骤所需的额外工艺有关。 无论是仅使用几个微孔来扇出BGA布线,还是用微孔和埋孔替换所有通孔,高密度互联工艺步骤的成本都是相同的。 在这种情况下,更换所有通孔将降低机械钻孔工艺的时间和成本。
更换整个印刷电路板上的所有通孔是有道理的:
– 它将为更好、更紧密的布线创造空间,从而在更小的空间内以更轻的重量容纳更多的组件。
– 它通过缩短信号路径、减少传输线以及改进GND和VCC参考平面功能和减少穿孔,从而提高信号完整性、控制阻抗并减少电磁干扰。
– 它无需在通孔上进行背钻,从而避免了短桩线(Stub线)的信号反射。
– 不带通孔的高密度互联印刷电路板对焊接工艺高温产生的热应力更具弹性。
机械钻孔和激光钻孔是如何实现的?
请观看ICAPE印刷电路板制造之旅第5集“钻孔”。
高密度互联激光微孔彻底改变了电子行业,使在更小、更轻的设备中集成更多的功能成为可能。 随着技术的不断发展,微孔将继续处于印刷电路板设计创新的前沿,为高密度互连和先进应用创造新的可能性。 通过了解与微孔相关的类型、制造工艺和设计注意事项,印刷电路板设计人员可以利用他们的专长技能创造未来的尖端电子设备。
报名参加ICAPE下一期关于高密度互联技术的网络研讨会,我们将在会上分享更多知识和提示,以优化您的印刷电路板设计和结构。